
5 minute read
ERDC Upgrades Blast Effects Research Capabilities
from America's Engineers: The People, Programs, and Projects of the U.S. Army Corps of Engineers '24-'25
BY MARY MILLER MORGAN
U.S. ARMY ENGINEER RESEARCH AND DEVELOPMENT CENTER
The U.S. Army Engineer Research and Development Center (ERDC) is advancing the study of blast effects with an upgraded facility designed to enhance protection for structures, facilities and most importantly, people. From testing military helmet designs to evaluating walls and high-performance materials, the Geotechnical and Structures Laboratory’s (GSL) updated Advanced Blast Load Simulator (ABLS) facility in Vicksburg, Mississippi, allows researchers to get a first-hand look at blast effects in a controlled environment.
Carol Johnson, Ph.D., a research civil engineer at GSL, leads the work at the ABLS. “The Blast Load Simulator [BLS] devices are more efficient and economical for testing rather than going out to the field. Here in Vicksburg, we can conduct more research and gather data at a faster rate with significantly reduced costs,” Johnson said. “We can then confirm a final design and take it out to the field to get validation.”
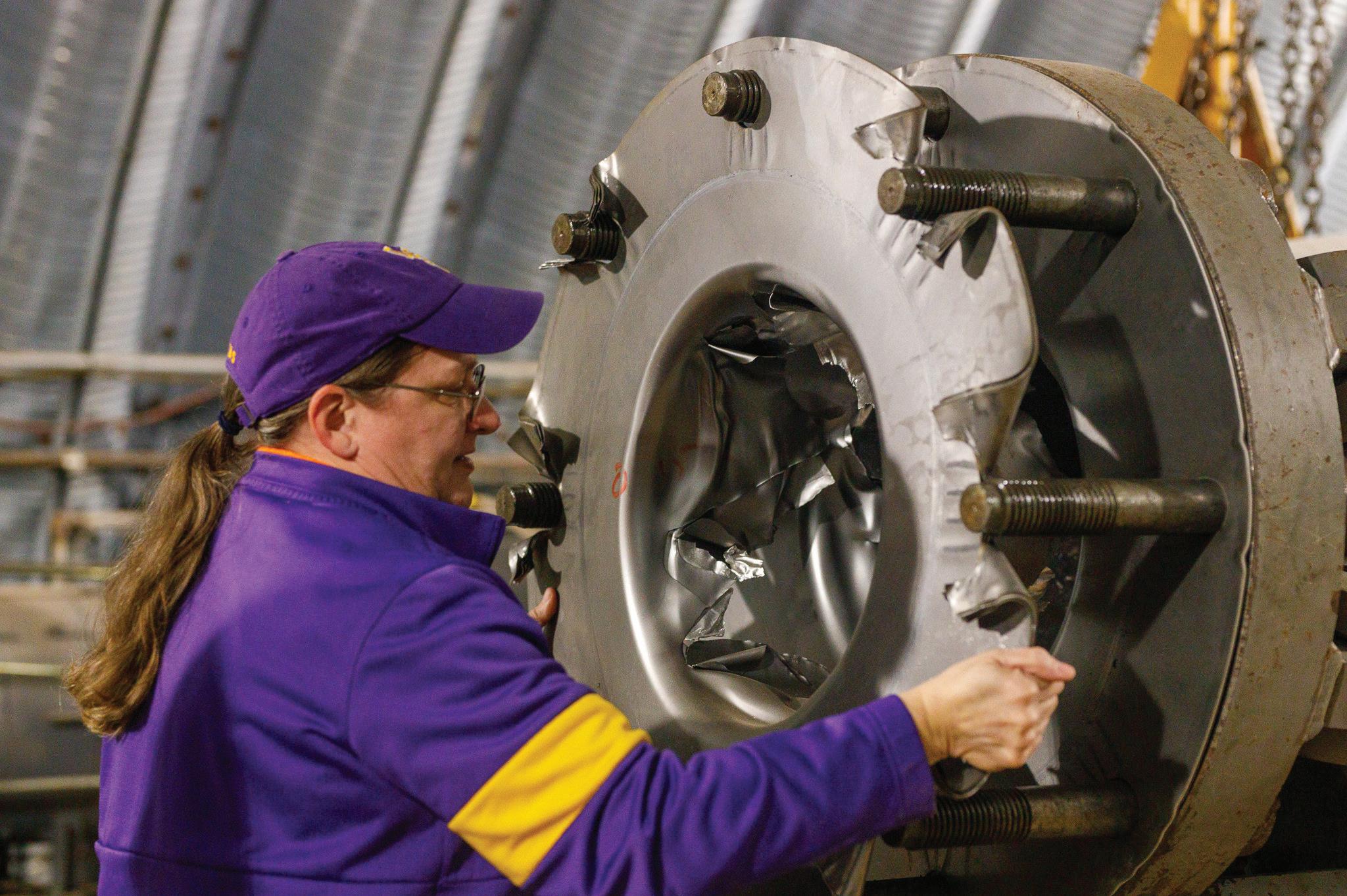
The facility simulates explosive devices detonating at a certain distance from a target. Research engineers can replicate the air blast associated with that explosive event, and from the results, understand the capacity of a structure, the response of buildings, or how to better retrofit structures.
The original BLS is a compressed gas-driven device with a pressure vessel on the front end. Research engineers pump air and helium into the pressure vessel and use steel and aluminum diaphragms to confine the gases. While under pressure, a mechanical striker impacts the diaphragms and forces them to rip and rupture. The blast wave then travels down the expansion cone, through the rings, and hits the target at the far end. After the blast wave impacts the target, it rebounds and travels back through the rings and vents out of the gaps of the BLS.
“New components were recently added to the BLS to expand the target size of 71-by-53 inches to a maximum target size of 8-by-8 feet,” Johnson said. “The largest experiment conducted in the original BLS replicated a maximum pressure and impulse combination of 55,000 pounds of TNT roughly 120 feet away from the target.
“The BLS is about 20 years old, so the new ABLS devices take advantage of a new patent and technological developments in this area. Due to target size limitations in the BLS, we’ve had to evaluate individual components in our experiments instead of testing full-scale targets,” she said. “The new ABLS allows us to conduct full-scale testing within minutes as opposed to hours.”
The new ABLS is a combustible gas-driven device with a booster chamber on the front end. Research engineers fill the booster chamber with a mixture of fuel and air and then detonate it, causing a “fireball” effect. Once initiated, the shock wave from the booster detonates the ethylene and air behind it and sends the blast wave toward the target.
One type of target tested is fully reflected, and typically consists of windows, walls, and doors. The other type is referred to as diffraction/engulfment experiments, which means a blast wave is sent toward an object and researchers then study how the blast propagates around that target. An example of a diffraction experiment would be placing a mannequin in the target space and testing for traumatic brain injury or personal vulnerability.
“The ABLS can hold a maximum target of 14-by-14 feet, and being able to conduct full-scale testing allows us to expand our knowledge base,” Johnson said. “The ABLS has increased our performance envelope, because we have the ability to conduct very low reflected pressure experiments required for personal vulnerability research and higher reflected pressure experiments required to evaluate blast designed structural elements – all in one device.”
For example, multiple mannequins, each with different protective equipment, can be tested simultaneously. They can be rotated at different angles to see the various results. Even an entire wall system with blast-designed window and door framing can be evaluated in a single experiment within the ABLS.
Highlighting the versatility of the ABLS, Johnson said “if customers bring in something that can fit in the space of one of these target vessels, we can and will shoot it for you.”
The facility also includes a functional, smaller prototype of the ABLS that can support a target size of 4-by-4 feet and is generally used for testing helmet designs, hearing protection, or high-performance material samples.
Each of the simulators can be operated daily, with testing starting small and advancing to larger experiments, which can be more efficient and economical than field evaluation.
The data generated from the BLS and ABLS experiments is also shared with ERDC engineers and researchers to validate and develop new numerical models for blast protection.
“The work we do here helps us better protect our structures, facilities, and our Soldiers,” Johnson said. “ERDC makes a huge difference in not only protecting our warfighters, but also making our nation and our world safer and better.” AE
–
Visit www.Americas-Engineers.com to sign up for a free print edition of our annual publication and to join our weekly newsletter.