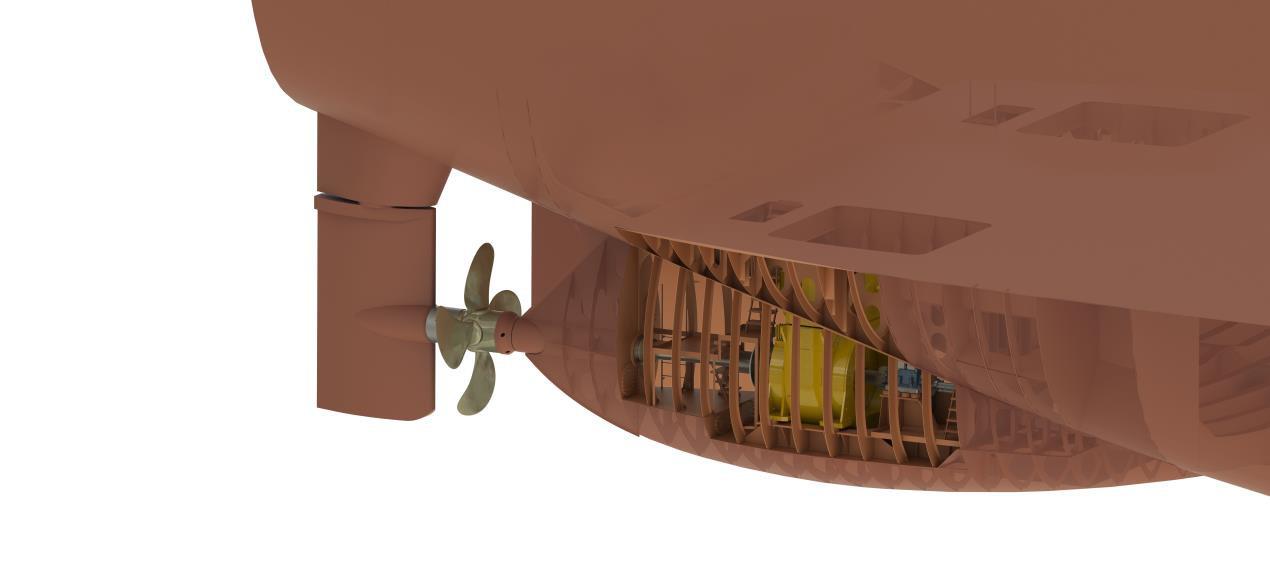
18 minute read
Machinery
The Berg Twin Fin system
Yaskawa/The Switch refits the Polarcus Naila
Advertisement
Finland’s Yaskawa Environmental Energy/The Switch’s co-operation with the system integrator, Sweden’s Berg Propulsion, on its Twin Fin dieselelectric direct-drive solution is a great example of a win-win partnership at a time when collaboration between OEMs and suppliers is critical in providing greener power solutions to reduce emissions from shipping while ensuring long-term gains for owners.
The Twin Fin is currently being installed in a self-unloading bulker being built in China and featuring a large internal MaK-powered variable-speed plant to meet high energy demand for propulsion, cargo handling and other vessel operations. The Switch is delivering permanent magnet (PM) propulsion machines, PM generators, DC-Hubs, Electronic Bus Links (EBLs) and Electronic DC Breakers (EDCBs) for the vessel as part of the environmentally friendly concept, for which Berg has a patent pending.
Twin Fin provides both increased cargo capacity usually associated with thrusters and the reliability and safety afforded by conventional propellers. Delivering higher thrust performance but with decreased energy consumption and emissions - it’s a real gamechanger for the industry offering superior efficiency and reliability. And reliability means optimal uptime.
Jonas Nyberg, Managing Director West, Berg Propulsion said that Twin Fin is tougher, as the motor is in a safer location than podded propulsors, where motors are directly in the pod. Twin Fin is like an advanced version of the twin-skeg forming an integrated part of the hull. Putting the machinery space in the fins also allows greater flexibility in hull design. “Electrical podded propulsors may have a higher degree of manoeuvrability but are less efficient than our solution due to the inherently high rpms and small propeller diameter. Azipod electrical podded propulsors are also less robust. Our solution is more cost effective, while the fins are also more hydrodynamic than bulbous pods.” In addition, almost all maintenance can be performed with the ship in the water.
Nyberg notes that a key disadvantage of electrical podded propulsors is that the units can rotate 360°. This puts limitations on the maximum propeller diameter. But with Twin Fin, there’s no restriction on propeller size. Propeller size is directly linked to efficiency – the larger, the better. It gives the freedom both to optimally position the propellers and have an enormousdiameter propeller.
Berg selected The Switch’s technology to ensure peak performance. There’s also the significance of direct drive versus the traditional gearbox concept. This is where The Switch’s highly efficient PM motors – which capture electrical energy and convert it into green mechanical power – really come into their own as integrated parts of the concept.
Traditional diesel-electric drive trains have a linear motor-gearbox-propeller shaft arrangement with a lot of mechanical components but using a compact directdrive PM motor eliminates the gearbox and the need to drive the propeller shaft directly. The PM motor stator is fixed to the hull, fully surrounding the rotor with only an air gap in between. This drastically reduces the number of components required, and that reduces the risk of mechanical issues. Along with the PM generators, the drive train contains the bare minimum of moving parts.
Twin Fin is also designed to be easily retrofitted with limited downtime. “The Twin Fin units are prefabricated, allowing rapid installation. It took just 45 days for us to retrofit the first installation on the seismic survey vessel Polarcus Naila,” says Nyberg. “Seismic vessels are a demanding application with full power needed 24/7 - without it, your streamers sink to the bottom. Whereas the owner had previously had reliability issues with another propulsion maker’s azimuth propellers, with our solution, we increased efficiency by over 25%.” Although Nyberg believes there will still be room in the market for electrical-pod concepts, he is confident Berg can capture the market where reliability and efficiency are paramount.
The role of emissions, legislation and financial stability is focusing industry awareness on the importance of ship design and earlystage equipment selection in lowering OpEx. Whereas before, there were practically no rules governing design for environmental efficiency, and most time and energy went into the true purpose of the vessel in terms of cargo factors, now we have EEDI/EEXI applying both to new and old ships. Shipping is rapidly embracing this change with more time, energy and CapEx being invested at the outset to ensure an efficient product.
Nyberg notes the efficiency difference of a brand-new optimised ship versus a vessel built even five or 10 years ago is in the double digits. “Projects like our direct-drive solution are key building blocks in the drive to enable a more responsible, sustainable and profitable industry, and I certainly believe the future belongs to efficient, space-saving technologies like The Switch’s PM machines and DC-Hub, with or without Twin Fin,” he says.
Vroon contract for Berg Propulsion
A recent retrofit to optimise a containership’s propeller blade design has brought performance and fuel efficiency gains that are measurable in real-world conditions. Holland’s Vroon recently approached Berg Propulsion to investigate the possibility of optimising the propulsion system on its containership Indian Express, fitted with a controllable pitch propeller originally manufactured by ZF. The aim was to secure the sustainability benefits available through greater ship efficiency, as part of Vroon’s continuing strategy to find the best practical answers to lowering CO2 emissions, ahead of IMO’s Energy Efficiency Ship Index (EEXI) and Carbon Intensity Indicator (CII). The work was carried out in Suez Shipyard, Egypt.

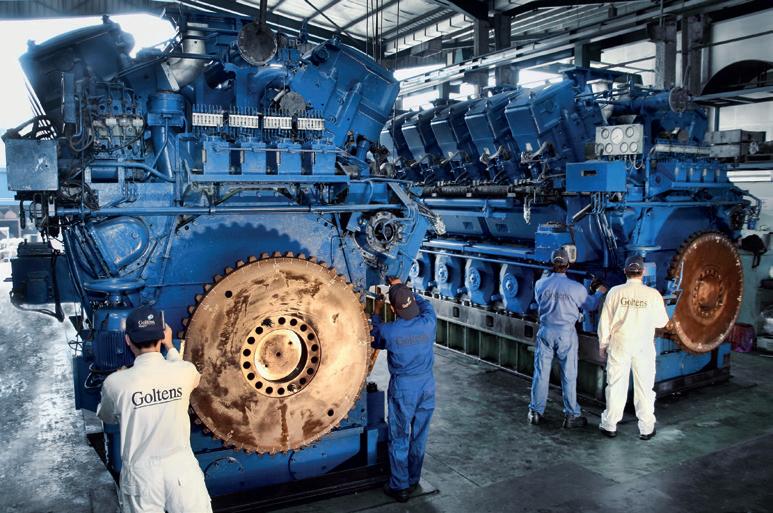
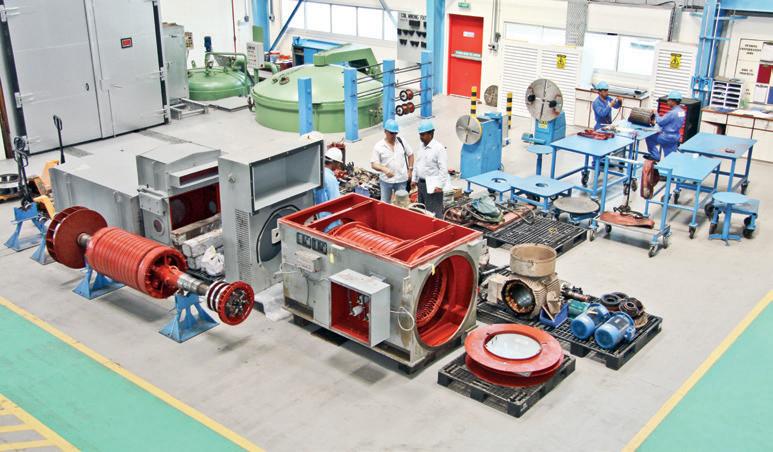


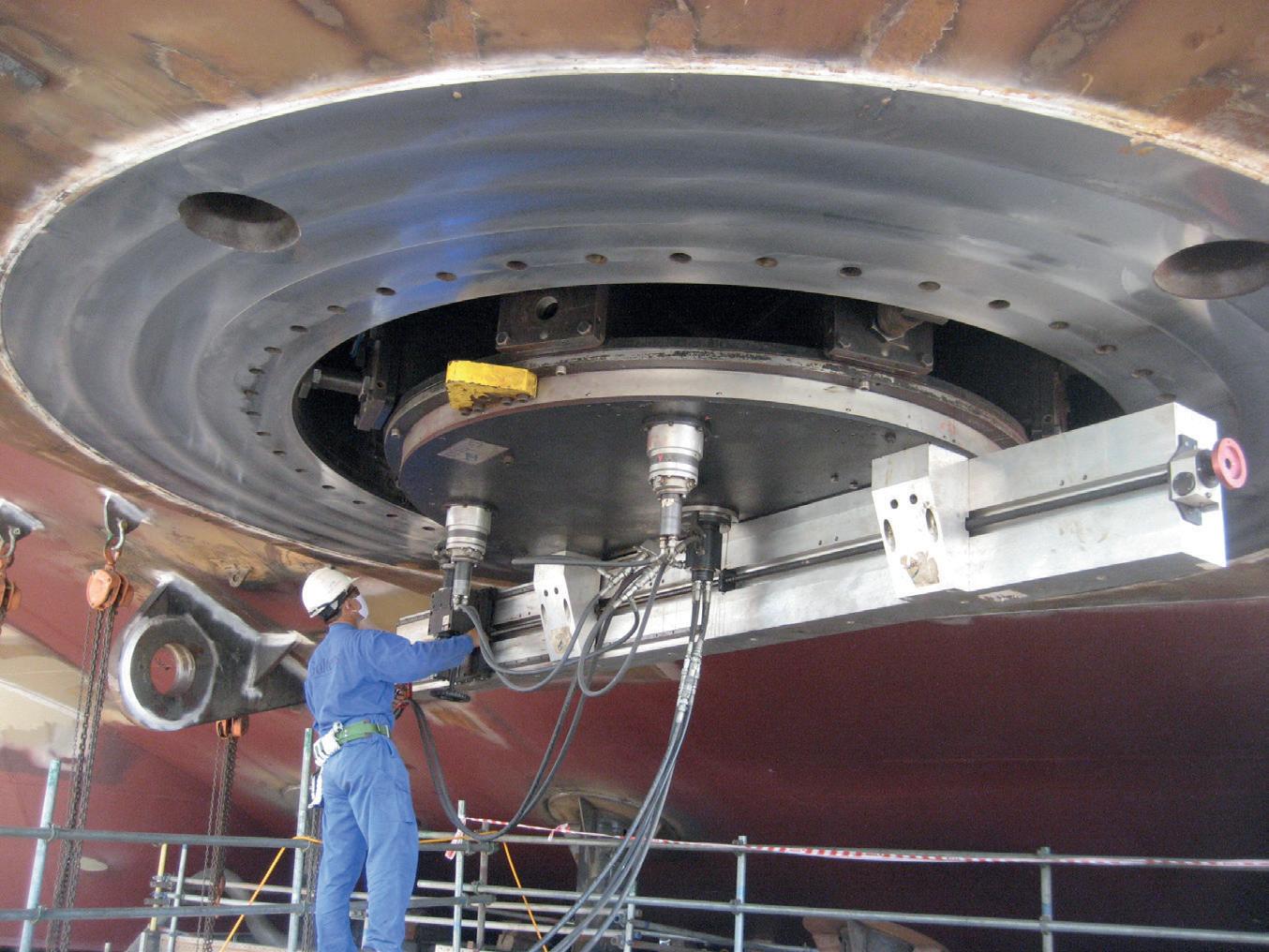
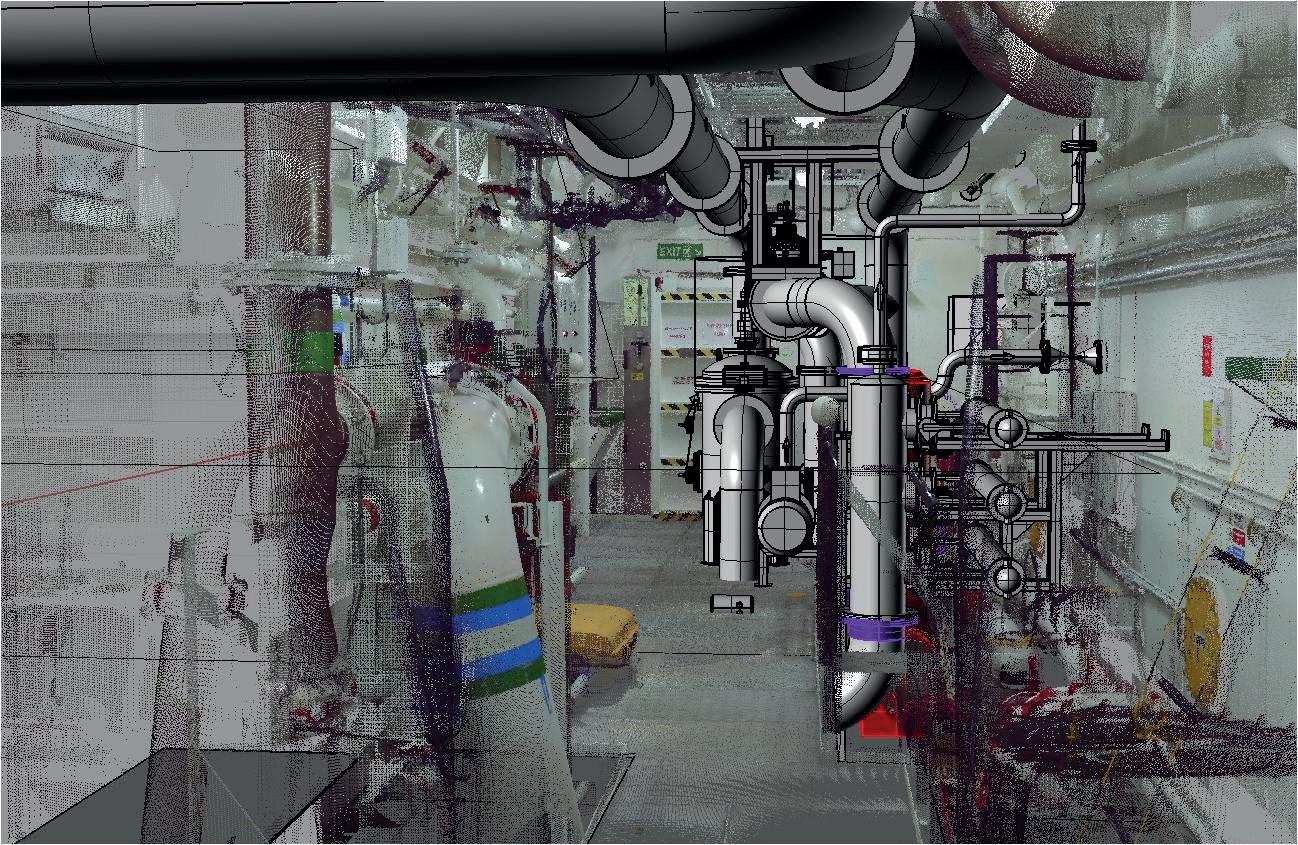
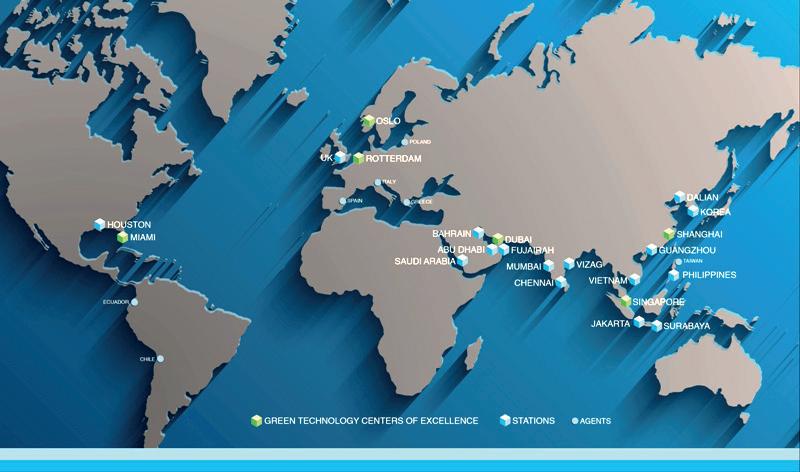

The Indian Express in drydock
David Sakandelidze, Berg Propulsion Business Manager – Energy and Efficiency, explained the process which established Vroon’s requirements. “In close co-operation with the shipowner and shipoperator, we analysed the vessel’s current and future operation needs and defined its operation profile,” he said. “Next, the performance of the original propeller blades was benchmarked against the vessel’s defined operation profile.”
From here, Berg Propulsion’s advanced simulation tools were used to develop new propeller geometry, which modelling showed would achieve remarkably superior performance the new operation profile anticipated for the ship. In line with these findings, Berg Propulsion designed blades tailored for the operation, improving efficiency significantly, according to Sakandelidze.
“Efficiency gains are made for much of the time and, at 12 knots, the new blades achieve up to 50% higher efficiency than the ones they replace,” he said.
With performance improved at the speeds most commonly required during operations, Indian Express would achieve an astonishing 22% fuel saving overall, as well as lower emissions that should go farther than the requirements of IMO’s carbon Intensity Initiative goals for 2026. “We have recently put a new focus on CII and EEXI and supporting customers to improve and optimise vessels already in operation,” said Jonas Nyberg, Managing Director West for Berg Propulsion. “We are excited to partner our customers, and to help them become more efficient while reducing their environmental footprint.”
Berg’s focus targets hydrodynamic upgrades such as blade optimisation, control system upgrades such as installing an engine pitch and rpm optimisation system, Dynamic Drives, and electrical upgrades to run shaft alternators with variable frequency coupled with energy storage, said Nyberg.
New mtu units for Balearia catamaran
Rolls-Royce’s new mtu engines, new mtu ship automation system, and the new mtu Go! tool for remote service have well and truly futureproofed the high-speed catamaran Avemar Dos run by Spanish operator Balearia. Four newgeneration mtu 20V1163 M84 units replaced the previous 1163 units, taking the vessel to a new level of ecological soundess.
Fuel consumption – and with it CO2 emissions – are 8% lower than with the previous propulsion system. The new Series 1163 units deliver the same power output, but with a 33% reduction in nitrogen oxide emissions, thereby meeting the requirements of IMO’s Tier II emissions standard.
The ferry’s automation system has also been renewed - the mtu ship automation not only controls and monitors engines and gearboxes, but numerous other crucial ship systems such as fuel tanks and on-board generator sets. That means that the crew can benefit from an all-round view of the ferry. The new ship automation system brings not only new software, but new screens and computers with interfaces to other systems on-board. The digital platform mtu Go! puts the finishing touch to the ferry’s all-round update, allowing the customer to remotely access the vessel’s operating data at any time, monitor its condition and predictively plan maintenance.
Pablo Vivancos, Sales General Manager at Rolls-Royce Solutions Iberica, said, “The Avemar Dos is now the fourth Balearia ferry to be powered by mtu. Several of these ferries are supported by mtu Value Care maintenance agreements, individually tailored to suit each vessel. We’re very proud to be Balearia’s trusted partner.”
The Avemar Dos catamaran was built in 1996 by the Austal shipyard in Australia. It went into service in 1997 and following several changes of owner was taken over by ferry operator Balearia in 2008. It originally served the Strait of Gibraltar route between Algeciras and Ceuta. Now the new repowered ferry plies between the mainland Port of Denia and the Balearic Islands of Ibiza and Majorca. The 82-m ferry can accommodate 855 passengers and 174 vehicles.
Besides the Avemar Dos, the Ramon Lull high-speed ferry was recently re-powered using mtu engines – in this case Series 4000 units. Other high-speed ferries, like Nixe and HSC Formentera Direct, have used mtu propulsion ever since going into service.
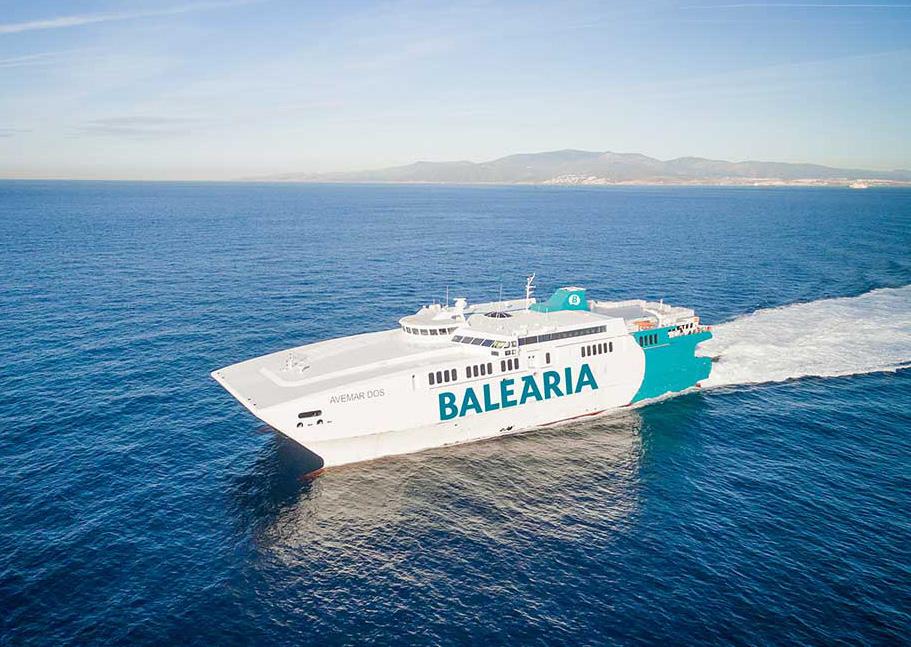
The Avemar Dos
Strategic Marine and Global Marine’s contracts for Royston
New electronic fuel management systems (EFMS) from UK’s Royston have been specified for fast crew boats being supplied to one of the largest vessel operators in South East Asia.
The work sees the supply and commissioning of enginei systems, featuring on-board HMI (human machine interface) and a specially configured remote platform, for three vessels from Singapore-based boat yard, Strategic Marine.
Offering easy-to-understand fuel data analysis and reporting options, enginei is an advanced fuel monitoring system that can be installed as part of a comprehensive suite of digital marine technologies, delivering longterm vessel efficiency and improved operational performance.
Strategic Marine continues to design-in enginei capability as part of its vessel systems to ensure compliance with customer specifications for advanced electronic fuel management capabilities, which help to improve fleet operations and overall vessel management.
The new systems are being overseen by Royston’s Singapore-based operation, which is seeing strong demand from Asia Pacific-based vessel owners and operators for easy-to-use technology with accurate measurement, control and analysis of fuel consumption data capabilities.
With more than 350 vessels worldwide featuring enginei systems, including OSVs such as anchor handlers, jack ups, PSVs and crew boats, operating in West Africa, the North Sea, Asia, Egypt, Mexico and Brazil, Royston continues to targets fleet owners and operators in the South East Asia market.
At the heart of system is expanded on-board flowmeter and sensor technology. This gives the advanced system the ability to acquire comprehensive real time engine and vessel performance measurements beyond the usual RPM, GPS and fuel inputs to take in a wide range of other engine control unit outputs.
The data is displayed live through a touch screen bridge display and transmitted remotely to the enginei web portal where the state-ofthe-art interface enables the rapid production of intuitive online reports and trending graphs, as well as providing alerts and map dashboard
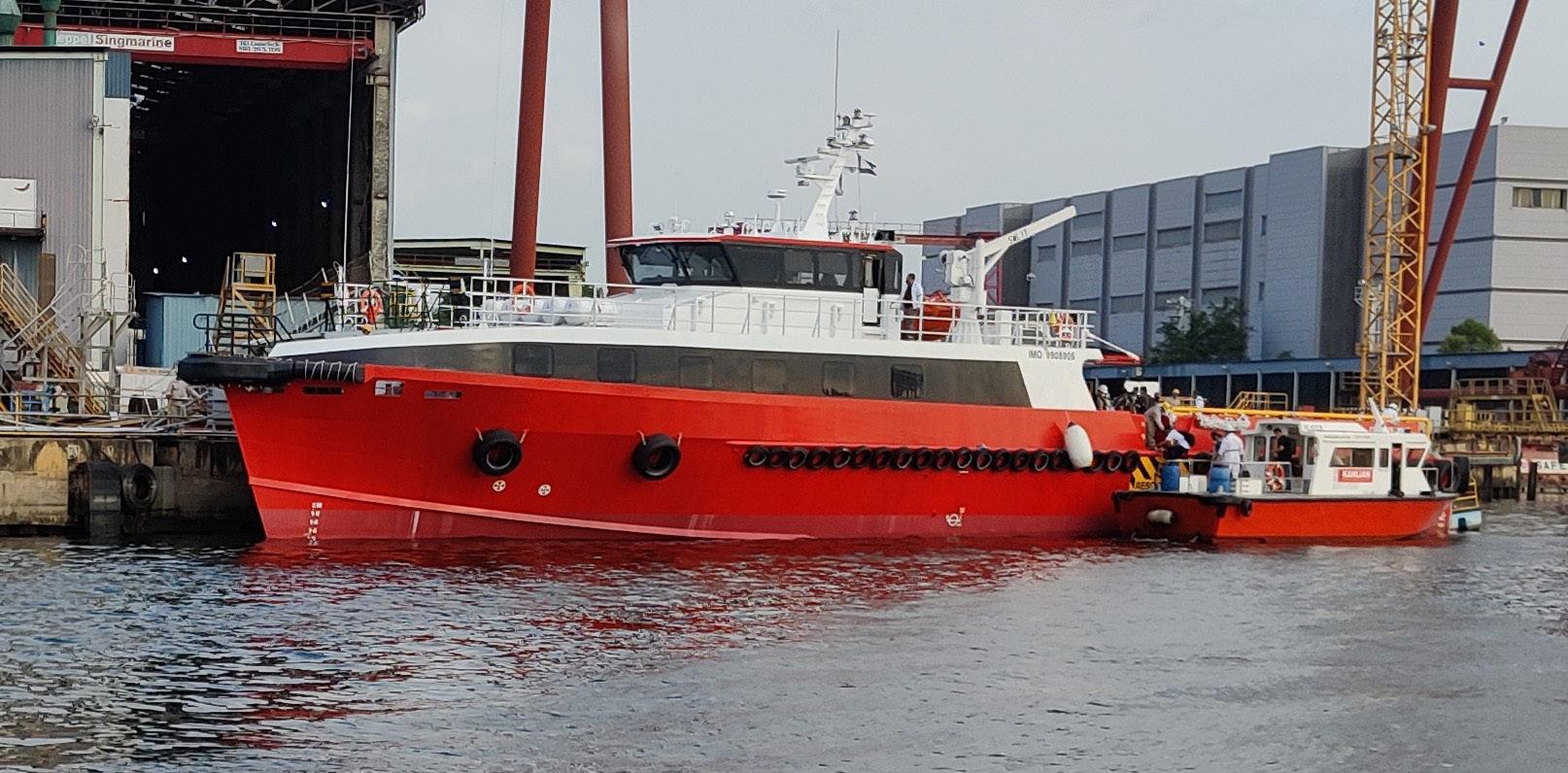
Strategic Marine uses Royston’s enginei EFMS in its vessels

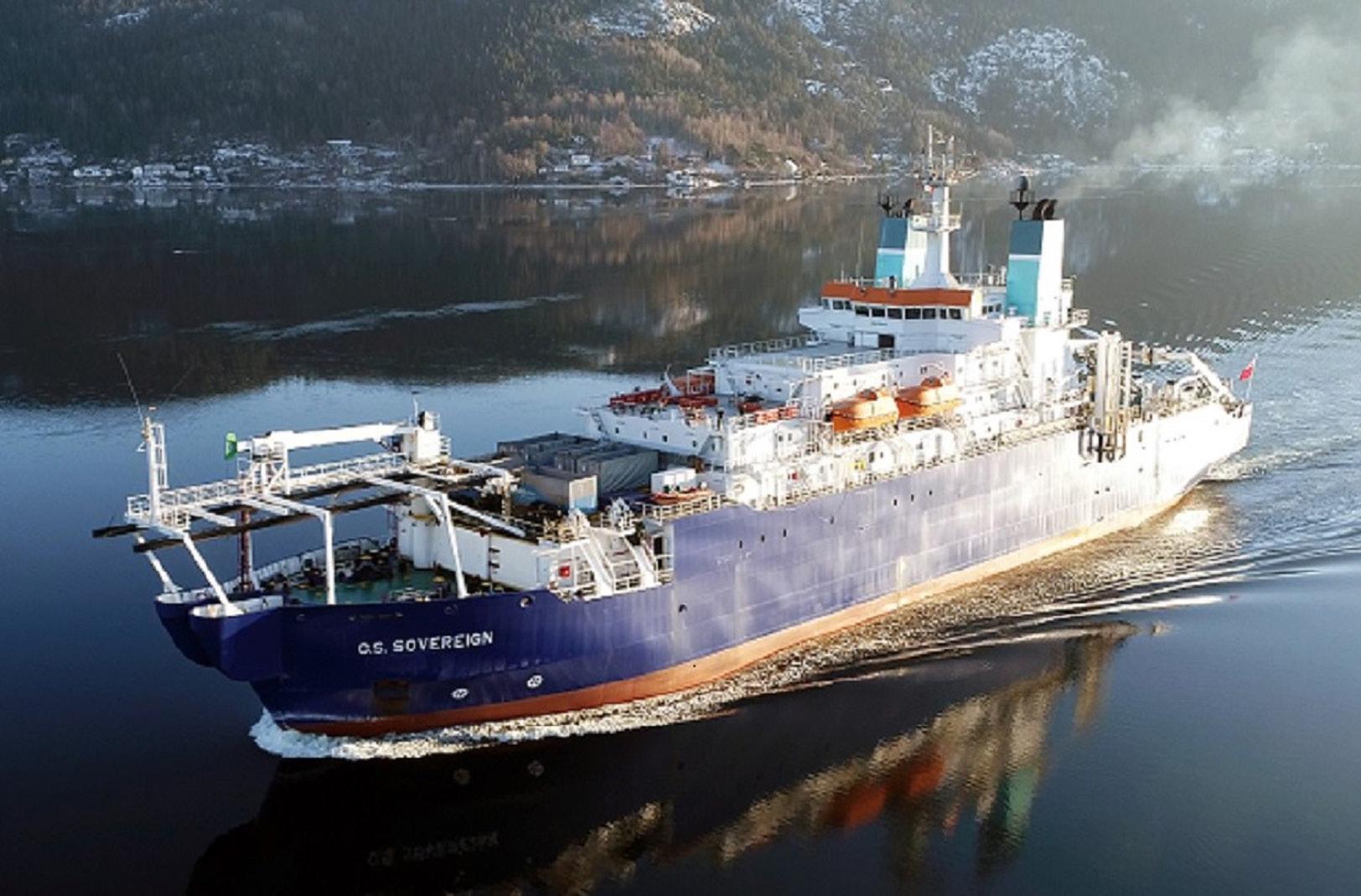
Royston has completed the overhaul of two diesel power plants on-board CS Sovereign
tracking with weather overlays, showing a detailed operational profile for a vessel.
Meanwhile, Royston has completed the overhaul of two diesel power plants on-board a Global Marine Group operated multi-role subsea cable installation and repair works vessel. Drawing on its extensive capabilities and resources, a five-strong team of engineers completed the 24,000 running hours service work on a Stork-Wärtsilä 12SW280 engines and a Stork-Wärtsilä 16SW280 unit on-board the 130 m length CS Sovereign while the vessel was in dock at Damen Shiprepair Rotterdam, in Rotterdam.
This involved the overhaul of the crankshaft vibration damper on the main engine generator DG.1 before refitting with new gaskets. Main engine works on the two other generators (DG.2 and DG.3) saw the similar overhaul of crankshaft vibration dampers alongside checks and repairs to cylinder heads, liners, bearings, connecting rods and pistons. On completion of engine work, full sea trials were successfully undertaken. Royston engineers have also recently completed the overhaul of diesel power plant systems onboard another vessel within the Global Marine Group fleet of offshore vessels, the 130 m length Global Symphony, in a tight 10-day time frame.
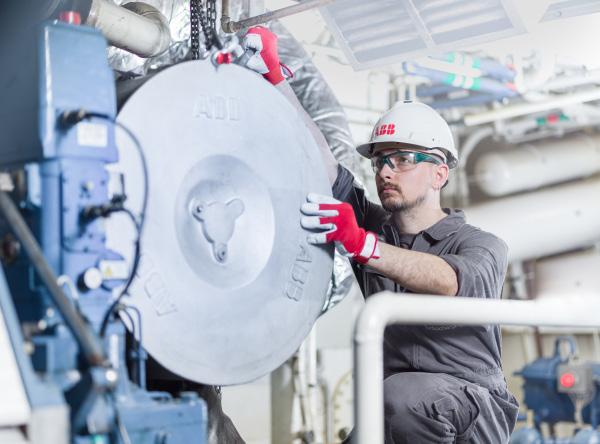
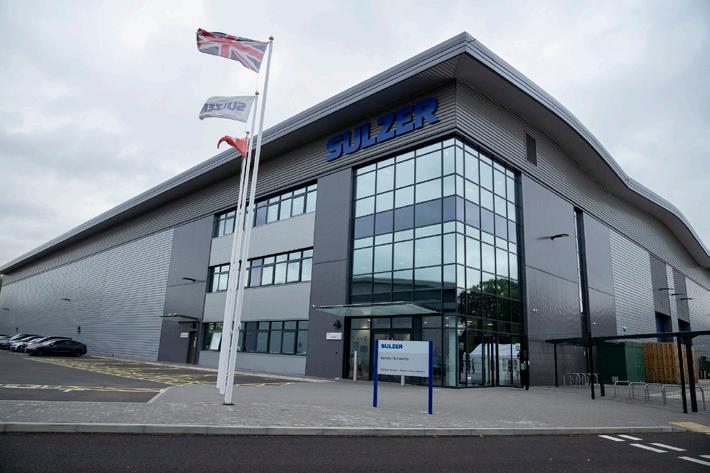
Sulzer’s new service centre
New UK service station for Sulzer
Following the recent completion of Sulzer’s purpose-built service centre in Birmingham, the facility was officially opened on October 27th, 2021. The investment in this state-of-theart service centre represents Sulzer’s on-going commitment to delivering the next generation of service excellence and provides 24/7 support to customers around the world.
Located on the prestigious Birmingham Business Park, the latest enhancement to Sulzer’s extensive network of service centres has been specifically designed to optimise workflows. It ensures customers receive bestin-class service in terms of quality and speed of repair. Following the official opening, guests were given a guided tour of the new facilities and shown how their businesses will benefit from the latest in advanced repair technologies provided by Sulzer.
Building on the legacy of the Camp Hill site, which has provided engineering expertise for 100 years, Sulzer has relocated its wealth of engineering knowledge and craftsmanship to a purpose-built facility. The comprehensive range of in-house design skills and cutting-edge technology are being used to deliver precision repairs and improve equipment performance.
Chris Powles, Head of Electro-Mechanical Services - EMEA, commented, “We have created a centre of excellence, which operates on lean manufacturing principles and sets the benchmark for the maintenance and repair of all vital equipment. Our engineering expertise and experience mean we deliver the highest quality of service and we encourage customers to visit us and see for themselves.”
As part of the relocation, Sulzer has invested in new equipment including larger, 50-tonne overhead cranes and constructed an upgraded overspeed balancing pit, which is the only independent facility in the UK. The company offers optimised overhaul projects for all crucial industrial equipment including cutting-edge additive manufacturing and state-of-the-art digital technologies. Together with the ability to design, manufacture and test high-voltage coils, as well as advanced reverse engineering capabilities, Sulzer delivers best-in-class services to its customers.
50th lifecycle award for ABB Turbocharging
Switzerland’s ABB Turbocharging has welcomed the 50th customer for its Turbo LifecycleCare annual service agreement as operators in the marine and power sectors seek to maximise uptime while benefitting from predictable maintenance costs and high-quality OEM service. The full-scope service agreements, suitable for main and auxiliary engine turbochargers in the marine and power plant sector, are based on a fixed price per running hour covering standard spare parts, wear and tear and labour.
Turbo LifecycleCare was launched in 2017 and since then has provided customers with
An ABB service engineer conducting maintenance work
confidence that their costs will reflect actual running hours. One early adopter was bulk carrier operator Equinox Maritime, a Turbo LifecycleCare customer since 2018. According to technical manager Leontios Pitaoulis, the service also provides assurance of high-quality maintenance at the hand of ABB Turbocharging experts.
“Reliability and uptime are of utmost priority for our operations. With ABB’s Turbo LifecycleCare service agreement, all spare parts planning and servicing are conducted on time, efficiently and within fixed budget. This agreement has given me peace of mind on turbochargers so I can focus on other important operative needs,” said Pitaoulis.
Dirk Balthasar, Head of Global Service Sales at ABB Turbocharging, added, “Our Turbo LifecycleCare agreements address customers’ needs for service plannability and financial predictability. With these agreements we make sure that our customers can focus on the essentials of their business, while we take care of their turbochargers in terms of service scheduling and execution – with fixed budget and no surprises from day one.” To date, ABB Turbocharging has secured Turbo LifecycleCare contracts for a wide range of marine and land-based customers valued at around US$125m in total.
Wärtsilä launches EEXI solution
Finland’s Wärtsilä has launched a new series of power limitation solutions that enable compliance with IMO’s Energy Efficiency Existing Ship Index (EEXI) regulation. These latest Wärtsilä innovations mean that the company now has a complete range of solutions for environmental regulatory compliance, covering both newbuild and retrofit projects.
The EEXI regulation comes into effect in 2023 and stipulates the minimum energy efficiency level for existing ships already in service. Wärtsilä’s new power limitation systems allow owners to meet this requirement, despite the tight implementation schedule. Wärtsilä’s environmental offering also includes various energy efficiency solutions that enable compliance with IMO’s Carbon Intensity Indicator (CII) requirements, which form part of IMO’s strategy for reducing greenhouse gas emissions from shipping.
For meeting the EEXI requirements, three macro areas are relevant, namely Power Limitation, Energy Efficiency technologies, and Fuel upgrades. With the introduction of these latest power limitation solutions, Wärtsilä covers all three areas with proven solutions, and can thus recommend the optimal choice for meeting the specific needs of owners and operators.
“With this latest launch, Wärtsilä once again emphasises its commitment to supporting customers in their decarbonisation efforts in line with the global targets set by IMO. We can offer a complete set of opportunities for complying with the existing and upcoming regulations,” says Giulio Tirelli, Director Business Development at Wärtsilä.
The power limitation upgrades being launched by Wärtsilä are verified and approved systems. They comprise Engine Power Limitation for 4-stroke engines, Engine Power Limitation for 2-stroke engines, Shaft Power Limitation for vessels with a controllable pitch propeller (CPP)
YOUR PROPULSION EXPERTS
EXTENDED LIFECYCLE THANKS TO SCHOTTEL MODERNIZATION
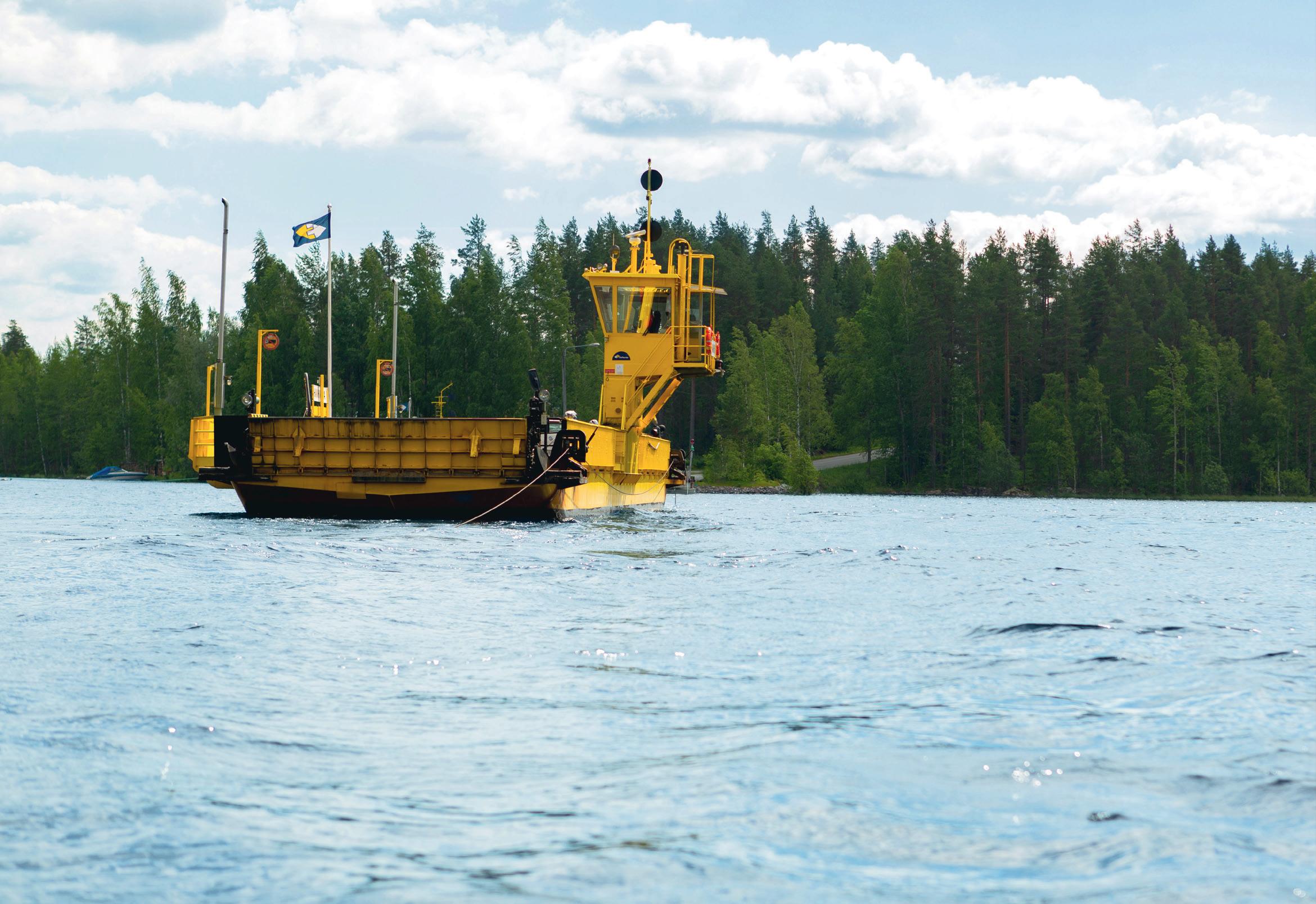
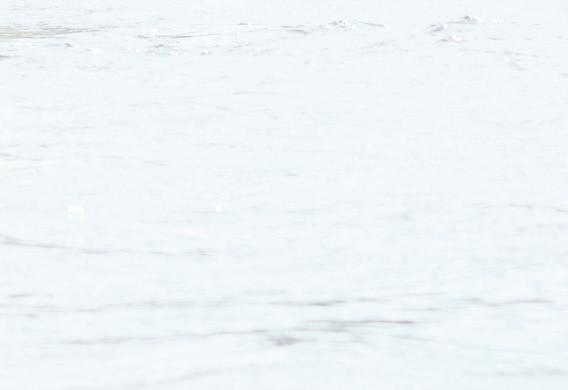
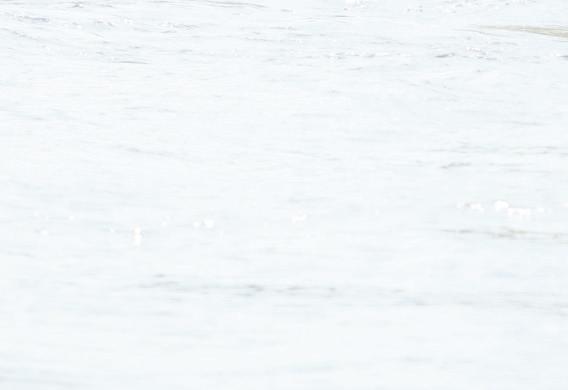
Two vessels in Finland’s ferry network are ready for further decades of service. Originally equipped with various propeller systems, a tailored concept by SCHOTTEL now allows the same propeller assembly to be used in both ferries without having to alter the steelwork. ADVANTAGES
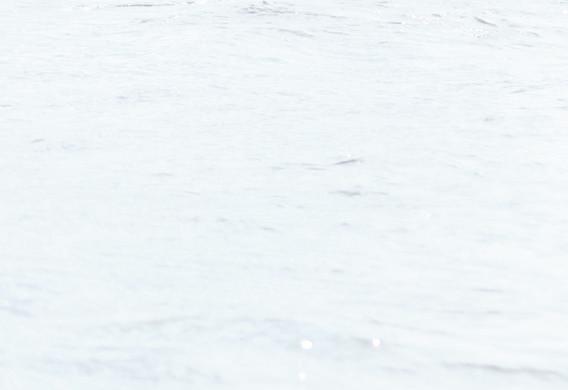
+ Higher degree of standardization + Simplified spare part management, increased availability + Worldwide network of service engineers + Spare parts for decades with SCHOTTEL as OEM + SCHOTTEL Academy: worldwide network of training centres and trainers
www.schottel.com

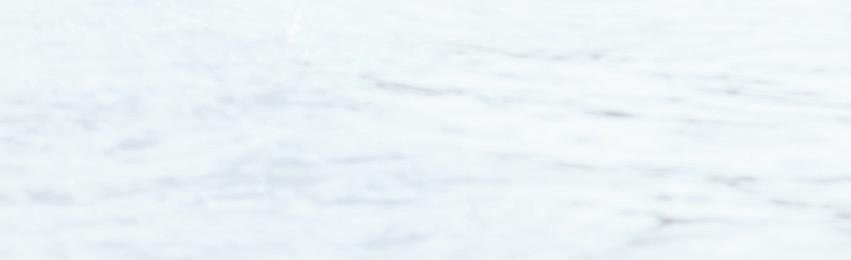
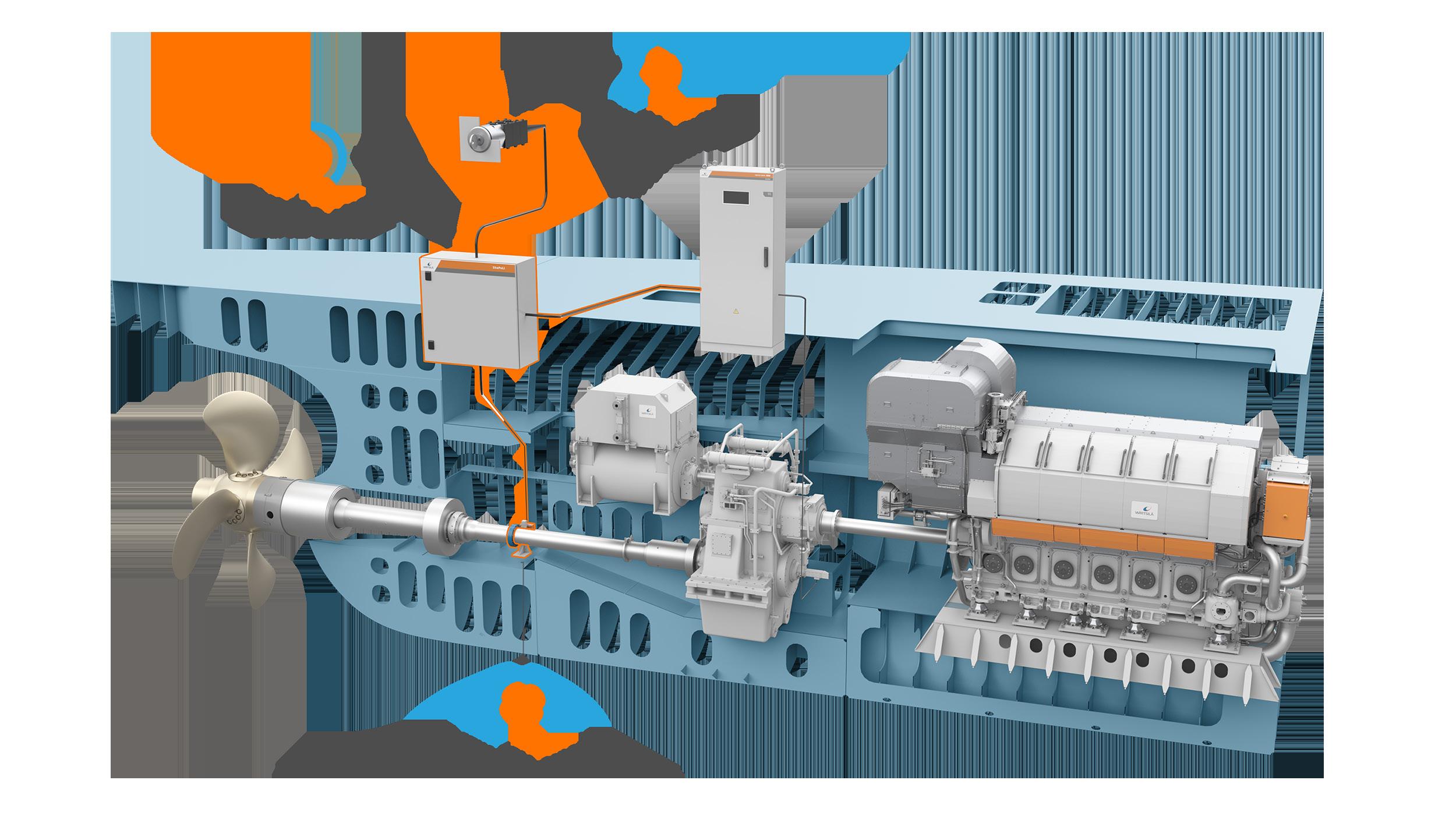
Wärtsilä has launched EEXI compliancy solutions through power limitation
and a Wärtsilä Propulsion Control System, and Power Limitation specifically dedicated to dieselelectric installations.
The upgrades effectively limit the engine or shaft power during normal operation, regardless of the power train combination and control system arrangements. The set limits of the solutions can all be overridden from the bridge. This is a mandatory feature stipulated by IMO’s MEPC guidelines, as are the monitoring and recording functions. The system data is stored in accordance with the regulations for inspection purposes.
100 orders for MHI-MME retrofit propeller
Japan’s Mitsubishi Heavy Industries Marine Machinery & Equipment (MHI-MME), has achieved order 100 units of the retrofit propeller, which began delivery since 2013. MHI-MME began producing propellers for the first time in Japan on 1904, and has a long history of more than 100 years. MHI-MME has continued producing and developing high performance propellers on the basis of a proven track record, which now the production record is over 6,000 units.
The retrofit propeller is designed for slow steaming conditions by the limitation of engine load and MHI-MME shows the large effects for the improvement of fuel efficiency with applying the suitable design for slow steaming. The retrofit propeller efficiency improvement in a certain vessel reached about 8%, up to the limitation of engine load. MHI-MME applies the design for the retrofit propeller to Mitsubishi Advanced Propellers (MAP) Mark-W, which propeller was launched in 2010 and can improve the propeller efficiency without sacrificing cavitation margin.
Many customers in Japan and overseas expect the benefits of retrofitting and have adopted our propellers for large containerships, LNG and conventional tankers, which are often applied in slow steaming. And orders for retrofit propellers have been increasing due to the need to comply with EEXI (Note1) regulations.
Additionally, MHI-MME carries out the evaluation of the propeller efficiency improvement after propeller retrofitting and confirmed. When retrofitting a propeller, MHI-MME also proposes to buy the propeller currently installed on the customer’s vessel, thereby offering an opportunity for customers to reduce their initial investment. SORJ
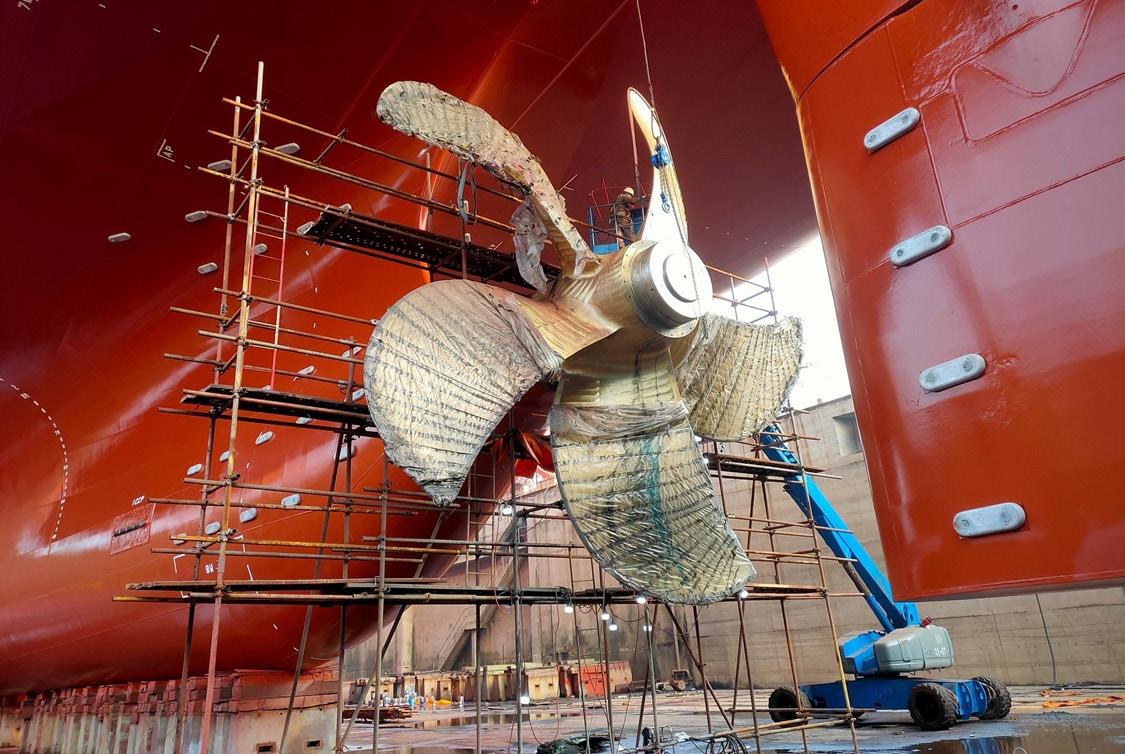
The MHI-MME retrofit propeller