
6 minute read
Aerial Pine Seeding by Helicopter
by Wes Kay, Aerial Spray Manager, Expedition Helicopters Fashor Yu, AgNav, Inc. / Lai Nguyen, P.Eng., AgNav, Inc.
With catastrophic wildfires happening in many places in the world, forest protection and reforestation are big concerns for countries that have wet and dry weather that varies, such as the United States, Canada and Australia. This year millions of hectares of wildlands and forests were burned. People lost homes and even their lives. Wild animals lost their habitats, as seen in recent Australian wildfires. The damages accumulated to billions of dollars. After wildfires, forests must be restored to return the ecological climates for local residents and habitats for animals. Like other developed countries, each year Canada spends millions of dollars to manage forests, keep them healthy, make them more resilient to insects and diseases and replant trees after harvest. It has been proven that aerial application plays a critical role in forest management.
In January 2019, Expedition Helicopters, a company based in Cochrane Ontario, Canada, won a bid for aerial seeding programs on forests in the Northwestern Region of Ontario. This project involved seeding a total 1,164 hectares (4,657 acres) of pine forests in northern Ontario. The program planning commenced mid-March and the actual seeding carried out by mid-April 2019. The challenge for applicators was the seeding rate was so small, only 75 to 125 grams of seeds per hectare (0.067 to 0.11 lbs/acre).
The existing system used a tank having an orifice plate on the dispensing gate to spread seeds. The orifice size was calibrated on the ground to the desired amount of seeds per minute. Every time the seeding rate was changed, the orifice had to be calibrated again. This method worked, assuming the pilot could always maintain the same aircraft ground speed when spreading. This was tough for the pilot, especially when there was wind. Considering application precision, this method exposed a few major problems. First, the amount of seeds released at any time was not measurable during flight and not controllable based on aircraft speed. Due to gravity, more seeds might be released when the tanks were full than when the tanks were half full or almost empty.
Upon winning the tender, Wes Kay, the Aerial Spraying Division Manager for Expedition Helicopters, contacted AgNav, Inc to discuss how to make a better system for pine seed spreading at the required rate. Kay brought to AgNav a bucket of pine seeds to test with the AgNav granular flow controller (GFC) which includes a universal flow control (UFC) box and two rotary dispensers manufactured by AgNav. The dispenser works as a rotary metering gate for the Isolair granular applicator and consists of a DC gear ratio motor, encoder and impeller.
In the past, the AgNav GFC has been used mostly for mosquito control to spread granules for larviciding. this rate, the GFC motor turned only 1 to 1.5 revolutions per minute (RPM). This rotational speed was too slow to control the existing GFC. During the test, when the GFC speed was less than three RPMs, the motor operated in a pulsating pattern, i.e. stop and go.

AgNav GFC dispenser with a standard impeller
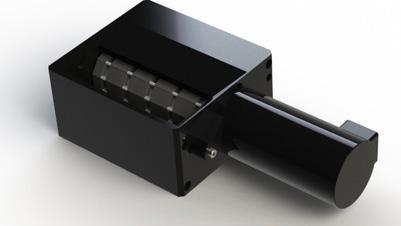
AgNav GFC dispenser with modified impeller
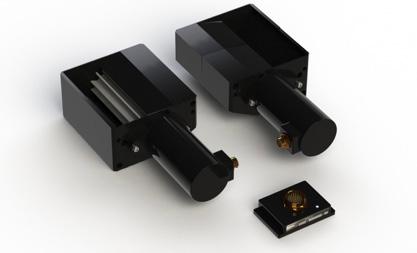
AgNav Granular Flow Controller
After working with Expedition Helicopters for the GFC calibration, it was found the impeller dispensed around 125 grams of seeds per revolution.
With the helicopter having a swath width of 18m (60ft), flying at 100 km/h (60MPH), the pilot covered 3.0 hectares per minute. At the required rate of 75 to 125 grams of seeds per hectare, the pilot needed to spread 225 to 375 grams per minute (g/min).
The helicopter was equipped with two Isolair tanks. Each tank spread 113 to 188 g/min. At this rate, the GFC motor turned only 1 to 1.5 revolutions per minute (RPM). This rotational speed was too slow to control the existing GFC. During the test, when the GFC speed was less than three RPMs, the motor operated in a pulsating pattern, i.e. stop and go.
To make the GFC work for Kay, AgNav engineers first modified the impeller by making shallower petals and adding spacers in a way that seeds were still be released evenly, but at a smaller amount with the impeller turning. The goal was to increase the motor’s speed so it would run smoothly. After a few modifications, the final impeller dispensed 62 grams of seeds per revolution.
The GFC ran better, but still pulsated. Due to low kinetic energy at a very low speed, friction and load change could cause the motor speed to vary significantly. A tiny adjustment caused the motor to run too fast or too slow. The proportional–integral–derivative (PID) controlling algorithm used in GFC firmware was fine tuned to allow the motor to run smoothly at a speed below three RPM. The 24V motors used in a standard GFC were replaced with 12V higher gear ratio motors to gain better accuracy. This helped reduce speed oscillation and converged to a target speed twice as faster. The Navigate software in the AgNav guidance system was also modified to allow the pilot to enter a small application and display rate value in grams for monitoring. The final system worked well.
After installing the GFC into the helicopter’s Isolair tanks, Kay calibrated it again and demonstrated the system to the seeding program supervisors. One of the treated areas was flown by using flight simulation. The aircraft speed was varying from 100 to 120 km/h. When the helicopter entered the area, the GFC automatically ran the motors to release seeds into collection containers. When the helicopter exited the area or was over an exclusion zone, the GFC stopped the motors. When one pass was completed, the next pass was selected automatically. The auto-spray feature in the AgNav guidance system eliminated the human error when operating the spray on/off function at boundaries. This helped significantly when the spray boundary was not clearly seen because of the forest canopy. After finishing an area, seeds in the collection containers were weighed. According to Kay, the released weights were perfectly matched with the ideal weight that was prescribed for the area. The spreading system was approved for the program.
In April 2019 when weather allowed, Kay carried out the seeding program. During the mission, aircraft speed varied from 95 to 120 km/h when spreading seeds. There were some minor problems found due to installation that caused seeds to leak through a small gap. When this was fixed, the GFC calibration was correct. To overcome friction, GFC motors had to run at a speed higher than the target speed. It took only about a second to stabilize and meet the target speed. For this reason, there were some minor errors for short passes or passes having several cut-offs or segments. After two days of applications, Kay finished the seeding program successfully. The spray data was submitted to program supervisors for replay, verification, report and analysis.
Kay met with AgNav again after the program to provide feedback. Based on his inputs, AgNav engineers continued working on the GFC to improve its performance even further. A new impeller suitable for ultra-low spread rate was designed. The goal was to increase motor speeds to 10 RPM or more for better, precise control. The newly designed GFC will be ready in 2020 for aerial seeding applications. The aerial pine seeding of the Northwestern Ontario program proved that when facing challenges, companies could find a solution when working together. More than ever, it’s our responsibility to maintain forests in a good growth environment, keeping them a lush green, not only for our benefit, but also for generations to come.

Expedition Helicopters applying pine seeds for reforestation.

Pine seeded coverage on treated areas
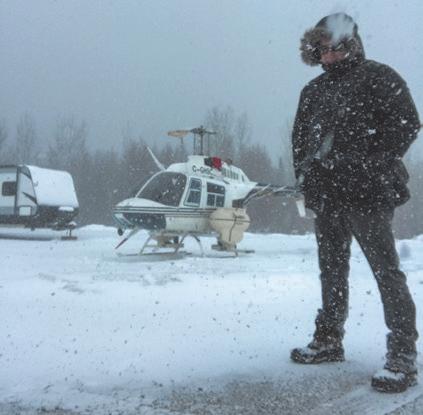
Wes Kay, Aerial Spraying Division Manager for Expedition Helicopters, during Canadian pine seeding project, April 2019.