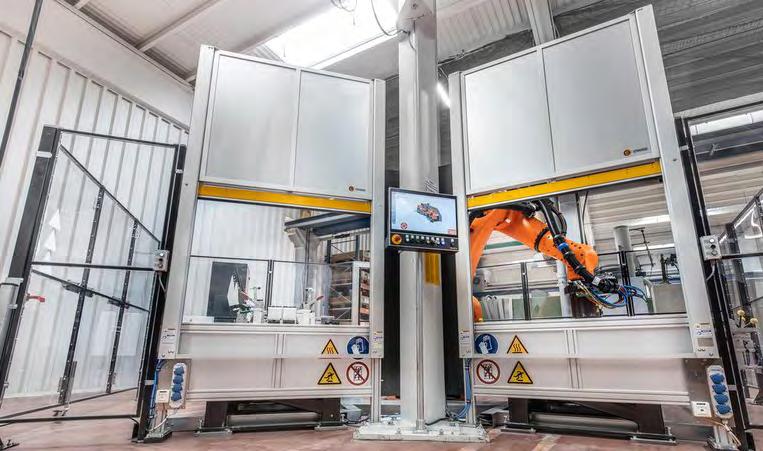
4 minute read
Lyft - Materialhantering - Automation - Robotteknik - Utbildning
Ny cell för friktionsomrörningssvetsning utökar kontraktstillverkning hos KUKA
En ny cell med friktionssvets från KUKA, cell4_FSW, svetsar även stora komponenter med hög foghållfasthet och minimal svetsfördröjning. Cellen är extremt flexibel, vilket är fördelaktigt för företag inom
Advertisement
ramen för kontraktstillverkning.
Svetscellen öppnar nya möjligheter för hopsättning av till exempel fasta aluminium- och kopparlegeringar.
Utöver robotar, programvara och anläggningar erbjuder KUKA även kontraktstillverkning för specialsvetsprocesser och komponenter i alla batchstorlekar. Automatiseringsspecialisten har nu kompletterat sin egen maskinpark med en innovativ svetscell för friktionsomrörningssvetsning, cell4_FSW (”Friction Stir Welding”). Detta öppnar framför allt nya möjligheter för hopsättning av material som tidigare ansågs vara problematiska att svetsa: till exempel fasta aluminium- och kopparlegeringar.
Alltid i rörelse - kontraktstillverkning som förfarande
för friktionsomrörningssvetsning
Förfarandet är fördelaktigt där fogar verkligen måste vara täta och dessutom kräver hög hållfasthet. Till exempel för strukturkomponenter inom bilindustrin eller för fl yg- och rymdindustrin. Tack vare den modulära konstruktionen på cellen kan KUKA uppfylla näst intill alla kundönskemål. cell4_FSW är maximalt fl exibel för kontraktstillverkning – den kan dessutom konfi gureras individuellt av företag som investerar i en egen cell. Ett ytterligare plus: Den robotbaserade friktionssvetsningen är fl exiblare och billigare jämfört med tekniken med portaler.
Kompakt cell gör stordåd
”Små komponenter kan många svetsa. Mycket få kan svetsa de stora”, säger Rainer Simanowski, chef för Technology Services på KUKA. ”Vår tillverkningscell har två arbetsbord på vardera tre och en halv meter och är topputrustad för stora komponenter. Dessutom har vi två möjligheter att mata cellen: via lyftportar för småldelar samt vikdörrar, som öppnas över hela arbetsbordets bredd.”
KUKA hjälper till från början
Storleken räknas, men det gör även KUKA:s expertis inom komponent- och produktutveckling. Inom ramen för kontraktstillverkning står KUKA till förfogande från början, vägleder intressenter vid rätt val av svetsprocess och genomför uppdrag oberoende av produktionsvolym. cell4_FSW utökar nu KUKA-portföljen i detta område: Detta omfattar en redan omfattande maskinpark för Magnetarc-svetsning och rotationssvetsning – för användning av prototyp- och serietillverkning i alla batchstorlekar.
KUKA:s robotstyrning underlättar åtkomsten vid friktionsomrörningssvetsning.
Som fogförfarande för anslutningar av aluminium- och kopparmaterial är friktionsomrörningssvetsning idealisk: Det går att upprätta en stumfogs- eller överlappssvetsning. Längs med beröringsytorna för arbetsstyckena som ska sammanfogas leds ett roterande verktyg (”stift”). Den nödvändiga värmen för svetsning skapas genom friktion. Materialet längs med svetsfogen kondenseras bara plasticerat och inte i fl ytande form. En fördel vid användning av aluminiummaterial är att fogarna är fria från porer och sprickor och därmed tryck- och vakuumtäta. ”Med vår cell underlättare vi för producerande företag att begagna sig av denna teknik”, säger Simanowski. ”Prisvärt, med en fl exibel anläggning, som gör friktionssvetsning attraktiv för varje batchstorlek.”

Jungheinrich automatiserar för Coca-Cola
• 42 meter högt pallager i silokonstruktion
• Monorail-lösning med bro skapar nya transportvägar
• Alla lösningar från en och samma leverantör
Jungheinrich bygger en automationslösning för Coca-Cola HBC vid företagets fabrik i Radzymin i Polen. Det nya lagersystemet utökar den befi ntliga anläggningen och erbjuder toppmodern teknik. Vissa byggåtgärder kommer att slutföras under pågående drift och idrifttagning planeras till 2022.
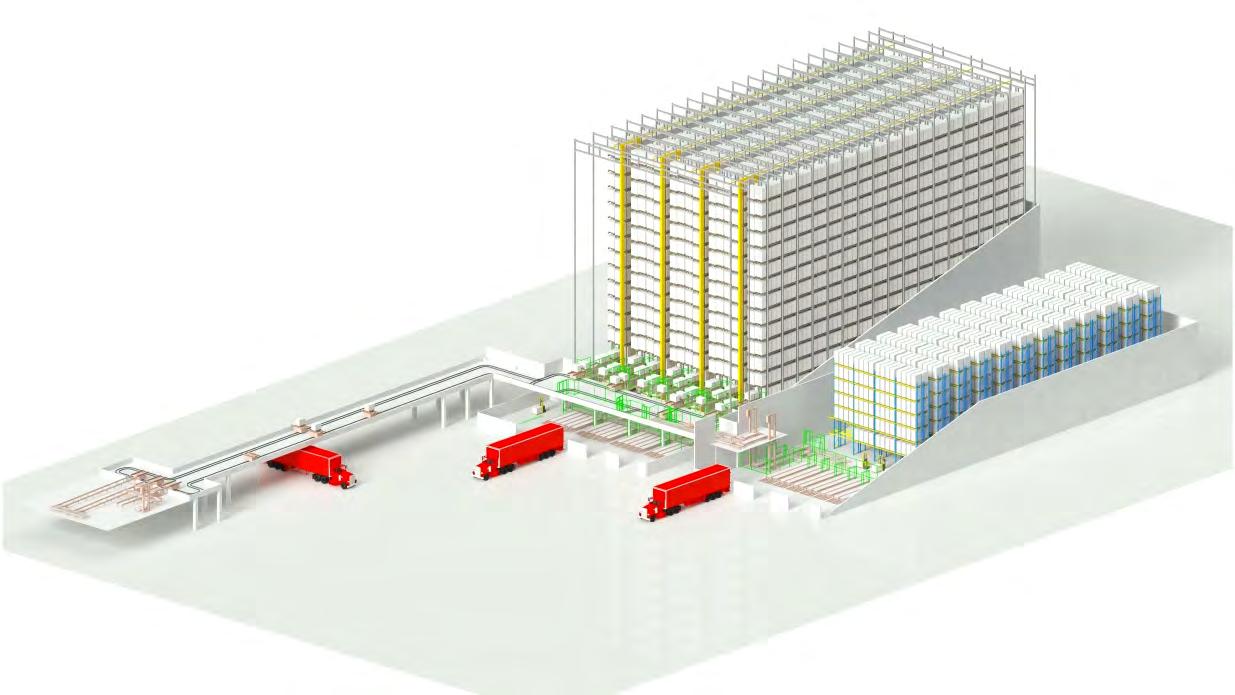
"Utnyttja tillgängligt utrymme till fullo, skapa ny lagringskapacitet och öka varugenomströmningen" Det var Coca-Colas uppdrag till Jungheinrich. Lösningen föll på det 42 meter höga och 60 meter långa höglagret i silokonstruktion. Det garanterar maximalt utrymmesutnyttjande samtidigt med hög hanteringskapacitet. Det automatiska höglagret omfattar totalt fyra gångar och ger plats för upp till 14 000 dryckespallar, som kan förvaras i dubbeldjup. Alla processer i höglagret är helautomatiserade. Jungheinrichs experter utformade det med möjlighet till expansion: Ytterligare gångar kan läggas till vid senare tillfälle utan komplikationer, allt under pågående drift. Den nya lagerlösningen från Jungheinrich förbättrar också transportvägen från produktionen. För detta ändamål har intralogistiskexperter genomfört modifi eringar och utökat befi ntliga transportörsystem: Ett monorail-system med en bro är nu hjärtat i Radzymin-anläggningen. Den transporterar färdiga dryckesfl askor till alla tillgängliga lagringsplatser - både i det nya höglagret och i automatlagren. Jungheinrichs skräddarsydda intralogistikkoncept möjliggör ett optimalt materialfl öde mellan de olika områdena i anläggningen.
Szymon Matulka, BU Engineering Manager Poland & Baltics vid Coca-Cola HBC:
”Anläggningen innebär något speciellt för oss. Med det automatiska höglagret och de förbättrade transportvägarna sätter vi nya standarder när det gäller effektivitet och säkerhet. På detta sätt säkerställer vi en konsekvent hög tillgänglighet för våra produkter.” Dessutom ger lagrings- och plockmaskiner från MIAS, en partner till Jungheinrich, hastighet till det automatiska pallagret: Tack vare specialanordningar sker transport och hämtning av varor som väger upp till sju ton med hög hastighet. Även här kan ytterligare enheter integreras om det behövs. Dessutom har det befi ntliga lagerhanteringssystemet (WMS) ersatts av ett nytt. I framtiden kommer Coca-Cola HBC endast att använda ett WMS för hela lagret, ett system som inkluderar olika intralogistiska lösningar. Det kommer att användas för att hantera alla anläggningar och processer. Programvaran hjälper till att identifi era möjliga optimeringar, till exempel distribution av varor till de olika lagerområdena.