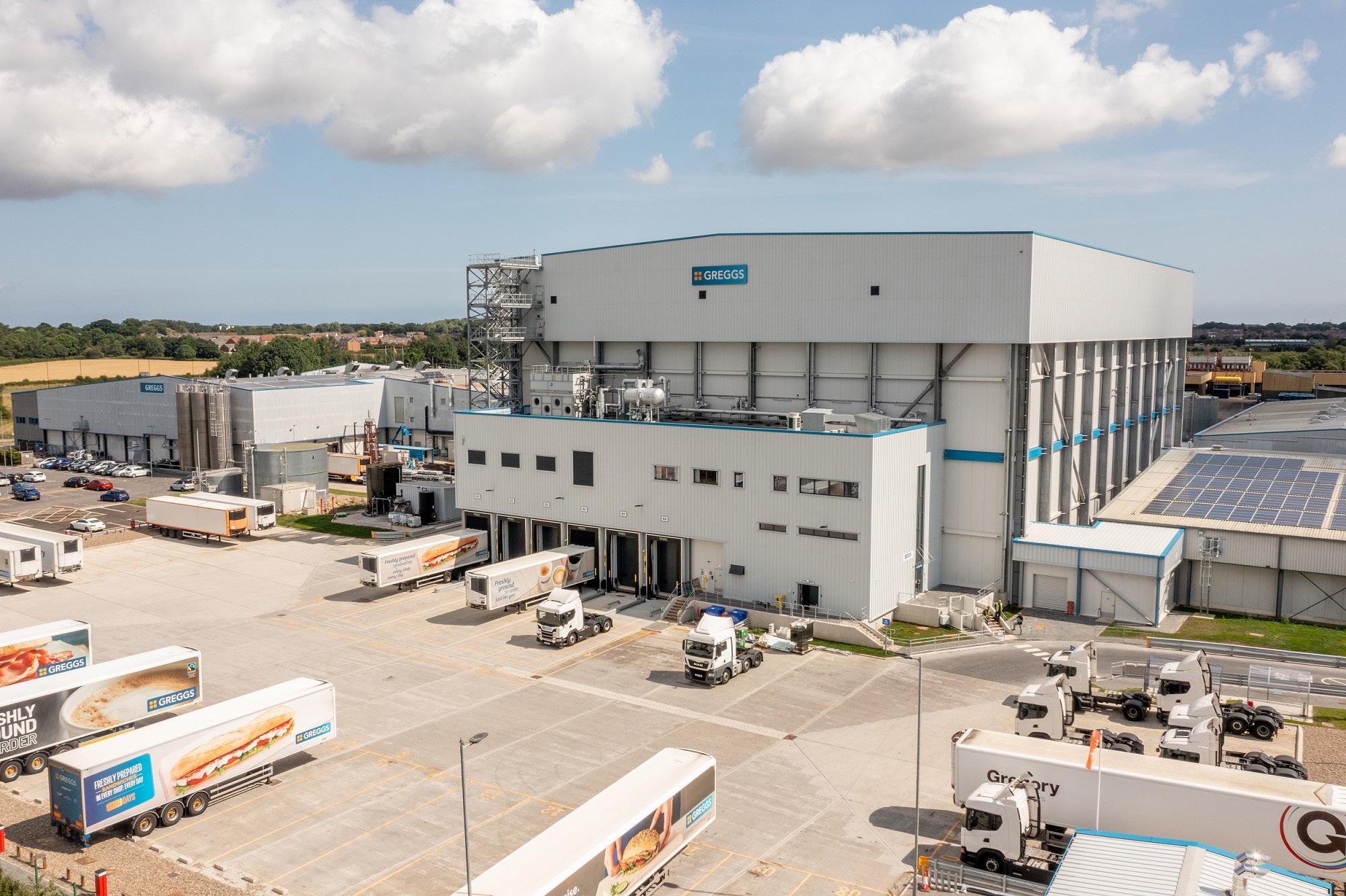
12 minute read
NEWS
CLEGG FOOD PROJECTS DELIVERS ‘COOLEST’ PROJECT YET FOR GREGGS
A brandnew automated cold store has been built by food and drink construction expert Clegg Food Projects for the UK’s leading bakery food on the go chain Greggs.
Located between two existing manufacturing units at Greggs’ Balliol Business Park in Newcastle Upon Tyne, the new automated high bay frozen cold store is 32m high and will be used for the bulk storage of frozen products ready for distribution to Greggs stores across the UK, supporting the firm’s growth plans.
Clegg Food Projects was appointed as the principal contactor for project, marking the 20th large scale CAPEX scheme completed for Greggs, with a cumulative value of almost £100 million.
John Moxon, business development director at Clegg Food Projects, said: “We have a great relationship with Greggs and really enjoy working with the team, so we’re delighted to have delivered another successful project.
“Following coordination meetings with the Greggs team and their specialist mechanical systems suppliers and logistics consultants, works started on site in October 2019. The construction sequence was continually updated and modified as details were confirmed, with extensive groundworks and piling installations carried out to cope with the high structure as well as the volume and weight of the products being stored in the building.
“Access routes alongside installation and commissioning plans were also jointly agreed and equipment was installed during the main construction works to meet the overall project timescales and ensure the project ran smoothly.”
The new cold store is a fully ‘lights out process’ facility and will free up space on site as well as enabling efficient and faster delivery of finished goods to be baked in store.
The facility also includes six new loading docks, nine levels of automation, and reduced oxygen fire suppression.
Senior project manager at Greggs, Peter Boughton, said: “We are very pleased with the cold store as it enables us to free up space in the existing facility and improve the distribution efficiency to our stores. Designed with sustainability in mind, this project highlights our commitment to Net Zero Greggs with carbon efficiency considered at every stage of the construction process.
“A first for Greggs, the automated warehouse demonstrates our commitment to innovation and investment in our sites and the business. The Clegg team brings a wealth of knowledge as well as an understanding of our business and our priorities when it comes to the delivery of projects.”
Clegg Food Projects is a national designer and constructor of food manufacturing and distribution facilities with more than 40 years’ experience in the sector. Part of Clegg Group, the firm has worked for a number of household brands, both in the UK and abroad, across a wide range of sectors including bakery, beverages, dairy, fresh and frozen produce and many more.
For further information visit www.cleggfoodprojects.co.uk or follow @CleggFoodP on Twitter.
PEEL PORTS NOMINATED AS PORT OPERATOR OF THE YEAR
Peel Ports has made the shortlist for Port Operator of the Year at the prestigious 2021 Multimodal Awards for the logistics industry.
As the country’s second largest port group, Peel Ports manages several key regional trading hubs for the UK economy, including major facilities in Liverpool, London Medway and Glasgow.
The nomination for the award comes on the back of a decade of strong financial performance and investment, which has seen EBITDA double over the last 10 years, by £131m (FY11) to £275m (FY21), and £750m+ invested on infrastructure over the past five years, contributing to significant employment, regeneration, and regional growth.
Mark Whitworth, CEO at Peel Ports said: “Our company has transformed since 2011 and we believe the long-term approach we have taken with the business is a significant factor in being recognised as one of the UK’s top operators. The investment we have made into our ports and our wider logistics business continues to improve services for customers, create jobs and support the wider economy.
“Despite the challenges of Brexit and the pandemic, our team has risen to every challenge and continued to provide first class services to the supply chain. That gives us a lot of confidence that we are on the right track and I’m certain that even more successful times are ahead of us.”
The 2021 Multimodal Awards recognises excellence in air, road, rail, maritime, and freight forwarding services, with categories voted for by readers of the Multimodal newsletter and exhibitors & visitors to Multimodal.
The awards ceremony will be held at the NEC in Birmingham on Tuesday 19th October 2021, with more than 650 guests from across the sector expected to attend.
Peel Ports Group is the UK’s second largest port group, owning and operating six of the UK’s most important ports (Liverpool, Heysham, Manchester Ship Canal, Medway (Sheerness / Chatham), Clydeport and Great Yarmouth). It also operates a container terminal in Dublin and owns BG Freight Line, which provides short sea container services between the UK, Ireland and mainland Europe and feeder services between the UK and Ireland. Peel Ports Group also owns Peel Ports Logistics (formerly Quality Freight UK), which provides chartering and port services from a 40 acre multi modal facility at Ellesmere Port in Cheshire.
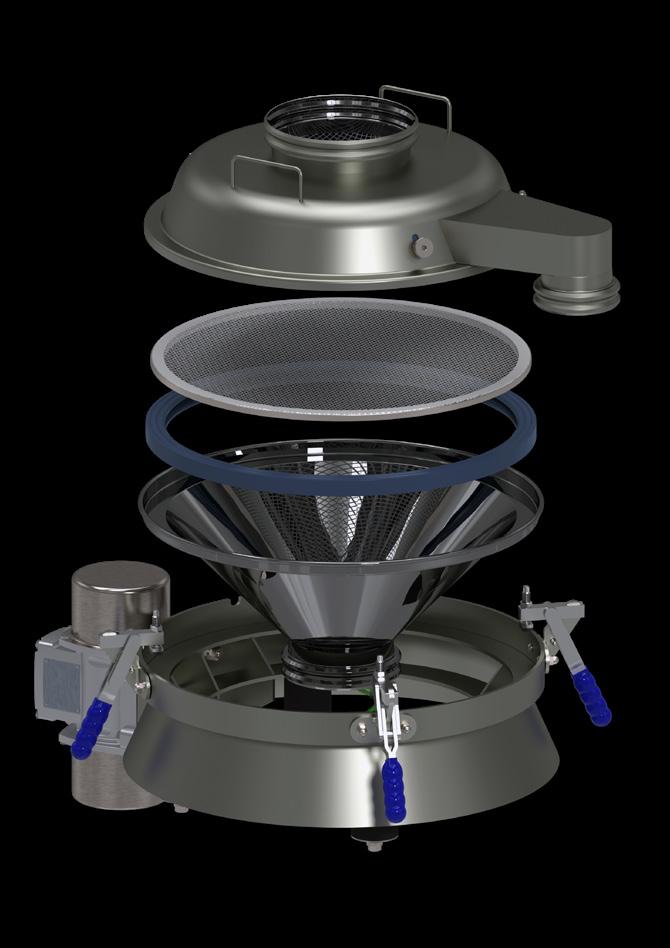
Peel Ports handles 70 million tonnes of cargo every year. 14% of the total UK major ports traffic flows through ports operated by the Group. Headquartered in Liverpool, it employs around 1,600 staff, and had revenue of £760m and EBITDA of £275m for the year ended 31 March 2021.
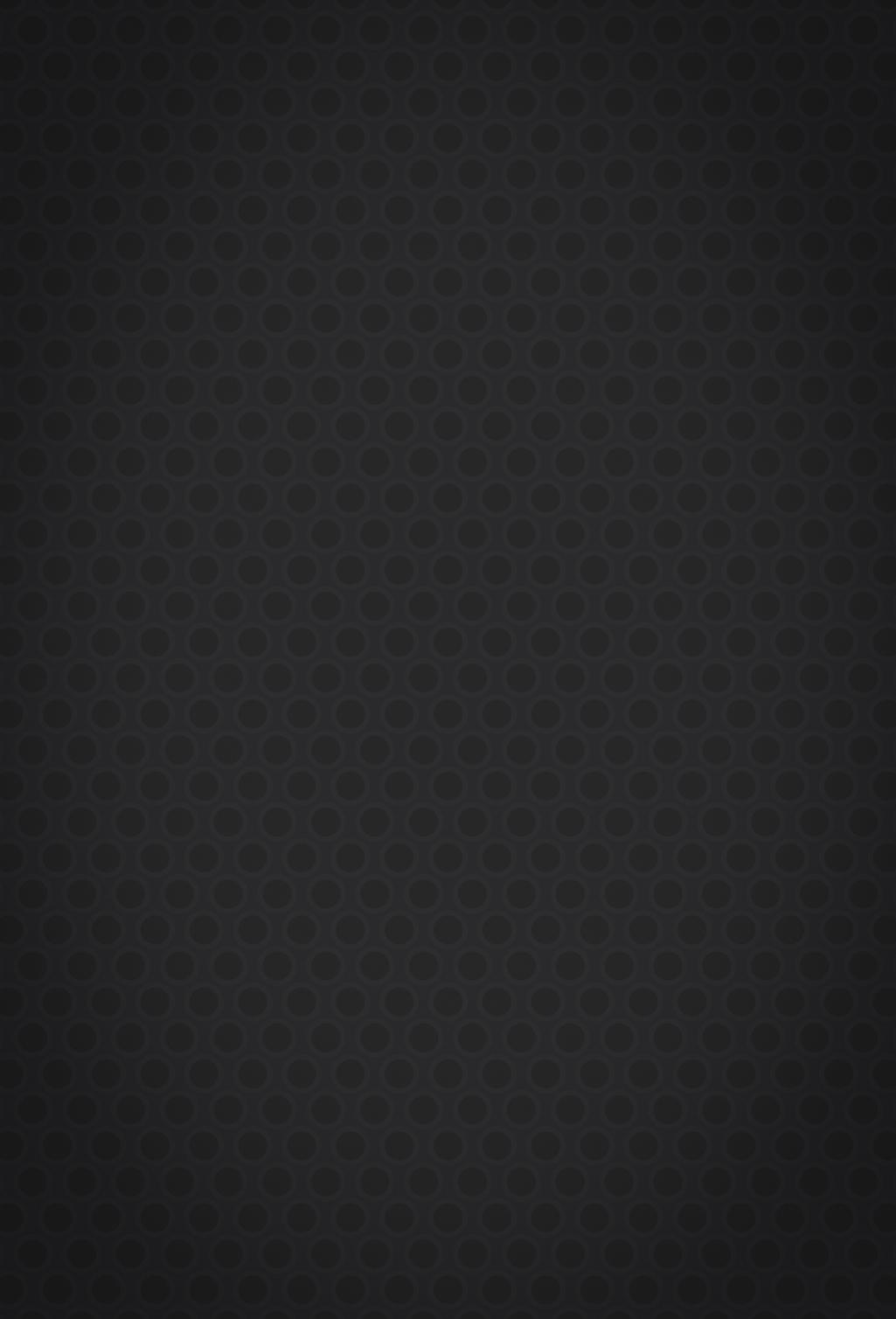
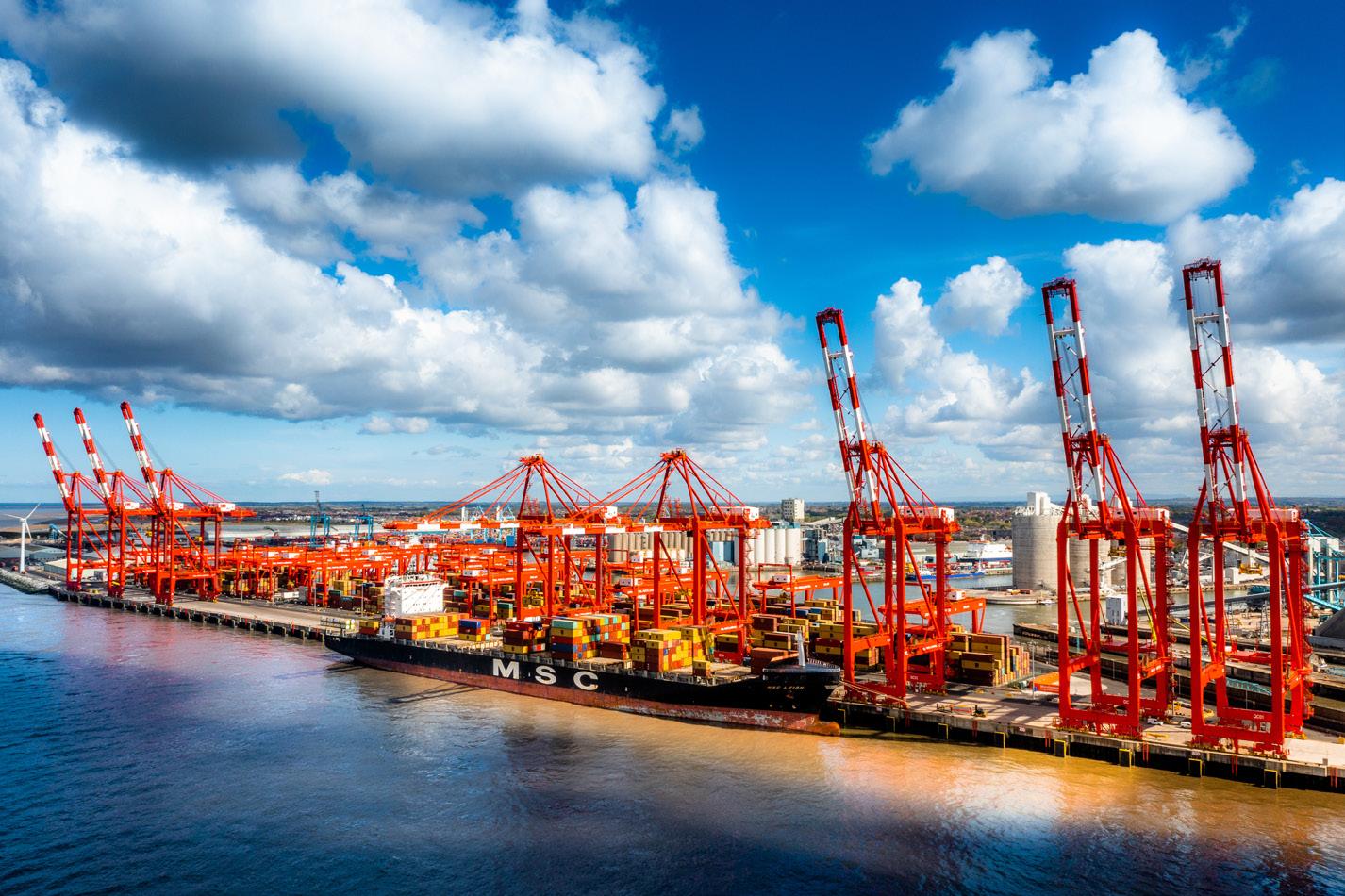
YOUR SIEVING & SCREENING PROCESS REDEFINED WITH SIEVMASTER BY FARLEYGREENE.
Sieves, screens, sifters. +44 (0) 1256 474 547 www.farleygreene.com enquiries@farleygreene.com
NORILSK NICKEL BUYS FIVE NEW BOBCAT ROTARY TELEHANDLERS
The new TR50.210 rotary telehandlers are the first in Russia -
MMC Norilsk Nickel, one of the leaders in the Russian mining industry, has purchased five new Bobcat TR50.210 rotary telehandlers and related attachments from the Bobcat Authorised Dealer in Russia, NAK Machinery. These are first of the new range of Bobcat rotary telehandlers to be purchased in Russia and the biggest order since their launch in December last year. A NEW SOLUTION BORN OUT OF A STRONG ONGOING RELATIONSHIP
In 2021, MMC Norilsk Nickel finished the reconstruction of its warehouse complex in Norilsk, a city in Krasnoyarsk Krai, located above the Arctic Circle. This project was part of a long-term modernization of the Unified Warehouse Facility (UWF) run by the company. This facility supplies material and technical resources to all the production departments of the Polar Division, subsidiaries and third-party organizations of the Norilsk Industrial District.
One of the main elements of the modernization was the renovation of the equipment fleet, including the telehandlers. New machines were needed to improve the speed and quality of cargo handling. Given the extreme climatic conditions in the region beyond the Arctic Circle, the company needed reliable special equipment capable of working in any situation, even when the average winter temperature is around −30 °C.
Specialists at MMC Norilsk Nickel have been working with Bobcat products for a long time and have first-hand experience with the durability of these machines. This fact together with the long-term relationship with Krasnogorskbased NAK Machinery, the largest Authorised Bobcat Dealer in Russia, predetermined the choice of the Bobcat new TR50.210 model. These rotary telehandlers, launched in December 2020, are unique in the Russian market. MMC Norilsk Nickel also purchased a range of attachments for the new machines, including light material buckets, pallet forks and a crane jib.
“The delivery of the new Bobcat TR50.210 machines is a first for our company in rotary telehandlers, but we are confident that the customer will appreciate this new line, and we will receive new orders for such equipment in the future,” said Andrey Gerasimov, Bobcat Brand Manager at NAK Machinery.
GROWING MARKET FOR ROTARY TELEHANDLERS
Evgeny Supletsov, Country Manager for Russia & CIS for Bobcat said: “In the EMEA region, the concept of rotary telehandlers is gaining popularity and in the last five years showed strong growth from 1035 units in 2015 to 1809 units in 2020. In fact, about 85% of all global sales of these machines came from EMEA, and that is why Bobcat has brought new models of this class to the market.

“We are delighted that our long-time partner MMC Norilsk Nickel became one of the first customers for these new machines. This demonstrates a high level of confidence in Bobcat’s special equipment, and we are sure that the quality of our machines will meet the harsh conditions in which they will have to work.” CHALLENGING LOGISTICS THROUGH NORTHERN SEA ROUTE
Thanks to the close cooperation between Norilsk Nickel and NAK Machinery, the companies were able to successfully coordinate the complicated process of delivering the new equipment. Norilsk is not connected to the mainland by roads, so the machines could only be delivered by the Northern Sea Route.
In the first part of the journey, the telehandlers were transported by trailers to the seaport of Murmansk, and then went by sea to the port of Dudinka, from where they finally reached their destination on trailers again. In spite of such a difficult and long route, the delivery went according to plan and without any delays. A NEW MULTIFUNCTIONAL RECRUIT
Bobcat rotary telehandlers have a number of features that make them versatile and suitable for a variety of industries and applications. The possibility to rotate the platform through 360° allows the operator to move a load anywhere within the reach of the boom without having to change the machine’s position. This is ideal in densely built-up cities or in warehouses, where manoeuvring space is limited. Versatility is also offered by the wide range of Bobcat attachments for the rotary telehandlers, which allow the customer to optimize machines for different tasks.
The Bobcat TR50.210 is the middle model in the new range of rotary telehandlers, designed specifically for the Russian and CIS markets, but also for use in Europe, the Middle East and Africa. The lift capacity of the TR50.210 is 5 tonne and it can lift loads up to a height of 21 m.
FEATURES OF THE MACHINE
Like all the new rotary telehandlers, the Bobcat TR50.210 is highly automated, which simplifies the work of the operator, as well as enhancing the reliability of the machine and increasing safety on site. For example, the 134 HP engine can automatically adjust its speed depending on the load, and the rear axle is equipped with automatic hydraulic locking.
The cab is also fitted with a wide range of features designed to increase comfort and therefore productivity. For example, its patented design includes an overpressure and fullflow air filtration system, as well as air conditioning, which allows the operator to work in difficult weather and environmental conditions. The machine’s fully glazed cab is offset to the side, giving the operator superior visibility. At the same time, a large touchscreen display, intuitive controls, certified ROPS/FOPS protection systems, an adjustable steering column and a comfortable, fully adjustable seat make operating the machine easy and safe.
Thanks to RFID technology, the loader automatically recognizes attachments while loading and displaying a chart of the load characteristics. This allows the machine to be ready to work almost immediately, and the displayed diagram helps the operator to keep track of the load’s centre of gravity.
For more information about Bobcat and its products, visit www. bobcat.com.
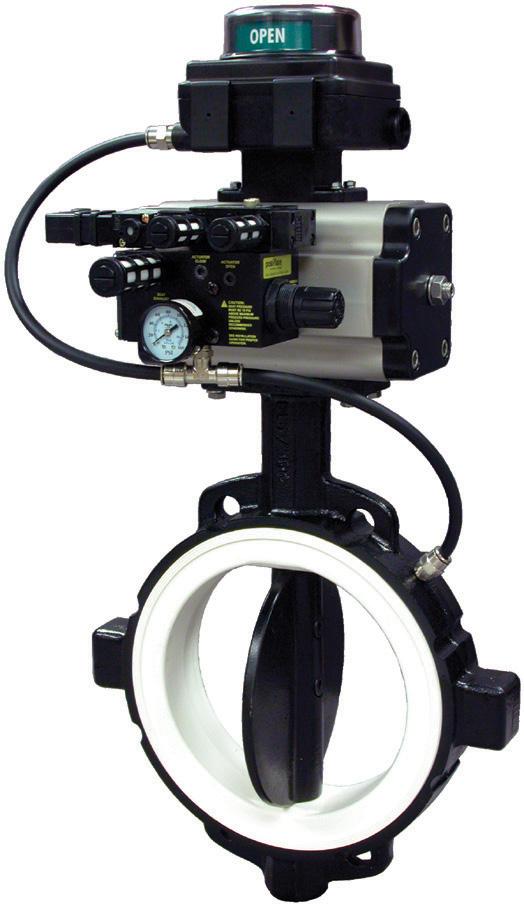
Other Valves Fight Friction, We Designed it Out Unlike other valves that seal with friction, Posi-flate’s unique butterfly valve uses an inflatable seat to seal with air pressure. Thus it requires less torque and a smaller actuator, resulting in lower cost. Plus, the seat automatically compensates for wear, providing longer life. Some users have reported over six million cycles and the valves are still going strong. • Less friction • Low torque • Low maintenance • Lower actuator costs • Longer valve life • More reliable Tel: +44 (0) 1908 622366
www.posiflate.com
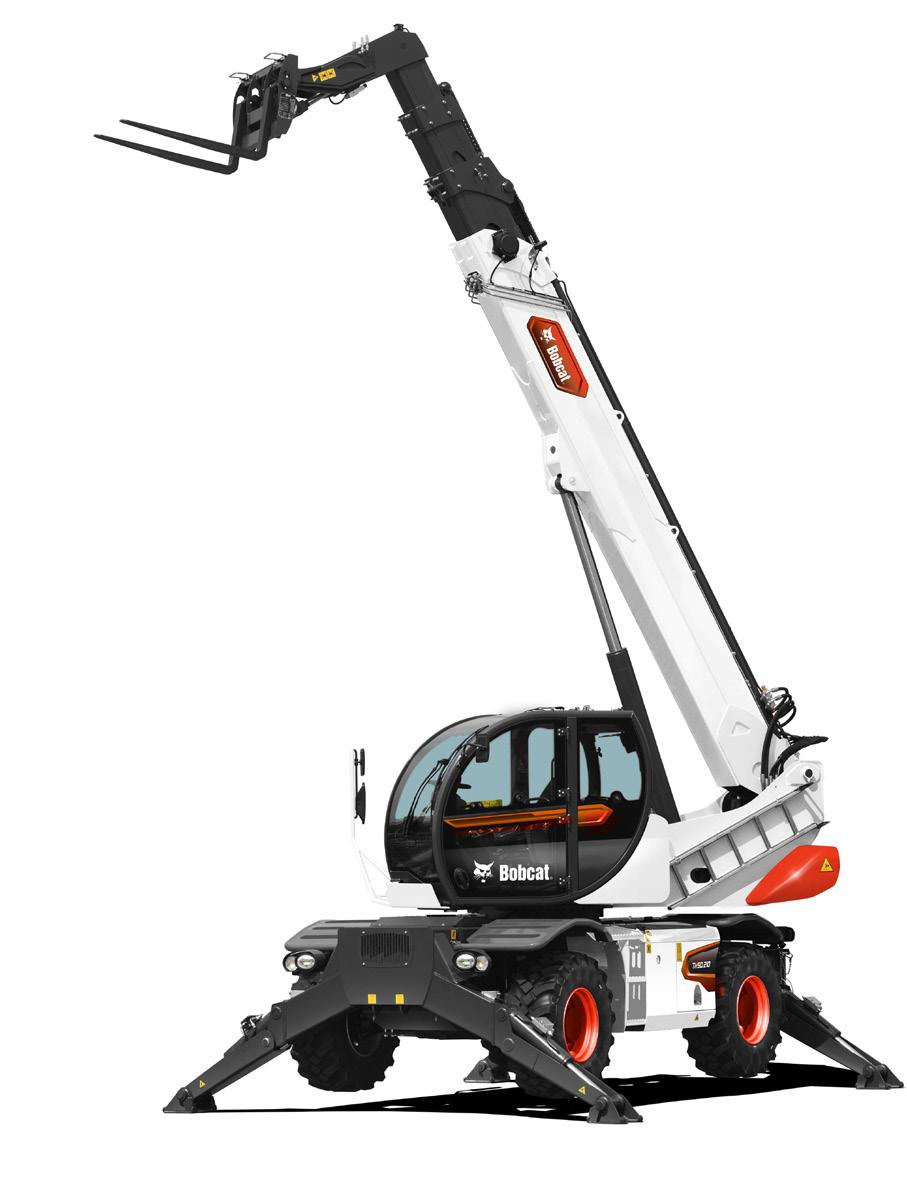
BIGCHANGE MOBILE WORKFORCE TECHNOLOGY DRIVES BUSINESS GROWTH FOR BREWSTER BROS
Recycled aggregates and waste management specialist Brewster Bros. has doubled its business with the help of the latest mobile workforce management technology from BigChange. The cloudbased system has completely automated the sales process, from initial enquiries through to order fulfilment and invoicing, as part of a move to paperless working. Providing an endto-end solution, BigChange is also reducing the back-office administration required to manage the mobile operation and is improving customer service with an online booking and tracking portal.
“We initially introduced BigChange’s JourneyWatch product when we took over the company a few years back to monitor driver behaviour and track our vehicles,” commented Scott Brewster, Managing Director of Livingston-based Brewster Bros. “We just needed to know who was doing what, where and when! However, after six months we realised the full jobbing system has so much more to offer. BigChange is now fundamental to our business and has helped us grow the operation by around 100 per cent from 2018 to 2020.”
A resource management company for the construction industry, Brewster Bros operates across the central belt of Scotland. Offering environmentally compliant waste disposal as well as supplying quality recycled aggregate products, Brewster Bros. can transport up to 500,000 tonnes of waste and product per year in its fleet of HGV tippers.
“Heavy bulk haulage is quite different from other types of haulage as it is local, high frequency work and our drivers have to return to base and/ or visit the same customer site multiple times per day,” continued Brewster. “Prior to BigChange we were heavily reliant on large volumes of paperwork which could be incorrect, incomplete or even go missing, and therefore consumed a significant amount of back-office resource to support.
“Using BigChange, we have complete visibility of the whole transport function of the business. We know where our vehicles are, how they are being driven and even when they tip! We capture this data, including complete proof of delivery and waste transfer note evidence, to improve our customer service offering, ensure regulatory compliance and expediate our accounting, which is improving cashflow and in turn fuelling continued business growth.”
Providing a single platform CRM, Job Scheduling, Vehicle Tracking and Mobile Workforce App, the BigChange solution is further supporting Brewster Bros as the business continues to expand. It is hoped the recently introduced BigChange powered portal will help customers to self-serve, booking and tracking collections and deliveries online, and automating waste transfer and delivery notes and invoices. www.bigchange.com
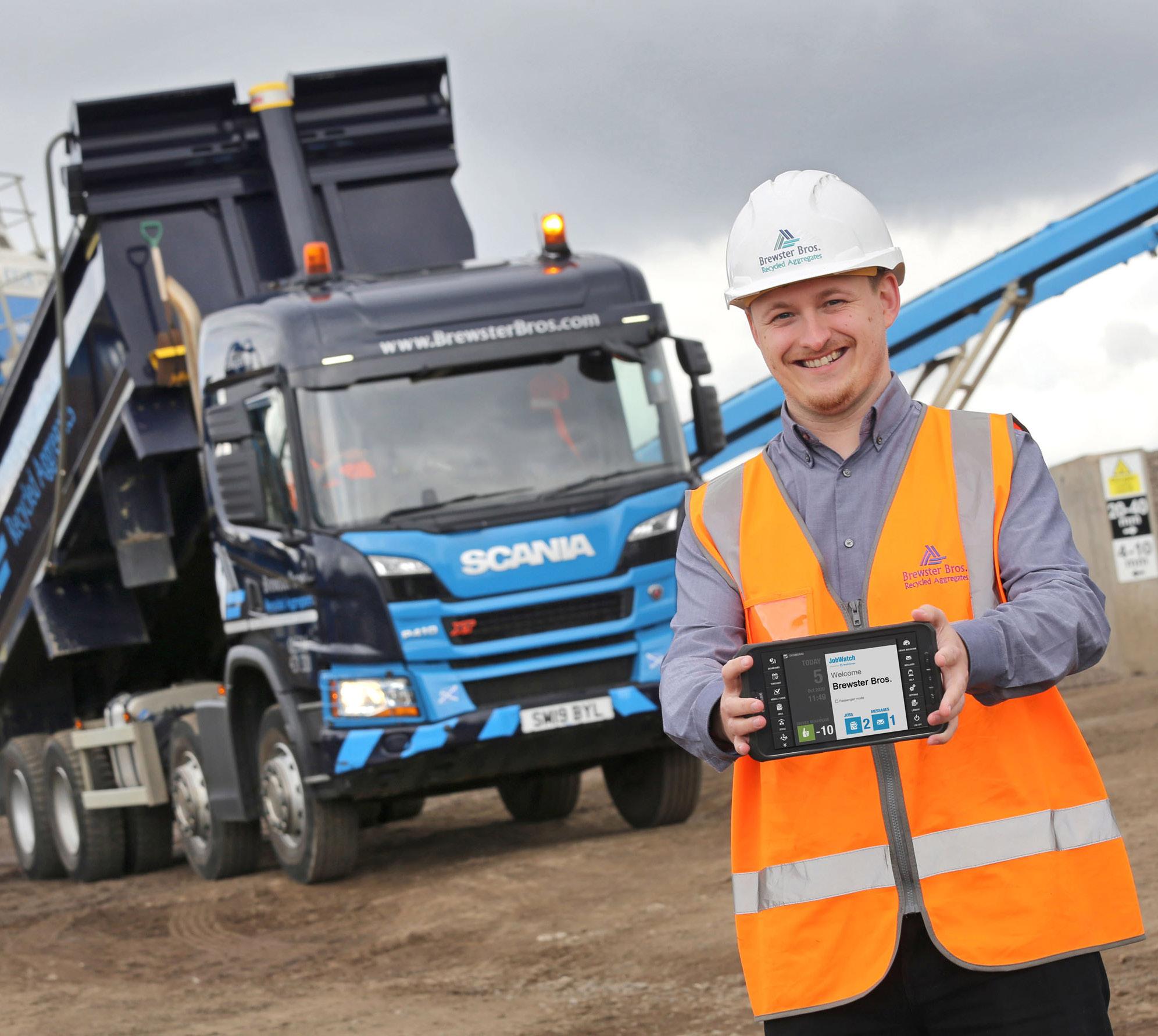