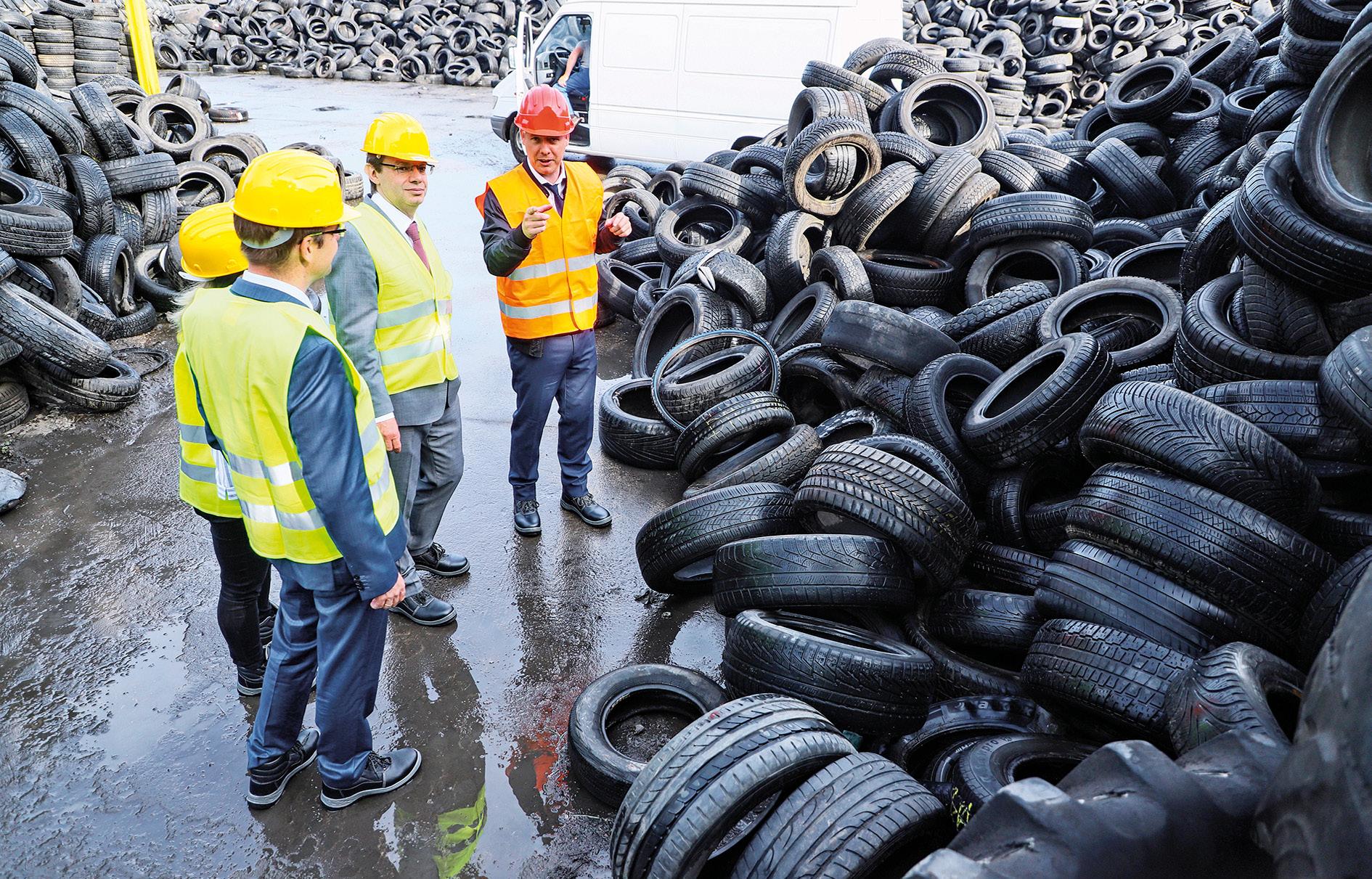
3 minute read
CASE STUDY Old Tires Given new Life in BASF, New Energy Deal
CASE STUDY OLD TIRES GIVEN FRESH LIFE IN BASF, NEW ENERGY DEAL
German multinational chemical company BASF SE has signed what it calls an uptake supply agreement with Hungary’s New Energy, a technology firm specialized in the manufacturing of pyrolysis oil derived from waste tires.
By BBJ Staff
According to the agreement, New Energy, based in Dunaharaszti, just 20 km south of the center of Budapest, will supply BASF with up to 4,000 metric tonnes of pyrolysis oil per year derived from waste tires.
Tire Mountain: Viktor Váradi (right), CEO of New Energy, shows Christian Lach (2nd from right), project lead for ChemCycling at BASF, the waste tires which New Energy is turning into pyrolysis oil in its plant in Hungary.
In a pilot phase, first volumes of the pyrolysis oil have already been utilized successfully in BASF’s Verbund integrated chemical production site in Ludwigshafen, Germany.
BASF says the agreement is part of its ChemCycling project, which was launched in 2018 and aims to achieve the chemical reprocessing of postconsumer plastic waste on an industrial scale. The first commercial products came on to the market this year.
The focus of the project is the use of mixed plastic waste, which would otherwise end up in landfill or incineration. Wrapped up in all of that,
BASF also sees an opportunity to increase recycling rates for end-of-life tires.
BASF feeds the pyrolysis oil supplied by New Energy into the Verbund site in Ludwigshafen, thereby replacing fossil resources. The share of recycled raw material is allocated to certain products manufactured in the Verbund by using a third-party audited mass balance approach. Products which carry the name suffix “CcycledTM” have exactly the same properties as those manufactured from fossil feedstock. Customers can therefore further process them in the same way as conventionally manufactured products and use them in high demand applications regarding quality and performance, such as automotive parts.
“So far, there was no technology that allowed the recycling of pyrolysis oil from tires into high value applications. By further broadening our raw material base to [include] waste tires, we can create a new circular value stream,” explains Christian Lach, project leader for ChemCycling at BASF.
“Moreover, we establish a second recycled feedstock in our ChemCycling project, with which we
can manufacture high-performance products for our customers’ demanding applications,” Lach adds.
DECADE OF DEVELOPMENT
Viktor Váradi, CEO of New Energy, is delighted the partnership with BASF has born fruit. “We spent almost a decade to develop and optimize our technology and are now successfully operating an industrial-scale plant, which turns waste tires into secondary raw materials. This puts us at the forefront when it comes to establishing a circular economy for tires,” he says. “Our objective is to achieve quantifiable environmental benefit. The reduced need for primary fossil resources clearly serves this objective as well as the reduced carbon footprint of the newly manufactured products,” Váradi adds.
BASF and New Energy say they are both committed to work on solutions for the global plastic waste problem. As evidence of that, the two parties have additionally signed an agreement for a feasibility study that targets the adaption of New Energy’s proprietary pyrolysis technology to the conversion of other plastic waste streams.
“The collaboration with New Energy underlines BASF’s ambition to use recycled raw materials in the chemical industry and lead the transition to a circular economy for plastics,” says Lach.
Rubber Residue: Shredded waste tires, ready to be further processed into pyrolysis oil by New Energy. The technology company will supply BASF with up to 4,000 metric tons of pyrolysis oil per year derived from waste tires.

According to New Energy’s website, there are currently three million tonnes of rubber waste generated every year in Europe alone. “When New Energy Ltd. was founded, our aim was to terminate the environmental impact caused by rubber waste by using a selfdeveloped technology which can be a final solution for environmental problems, at the same time can be a profitable investment for investors and besides fully meets all technical requirements,” the company website says. After 10 years of development, it believes it has reached that point.