
7 minute read
BULK MATERIALS HANDLING
DUST EXTRACTION SPECIALIST LAUNCHES TRIO OF POWERFUL VACUUM CLEANERS
Dustcontrol UK has officially launched its new, all-in-one range of powerful three-phase turbo vacuum cleaners.
The latest addition to the DC Tromb family, the DC Tromb Turbo offers optimum quality, containment and performance. One of the major updates is the three-phase turbo motor that has been designed specifically to target heavy-duty cleaning. The new range has also been developed with a thermal protector that activates at high temperatures, while a simpler filter change has also been included for easier and quicker removal.
The DC Tromb Turbo is available with Direct Start or a Frequence inverter (VFD), while those working in ATEX zone 22 can benefit from the EX model.
The DC Tromb Turbo with direct start is suitable for source extraction from medium-sized power tools such as grinders, jackhammers and saws, while the VFD model gives 50 per cent more Hepa filter area than its predecessor. For instance, it can remove dust during polishing of glass fibre, carbon fibre and epoxy with a hand-held sander. New safety features such as overheating protection is also added. Both models can be equipped with either a steel container, plastic bag or a Longopac bag.
The EX version is certified to IP65 standard, ATEX Zone 22, meaning it can operate in explosive environments. Like the other two versions, the EX Tromb Turbo has a tall cyclone, large filters and powerful motor package, allowing it to handle large amounts of debris.
James Miller, Managing Director of Dustcontrol UK: “We’re delighted to launch our new and improved Turbo Tromb range. The new models are not just more powerful, robust and effective than previous Tromb cleaners, but also incredibly resourceful. The powerful vacuum cleaners can handle an array of fine dust and materials on construction sites, created from cutting concrete, sanding, grinding or drilling floors or walls, as well as dust from many other industrial factory processes.”
The company, based in Milton Keynes, has over 45 years’ worth of experience in developing dust extraction solutions and centralised vacuum systems to fit client requirements in the aerospace, food and drink, construction, engineering, and manufacturing industries. They are experts in capturing dust at its source – both where and when it’s created.
James concluded: “Ultimately, the new range ensures those working in hazardous environments where dust is prevalent can carry out their jobs as safely and efficiently as possible.”
For further information on Dustcontrol UK’s products, please call 01327 858001, or email sales@dustcontrol.co.uk.
Alternatively, for further information on Dustcontrol UK visit www.dustcontroluk.co.uk.
IF YOU ARE INTERESTED IN ADVERTISING WITHIN BULK SOLIDS TODAY MAGAZINE, PLEASE DO GET IN TOUCH BY VISITING WWW.BULKSOLIDSTODAY.CO.UK OR EMAILING US AT BST@ABBEYPUBLISHING.CO.UK
HYSTER-YALE GROUP CELEBRATES 40 YEARS OF MANUFACTURING IN NORTHERN IRELAND AS PLANT EXPANDS
In 2021, the Hyster-Yale Group proudly celebrates 40 years of manufacturing lift trucks at its plant in Northern Ireland as it announces the expansion of its Craigavon site.
The facility, which was officially opened on 7th April 1981, was built and equipped with the most up-to-date robot systems and equipment. Over the years the plant has grown to be the largest volume forklift plant in the UK, manufacturing thousands of electric, diesel, and LPG forklifts each year for export throughout Europe, the Middle East and Africa.
The site, around 30 miles from Belfast, employs hundreds of people from the local area, which the company credits as key to its success story. This year, five team members will also celebrate the milestone of 40 years with the company, while more than 100 current employees at the site have 30 years or more of service.
“The success of our plant at Craigavon is driven by our people, where we see incredible dedication, perseverance, and loyalty from the team at all levels, with an average length of service of 17 years,” says Jim Downey, Plant Manager for Hyster-Yale Group EMEA in Craigavon. “Over the last four decades, our people have worked together to conquer challenges, embrace new opportunities, and maintain forward momentum, and that is why our facility continues to succeed, evolve, and grow.”
Transformation remains key to the Craigavon facility, where expansion of the 500,000 sq.ft site is currently in progress, in preparation for future manufacturing demands and product lines. The company has invested millions over the past 2 years developing the factory, which incorporates leading technologies and up-to-date automated systems. The extension will also create dozens of new jobs, including continued investment in apprenticeships.
“We have great confidence in the talent pool in Northern Ireland and are fortunate to have so many long-standing employees that bring with them significant expertise, including many of our management team who started their careers here on the shop floor,” says Downey. “However, at the same time, we are keen to optimise our operations with automation and new ways of working that best support our workforce and deliver the quality our customers need,”
Quality is key to the facility at Craigavon, which has been the recipient of numerous awards throughout its history. Among the team’s achievements is ISO 50001 certification for its commitment to energy efficiency, and sustainability continues to be a key driver for the company during its latest site expansion.
The new 60,000 sq. ft. extension to the factory will be known as the Sands Building, in honour of Harry Sands, former Senior VP and Managing Director, EMEA, for Hyster-Yale Group based in Craigavon, who retired in 2020 after 40 years with the company. It has been built with environmental specifications and ambitious objectives in mind. For instance, it incorporates a completely new approach to lighting which harnesses more natural light, decreasing electricity consumption and reducing CO2 emissions. A biomethane fuelled plant on the site will also be used to provide 80% of the electrical power required, with the heat by-product also used on site.
In line with the Hyster-Yale Group 2026 Corporate Responsibility Objectives, the site aims to reduce carbon emissions by 30%, in addition to targets for reducing water consumption, waste, and landfill. Waste to landfill from the facility has already reduced significantly, with 97% now being recycled, and a number of other waste reduction initiatives exist on the site, everywhere from the canteen kitchen to the packaging line.
The Craigavon plant also continues to be committed to biodiversity, encouraging rare wildlife in its grounds as a result. The latest plant extension incorporates a Sustainable Urban Drainage System, which mimics natural drainage and is more environmentally friendly.
“Throughout its 40 years the Craigavon facility has continued to innovate and build capability to be an agile and flexible facility, that is able to meet and exceed customer expectations through automation, people and processes,” says Downey.
“Now is an exciting time as ever, as we adapt our assembly lines, connect with new technologies, and develop our product ranges, laying the foundations for future growth and many more decades of success,” he concludes.
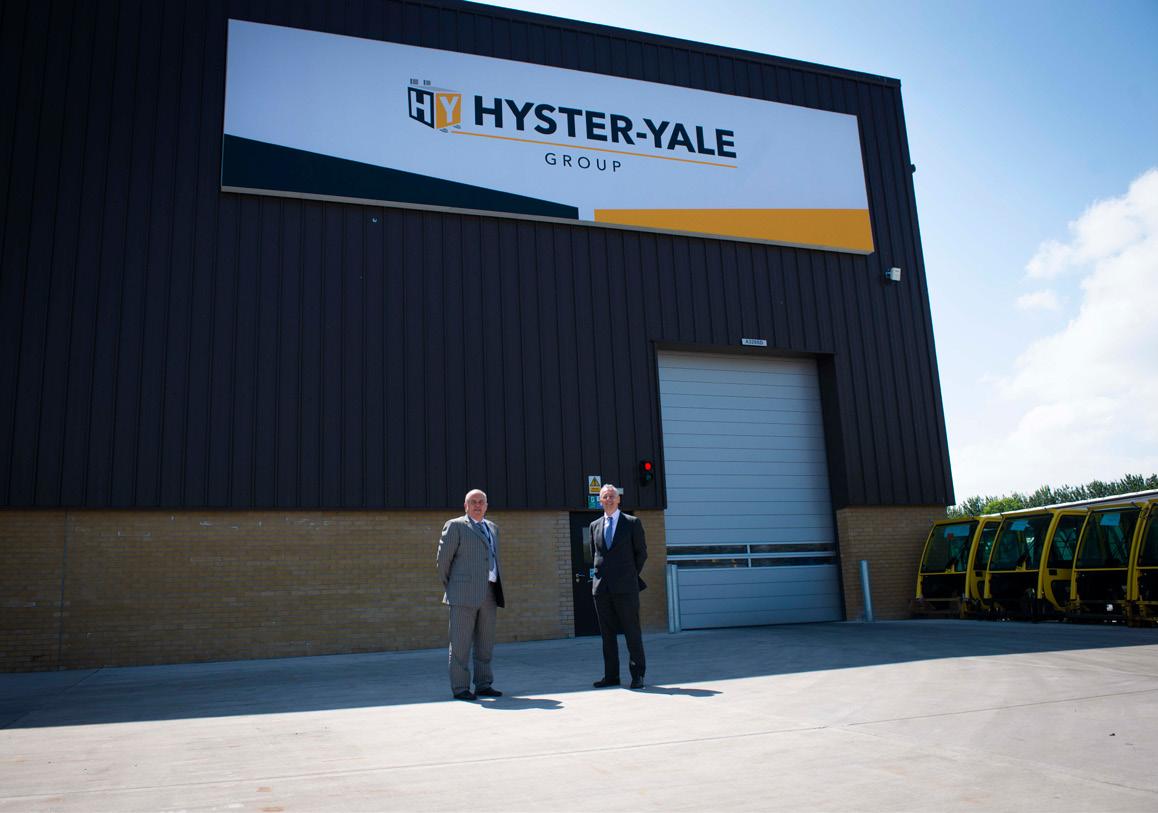
ABBEY LOGISTICS FORMS STRATEGIC PARTNERSHIP WITH CISTERNAS AMARILLO S.L
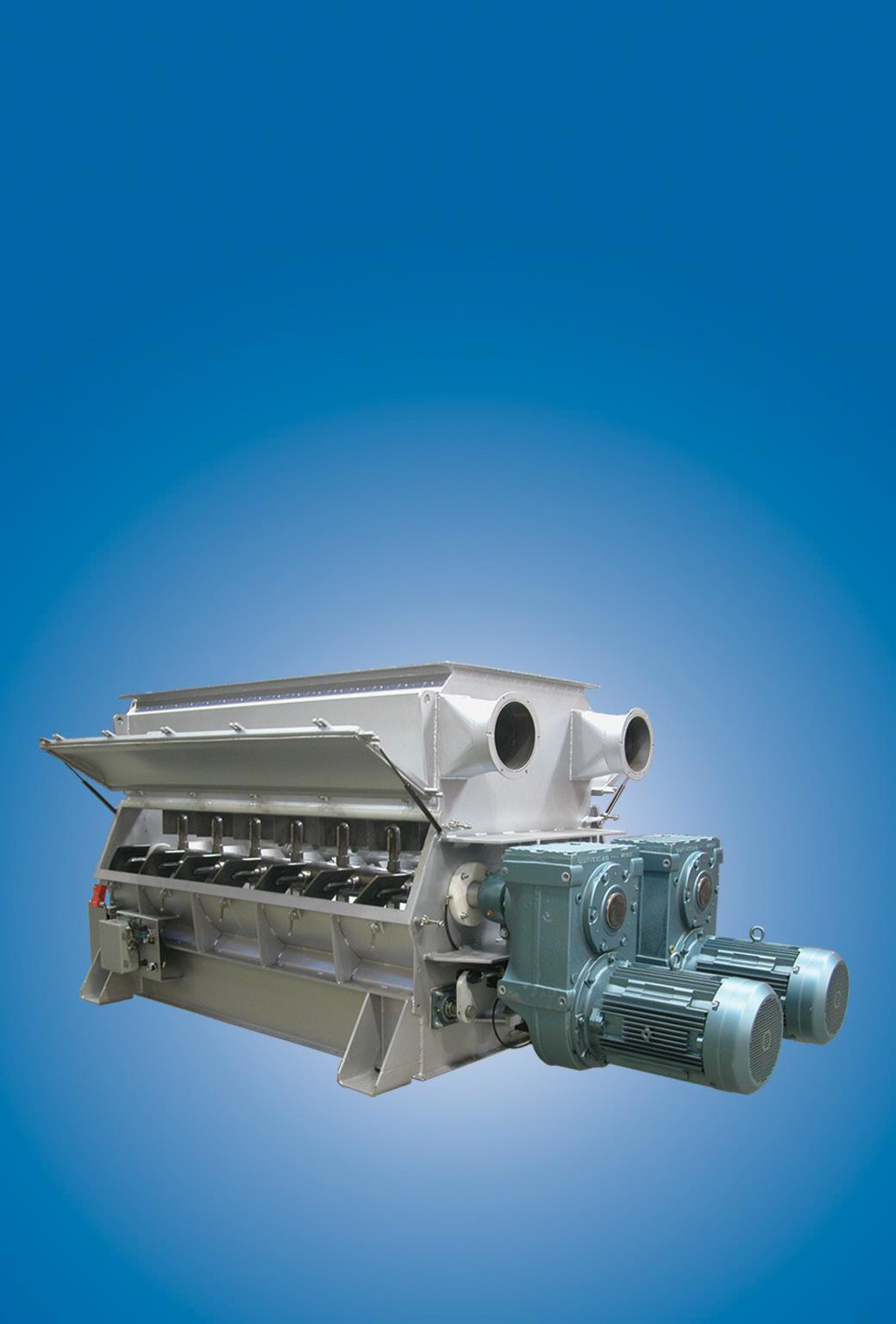
Abbey has formed a new partnership with Cisternas Amarillo S.L (Amarillo), a large bulk powder road tanker company based in Seville, Spain and part of the full-service logistics company, Pantoja Grupo Logistico.
The partnership is designed to provide continuous movement of customers’ products between the UK and Spain and provide customers with a faster more reliable and cost-effective transport solution through a well-managed joined-up approach that optimises the reach of the two businesses.
The partnership combines Abbey and Amarillo’s extensive knowledge and experience in bulk food road tanker transport and maximises their collective fleet capabilities to provide a reliable flow of feedstock ingredients between the two countries.
Utilising multimodal transport links, the tanks are reloaded for the return journeys, minimising empty miles and fully utilising both company’s vehicles and drivers to ensure products move on a continuous basis.
Paul Laverick, Head of Abbey’s Powder Division said:
“This new partnership further demonstrates Abbey’s unique ability to support road tanker companies in Europe thanks to our scale and network capability in the UK.
Amarillo is highly regarded for its skills and experience in bulk dry food grade products and we are delighted to begin working together as we maximise the vast experience our combined businesses have for the benefit of our customers.”
Lars Stendahl, Amarillo’s Operations Director said:
“Abbey Logistics is well known to us and their reputation for customer service and flexibility together with their specialist knowledge of the products we carry, made them a natural fit for our operations and customers.
Abbey Logistics is committed to delivering costeffective, dependable and responsive road tanker logistics for bulk liquid & powdered products in the UK and Europe.
The Group also provides warehousing and materials handling services on the Wirral in the UK, and multimodal transport solutions throughout the UK and Europe.
Visit www.abbeylogisticsgroup.com for more information about Abbey Logistics Group.
High Efficiency Drying or Cooling of Bulk Solids
The Bella dryer/cooler offers thermal efficiencies to 80 percent or better because air flows around material while it is suspended in the weightless zone. The result is a more consistent material.
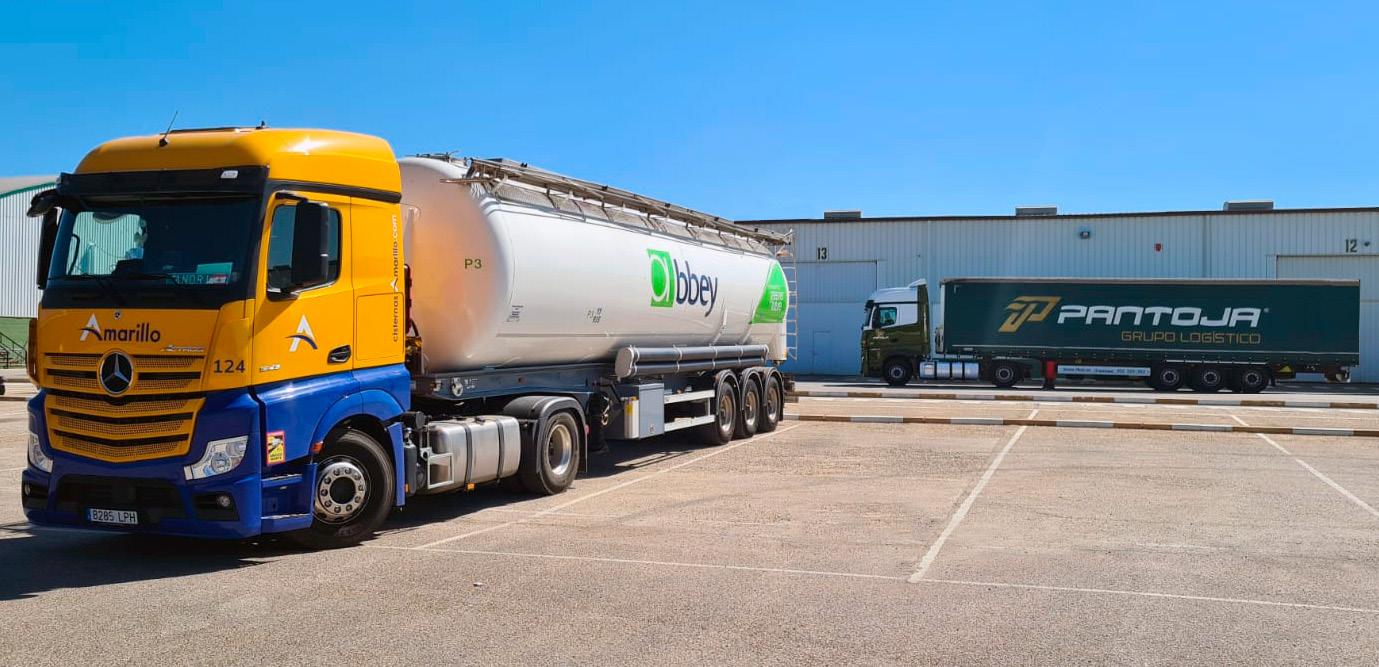