
4 minute read
Auger Dan Delivers Loader Truck to Kenya
by Bill Lavender
The building platform for the Kenya-bound loader rig in Jonesboro, Arkansas. There’s a great amount of skill, and even art, to custom building an agricultural aviation aircraft dry loading truck. Probably one of the best known loader truck builders is Dan Whited’s Auger Dan LLC based in Jonesboro, Arkansas. Recently, those skills and most certainly artform by Auger Dan expanded into Kenya Africa.
While at an NAAA annual tradeshow in Savannah in 2017, Dan met with Toby Dunn of Farmland Aviation based in Nakuru, Kenya to discuss building an all-stainless steel custom loader unit with folding 12-inch auger and digital scales. Farmland Aviation was formed in 1984 and today operates a fleet of three AT-602s, three 510P Thrushes and one Cessna C-188 Ag Truck for a total of seven ag-aircraft. It is a fullservice aerial application business offering dry and wet applications. CP Products nozzles are used for normal and high volume applications, while Micronair rotary atomizers are used for low volume and ultra low volume applications. A Transland spreader is used for the majority of the dry applications. The primary crop treated by Farmland Aviation is tea, which requires about 10 dry applications of 600-800 kilograms/hectare (528-700 lbs/ac) that requires a two trips per application.
Farmland Aviation operates primarily in three countries; Kenya, Tanzania and Uganda. However, the company is currently busy with the recent locust outbreak in the “horn” of Africa that includes Kenya, Rwanda, Tanzania, Uganda and Ethiopia. Farmland Aviation aircraft are also flying in the Middle East to include Saudi Arabia.
Before purchasing the Auger Dan loader truck, Farmland Aviation had to disassemble loading equipment for transport on large trucks to cross country borders. This incurred tariffs going and returning back to the home base in Nakuru. Leaving equipment in a foreign country was not a viable option. With the Auger Dan loader truck, these issues are avoided, as the unit mounted on a truck is considered a complete mobile unit that can be driven across borders.
Auger Dan faced multiple challenges to custom build a loader truck for Farmland Aviation.

The Auger Dan loader unit built in Arkansas in action at its new home in Kenya Africa loading a Farmland Aviation Air Tractor.

The modified auger support frame that allows the cabover Mitsubishi truck’s cab to tilt.
For instance, the unit had to fit into a 45-foot long, high cube shipping container. This required partial disassembly. Considerations had to be made to fit the unit to a righthand steering, cabover Mitsubishi truck. The typical Auger Dan loader unit front support prevents a cab from being able to tilt. The design for Farmland Aviation had to allow for the cab to tilt.
Because the system uses hydraulics to power the auger and overall system, a PTO had to be found to fit the Mitsubishi model truck Farmland Aviation was using. Additionally, the scales for weighing the dry material had to read in kilograms, which is not normally found in the U.S.
Dan knew he had interesting challenges that Auger Dan LLC had not been confronted with before. For this reason, he used a local truck as a prototype to be sure all worked as it should. The front support was replaced with a rear (behind cab) selfsupport. The rear self-support and a small valley fabricated into the top of the cab resolved the tilt issue.

To be sure the Auger Dan loading system bound for Kenya would work correctly after many modifications, an identical unit to the Kenya-boundunit was mounted on a local ag-operator’s truck (Empty Pocket’s FlyingService / Osceola, Arkansas) for proof of concept.

The auger support frame is loaded into the 45-foot long, high cube shipping container first, before the auger, hopper and other components are loaded.
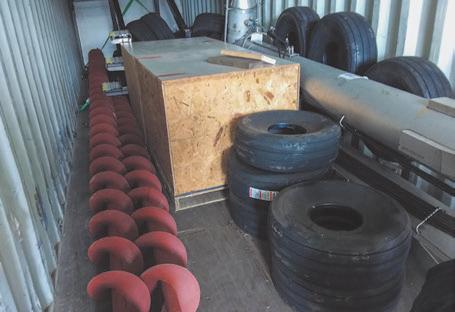
Middle: The auger support frame is up front, looking from the back of the shipping container with the auger and extra auger screws and a crate of parts tightly fitted into the shipping container.

Right: The last component of the Auger Dan loader truck system, the modified-to-fit stainless steel hopper, loaded into the shipping container.
The standard Auger Dan hopper is too large to fit in the shipping container. The hopper was redesigned using its standard length, but was narrowed to within one-inch of clearance on each side of the shipping container. The entire unit was built for fork liftable components palletized for ease of removal from the shipping container and installing on Farmland Aviation’s Mitsubishi truck.
The 12-inch auger used was a foldable, standard Auger Dan auger. This simplified the need for replacement parts. Dan knowing components that would most likely need replacement at some time in the future, tagged and sent extras. This included parts like the auger screw and bearings.
For the Mitsubishi truck, Dan had to machine and build drive shafts to the drive pad mounted hydraulic pump. He also had to build mounting brackets for the unit to be mounted on the truck; all without the actual truck onhand.
After numerous months of design and construction, Auger Dan finally was able to mount the unit to a prototype truck, checking to be sure all worked. Once Dan was satisfied the unit was ready for delivery, it was removed from the prototype truck, fully inspected, loaded into the shipping container and shipped to Kenya December 4, 2018.
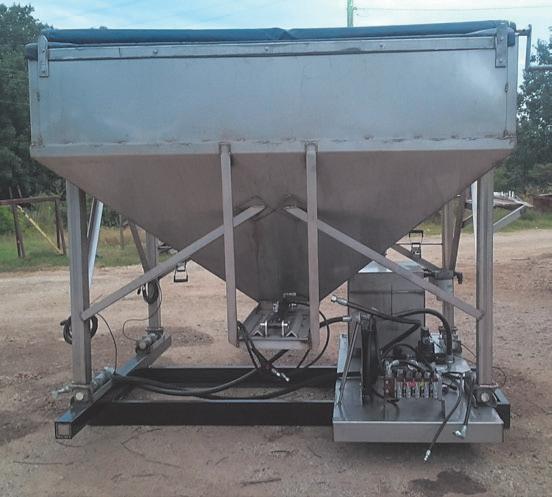
The all-stainless steel, modified Auger Dan hopper with hydraulics control levers ready for loading into shipping container headed toKenya, East Africa.
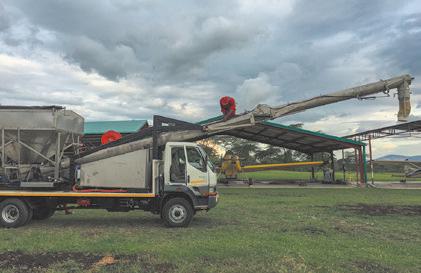
The Auger Dan “special Kenya build” loader rig mounted on Farmland Aviation’s Mitsubishi truck in Nakuru, Kenya.
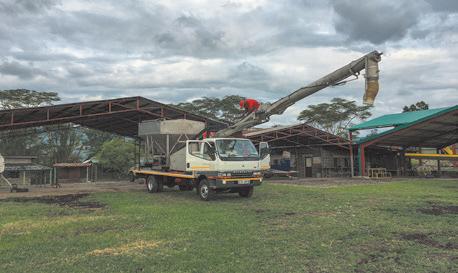
The Auger Dan “special Kenya build” loader rig mounted on Farmland Aviation’s Mitsubishi truck in Nakuru, Kenya.

The Auger Dan “special Kenya build” loader rig mounted on Farmland Aviation’s Mitsubishi truck in Nakuru, Kenya.