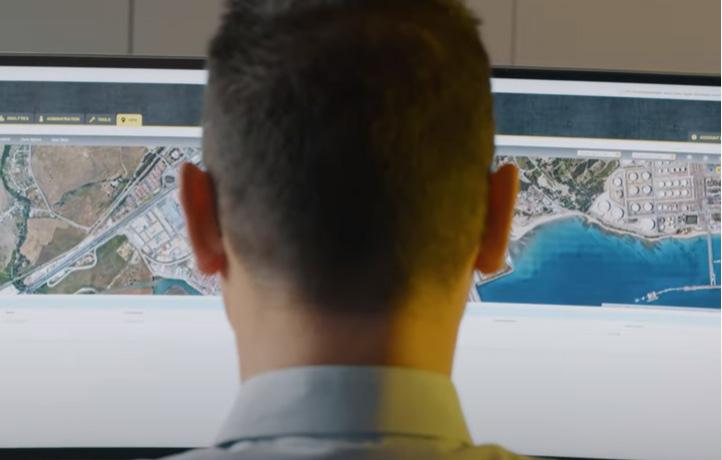
13 minute read
BULK MATERIALS HANDLING
HYSTER® TELEMATICS KEEPS LIFT TRUCK DRIVERS ON TRACK FOR HEAVY METAL HANDLING
Hyster has provided a new fleet of forklift trucks and ReachStackers featuring the Hyster Tracker wireless asset management system to support tough metal handling operations at the Port of Oxelösund in Sweden.
The Port of Oxelösund specialises in receiving big vessels and has a dedicated steel port. Here, metals, mostly coils, arrive at the port by trains, which are unloaded with a crane. Then, forklifts carry the goods to the port cranes, which load coils onto the ships.
When the port was recently looking to update its fleet, local Hyster® distribution partner in Sweden, Nordisk Truck-Trans and Hyster worked with the customer to create a total application-specific solution, including the Hyster Tracker telematics system.
“The beauty of Hyster Tracker is that it has a wide range of functions for effective fleet management,” says Dmitry Dubrovsky, Big Truck Manager for Hyster Europe. “This enables applications to utilise the features that are relevant to their specific operation, so they can see the bigger picture, gain insights, and reduce costs.”
For instance, at the Port of Oxelösund Hyster Tracker is fitted to Hyster® H32XM-12 and H20XM-9 lift trucks, with 32 and 20-tonne capacities, as well as Hyster® RS46-36CH ReachStackers to limit drivers, so only those who are correctly authorised can drive a truck during working hours. Drivers present a card to a reader by the steering wheel and the system then
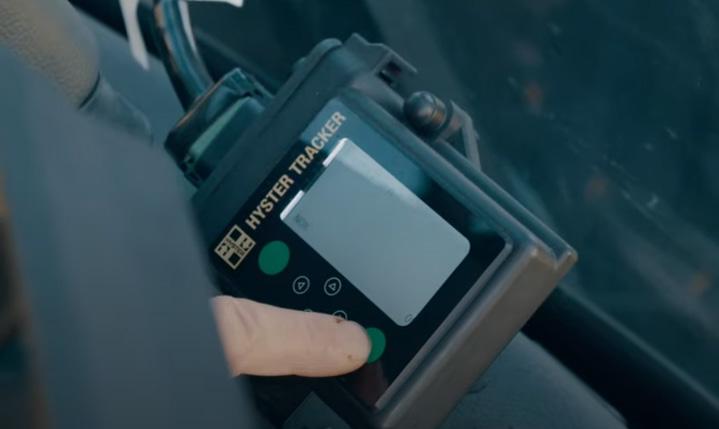
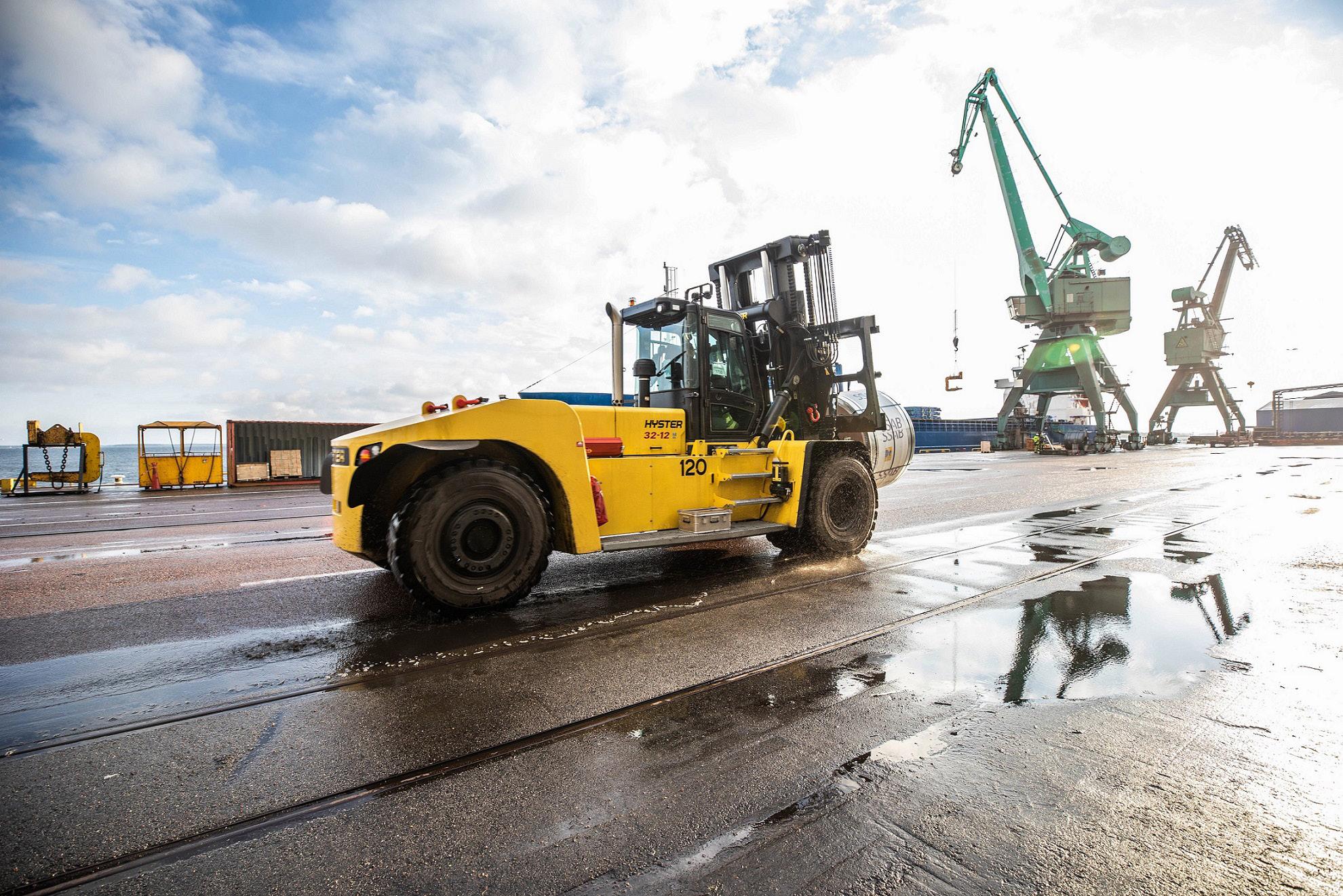
confirms whether the driver has the right license to operate the particular truck. This gives the busy metal handling application increased security.
“With Hyster Tracker, operators at the Port of Oxelösund also have a daily pre-use check to complete that appears via an in-cab display,” says Erik Progrebnjak, sales representative for the local Hyster® distribution partner, Nordisk Truck-Trans AB. “This check-up must be done before the truck is used and then at intervals after the vehicle has started.”
The Port can also see how the vehicles move on a map. This allows the operation to analyse potentially difficult traffic situations and see how the trucks are being driven.
“Increased productivity starts by knowing what your trucks are doing,” says Dmitry Dubrovksy. “With truck utilisation analysis, Hyster Tracker helps enhance fleet management and workforce productivity. It provides data-driven insights to help applications fine-tune the fleet size and composition to keep operations running efficiently.”
Hyster Tracker, which can be accessed on a Desktop portal or via a free app, also provides diagnostics and tracking which can help address problems before they arise by monitoring equipment performance.
“Even though most drivers think they are efficient, Hyster Tracker can show the facts,” explains Erik Progrebnjak. “There are sensors that detect if an impact occurs. It also warns if the speed limit is violated.”
Hyster Tracker telematics also helps applications to streamline maintenance scheduling, conserve energy and reduce unnecessary equipment wear. Battery and tyre pressure monitoring add-ons are available to further help manage maintenance and costs and optimise equipment performance.
For more information on fleet management solutions for metal handling applications, or to locate a local Hyster® dealer, visit www.hyster.com
IF YOU ARE INTERESTED IN SUBSCRIBING TO BST MAGAZINE, PLEASE DO GET IN TOUCH BY VISITING WWW.BULKSOLIDSTODAY.CO.UK OR EMAILING US AT BST@ABBEYPUBLISHING.CO.UK
DOOSAN LAUNCHES NEW DL420CVT-7 WHEEL LOADER
New Model in Award-winning DL-7 Series Features Fuel-Saving CVT System -
As part of the company’s award-winning DL-7 series, Doosan has launched the new DL420CVT-7 Stage V compliant wheel loader equipped with a Continuously Variable Transmission (CVT). With a maximum bucket capacity of 4.5 m3, the Doosan DL420CVT-7 wheel loader is intended to meet a wide range of material-handling needs from loading and transporting granular material (such as sand or gravel) to quarrying, mining, construction, demolition, industrial, waste and recycling applications.
A CVT transmission is the result of a permanent combination of a hydraulic technology and a mechanical technology which provides a smooth and continuous speed variation. The CVT design combines the benefits of a hydraulic mechanical transmission and a hydrostatic transmission in the same machine. It allows the DL420CVT-7 to automatically transition from hydrostatic power at low speed to the mechanical system to operate at higher speeds.
By combining the two types of transmission, the CVT technology ensures high loads can be carried at low engine speeds with high dynamics for an optimum wheel loader operating cycle. The DL420CVT-7 therefore provides an increase in machine performance for operators working in digging, loading and lifting applications. For most tasks, operators will utilise the hydrostatic part of the transmission, which offers greater fuel efficiency in low-speed applications. The combination of the two transmissions is automatic and fully transparent for the operator.
UP TO 15% ADDITIONAL FUEL SAVINGS
The complete driving range, forwards and in reverse, is controlled by the CVT system. Low engine speeds ensure a high efficiency and the highest driving comfort irrespective of the traction speed. The power splitting continuously variable technology facilitates moving off softly and hydraulically. Furthermore, with the CVT, a fuel saving of up to 15% can be achieved.
With an output of 240 kW (326 HP) of power at 1800 RPM, the Scania DC09 engine in the DL420CVT-7 provides generous torque at low RPM and meets Stage V emission regulations without the need for exhaust gas recirculation (EGR), through the use of selective catalyst reduction, diesel oxidation catalyst and diesel particulate filter (DPF) aftertreatment technologies. The soot cleaning cycle on the DPF has been improved to over 6000 h and the operator is fully informed about the status of the DPF via a soot level indicator on the new touchscreen display in the cab.
NEW AWARD-WINNING DESIGN
The new DL420CVT-7 features the same awardwinning external design common to all models in the DL-7 series, creating a three-dimensional effect with an innovative cover shape and a vibrant, dynamic image for the range. It has already received great acclaim globally, winning Germany’s 2020 iF Design Award, one of the world’s top three design awards and the ‘Best of the Best’ category in the Korean PIN UP Design Awards.
INCREASED PRODUCTIVITY AND VERSATILITY
The Z-kinematic lift arm on the DL420CVT-7 delivers high breakout forces and lifting capacities, especially for heavy materials, and a large dump angle for efficiently unloading sticky materials. An optional high lift arm is available where higher dump heights and increased versatility are required. Doosan is also offering a wider choice of options to provide more work tools for a better match with applications, further increasing output.
Like all DL-7 wheel loaders, the DL420CVT-7 loader has smooth and responsive hydraulics and auxiliary hydraulic connections. It is equipped as standard with a 3rd spool valve with settable flow and detent function, providing a constant flow for hydraulically driven attachments. Operators can easily and comfortably control hydraulic attachments via the proportional switch on the joystick. Various bias and radial tyre options are also available from leading global manufacturers, to cover the widest possible range of conditions and applications.
In addition, the new wheel loader can be ordered with a heavier optional counterweight, depending on the application.
EXCELLENT OPERATOR VISIBILITY
The new cab on the DL420CVT-7 offers a greatly improved field of vision for the operator, with blind spots around the cab minimized and a 14% larger glass window area compared to the previous DL-5 model. The DL420CVT-7 wheel loader also offers the option of electrically adjustable rear view mirrors for added safety. Full LED working lights are installed on the cab (four on both the front and rear as standard, with the option of six each at the front and rear). For higher pedestrian safety, the LED lights on the rear bonnet have an automatic strobe function to indicate when the wheel loader is reversing.
An air compressor with air blower is available as an option - fitted in the cab for easy access, this is a powerful tool that can be used to clean the cab whenever necessary.
NEW SPACIOUS ERGONOMIC CAB DESIGN
Inside the cab, the DL420CVT-7 provides significantly enhanced operating comfort, an enhanced steering system and advanced electronic controls. Using the new Doosan Smart Key system on the control panel in the cab, the operator can start the machine using a keyless device, helping to prevent machine theft. The Smart Key system provides remote door control, door lock and unlock, door release, searching and other functions. The control panel also includes two USB sockets.
The new cab has a Grammer Actimo XXL seat with fully adjustable horizontal and vertical suspension settings, a pneumatic lumbar function and seat heating as standard. There is a 3-point safety belt with alarm icons on the new Doosan Smart Touch 8 inch touchscreen monitor and on the gauge panel, which features a new layout and anti-reflective glass.
The new EMCV (Electric Main Control Valve) joystick fully integrated in the armrest is another standard feature in the cab, providing the operator with smoother and precise controllability of the lift arm and attachments on the wheel loader. Features available via the EMCV system include Automatic Return-to-Dig, Bucket Tilt Kick-out and the Bucket crowd stop position and shock prevention for higher operator comfort.
Designed to give the operator more precise control with a shorter lever stroke, resulting in less fatigue, the sensitivity of the ergonomic joystick control can be set and altered according to operator preferences using the new Doosan Smart Touch touchscreen monitor. User-friendly and easy to read in all conditions, the new touchscreen provides all the important settings and information the operator needs in one place.
Included in the information at the operator’s fingertips on the touchscreen is the feed from the rearview camera, the weighing system, the HVAC controls (heating, ventilation and air conditioning), Radio & Bluetooth devices (music streaming, hands-free) and the operator help function.
Overall, the redesigned interior offers a much larger, quieter and more comfortable operator environment, which improves safety and productivity and helps the operator work with high concentration. The operator also has increased leg room, an enlarged storage area and cool-box position and an improved air conditioning system (with optimized air circulation).
HIGHER PERFORMANCE
The LIS (Load Isolation System) provides a smoother ride and higher comfort for the operator, as well as higher productivity due to improved stability when the wheel loader is moving. The lift arm is cushioned by a hydro-pneumatic accumulator linked to the lift hydraulic system, acting as a shock absorber. The benefits include reduced cycle times, higher performance and better fuel efficiency while carrying out load and carry applications.
With heavy duty HDL axles as standard and enhanced traction with Differential Hydraulic Lock (DHL), the DL420CV-7 wheel loader operates exceptionally, especially in high-load environments. The differential hydraulic 100% lock can be engaged at full torque automatically without any action from the operator.
Optional independent oil cooler circuits for the front and rear axle ensure low oil temperatures, provide oil filtration and extend the lifetime of axle components, especially for demanding applications, such as long distance load and carry in high ambient temperature conditions.
Improvements have been made throughout the powertrain, to provide operators with best-in-class driveability and faster driving, reaching the 38 km/h maximum speed quickly and safely.
FULL 3-YEAR/5000 H WARRANTY AS STANDARD
The upgraded hydraulic system and major parts ensure greatly improved durability and maintainability. Providing increased peace of mind for the customer, the high reliability and quality of the new DL420CVT-7 wheel loader is backed up by a standard full 3 year/5000 hour warranty.
DOOSANCONNECT FLEET MANAGEMENT SYSTEM AS STANDARD
The DL420CVT-7 wheel loader is factoryinstalled with the latest DoosanCONNECT TMS2.0 state-of-art wireless fleet monitoring system. The DoosanCONNECT system is a tool designed specifically for the Doosan range, providing comprehensive information about machine performance in a dual mode (satellite, Mobile network).
The DoosanCONNECT system offers a web-based fleet and asset management solution which is very useful for managing the performance and security of machines and promoting preventative maintenance.
For more on Doosan construction equipment, please visit the website: www.eu.doosanequipment. com

A new Flexicon Mobile Bulk Bag Discharger with Mobile Flexible Screw Conveyor allows dust-free discharging of bulk solid materials and conveying to downstream process equipment or storage vessels throughout the plant.
Mounted on locking castors, the BULK-OUT® BFF Series discharger has four adjustable extension posts to accommodate bulk bags 915 to 2135 mm tall. The removable bag-lifting frame with Z-CLIP™ strap holders allows bulk bags to be attached at ground level, then forklifted into receiving cups on the discharger frame.
A SPOUT-LOCK™ clamp ring atop a pneumatically-actuated TELE-TUBE™ telescoping tube secures the clean side of bag spout to the clean side of the equipment, and exerts continuous downward tension on the bag as it empties and elongates, promoting flow and evacuation. A vent port with filter sock contains dust.
Additional flow is afforded by FLOW-FLEXER™ bag activators that raise and lower opposite bottom sides of the bag at timed intervals into a steep “V” shape, and top-mounted POP-TOP™ extension devices that elongate the entire bag, promoting total discharge with no manual intervention.
The discharge housing of the mobile flexible screw conveyor is supported by a mast affixed to the mobile discharger frame, allowing the transfer of free- and non-free-flowing bulk materials to multiple destinations.
The flexible screw is the only moving part contacting material and is driven by an electric motor beyond the point at which material is discharged, preventing material contact with seals.
The entire unit can be rolled to a cleaning station. A lower clean-out cap on the conveyor tube can be removed to flush the smooth interior surfaces with steam, water or cleaning solutions, or to fully remove the flexible screw for cleaning and inspection.
The system is available in carbon steel with durable industrial coating and stainless steel material contact surfaces (shown), or in all-stainless steel finished to industrial, food, dairy or pharmaceutical standards.
Flexicon also manufacture other configurations of bulk bag dischargers and flexible screw conveyors, as well as tubular cable conveyors, pneumatic conveying systems, bulk bag conditioners, bulk bag fillers, bag dump stations, drum/box/container dumpers, drum fillers, weigh batching and blending systems, and engineered plant-wide bulk handling systems with automated controls.
For information contact Flexicon Europe Ltd, +44 (0)1227 374710, sales@flexicon.co.uk, www.flexicon.co.uk

AJAX AGITATED SCREW FEEDER FOR LIANHETECH EUROPE
Solids handling specialist, Ajax Equipment, has supplied leading fine chemical manufacturer, Lianhetech Europe, with an Alloy 22, extremely corrosion resistant high nickel alloy, agitated screw feeder for Lianhetech Europe’s Seal Sands production site near Middlesbrough, UK.
The feeder receives batches of product from a centrifuge into its horizontal cylindrical hopper section fitted with a multi-bladed agitator that sweeps the body internal diameter and along the full length to disturb time consolidation and sweep product into an integral LynFlow™ ribbon screw feeder that extracts along the full length to regulate feed into the site’s dryer. The agitated feeder is ATEX compliant for Zone 1/21, category 2 equipment (inside and out) with N2 purge and was water fill tested as part of successful Factory Acceptance Tests (FAT) at Ajax’s Bolton, UK works. The agitated screw feeder also features multiple sight glasses enabling monitoring at several points.
“Following initial meetings and the specification of Lianhetech’s requirements, Ajax provided a bespoke design for the screw feeder and supplied the unit within the challenging timelines of the project. Ajax takes the time to understand the requirements of each specific process rather than supply a generic design and this is one of the key reasons that ensures the units can do the job from the start,” said Imran Khaliq, engineering manager, Lianhetech Europe.
“Ajax designs its agitated screw feeders to each customer’s process needs including the flowability of the material, required discharge rate and holding capacity,” commented Eddie McGee, managing director, Ajax Equipment. “Due to the process materials involved the construction required Alloy 22 which is noted for its excellent resistance in a wide range of chemical environments. It is significantly harder than stainless steel so working to shape and of course polishing for smooth flow conditions was quite the task which Ajax duly met.”
For more information on Ajax Equipment agitated screw feeders call +44(0)1204 386723, email: sales@ajax.co.uk and visit www.ajax.co.uk.
