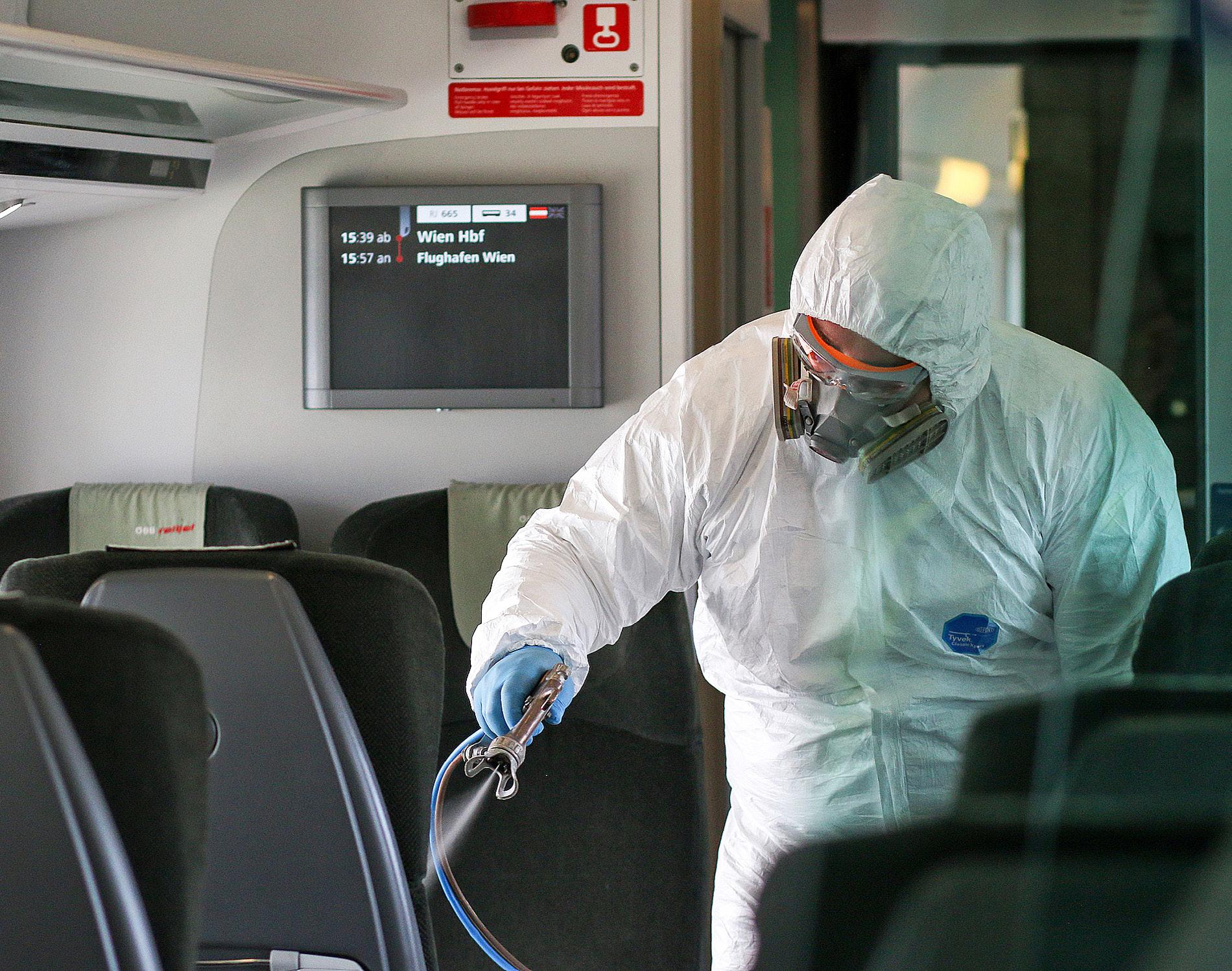
11 minute read
CASE STUDY ReSysten at the Forefront of Combating Infection From Contaminated Surfaces
Located in Törökbálint, a village abutting the southwestern boundary of Budapest, a company with a headcount of just 20 people is in the advance guard of coating technology, a fast-growing sector seen as crucial to the fight against pandemics such as COVID-19.
By Kester Eddy
In 2011, János Pintér was perusing a research paper on the biological properties of Titanium Dioxide (TiO2). Although an information technology professional, Pintér’s entrepreneurial spirit was aroused: he found the results intriguing. Prepared correctly, a very fine nanocoating of TiO2, when exposed to light, acts as a catalyst to create chemicals that decompose and destroy cell membranes. Because most microbes are single cell cells, they die very quickly once they come in contact with any such coating.
Knowing that there were serious issues with infections by highly resistant, socalled “super bugs” in hospitals, Pintér saw huge potential for TiO2, a food additive used in such everyday items as toothpaste and chewing gum, in combating this threat. He quickly began working with contacts in chemical research laboratories to find ways to create an affordable titanium dioxide-based coating that would act as a safe, efficient disinfectant over a long time period.
“In short, we wanted to revolutionize the anti-microbial coating industry, which was then still in a very much nascent state of development, with an industry-standard solution,” Pintér told the Budapest Business Journal. After three years of research and development, the former IT specialist believed his spray-on product had the simplicity of application, cost and lifespan that made it competitive with anything else on the market. Teaming up with Péter Lohockzy, a management and sales expert who became CEO, the pair founded ReSysten Hungary Kft., a company synonymous with its core product. However, they soon found the going tough, even in their native Hungary. “It takes time for any new hygiene
technology to be accepted, and we had to prove our worth. The early adopters of ReSysten were public transport companies and the food industry,” Pintér, the company’s chief data officer, says.
LARGE-SCALE TESTS
Since the pioneering days, researchers have continued to fine tune the formula, “vastly improving” the durability and sensitivity to lowlight environments. ReSysten, in cooperation with transport companies, has also carried out several largescale tests on trams and buses, and even escalator hand-rails on the Budapest metro system. Pintér describes the latter experiment as “the toughest of them all”. “I believe this remains the only largescale handrail coating experiment using a photocatalytic anti-bacterial solution in the world,” he says. “Think about it, the Budapest metro moves more than one million passengers every day. The coating has to perform in relatively lowlight conditions, with hundreds of thousands of passengers adding to the contamination every day.”
In addition, the handrails themselves are subject to continuous abrasion from the driving mechanism.
Astonishingly, eight months after the application the coating performed better than when
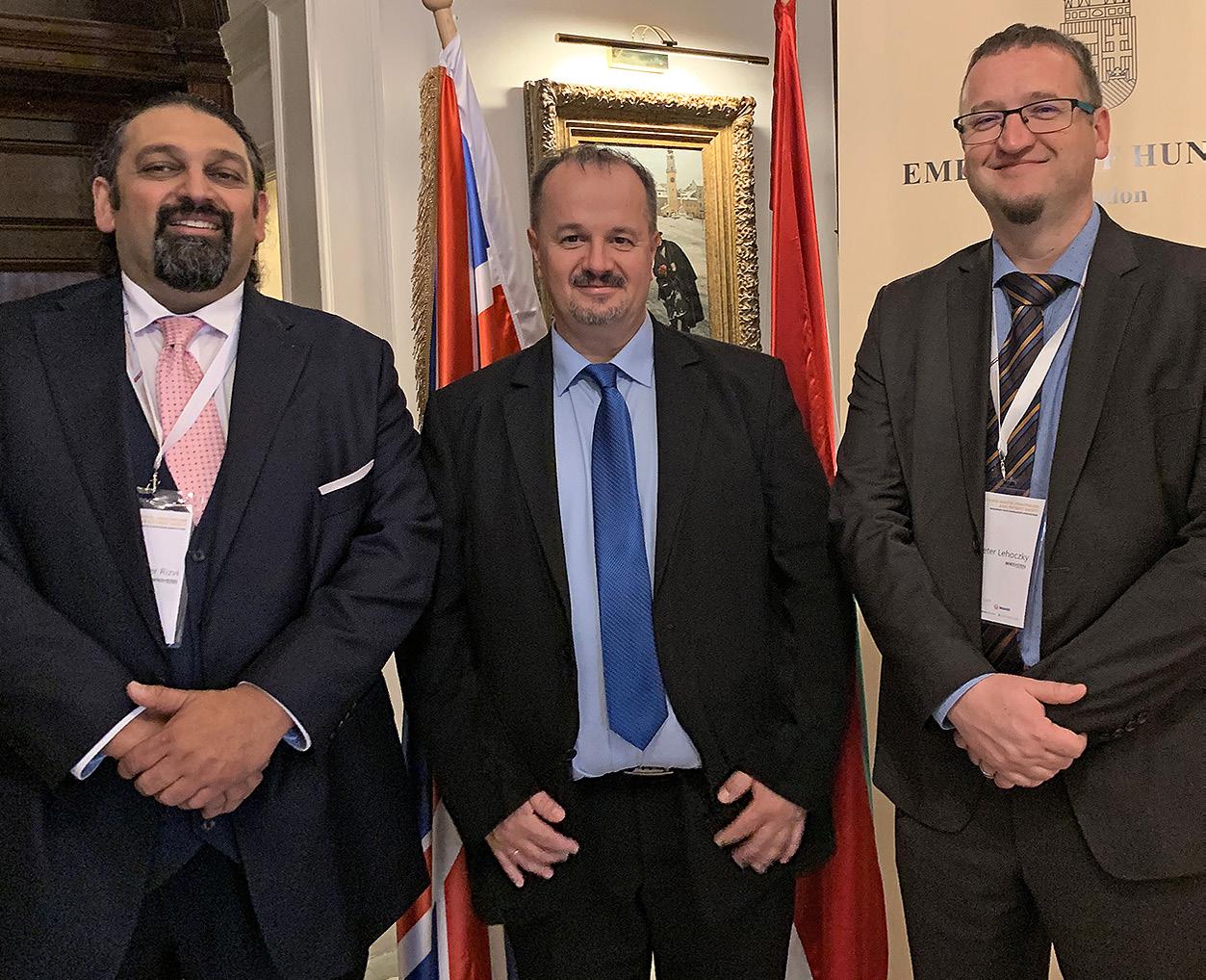
From left, Shajjad Rizvi, János Pintér, and Péter Lohockzy at the U.K. launch of Resysten at the Hungarian embassy in London.
originally applied, a result put down to the effect of low light levels, the coating actually improving as exposure to light built up.
Growth, however, has been steady, if limited, and largely restricted to Hungary. ReSysten has an impressive array of companies and institutions on its website that have
The fear of falling victim to the coronavirus has brought the airline industry to its knees, decimating passenger loadings around the globe.
But that fear is mainly perceived to be in the flight itself. In fact, the chances of infection go well beyond the time in the aircraft, and ReSysten was working with
Budapest Airport, the operator of Ferenc Liszt International, last year (well before the onset of the
COVID-19 pandemic) on a project to eliminate pathogens on the humble tray used at security checks.
As every frequent flyer knows, these trays are used by scores, possibly hundreds of passengers every day,
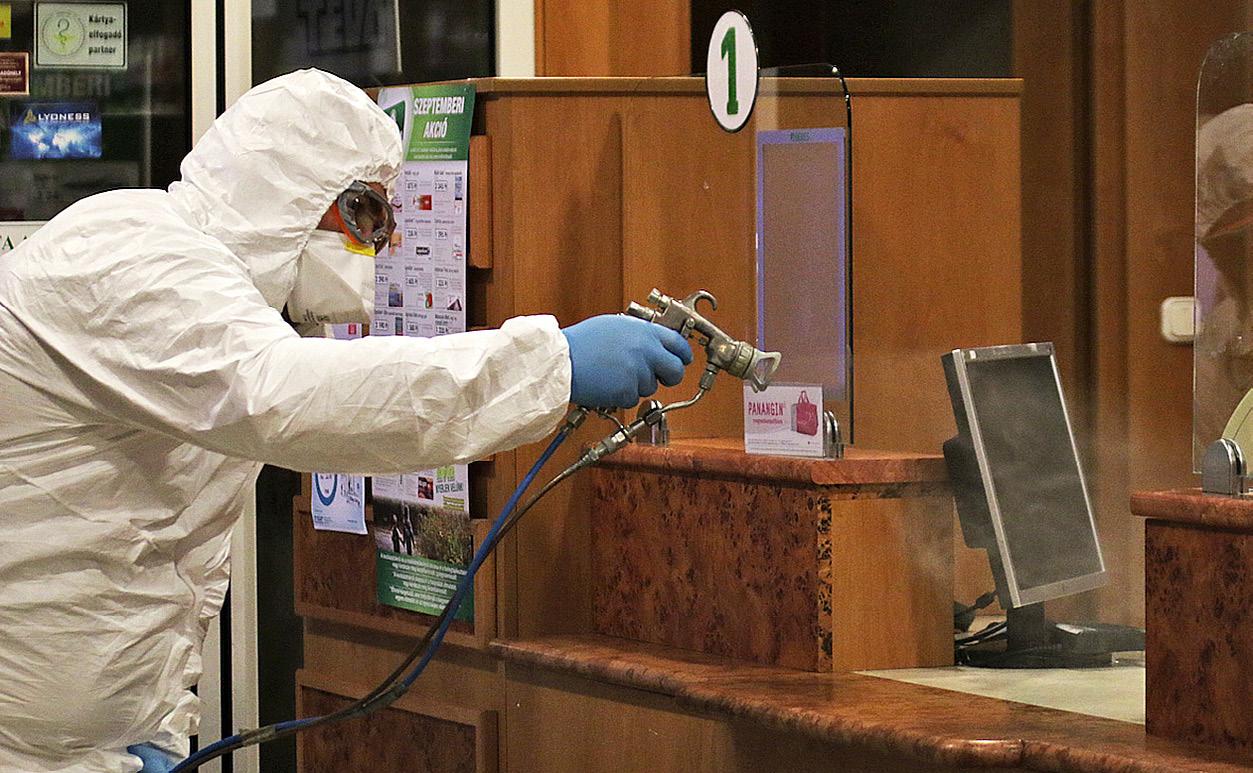
signed up for the coating, but most are domestically based – or the local subsidiaries of multi-national operations, such as Audi and Spar. (One notable exception is Austrian Federal Railways, ÖBB.) Prior to COVID-19, the volume of work doubled each year, and in 2019 the company had revenues of some EUR and are thus potentially deadly transmitters of infection, even if few in the queues eager to get past the X-ray machines are conscious of the risk.
Using industry-standard ATP swab tests, ReSysten measured the results before applying a coating, and three months after application to assess the relative merits of its product.
The results (see chart) were dramatic, a virtual elimination of pathogens on the trays a full 90 plus days after treatment.
FLIGHT-WORTHY
The Budapest-based company also insists its coatings are equally 500,000 from coating in excess of 30,000 sqms of surface area.
“That may not sound like much, but we only coat critical touch areas, not, for example the roof or floor of a tram. In offices, if the building is 1,000 sqm, we coat about 15-20% of that,” Pintér notes. Then, early this year, came the coronavirus.
‘BONKERS’
“Things went bonkers,” is how Shajjad Rizvi, the international development manager, succinctly describes interest in ReSysten as the pandemic exploded. Rizvi, a Briton who joined the company in part to help it respond to the surging demand, says that over the summer, mostly as a result of online approaches, the company has signed distribution agreements in more than 20 nations.
Managing, and particularly financing, such expansion, causes its own headaches. But such is the demand that ReSysten has been able to team
ELIMINATING THE RISK OF INFECTION IN THE AVIATION INDUSTRY
up with local partners who have been effective and, indeed, cost-saving when applied to the flying part of air travel.
“A modern, mid-range airliner, such as the A321 Airbus, working with a modern, low cost carrier, will normally do four trips a day, and that means, if sanitizing with once-use materials, four wipe-downs between flights,” says Shajjad Rizvi, international development manager for ReSysten.
Assuming a time of one hour for a two-person team to wipe down properly, this means each plane needs eight-man-hours per day for sanitation, he argues.
ready to invest themselves in order to become the exclusive distributor for their nation and initiate use of the much needed coating.
“The process of approval in each country varies, and so does the cost. In the Netherlands, for example, it takes a year for the approval process to run its course, and the cost is close to EUR 50,000. We have a partner working on and money, and it can be a real pain,
this,” says Rizvi.
In other countries the barriers are even more daunting. In the United States, gyms and courthouses.
the approval also takes time and the cost can climb into the millions. Again, ReSysten has begun working with local partners to make progress.
to establish regulations and standards for TiO2-based, antimicrobial coatings, and approval is something of a moving target, being written on the hoof. “They don’t even have a process for our type of technology, and we have
to do extra testing. This all takes time you can imagine,” says Rizvi.
These processes have been further complicated by the new sectors seeking protection, including, for example, office buildings, schools, In some cases, countries have yet
WELL-FINANCED
Naturally, given that the photocatalytic properties of TiO2 have been known about for a century (and its ability to destroy pathogens for perhaps half that
BUD AIRPORT – SECURITY CHECK TRAYS – ATP MEASUREMENTS
422640 307829 188003 164713 time), ReSysten is facing stiff, and often well-financed competition, with many more players appearing in the world of coatings.
“Some are using TiO2 as a base, some silver or copper as a base,” says Rizvi. “I guess one area where we differ is, we stress the application is as important as the product, if the coating is not applied correctly you will not get the desired result, such as the one-year effectiveness that we get from ReSysten.”
Indeed, the durability of the Hungarian product is a huge plus in its favor; one competing product in the United Kingdom with an

advertised lifetime of just 30 days
331
Low Wall Tray 965 1582
High Wall Tray RLU Values TO-2020.03.19. Padded Tray RLU Values T1-2020.06.24. 238
Padded Tray Sidewall
Scaled up, such operations will result in a total wage bill of approximately EUR 15,000 per plane per year, not including materials. “We would do the same jet for approximately EUR 5,000, and that covers the material costs of 20 liters of fluid, valued at EUR 3,000,” he says. Naturally, cabin crew or someone would still have to do a litter clean up, but ReSysten would guarantee the surfaces free of infection for an entire year .
The cost benefits to any airline using the system would clearly be huge, which could, naturally, be passed onto the price of a ticket.
“When I recently quoted a ReSysten solution to a low-cost carrier, it came to just EUR 0.12 cents per passenger over the year,” he says.
So far, however, “no airline has yet bitten,” he admits, though he argues take up depends on timeconsuming approvals and is “just a matter of time.”

failed to live up to its hype, and was forced to withdraw the claim.
It is, then, no surprise that ReSysten is very coy about its business secrets. Asked for only the basic details of its production process, the normally voluble Rizvi is uncharacteristically tight lipped. “We buy the raw ingredients; I can’t say more than that. The formula has other elements, not just TiO2.”
GUESSING GAME
With the current explosion of interest, coupled with the uncertainties of approval, ReSysten’s financial future looks full of promise, but the shortterm is something of a guessing game.
“If all 20 plus countries come online – but we are still in the regulatory approval process in many of these, even if some are in the final stages – we are looking at perhaps EUR 0.5 – 1 mln in revenues generated from
ReSysten, as the company explains on its website, uses so-called ATP technology to check the activity level of micro-organisms on a surface, both before and after treatment.
The test is a standard used in medical and pharmaceutical facilities, along with food and drink industries, based on the each country,” says Rizvi. “I’m using pre-COVID and Hungary’s model as a benchmark here, but these countries also have the potential for a lot more.” Astonishingly, ReSysten has financed its development thus far from its founders’ own pockets and generated profits. Yet, despite the global concerns caused by the COVID-19 pandemic fueling unprecedented demand, this small Hungarian company (it currently has a mere 20 employees) is wary of external funding.
“We have always been keen to explore funding, but not at the risk of losing control or direction of the company,” says Pintér, who adds: “We are six years old, have a positive bank balance and no debt. We are not opposed to investment; the added capital injection would fastrack so many aspects [of development]. But, we don’t want investors who are keen on making a quick buck, and want control of the company’s direction.” levels of detection of adenosine triphosphate, or ATP. ATP is a molecule found in and around living cells, and as such it gives a direct measure of biological concentration and health. ATP is quantified by measuring the light produced through its reaction with the naturally occurring firefly enzyme Pintér had confidence in the future well before the onset of the coronavirus pandemic, and his optimism stretches beyond it.
“Coatings are the new world in hygiene, and we will see huge interest and growth in this area,” he argues. “Certainly, COVID-19 has accelerated the demand for ReSysten locally and internationally. But we’ve had six years of growing the company based on the need for increased hygiene solutions, and when COVID-19 is done and dusted, hopefully as soon as possible,
THE ATP TEST: HOW TO MEASURE CONTAMINATION OF A SURFACE
the need for ReSysten will continue.” luciferase, using a luminometer. The amount of light produced is directly proportional to the number of living organisms present in the sample.
Modern monitoring systems are capable of immediately detecting the presence or absence of organic material, alive or dead, on solid surfaces.