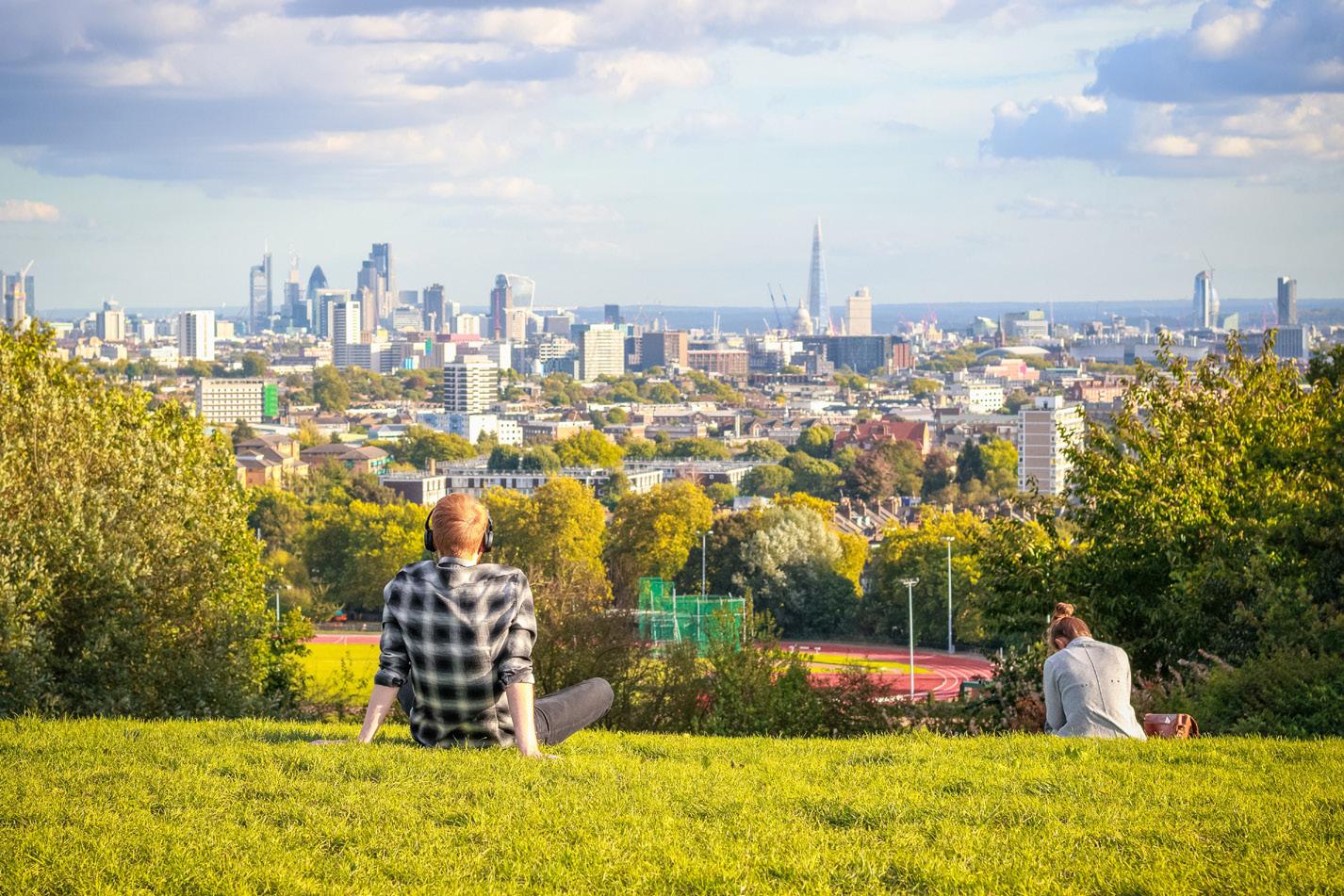
20 minute read
NEWS
AGGREGATE INDUSTRIES URGES BUSINESSES TO PRIORITISE SUSTAINABLE MATERIALS AMID NEW NET ZERO RULES FOR UK GOVERNMENT CONTRACTS
• From September, firms bidding for £5m+ government contracts must be committed to Net Zero by 2050 • Leading construction materials supplier Aggregate Industries says low-carbon concrete and asphalt will be vital for successful tenders • Last year, parent company LafargeHolcim became first construction materials firm to sign Net Zero Pledge
Leading construction materials supplier Aggregate Industries has welcomed the news that firms looking to bid for UK government contracts worth more than £5m will need to prioritise sustainable building materials as a new rule requires them to commit to achieving net zero carbon emissions by 2050.
Earlier this month, the UK government announced that from September it will require businesses to commit to net zero by 2050 and publish clear and credible carbon reduction plans before they can bid for major government contracts1. Contactors will also need to demonstrate how they will manage their impact on the environment throughout the contract.
Welcoming the new measures as a ‘major leap forward for sustainability’, Aggregate Industries, whose parent company LafargeHolcim last year became the first construction materials company to sign the Net Zero Pledge, is pressing firms to make the most of emerging sustainable materials such as low-carbon concrete and asphalt.
Kirstin McCarthy, Sustainability Director at Aggregate Industries, comments: “Given the billions of pounds the government spends on construction schemes each year, these new rules are a major leap forward for sustainability – positioning the UK as a worldleader.
“However, it also means that companies hoping to win these lucrative government contracts must demonstrate a credible, robust and ambitious plan for achieving net zero carbon emissions.
“The good news is that Aggregate Industries have invested heavily to innovate and develop low-carbon materials in recent years including concrete, concrete blocks and asphalt. The speedy adoption of these will be fundamental to any successful tender, hence, we’d urge those that haven’t done so already to prioritise the use of sustainable building materials now.”
The advice comes as for the first time, the UK government will require companies to report some scope-three emissions, including transportation, distribution, and waste from their operations as well as suppliers – which often represent a significant proportion of an organisation’s carbon footprint.
As part of a long-term strategy to decarbonise its operations, Aggregate Industries recently announced that its Cauldon Plant in Staffordshire will undergo a £13m investment project to reduce its carbon footprint. This will be achieved by building a new pre-processing plant for the storage, handling and feeding of solid alternative fuels, that would otherwise end up as landfill.
Kirstin adds: “While reaching Net Zero remains a big challenge for the construction sector, we’re seeing tangible progress. For instance, at Aggregate Industries not only are we committed to removing as much transport from roads as possible through the use of rail and water transport but we’re also leading the way in helping clients to make sustainable design and purchasing decisions by providing carbon calculations.
“By working with suppliers truly committed to Net Zero, contractors will be well-placed to demonstrate their environmental credentials to help them secure public sector projects in the coming years.”
Aggregate Industries has a growing portfolio of low-carbon building materials, including ECOPact low carbon concrete and Superlow carbon neutral asphalt.
For more information, please visit: https://www.aggregate.com/ sustainability/climate.
WAREHOUSE EXTENSION PROVIDES EXTRA CAPACITY FOR MEDICAL SUPPLIES DISTRIBUTOR
Medisave is one of the UK’s leading distributors of medical supplies to the NHS and healthcare professionals. Based in Weymouth, Dorset, the company’s range comprises over 30,000 product lines, including top branded stethoscopes, diagnostic sets and medical furniture as well as a comprehensive choice of medical disposables.
The heart of the company’s operation has always been its warehouse, where stock worth an estimated three million pounds is stored ready for next day despatch to hospitals, GP surgeries, medical students, nursing homes and, in fact, anyone with a need for medical equipment.
Clients have the option of placing their orders online, by telephone or, if they prefer, by fax and goods are picked, packed and on their way within 24 hours.
Even before the onset of the pandemic – which, of course, led to a massive spike in demand for all forms of personal protection equipment (PPE) and other medical instruments and kit – Medisave had been experiencing a sustained period of significant growth. To keep pace with the demands of its client base, the company opted to extend its existing warehouse unit by an extra 60 per cent.
The new building has been fitted out with modern very narrow aisle (VNA) racking to maximise storage capacity, while a mezzanine provides valuable extra office space as well as an area dedicated to small parts storage.
Additional pallet and order picking locations have been provided by the development – which, in effect, has increased the site’s storage capacity by close to 100 per cent.
Altegra Integrated Solutions Ltd - Medisave’s long-term intralogistics solutions partner - specified a fleet of Flexi Digital articulated forklift trucks to serve the facility.
Because Medisave’s warehouse extension is significantly taller than the original unit – the highest racking beam is nearly eight metres in the new part of the store, whereas the top beam in the existing building stands at 5.5 metres – the new Flexi trucks are fitted with four-stage ultra low-lift masts that extend to a height of eight metres but have a closed height of just 2.9 metres.
The use of four-stage ‘Quad’ masts allows the Flexis to safely travel and operate below the three metre high mezzanine floor which is a feature of the existing warehouse.
The safety of warehouse personnel is further enhanced by the fact that the ‘Quad’ mast’s HiVis design ensures that the Flexi operators enjoy best-in-class forward vision as they shuttle throughout the extended store.
“The extra height that the new building provides helps to increase Medisave’s capacity considerably. But, of course, because the existing unit is some 2.5 metres lower than the extension, Medisave’s original trucks – which were also Flexis – did not have the lift height to reach the highest racking beam level within the extension,” explains Altegra’s area sales manager, Darren Palfreeman.
He continues: “Medisave has operated Flexis for several years and for the new project they needed Flexi articulated truck technology with the lift height to reach the upper racking levels in the new part of the store. But the trucks also had to be able to pass safely and operate underneath the existing mezzanine floor structure that is prominently located within the original building.
“The closed height of a conventional three-stage mast would have been too tall, but the Flexi trucks’ four-stage ‘Quad’ mast overcame the mezzanine underclearance issue and enabled the trucks to travel between the old and the new parts of Medisave’s warehouse unhindered, reach the uppermost racking beams of the new building comfortably and, most importantly, operate safely beneath the mezzanine.”
The Flexi trucks deployed at Medisave feature digital electric motor technology that allows all independent drive, hydraulic and unique power-steering motor functions to be controlled digitally - ensuring the most productive, energy-efficient and safe driving performance throughout the working day.

YOUR SIEVING & SCREENING PROCESS REDEFINED
WITH SIEVMASTER BY FARLEYGREENE. Sieves, screens, sifters. +44 (0) 1256 474 547 www.farleygreene.com enquiries@farleygreene.com

ADVANCED DESIGN EXPERTISE ENSURES SUCCESS OF ULTRA-LONG OVERLAND CONVEYOR FOR MAJOR ALUMINA PRODUCER
TAKRAF India outlines the design features and challenges overcome in designing an overland conveyor, the “life line” for Utkal’s alumina plant, supplying bauxite ore from mine to plant.
The successful completion of the approximately 19 km overland conveyor system for the green fields Utkal Alumina project in Tikri, Raigada, in the Orissa state of India, marked yet another TAKRAF milestone development for the global conveyor industry. The contract from Utkal Alumina International Limited (UAIL) called for an overland conveyor system to transport bauxite from the mines to a new 4.5 mtpa alumina plant. This also included the longest single- flight conveyor system to be installed to date within Indian territory.
With the best quality bauxite as its input, and tightly integrated logistics between the mines and the refinery, Utkal Alumina’s operating cost per ton of alumina is among the lowest in the world. The bauxite for Utkal Alumina is sourced entirely from the Baphlimali mines, some 16 km (aerial distance) from the plant site in the Doragurha village. Prior to being conveyed overland to the processing plant, the bauxite is crushed to a size of -150 mm, with the fixed crushing package having been provided in 2012/13 by a sister company, the then Bateman India (acquired by Tenova in 2012).
CONVEYING ORE FROM MINE TO PLANT
The scope of the overland conveyor project covered design, basic and detailed engineering, procurement and fabrication, right through to erection, which included civil and structural work, commissioning, performance guarantee test runs and handover of the 2,850 t/h conveyor system. An intermediate transfer point and unloading station, including silos and buildings, were also supplied with complete electrical and instrumentation systems.
The system design brief called for the primary crushed bauxite ore of size -150 mm to be fed from the mine end junction house, through a chute to an overland conveyor of 14.5 km. This overland conveyor, ending at an intermediate junction house, in turn feeds an overland conveyor of 13.6 km. The latter, shorter conveyor ends at a plant end junction house, feeding a 500 t material surge hopper via a twoway chute. The overland system comprises 2,000 and 4,000 tensile strength steel cord conveyor belting, with a minimum belt safety factor at a steady state of >5.5, supported on a series of underslung-type idlers. These, in turn, are supported on a structural system made up of ground modules and gantries, with the overland conveyors routed partly along the ground and partly along an elevated portion. From the surge hopper, material is fed either directly to plant conveyors or to a stockpile through stockyard conveyors supplied by others.

ADVANCED DESIGN AND ENGINEERING
The execution of the project represented a group-wide effort, drawing on the global overland conveying expertise of TAKRAF Group, with the length of the required conveyor system and the challenging topography along the conveyor path calling for state-ofthe-art design and engineering. Industry-leading software was used to maximize routing and equipment utilization and specifications. The conveyor design was supported by horizontal curve analysis and dynamic analysis to optimize the long-distance conveyor power and belt tensions. Global procurement was also followed in order to optimize costs but at the same time source the most advanced and reliable components.
Initially, two technologies were considered, overland trough belt conveying and cable belt, with the client selecting the former due to its many advantages in such inhospitable and remote terrain. In addition, a major advantage of using trough belt conveying was that almost all the components and spares for trough belts are available in India, with a very small percentage of imported components.
DESIGNING FOR A COMPLEX TERRAIN
In its final configuration, the system’s two conveyors traverse a highly undulating and complex terrain. Dropping in total by 250 m over its course from material loading to discharge, the conveyor system passes through 11 nalas (branch rivers), the Ratachuan River, one forest stretch of nearly 470 m in length, a high voltage line crossing, 37 road crossings, a paddy field adjacent to the plant boundary with a stretch of approximately 2.5 km, eight hills and several villages. The elevated structures were provided with cage ladders spaced at approximately 150 m, and pile foundations were provided for the river crossing and one of the downhill crossings.
As a result of the topography and due to the conveyor length, the conveyors were designed with head and tail drives, and multiple, very tight compound horizontal and vertical curves. In total, the conveyor system features 10 right hand curves, 4 left hand curves and horizontal curve radii of 2,500 m across all locations but one: a critical zone on the shorter conveyor where the horizontal curve is 1,800 m. This portion of the conveyor passes over a hill and through the plant boundary. The longer conveyor has a ground module and a graded portion. The ground module comprises 17 straight sections, 1 left hand curve and 1 right hand curve section, while the graded portion consists of 12 straight sections, 2 left hand curves and 4 right hand curves. The overland gallery on both conveyors together features 403 straight sections, 154 right hand curves and 61 left hand curves, with a maximum gallery length / support interval of 49.5 m and standard gantry length of 27 m.
The idler spacing for the straight and inclined portions of the galleries on both conveyors is 4.5 m for the carry idlers and 9.0 m for the return idlers, except for one section on the longer conveyor where the carry idlers are spaced at 3.5 m and the return idlers at 7.0 m. On both conveyors, the carry idler spacing for the horizontal curved galleries is 2.25 m; and the return idlers are spaced at 4.5 m. With an installed power of 6x850 kW and 2x850 kW, the conveyor system features 6 drives at the tail end and 4 at the head end on the longer conveyor, while the shorter conveyor has 2 drives at the head end only. There are 2 belt turnovers on each conveyor, 1 at the tail end and 1 at the head end. Each conveyor features a fail-safe hydraulic disc brake at the tail end. A take-up winch with capstan brake arrangement has been provided at the head end of both conveyors.
The intermediate transfer point between the 2 conveyors is located in hilly terrain and, since the 4 head end drives of the longer conveyor are also located there, the conveyor drive and take-up areas are mounted on a portal steel structure. These lightweight but high strength structures provide the design flexibility to accommodate the terrain. Advanced material flowability testing and modelling was used in the design of the transfer chutes at the intermediate transfer point and the plant end junction house to minimize risks such as environmental pollution and spillage, accelerated belt wear and blockages. To facilitate maintenance, approach roads and a mine road were made available all along the conveyor length, with the cage ladders provided on the elevated structures enabling ease of access.
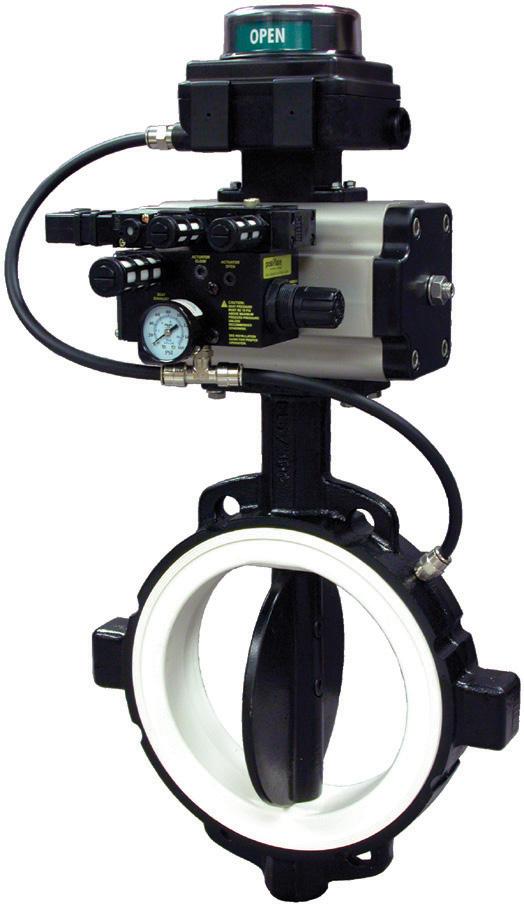
CONVEYOR ERECTION FOCUSES ON ZERO HARM
Erection of the conveyor system was complicated by the requirement to accommodate and minimize disturbance of the population of the various villages through which the conveyor system passes, as well as the need to blast and excavate a suitable route through the hilly region of the conveyor path. Approach roads for erection of elevated structures on the hilly terrains also had to be provided. With major equipment such as heavy cranes and excavators used for erection of the elevated structures, particularly in the challenging hilly terrain, TAKRAF India placed particular focus on safety, strictly conforming both to TAKRAF’s global promise of Zero Harm and to the client’s safety protocols. Performance guarantee testing was carried out over nearly one week, with the system consistently achieving its present capacity of 1,500 t/h. As a result, the conveyor system could be handed over to the client in December 2016 at a special event where celebratory Pooja rituals were carried out in the presence of top management of both companies. The successful completion of this project is testament to TAKRAF’s ability to employ their long-standing experience in designing conveyors to meet new challenges. Other Valves Fight Friction, We Designed it Out Unlike other valves that seal with friction, Posi-flate’s unique butterfly valve uses an inflatable seat to seal with air pressure. Thus it requires less torque and a smaller actuator, resulting in lower cost. Plus, the seat automatically compensates for wear, providing longer life. Some users have reported over six million cycles and the valves are still going strong. • Less friction • Low torque • Low maintenance • Lower actuator costs • Longer valve life • More reliable Tel: +44 (0) 1908 622366
www.posiflate.com
DUST EXTRACTION SPECIALIST SET TO EXHIBIT AT ADVANCED MATERIALS SHOW 2021
Dustcontrol UK has announced it will be exhibiting a range of its highly effective extraction equipment at this summer’s Advanced Materials Show 2021.
Taking place on Wednesday, 7th and Thursday, 8th July at the National Exhibition Centre, Birmingham, the Dustcontrol team will be showcasing the firm’s extensive range of both fixed and mobile cyclone-based dust extractors and air cleaners at stand 17312.
The DC 11-Module for example, which comes in several models, is an optimised stand-alone unit for source extraction and industrial cleaning. It has been designed to service up to six normal extraction points or several cleaning outlets at a time, and is modularly built, meaning it can be tailormade to suit any manufacturing and production environment.
As with all of Dustcontrol’s UK equipment, the DC 11-Module can be fitted with Hepa 13 filters, meaning exhaust air can be safely returned to the work environment.
James Miller, Managing Director of Dustcontrol UK, said: “We’re excited to be showcasing a range of our most efficient extraction equipment on our second attendance to the Advanced Materials Show.
“As well as showcasing centralised systems, we’ll be exhibiting a range of H Class mobile air cleaners and cyclone-based vacuum units. A selection of ATEX-approved models and accessories will also be on display to complete the extensive range.
The company, based in Milton Keynes, has over 45 years of experience in developing dust extraction solutions and centralised vacuum systems to fit client requirements in the manufacturing and production industries. They are experts in capturing dust at its source – both where and when it’s created. With more than 300 exhibitors and 3,000 visitors expected to attend next month’s show, the event promises to offer an unmatched insight into current and future materials development, with a specific focus on high-performance materials technology, innovation, design and use.
James concluded: “The Advanced Materials Show will provide us with a platform to show trade users first-hand how our elite dust extracting equipment can help to create safe and healthy working environments.”
For further information on Dustcontrol UK’s products, please call 01327 858001, or email sales@dustcontrol.co.uk.
Alternatively, for further information on Dustcontrol UK, visit www.dustcontroluk. co.uk, or for more information on Advanced Materials Show 2021, visit https://www.advancedmaterialsshow.com/.

RTITB TO LAUNCH NEW FORKLIFT OPERATOR ID ECARDS
RTITB will become the first accrediting body to issue lift truck operators with electronic ID cards, as opposed to physical photo ID Cards, starting from 12 July. Materials Handling Equipment (MHE) operator ID cards are important as they help to quickly identify the operator and ensure the person named on the training certificate is one and the same.
“We are committed to improving the safety of everyone in the supply chain,” explains Laura Nelson, Managing Director for RTITB. “So, just like our existing physical National Operator Registration Scheme or ‘NORS’ ID card, the new electronic eCard shows employers that an operator has received the required training and obtained the necessary qualification to support safe operating practices.”
“During the pandemic there was huge demand for lift truck operators, and businesses had a need to get qualified operators up and running quickly and safely,” says Laura. “Whatever happens going forward, the new eCards will help speed things up, thanks to an average four-hour delivery time and our ability to dispatch them anytime, even during a national lockdown.”
From 12 July, on successful completion of RTITB Counterbalance Lift Truck Operator training, or similar courses, the training provider will be issued with a link to the eCard via email. For data security reasons, a separate email will go to the employer or operator with a code to access and download the ID card. This means that if the training provider sends the email to the wrong person, no personal data is compromised.
“We are also very aware that these are difficult times for many businesses, so the new eCard allows us to reduce the cost of ID cards, with the added benefit of Covid-safe fast delivery as well as being more environmentallyfriendly,” says Laura. “This change will help prevent pollution by reducing the amount of new raw materials used, as well as saving energy and reducing greenhouse gas emissions”.
Operators can use either an Apple or Android smartphone to save the card to their preferred digital wallet (Apple Wallet or Google Pay), and view, save, and print a PDF version of their card if they wish. A PDF eCertificate will also be an option for those without a smartphone. Once an operator has been issued with their RTITB eCard, any subsequent new or updated qualifications will be added to their card.
To help employers, training providers, and operators transition to eCards, RTITB will provide full support in the set-up, providing helpful guidance documents and videos.
Information on the eCard will include the operator’s photo, name, and RTITB registration number, logos for RTITB and the Accrediting Bodies Association for Workplace Transport (ABA) logo, ABA truck code, where applicable plus the training provider’s name and website address. The course title and a QR code to easily verify operator qualifications will also be included.
“Also, with safety and infection control bound to remain a priority for the supply chain long after restrictions are eased, the eCards reduce contact points, while offering a secure, easy to update, and robust system that helps employers ensure only correctly qualified operators are using a lift truck,” says Laura.
The new RTITB eCard is the latest digital transformation for RTITB, following the launch of a wide range of innovative eLearning solutions and the unique MyRTITB TrainingFriend android app, which enables lift truck operator testing to be 100% paperless, while improving operator testing standards and training record compliance. RTITB also recently switched most of its Training Materials to USB, instead of hard copy and is working towards all training materials going digital, instead of being on paper.
These new digital options are developed with the environment front of mind. The eCard will help reduce the use of single use plastic, just as the other solutions help remove unnecessary paper usage from training and administration.
For more information about the new lift truck operator eCards, please contact us on solutions@ rtitb.com or +44 (0)1952 520200 or visit www.rtitb.com.

GYRO EX BIN ACTIVATING FEEDER/DISCHARGER
Accurate Feeding and Discharging
The GYRO EX bin activating feeder and discharger produces a controlled gyratory motion to positively withdraw granular materials from bins, storage silos and hoppers at any desired feed rate for a more consistent and reliable discharge. At the heart of the GYRO EX bin activating feeder and discharger is the drive that produces a radial force creating a uniform circular motion on both the upper activation cone and the lower discharge cone. It is this annular radial vibratory motion which imparts the force to the material, assuring a more reliable and predictable material discharge.
A unique feature of the GYRO EX bin activating feeder and discharger is that the stored material load is completely supported by the upper bin activation cone which has a lower cone angle than the discharge cone, assuring an uninterrupted and positive discharge of the stored material. The GYRO EX bin activating feeder and discharger can also be started and stopped as desired because material is not allowed to accumulate or stagnate in the lower discharge cone which might create packing or plugging problems. Irrespective of the particle size, the GYRO EX bin activating feeder and discharger is well suited for almost any size material and the rate can easily be increased or decreased by adjusting the gap between the inlet opening and the upper activation cone. Features:
A. Low headroom reduces height.
B. Material stops due to angle of repose.
C. Gap is adjustable to increase or decrease feed rate.
D. Circular distance of activation cone creates a wide feed zone.
E Vibrating lower cone is selfcleaning.
F. Exterior mounted vibrating motor.
G. High strength reinforced flexible connector.
https://www.dynamicair.com/ products/vibratory/productsv.html
Dynamic Air Ltd. Milton Keynes, United Kingdom Phone: 44 1908 622344 E-mail: sales@dynamicair.co.uk www.dynamicair.com
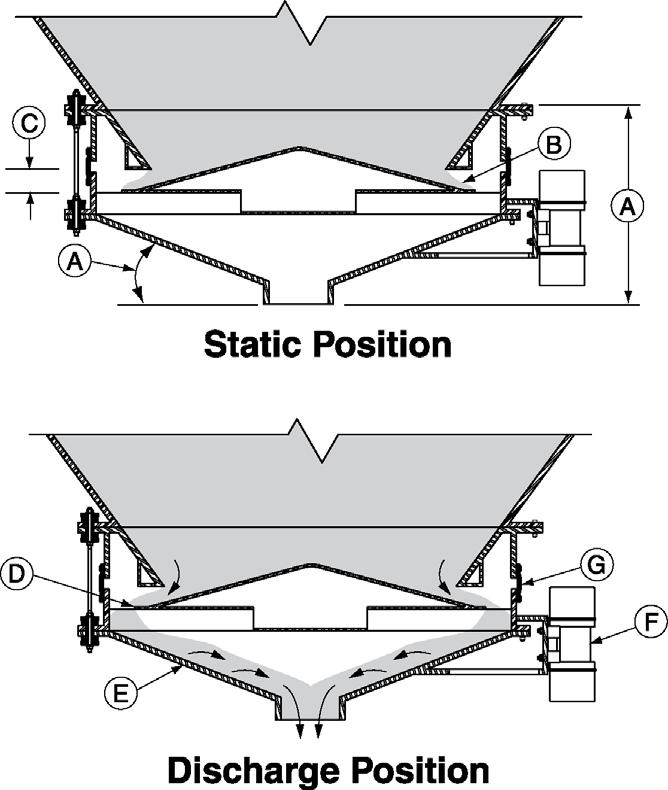
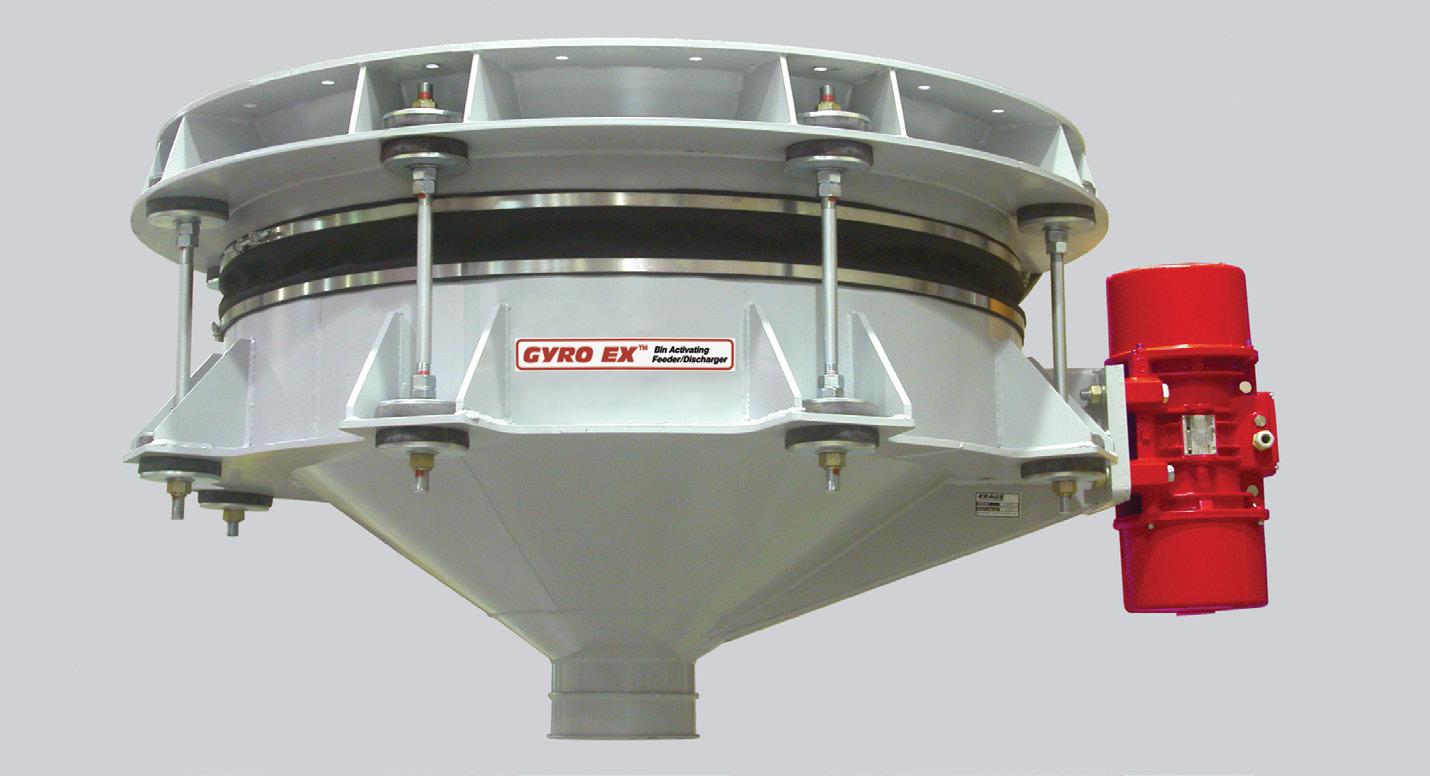
