
7 minute read
Features
Raise questions to select the correct equipment
In this article, Hydro Systems’ Global Director of Brand and Marketing Communications, Alistair Blair-Davies
Advertisement
explains how selecting the correct chemical-dispensing equipment is one of the most crucial decisions you
will make. Without being sure of delivering safe, cost-effective operation and high-quality cleaning – while
responding to all of your customer’s key requirements for quick installation, reliability of dilution, ease of use
and maintenance – you risk damaging the most important asset you have – your firm’s reputation.
Have you ever been disappointed by the performance of a chemical dispenser? Did the model turn out to be nothing like the sleek and efficient problem-solving unit that was promoted to you by the manufacturer? Were you even certain that your choice would have been able to satisfy your customer’s growth and aspirations in the future – let alone their immediate needs?
There is much to bear in mind when you choose a chemical-dispensing system. Avoid being seduced simply by price, by one highlighted feature, or assurances that nothing else on the market is better able to optimise the potential of your chemicals. Otherwise, when there is an irate caller on the line who stood in a pool of congealed chemical residue, reeling from a stream of disgruntled employees and disappointed customers, it is you who will be bearing the brunt of their aggravation.
Asking the right questions Above all, it is about the total package that you offer: the system you choose has to deliver a mutually beneficial high level of performance. What is right for you, is right for your customer – and vice versa. With what can appear to be a bewildering number of dispensers on the market, how do you ensure that you are giving your customers exactly what they want? Doing your research and asking the right questions is essential. If you do so, it will help you to maximise the benefits and lifespan of each unit, making for a smooth and profitable long-term relationship. From ensuring efficient dispensing, you can immediately begin to deliver a range of significant benefits to your customers, which you can promote in order to gain and retain business. These include improved environmental friendliness and cleanliness, in addition to labour cost savings, increased productivity and safety. A virtuous circle to the bottom line. Employing a dispensing system that delivers the right amount of chemical every time eliminates wastage and ensures that chemicals are not dumped where they can have a negative effect on water supplies and your brand. A closed dispensing system significantly reduces waste packaging that would otherwise end up in landfills. Greenhouse gasses are also reduced because less fuel is needed to ship chemicals in concentrate form.
With automatic dilution, there are no guessing games on whether too much or too little chemical is being used. The right dispensing equipment reduces customers’ cleaning costs by up to 30 percent by accurately diluting the proper amount of chemical – supporting their bottom line. Getting it right, safe and productive by automatically mixing concentrates with water, there is less direct contact with potentially hazardous chemicals, and no heavy containers to carry. Properly diluted chemicals also help to reduce the risk of litigation from dangerous slip-and-fall accidents. Dispensing systems avoid manual measurement, while correct dilution eliminates the need to fix areas that were not properly cleaned, resulting in a reduction of labour costs.
When cleaning chemicals are consistently diluted to the manufacturer’s specifications, it allows the concentrates to work at their full potential. Overly rich mixtures can leave slippery residues and even damage surfaces, while weak mixtures can leave germs remaining. Each scenario could leave the customer pointing accusingly at you.
Thinking ahead Try to be strategic and think ahead. You should base your selection decisions on being able to respond to both the current and future requirements of your customers. Make sure that features are well-suited for their application or they may not function as efficiently as you would like, and that units are user-friendly and enhance productivity. You will want any system to be easy to install to minimise potential problems, whether this is for your in-house team or any contractors you employ to do the job. Bear in mind that, although some dispensers are designed to handle only one or two chemicals, others allow for multiple options, which can improve cleaning efficiency. It is important to pick a manufacturer whose product line incorporates this range of functions. Water-pressure problems can be responsible for inconsistent dilution rates. Look for dispensing systems that address this, such as those that contain a regulating component. There are other features that can help to narrow your
choice such as easy-locking buttons on units, technology that enables perfect dilution rates every time, and the availability of extra space for maintenance and tubing purposes.
Maintaining dialogue and performance Maintain an open dialogue with your customers. Education and awareness is key. If your customers don’t understand how to use all aspects of the system, how will they get the most out of it? Make sure your installers remember to follow the proper plumbing codes. Don’t let them place the dispenser where it seems most handy. If the chemical is higher it’s possible it could be siphoned out. This means that too much is used – driving up costs – while delivering a negative impact on performance and productivity. To enable consistent and continuous use, maintenance is crucial. Regular maintenance ensures great cleaning performance and limits chemical waste, loss of productivity and added costs.
Hydro solutions Hydro’s dispensing systems are in use across a number of applications, including cleaning and sanitising, animal health, irrigation, and laundry, and feature user-friendly designs and minimal maintenance. They utilise three key technologies – Venturi, peristaltic pumps and volumetric injectors. Hydro Systems’ wide range includes models that deliver dilution accuracy regardless of fluctuations in water pressure, dispense multiple diluted products at multiple flow rates, have features that make switching from one function to the next incredibly easy, and exhibit durability to improve resilience against chemical corrosion. Just some of the many features that will enhance the use of your chemicals and the regard in which they are held among your customers. Access to such a comprehensive range of features means your customers reap the benefits more quickly. If you provide a bad dispenser, it has the potential to interrupt the smooth flow of chemicals and goodwill. Yet conversely, it will increase the flow of negativity to a flood that you will find very hard to control. This will impact your customer retention, industry perception, brand image and, ultimately, affect your profitability. The choice is yours.
For more information, visit: www.hydrosystems.com

What to look out for when purchasing a dishwash-dosing system
Maintaining high hygiene and cleaning standards in commercial kitchens is paramount to obtaining good food
hygiene standards. With this in mind, buying the right equipment to maintain the standards is essential. As the
number of people dining out is increasing, so increases the amount of dirty cutlery, crockery and glassware.
Therefore, dishwashers need to perform at their optimum to ensure clean results every time.
Dishwash dosing systems ensure optimal dishwashing performance as they consistently and accurately dose dishwashing detergent and rinse aid, taking out the guesswork and minimising contact with the chemicals. There are many dishwash-dosing systems on offer, which can make choosing the right system for your business slightly daunting, with many factors to be aware of. Brightwell Dispensers offers some important points to consider when choosing a dishwash-dosing system for your business:
Compact product design Chemical-dosing systems are often installed in areas with limited space; therefore, compact and robust product design is very important for ease of access to the system.
Accurate and consistent dosing of dishwashing chemicals A system that delivers accurate and consistent dosing of dishwashing chemicals is essential to deliver highquality cleaning results.
Cost-efficient equipment Chemical-dosing systems allow businesses to maximise cleaning performance and forecast their cleaning costs in an efficient way. In addition, these systems accurately dispense the correct amount of chemical needed each time, without the risk of chemical spillage, dosing the wrong amount and pilferage.
Easy installation and maintenance Ease of installation and maintenance is vital so that the job can be done quickly and efficiently, while minimising the impact on the kitchen operation itself.
System access codes When it comes to dosing systems, it is important to ensure that only authorised personnel have access to the system. This is so there is no tampering with the unit.
Customer service Suppliers should offer a good pre- and after-sales service as well as customer service. It is important that a supplier is interested in the long-term success of your company and is able to provide installation, maintenance advice
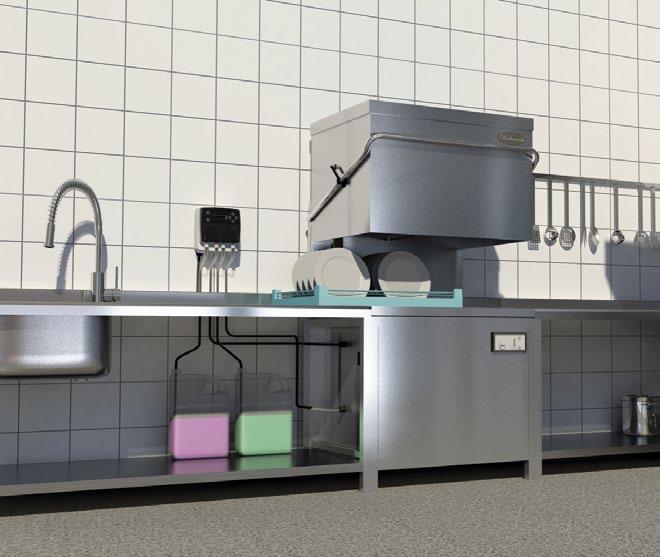
and training for the equipment you purchase.
To meet the demands of today’s commercial kitchens, Brightwell Dispensers released the Quantura dishwash-dosing range. Quantura is a versatile system that provides precise and consistent dosing solutions for a variety of commercial dishwasher applications. This includes glass, underthe-counter, single-tank, and tunnel/ conveyor dishwashers.
Compact in design, pre-wired for easy installation and with the option to set and use access codes for security, Quantura offers businesses an easy and efficient way to keep dishes clean, every time.
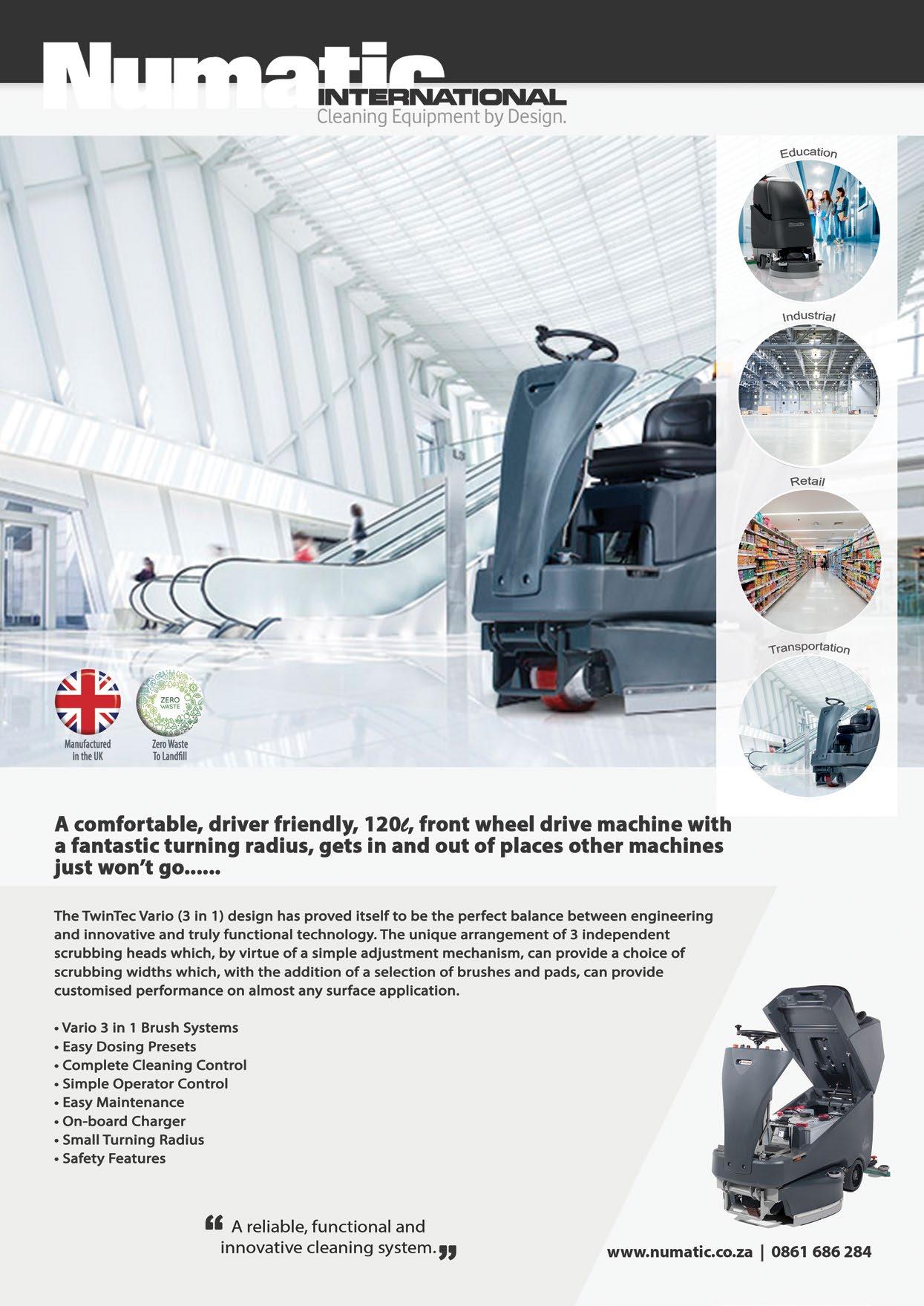