In this issue:
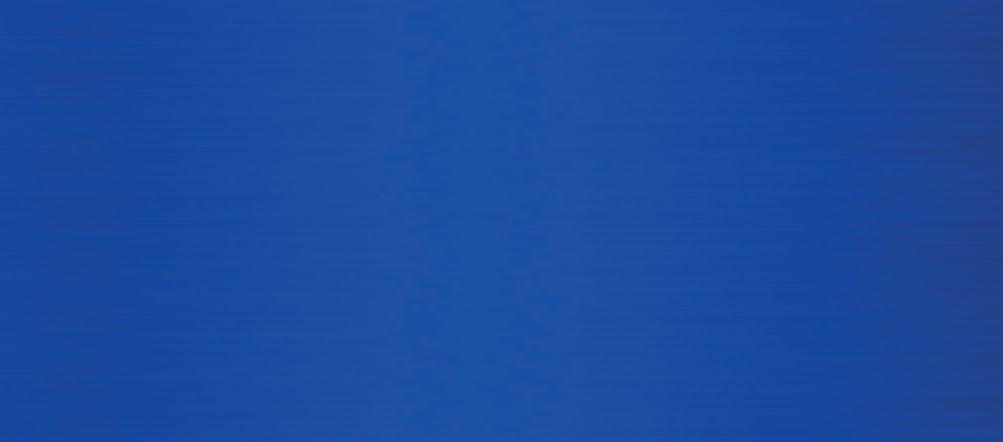
Effective hand hygiene practices

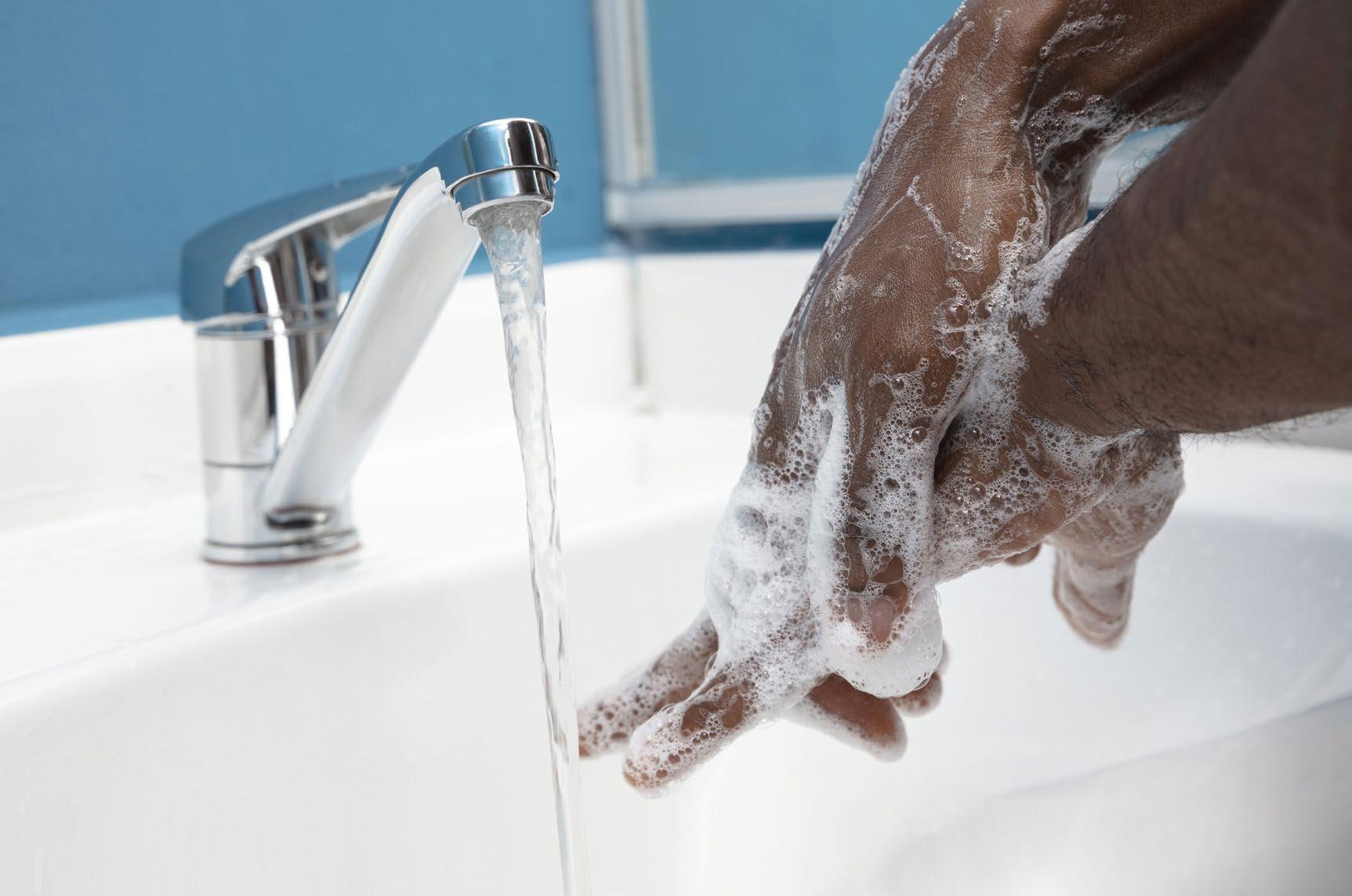
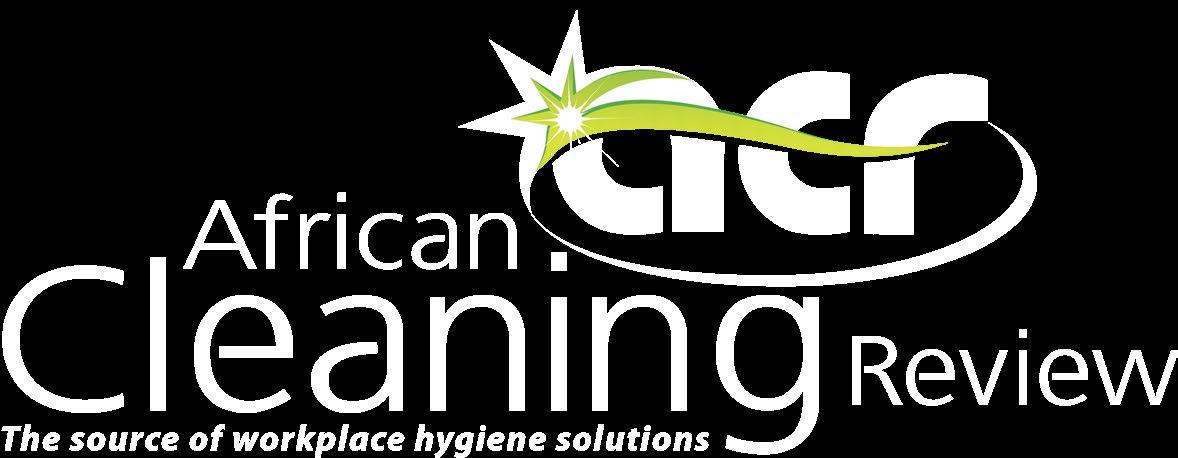
Cleaning hard floors
Solar and photovoltaic panel cleaning
The premier development event for Africa's cleaning industry leaders, created for your personal and professional success.
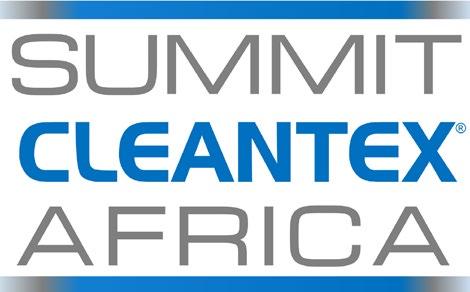
In this issue:
Effective hand hygiene practices
Cleaning hard floors
Solar and photovoltaic panel cleaning
The premier development event for Africa's cleaning industry leaders, created for your personal and professional success.
Don't miss the opportunity to attend the third, one-day Cleantex Executive Summit programme with interactive and engaging sessions on customer experience, innovation, strategy, leadership and sales management to help you build your company's vision for success. The Cleantex Executive Summit also offers great networking opportunities for hygiene & cleaning professionals. Association members qualify for a discount Limited number of sponsorship opportunities as well as niche table-top exhibition stands on offer.
LAGOON BEACH HOTEL
CAPE TOWN | SOUTH AFRICA
, Janine Botha, GM, Numatic International SA
For more information and/or to book for this executive cleaning industry event, contact: nande@cleantex co za | +27 11 238 7848
Endorsed by: Powered by:
"I have learned so much today! The speakers and topics were phenomenal. Cleantex Executive Summit '22 was exceptional and great value for money"
contents
MAY/JUNE 2023
VOL 24 NO. 3
Cover
The Unilever Professional range of commercial cleaning products helps you to easily, quickly and safely clean key areas of your business –giving you the best results with minimum effort. Read more on page 16 or visit: www.unileverprofessional.co.za
African Cleaning Review is aimed at end-users, contractors and suppliers of products and services to Africa’s Cleaning, Hygiene, Maintenance, Laundry, Pest Control and Facility Management Services, industries. It is published every other month by: e-squared publications.
Tel: +27 (0) 11 238 7848 or +27 (0) 72 611 1959
PO Box 1976, Halfway House, 1685, South Africa
Email: africancleaningreview@cleantex.co.za
Website: www.africancleaningreview.co.za
@AfricanCleanMag AfricanCleaningReview
african-cleaning-review
Publishing Editor: Johann van Vuuren
+27 (0) 11 238 7848 or +27 (0) 72 611 1959
Email: africancleaningreview@cleantex.co.za
Advertising: +27 (0) 11 238 7848 or +27 (0) 72 611 1959
Email: africancleaningreview@cleantex.co.za
Operations and Accounts: Nandé Jacobs
Email: africancleaningreview@cleantex.co.za
Opinion
• Business continuity – how to keep going in the face of crisis
Industry News
• Ground-breaking concept for sustainable tissue production
• Shaping the future together in a strategic partnership
• Recycling unit adds capacity to company’s fleet of vacuum and jetting trucks
• Global campaign accelerate action: SAVE LIVES – Clean Your Hands
• Recovered plastic dispenser contributes to sustainability targets
Features
Hand hygiene
• Conquer colds and flu this season with effective hand hygiene practices
2
4
8
• Wash your hands, save a life Hard Floorcare 20
• Cleaning hard floors – a specialised function
• Different choices of manual floor mopping material provide diverse hygiene outcomes – study
• Creating a floor cleaning toolkit
Editorial
• Reduce absenteeism in the workplace by being smarter 10 around your work area – Hygiene Systems
• Award-winning Tork VR Clean Hands Training now 11 available free of charge
• Flexible, cordless and convenient cleaning of hard 23 floors – Numatic
• New scrubber-dryer delivers true value for money – Hako 26
• Warning of near-pandemic level outbreak of cockroaches Educational
• How we dry our hands can affect the spread of 14 viruses –
•
• New city and venue boost international scope of Italy’s cleaning showcase – ISSA PULIRE 2023
•
•
Products 31
• Cleaning with dry ice blasting
Planned features for 2023
Feature sections in every issue:
• Laundry and dry cleaning review
• Facilities management review
July/August issue: Editorial deadline 15 June
• Healthcare cleaning and hygiene
• Wipes and wiping solutions
September/October issue: Editorial deadline 18 August
• Sustainability in cleaning
• Washroom hygiene
November/December issue: Editorial deadline 13 October
• Hospitality cleaning solutions
• Retail cleaning solutions
All editorial contributions can be sent to the editor who reserves the right to publish editorial based on the strength of its content. No articles or photographs may be reproduced, in whole or in part, without written permission from the publishers. Although every effort is made to ensure the accuracy and reliability of material published in African Cleaning Review, e-squared publications and its agents can accept no responsibility for the veracity of the claims made by contributors, manufacturers or advertisers. Copyright of all material published in African Cleaning Review remains with e-squared publications and its agents. Official
If there is one thing that was entrenched during the pandemic years, it was that regular handwashing is one of the best ways to remove germs, avoid getting sick and to prevent the spreading of microbes to others. Now, as we are entering the winter season and respiratory infections such as colds and flu are becoming more prevalent, it is imperative to continue spreading the message that clean hands plays a crucial part to combat the spread of disease and protect lives. Leading on from the World Health Organizations’ World Hygiene Day celebrated on 5 May, this issue takes a closer look at effective hand hygiene practices and products.
As part of our hard floorcare feature, we publish the findings of a recent study relating to how different choices in manual floor-mopping materials can provide diverse hygiene outcomes. Floors are the largest surface routinely cleaned in commercial settings and are typically contaminated with higher levels of bacteria.
And, in one of our two educational pieces, we explore the emergence of a new avenue in commercial cleaning services, that of solar and photovoltaic panel cleaning. With South Africa’s ongoing energy crisis in mind and the fact that many companies are hit by massive costs due to loadshedding, a recent report revealed that the country’s biggest retailer now has enough solar panels to cover 24 soccer fields, and this is growing. This is another example of an opportunity created for cleaning professionals to provide a specialised cleaning service. Despite all the daily challenges of conducting business, there is no time for complacency, let us move forward and foster the real value of clean.
Enjoy reading these and other topical issues.
The COVID-19 pandemic has taught the real estate sector that businesses with comprehensive continuity plans in place are more likely to overcome challenges quickly in the face of a major crisis.
Jason Griessel, who heads up strategic risk management at Broll Property Group, says when COVID-19 was just a murmur, no-one realised the profound impact it would have on the way people do business.
“The pandemic didn’t fall into what we would normally term an emergency response framework. It was ultimately a business continuity and resilience exercise. People had to figure out how to scale their businesses to enable communication – both upwards and downwards. After all, without managing, communicating and practicing a duty of care over your employees and – in some instances – your vendors, you don’t have a business.”
“Notably, in interfacing with client portfolios, we have discovered that businesses are more prepared than ever to put comprehensive business continuity plans into place,” he adds.
He says resilience and continuity are the holy grail of sustained business success. “For resilient businesses that have the correct resourcing to continue operating and servicing their portfolios, crises can present unparalleled opportunities for growth in the market.”
When the pandemic hit South African shores, businesses that were better prepared for emergencies started to gain market share. This was also evidenced during the KwaZuluNatal riots: some vendors and service providers were unable to deliver, creating a gap for others, who were better prepared, to thrive.
Griessel says COVID-19 was unique
because the business had to manage the increased sensitivity of employees while maintaining the integrity of facilities. “I haven’t met anybody who enjoys getting screened, vetted, probed or fingerprinted. Going into COVID-19, we had to address the psychology of how to make it easier to comply while not reducing the level of security and risk.”
Looking more broadly, Griessel is not sure that the cost of precautions going into the pandemic was beneficial to the wider population. “Going forward, I think we need to learn from the lessons of lockdown and its catastrophic impact on the economy and society, especially in respect of the accelerated rates of suicide, divorce and gender-based violence.”
Once continuity plans are in place, Griessel says businesses need to identify, train and support the people who are going to operate the plan, as well as conduct testing and reviews. “Employees are every business’ most important tool in managing crises. No artificial intelligence can manage crises, which often require personal and interactive inputs and processes.”
Going forward, property owners who own the cold chain distribution centres that power the country’s justin-time medical and food deliveries to commercial hubs need to consider national key point standards when they develop new builds. This is to be able to sustain an attack by the civil population. “Security and safety considerations need to supersede aesthetics,” notes Griessel.
He says businesses need to ensure their emergency frameworks and business continuity planning is kept up to date. “COVID-19 was a long version of a crisis, which gave rise to multiple mini crises. This was compounded by abnormal environmental systems, for example, we had two 100-year events, drought and flooding took place in 2022, an anomaly for us.”
Business continuity planning has become the cost of doing business in higher risk emerging markets like South Africa. “Globally, there is an acceptance that you need to provide resourcing for a black swan event within an organisation. Instead of lip service to fire and emergency evacuations and pandemic readiness, people are taking them seriously. There is greater willingness to look at proactive risk
management to be able to come out ahead,” adds Griessel.
He says more work needs to be done on identifying and forecasting risks across the sector. “There is enough data for forecasting: by anticipating risks, the industry can look at innovative solutions for solving them. Solutions are only going to be achievable at scale. One or two portfolios aren’t going to be able to do it by themselves.”
“We need to look at the impact of the pandemic on the likes of the South African Special Risk Insurance Association (Sasria) in terms of special risks and insurance costs. These are all costs that are already getting passed to the consumer. If we can’t put better solutions together to manage the risk, the costs will keep climbing and that will be detrimental to the economy.
Importantly, the pandemic has taught organisations that if they do not have some form of continuity planning and crisis management in place ahead of crises, it is almost impossible to put one together in the midst of one. This type of reactive response can triple or quadruple costs and render the business ineffective.
“There is enough data for forecasting: by anticipating risks, the industry can look at innovative solutions for solving them. Solutions are only going to be achievable at scale.”
Hygiene and health company Essity has entered an exclusive partnership with the global technology company Voith to develop a new tissue making process that will reduce energy and CO2 emissions while cutting water consumption by up to 95 percent.
After becoming the first company in the industry to produce tissue in a CO2-free production process using renewable hydrogen a few weeks ago, and producing high-quality tissue from agricultural waste a year and a half earlier, the hygiene and health company Essity is set to achieve yet another major milestone in the company’s commitment to achieving net zero emissions of greenhouse gases by 2050.
In an exclusive partnership with Voith, Essity will collaborate in the
development of a new disruptive concept that revolutionises and rethinks tissue manufacturing.
Compared to conventional paper making processes, this process enables CO2-neutral tissue production, and reduces freshwater consumption by 95 percent, and energy consumption by up to 40 percent.
“Sustainability is integrated into Essity’s strategy for long-term profitable growth. We are committed to reducing our environmental footprint and achieving net zero emissions by 2050. The partnership with Voith is yet another concrete example of this,” says Magnus Groth, President and CEO of Essity.
The initiative incorporates both Essity’s extensive expertise in the tissue industry and Voith’s know-how as a leading technology supplier.
Efficient facility cleaning requires a combination of machines, cleaning robots and manual tools to achieve the best hygienic result optimising consumption with both economic and environmental benefits.
This is the premise behind the announcement of a strategic partnership between TTS and Kärcher in which the two companies are joining forces and pooling resources and capabilities in order to offer customers around the world their wide range of products and services in the future.
With the TTS Equipment, Kärcher complements its portfolio of solutions for building cleaning and continues to position itself as a full-range supplier. TTS benefits from Kärcher’s worldwide brand awareness and comprehensive product range and, thus, expands its market position.
TTS specialises in professional manual equipment, and designs ergonomic and effective solutions for any environment such as hospitality,
healthcare and high traffic areas. Marco Cardinale, Vice President: Floor Care Solutions at Alfred Kärcher SE & Co. KG, explains, “we already offer products in the manual tools sector, but with the participation in TTS, we will complete and strengthen our portfolio. TTS will act as our competence centre managing the supply chain for manual tool equipment.”
The close co-operation is not only a good idea from an organisational point of view; the two family businesses also pursue a similar strategy in terms of corporate management. Currently, TTS Cleaning S.R.L. is making the transition to the second generation, with an even stronger focus on the future development of the company.
Renato Zorzo, CEO and owner of TTS Cleaning S.R.L., said, “with Kärcher, we have found a strong partner to rise our brand visibility opening up new markets and channels, expand production and increase our competitiveness. In addition, we can
“As the full-line supplier to the paper industry, we have set ourselves the ambitious goal of being able to realise CO 2-neutral paper production by 2030,” says Andreas Endters, President and CEO of Voith Paper. “The fact that we have developed this new process is an important milestone in the industry and demonstrates our high level of innovation. We are very pleased to have found a suitable partner in Essity, who shares our objective of climateneutral paper production.”
Successful test runs have already taken place on a laboratory scale, and the concept is now being transferred to a dynamic process. A pilot phase will be launched later this year before being implemented industrially.
Read more about Essity’s journey to net zero here
now combine our innovative approach to manual tools with innovative cleaning technology from Kärcher.”
TTS and Kärcher pursue a similar strategy in terms of both organisation and management, which lays the basis for a winning partnership that is set to revolutionise the cleaning world. For clear allocation and good market visibility, Kärcher and TTS have decided on a co-branding approach with both logos as seen in the image above.
Bokokotla Motshabo Construction & Projects, a Rustenburg-based company offering civil and structural construction services, as well as heavy-duty machinery rentals, has purchased a sixth high-pressure vacuum truck, procured from Werner Pumps, to add to its existing fleet. While the previous five truck units have either been vacuum trucks or combination vacuum and jetting trucks, the sixth one is an Amanzi Recycling Unit.
Bokokotla Eric Mahlatji, Director of Bokokotla Motshabo Construction & Projects, says the company has been in operation since 2012 and strives for continuous growth. “We are a family orientated business; we believe in the future of our young ones and that providing job opportunities will guarantee better futures for our children. Our motto is ‘Unity is the Power’ and we have a vision of growth,” he added.
Mahlatji says the new recycling truck is an important addition to the company’s jetting and pumping equipment, as it will increase the business’s capacity and enable it to service customers’ needs more effectively and efficiently.
Sebastian Werner, MD of Werner Pumps SA, says the water-recycling truck units are a recent addition to its range of 100 percent locally manufactured high-pressure vacuum and jetting equipment. “The benefit of the recycling unit is that it offers both wet and dry suction capacity and the ability to use water obtained
from sewer lines onsite,” he explains. “It’s an ideal solution for cleaning sewer and stormwater lines, and for municipal applications. The recycling unit saves up to 168,000 l of clean water per 8-hour shift, which means it caters for South Africa’s water scarce environment and is available in various forms and sizes.”
World Hand Hygiene Day was celebrated on 5 May with the message that germs are everywhere, so we should make handwashing with soap and water a healthy habit to protect ourselves and our families from getting sick.
According to the World Health Organization (WHO), hand hygiene saves millions of lives every year when performed at the right moments during health care delivery. It is also a smart investment that offers exceptional return for each dollar invested. Clean care is a sign of respect to those who seek care, and it protects health and other workers who provide that care.
Now is a critical time when countries across the world need to accelerate implementation of lessons learned from the COVID-19 pandemic and increase investments to close gaps in infection prevention and control (IPC), including hand hygiene. Indeed, many countries are demonstrating strong engagement and advancements in scaling-up those actions, but overall, the progress is slow, and the gains are at risk.
The WHO’s message is clear; together, we can galvanise action on preventing infections and antimicrobial resistance in health care. Strong and engaged communities of health workers, policy makers and civil society organisations (CSOs) can accelerate and sustain action at the point of care to keep people safe and healthy.
For World Hand Hygiene Day 2023, the WHO put CSOs into focus. Driven by their passion, values and strong social justice agendas, and often in close proximity to the communities
they serve, CSOs can spearhead and accelerate change at local, national and international levels.
WHO calls on all CSOs and other partner organisations (e.g. members of the Global IPC Network) to engage with the World Hand Hygiene Day campaign and accelerate progress at achieving effective hand hygiene at point of care.
For more information or to join the campaign visit: www.who.int/campaigns/world-handhygiene-day/2023
SC Johnson Professional recently launched a new washroom soap dispenser made from recovered coastal plastic.
The SCJ Professional Proline WAVE 1L washroom soap dispenser is made from 70 percent recovered coastal plastic, which is post-consumer recycled waste plastic collected on land within 50 km of an ocean so that it doesn’t reach oceans or landfills.
Each SCJ Professional Proline WAVE dispenser is the equivalent of 16 x 500ml waste plastic bottles that have been prevented from reaching the oceans or landfills in vulnerable coastal areas where there is little formal waste collection infrastructure.
Eight million metric tonnes of plastic reach the world’s oceans every year, equating to a rubbish truck full of plastic being dumped into
the ocean every minute and this is an issue around the world.
SC Johnson Professional CEO, Katja von Raven, said: “in the US and Europe, SC Johnson has already seen successful launches of bottles made from 100 percent recovered coastal plastic in Mr Muscle and Windex product ranges, thanks to the company’s global partnership with Plastic Bank. We are now excited to be bringing this truly innovative approach to professional markets with our Proline WAVE soap dispenser.”
“In our extensive market research with facility management professionals, we found that 91 percent of respondents believed that their choice of a skin care dispenser can contribute to meeting their business’s sustainability targets. So, by leading the way with our new dispenser made from recovered coastal plastic, we’re allowing our customers to act immediately on a topic they care about.”
For more information visit: www.scjp.com
Unfortunately, we are approaching the cold and flu season – that time of the year when everyone seems to get sick. And it’s not just in our heads. Scientists recently established the biological reason why we get more respiratory illnesses during the winter season. It is because cold air damages the immune response occurring in the nose.1 According to the study, reducing the temperature inside the nose by as little as 5 °C kills almost 50 percent of the billions of virus- and bacteria-fighting cells in the nostrils.
While cold and flu season is inevitable, there are ways to combat germs from spreading in your facility to help keep your building patrons healthy, according to Cintas Facility Services. While easier said than done, hand hygiene combined with thorough facility cleaning is a deadly weapon against pathogens and can significantly reduce the spread of infectious disease.
According to the USA Centers for Disease Control (CDC), handwashing is one of the best ways to protect yourself and your family from getting sick.2 While handwashing is simple and one of the most effective ways to prevent the spread of germs, this simple task is, unfortunately, not performed by everybody. In fact, a recent survey found handwashing frequency decreased 25 percent among adults compared to when the coronavirus first occurred.3
When it comes to hand hygiene, education is key. Dr William Sawyer, a hand hygiene and infection prevention
expert, founded the Henry the Hand Foundation in 2001 when he realised the need to educate both children and adults regarding the important life skill of effective hand hygiene to promote health and wellness. Endorsed by the American Medical Association and the American Academy of Family Physicians, his science-based multi-media and multi-sensory hand hygiene behaviour modification programme teaches hand hygiene, respiratory etiquette and cross contamination awareness using four key principles which include:
1. Wash your hands when they are dirty and before eating.
2. Do NOT cough into your hands.
3. Do NOT sneeze into your hands.
4. Do NOT place your fingers into your eyes, nose, or mouth.
These easy-to-follow principles can help everyone stay healthy this winter season and beyond. Facility managers can post signage throughout their building in strategic places, such as, washrooms and kitchen areas to remind building occupants of these four principles along with the correct way to wash hands. The CDC recommends scrubbing hands together with soap for
at least 20 seconds using clean, running water and either air drying or using a clean towel to dry.4
In addition, implementing a hand sanitiser programme in your facility can also help boost hand hygiene compliance. Place hand sanitiser stands in high traffic areas, kitchens, break rooms, or anywhere soap and water are not readily available. Also, the type of hand sanitiser used can make a huge difference in compliance. Many sanitisers on the market can have a drying effect on hands, which may discourage patrons from using it. It’s important to select a quality sanitiser that is effective, yet gentle enough for everyday use. Look for a formula that kills 99.9 percent of bacteria and that contains a moisturising agent to help keep hands soft and protect against drying skin.
Sources:
[1] https://www.cnn.com/2022/12/06/health/ why-winter-colds-flu-wellness/index.html
[2] https://www.cdc.gov/hygiene/personalhygiene/hands.html
[3] https://www.bradleycorp.com/handwashing.
[4] https://www.cdc.gov/handwashing/whenhow-handwashing.html
Hand hygiene is the process of cleaning your hands to remove any harmful germs and bacteria that may be present. It is a crucial step in preventing the spread of infections and diseases. Practicing proper hand hygiene is especially important in healthcare settings, where the risk of infection is higher, but it is also important in everyday life to prevent the spread of illness.
The World Health Organization (WHO) recommends that hand hygiene should be performed in several situations, including before and after touching a patient, before and after performing a medical procedure, after exposure to bodily fluids, after touching objects in the patient’s surroundings, and after removing gloves. Additionally, hand hygiene should be performed before and after preparing food, before eating, after using the washroom, after blowing your nose, and after touching animals or animal waste.
paper towel for maximum effectiveness and removal of germs.
In a case study conducted by Harvard Medical School in 2018, the following evidence was presented: what is a person to do to avoid picking up bacteria in a washroom? You should always dry your hands, as not drying them after washing helps bacteria to survive on the skin. Paper towels are the most hygienic way to dry your hands. For this reason, use of paper towels is already routine in health care settings.
There are two main methods of hand hygiene: handwashing with soap and water and hand-sanitising with an alcohol-based hand rub. Both methods are effective, but handwashing is generally preferred when hands are visibly dirty or contaminated with bodily fluids.
When washing hands with soap and water, it is important to wet your hands with running water and apply soap. Rub your hands together vigorously for at least 20 seconds, making sure to clean all surfaces, including the backs of your hands, between your fingers, and under your nails. Rinse your hands thoroughly with running water and dry them with a
When using an alcohol-based hand rub, apply enough product to cover all surfaces of your hands and rub your hands together until they are dry. It is important to use the recommended amount of product, as using too little can be ineffective and using too much can be wasteful.
In addition to practicing proper hand hygiene, it is also important to avoid touching your face, particularly your eyes, nose, and mouth. This can help prevent the spread of germs that may be on your hands.
Overall, hand hygiene is a simple but effective way to prevent the spread of infections and diseases.
By practicing proper hand hygiene in our daily lives, we can help protect ourselves and those around us from illness.
It is, therefore, our plight, as the doctors of our industry, to both educate and propagate the importance of protecting our families, colleagues, patients and clients by following the basic and simple formula of proper hand hygiene.
It all starts with you!
“Overall, hand hygiene is a simple but effective way to prevent the spread of infections and diseases. By practicing proper hand hygiene in our daily lives, we can help protect ourselves and those around us from illness.”
The winter season is fast approaching and this means one thing, an increase in colds and flu and a rise of absenteeism in the workplace. This leads to a decrease in production which means a loss in revenue for your business. There are generally over 30 common surfaces in the office that employees repeatedly touch throughout their workday, like the kettle, printers, cupboards, handles, office stationery and shared washroom facilities. Studies showed that a person will generally touch their face 23 times an hour. Couple this with the amount of common surfaces that you share with your co-workers and this increases the risk of contamination. When one staff member is sick, the chances of you or other co-workers getting sick increases exponentially. The moment one person gets sick, 70 percent of common surface areas are contaminated in one day, and this increases your chances of getting sick by 90 percent. The cost of absenteeism to the South African economy through colds and flu each year ranges between R1,7 and R2,25 billion and the average cost to a company for an absent employee is around R500 per day. The average cost of a hand sanitiser used 4–5 times per day is less than R0.12c per person per day. A small investment to make against a far larger threat.
You can contribute to reducing absenteeism in the workplace this winter by using personal and communal hand-sanitisers, and assist in promoting good hand hygiene practices, through handwashing with antibacterial hand soap and using paper products instead of air dryers.
Studies have illustrated that hot air dryers merely spread bacteria around, whereas paper towels dry efficiently, remove bacteria and cause less cross-contamination in the workspace environment. BetasanTM offers a range of paper towels and paper dispensing systems to keep shared washrooms bacteria free.
By placing a betasanTM sensor hand-sanitiser stand at the entrance of every facility, you will help to stop the spread of bacteria that causes colds and flu in its tracks. Having the correct washroom dispenser range such as a betasanTM hand soap dispenser with betasanTM antibacterial soap, a betasanTM compact paper towel dispenser instead of a hot air dryer, and lastly, issuing each member of staff with a betasanTM personal handsanitiser and lanyard will safeguard your employees this winter against all forms of virus’ and bacteria. Additionally, betasanTM encourages all businesses to educate their employees on the best handwashing practices as well as to regularly sanitise both their hands and their workspace. The betasanTM range of products offers a complete solution to protect you and your staff, therefore, reducing the loss in revenue by eliminating the threat of absenteeism in the workplace this winter.
For more information about hand hygiene solutions visit: www.betasan.co.za
According to the World Health Organization (WHO), this year’s World Hand Hygiene Day focuses on the theme ‘Seconds SAVE LIVES, Clean Your Hands!’ This important topic highlights the life-saving importance of clean hands and aims to improve hygiene standards globally. To contribute to this work and support hand hygiene compliance among healthcare professionals, Tork, an Essity brand, made the award-winning Tork VR Clean Hands Training available on any device. This means that healthcare professionals can train hand hygiene routines anywhere, at any time. A study shows that eight out of ten healthcare professionals would like to improve their hand hygiene compliance.* But traditional forms of hand hygiene training are often perceived as uninspiring. Tork VR Clean Hands Training invites users into a digital world where they can interact with, and train on, the WHO’s ‘5 Moments of Hand Hygiene’ in a realistic environment. “Hand hygiene has always been important within healthcare, and the recent pandemic has made it only more so. Healthcare professionals are doing tremendous work to secure hand hygiene compliance to protect their patients and themselves, but, at the same time, they are looking for ways to improve. By making the Tork [VR] Clean Hands Training available on desktop and other platforms, we can make hand hygiene happen by empowering healthcare professionals to train when and where they want”, says Tom Bergin, Marketing Director – Healthcare, Essity Professional Hygiene. Tork VR Clean Hands Training, which was a category winner at last year’s Interclean Amsterdam Innovation Awards, has been developed in collaboration with behavioural scientists, world-leading experts in hand hygiene from the Infection Control Programme at the University of Geneva, hospitals, Faculty of Medicine Geneva, Switzerland, and university hospitals around the world to make it intuitive and efficient as a learning tool.
continues on page 13 >>
CropLife South Africa has warned that the very wet and humid weather conditions over the summer months have brought about an outbreak of German cockroaches in South Africa. It also added that cockroach numbers had increased recently, not only because of the weather, but also due to the unhygienic conditions that prevail in the country.
CropLife South Africa, a nonprofit industry association for manufacturers and suppliers of pesticides, believed the surge in cockroach infestations had triggered large-scale unlawful use of pesticides not registered for indoor use.
The association said, “cockroaches are primarily active at night, but the current outbreak is of such magnitude that the insects are running around during the day in most homesteads. Homeowners, the fast-food sector, retail sector and hospitality industry should act quickly to stop the tide of cockroaches in South Africa.”
They urged all citizens to abide by the statutes of the country and only use registered pesticides, strictly according to their label instructions to avoid health impacts on themselves, their families or their clients.
Elriza Theron, spokesperson for CropLife, said, “do not buy unlabelled
pesticides in small containers from social media advertisers or street vendors, as those products are likely to pose a severe hazard and risk to people when applied indoors.”
Theron said cockroach control started with a serious effort to sanitise human habitation of refuse and left-over foodstuffs, “a dirty kitchen that is littered with left-over food and freely available pet food needs serious intervention to deny these unsavoury critters from invading a home and setting up a colony.”
Operations and stewardship manager, Gerhard Verdoorn, explained that they became aware of the outbreak after a rapid increase in enquiries received by the Griffon Poison Information Centre (082 446 8946) from members of the public about cockroach control.
“CropLife SA also uncovered a network of syndicates that acquire,
decant and sell highly toxic pesticides that are not registered for indoor use at all via social media to the public. We are working with the Inspectorate of Act No 36 of 1947 to put an end to these malpractices,” Verdoorn said.
The Department of Agriculture, Land Reform and Rural Development (DALRRD), however, said it has not been made aware of an outbreak or increases in sightings of German cockroaches, and that the relevant government department would be the Department of Health or municipalities to respond to this issue.
Department spokesperson, Reggie Ngcobo, said, “CropLife South Africa partners with the department on a number of pesticide regulations, including monitoring. To date, we have not observed or been made aware of the illegal importation and use of pesticides to control cockroaches.”
The addition of a desktop version makes finding time for and being involved in performing hand hygiene training much easier. As part of making the innovative hand hygiene training more accessible for healthcare professionals, the training will be available in seven languages including English, German, Polish, Dutch, French, Spanish and Arabic.
We are proud to make our hand hygiene training more accessible for healthcare professionals. Hand hygiene is an important subject and improvements have the potential to save lives. Tork supplies high-quality sanitiser systems suitable for use in a demanding hygiene environment.
Tork sanitiser dispensers are compatible with care routines, are fast and easy to refill. The flexible assortment suits your needs”, added Bergin.
To learn more about our sanitiser assortment, or to access Tork VR Clean Hands Training, visit tork.co.za/cleanhands or email us at: tork.rsa@essity.com
*Source: Survey among 1017 healthcare professionals in five markets: United States, United Kingdom, Sweden, Germany and Poland. The survey was conducted between 23 November to 7 December 2018 by United Minds on behalf of Tork and in collaboration with the panel provider CINT.
There is clear evidence that hand hygiene habits have changed since the COVID-19 pandemic: washing of hands more frequently throughout the day and using paper towels is the most hygienic way to dry hands when out and about.
Now, a new mask study provides scientific data to support these preferences. It seems that, as is so often the case, the consumer knows best.
The research found that contamination of hand dryer users by splattering was ten times higher when using jet air dryers than when using paper towels, and contamination of other washroom users was also significantly greater.
The findings have major implications for hygiene in public washrooms. Hand drying is an essential step in ensuring optimal hand hygiene, helping to remove microbes remaining on hands following poor handwashing and so reducing the spread of infection in the community.
The study was carried out by a team at the Leeds Institute of Medical Research, University of Leeds, UK and the Department of Microbiology, Leeds Teaching Hospitals NHS Trust, UK. Participants dried their hands using
either a jet air dryer or paper towels and wore face masks as a way of measuring the risk of inhaling viruses.
• When using jet air dryers, 89 percent of masks were contaminated by viruses, compared with 29 percent of masks when using paper towels.
• Facemask contamination with virus aerosols was higher in the first five minutes following hand drying for both methods. Virus load was significantly higher with jet air dryer use.
• In trials using jet air dryers, facemask contamination increased at 15 minutes post-hand drying, suggesting aerosolisation of small particles that remain airborne for longer.
The study demonstrates that the method of hand drying has the potential to impact airborne dissemination of microbial pathogens – including respiratory viruses – so potentially increasing risk of exposure and infection for other washroom users. Armed with this new research, restaurant
and bar owners, and procurement managers responsible for facilities in large sporting and shopping complexes, would be wise to review the hand drying equipment they offer and be sure to provide customers with the most hygienic option – paper towels.
More details about the results of the study, can be found here.
A bacteriophage (a type of virus) was added to volunteers’ hands before they dried them in order to investigate whether microbes on poorly washed hands can spread across the washroom. The contamination of masks by splattering and droplet deposition was investigated for up to 15 minutes afterwards. Contamination of the facemask of the person drying their hands and on the mask of another individual in the washroom at one metre and two metre distances, was measured. Volunteers waited for 15 minutes post-hand drying to examine whether air droplets continued to settle on fresh masks that were changed every five minutes.
in the primary African trade magazine for the commercial cleaning and hygiene sectors. Reach your target market cost-effectively with a direct link to end-users, building service contractors, facility management and key institutional segments.
During May, African Cleaning Review Editor, Johann van Vuuren, visited the ISSA PULIRE 2023 show for cleaning professionals as part of an international delegation, facilitated by the Italian Trade Agency. The show hosted exhibitors from 21 countries, 104 of which were new participants.
Regarded as a significant hygiene and cleaning event on the European calendar, ISSA PULIRE, also known as The Smart Show, took place in Milan, Italy from 9-11 May this year, welcoming producers, distributors, service and FM companies as well as end users. A total of 373 exhibitors including foreign and Italian brands filled two exhibition halls at Fiera Milano. With the aim of broadening the international scope of the exhibition, the 26th edition of the show took place in the city of Milan, which heralded an exciting new chapter for ISSA PULIRE that co-located with three other trade shows to add value.
To compliment this year’s show, the organisers added a comprehensive conference programme over the three days which included amongst others, topics, such as, healthcare environment hygiene; health and safety; “cleaner” – finally a recognised profession; and the future of sustainability in cleaning.
The organisers reported that over 20 000 visitors from 107 countries visited the three-day show which included international delegations from Egypt, Ghana, Kenya, Morocco, South Africa and the USA. All in all, the show, with all its activities and innovations, was well worth a visit having rebounded spectacularly from the arduous COVID-19 years. The next ISSA PULIRE show is scheduled for 2025.
A first for the show was the introduction of a hackathon – a competition in which teams of university students are called upon to solve problems assigned to them in real time focusing on a Smart Facility Theme: Cleaning Connected to the Future. The cleaning sector, like many other industry sectors has seen rapid transformation and digitisation to assist service providers to improve health and safety conditions in facilities. While competing, the teams demonstrated how cleaners, trained and equipped with digital tools, can contribute to achieving Environmental/Social/Governance (ESG) objectives with measurable results.
The visit allowed for an opportunity to visit leading Italian cleaning equipment manufacturer COMAC’s production facility located in Verona together with South African distributor Kyle de Rose. The factory tour offered a first-hand experience of how scrubbers and sweepers and other mechanical cleaning equipment are assembled. The company prides itself on the ability to design and manufacture products that aim to reduce the environmental impact of its cleaning operations.
A new area dedicated to pest control products and services added additional capacity to the exhibition by creating a common meeting place for operators in this sector.
The ISSA PULIRE Product of the Year Award finalist competition was hotly contested and eventually cumulated in a draw which saw a winning tie:
• The XIBU 2WIPE hybrid automatic wet wipe dispenser by Hagleitner. The world’s first automatic wet wipe dispenser features the ability to dispense touch free surface sanitising wipes, cloth after cloth whilst protecting the contents. The never empty feature allows it to work with two wipe packs. When one runs out, the dispenser automatically switches over to the next, keeping wipes moist, from the first to the last wipe.
• The joint winner was the cordless robot floor cleaner by Makita, equipped with a camera and 3600 laser radar capability which can map up to five areas and up to 10,000 square meters.
Hard floor cleaning solutions are not only isolated to a singular task but more to a system that must be implemented to keep floors in the best possible cosmetic condition and improve the hygiene levels in the facility no matter what market sector we’re addressing. Before designing a system to maintain the floors, we need to consider the amount of foot traffic, understand the nature of the soiling, location of the building and what elements the facility is exposed to, says Prime Cleaning Suppliers’, Neil Labuschagne.
Most of the soiling in any facility is tracked in from the outside, yet people neglect to implement proper entrance mattingsolutions which should include a scraper fall through mat on the exterior to remove course dirt and dust control mats on the interior for finer particles and where applicable be able to deal with moisture.
The starting point for any hard floor cleaning system should be dry dirt and dust collection or binding. By removing the dry soiling first, you aid in simplifying the damp and wet cleaning processes. The most effective means of dust binding is by using an impregnated cloth that fits on a dust binding tool. Although, for larger areas the traditional swivel flat mop sweepers will be a more cost-effective solution.
The wet cleaning process should, without a doubt, be done with an auto scrubber. There is no better way to remove soiling effectively and efficiently. The size of the auto scrubber will be determined by the square meterage to be cleaned, cleaning frequency and time in which the task needs to be completed. A crucial step
in the hard floor cleaning process is the identification of what type of floor you are dealing with. The characteristics of the floor will determine which chemical to use in conjunction with the appropriate consumable that will yield the best results with the least effort.
Mopping systems are not effective as a primary wet cleaning solution. Most of the time they become ineffective within the first couple of square meters and just re-arrange the dirt. They should only be used for spillages and spot cleaning that occur post auto-scrubbing. Mopping systems should be microfiber flat mopping systems rather than fan or traditional spaghetti mops. Microfiber flat mopping systems make contact with a larger surface area of the floor consistently and the characteristics of the fibres is such that it traps and holds the dirt. However, it should be rinsed regularly to stop it from becoming partially effective.
The reason for becoming partially effective is that microfiber needs to be rinsed at temperatures of 40 °C and higher to open the fibres to maximise the release of dirt.
Beyond understanding that cleaning hard floor surfaces require a systematic approach, we need to apply the correct chemical, dilution ratio, consumable and mechanical action in the process. Different floor types are prone to damage if the wrong chemical or cleaning action is used which could result in a costly and unpleasant exercise if the client insists on floor replacement. Some flooring types require treatment using polymer, acrylic or penetrating sealers, others simply need natural enhancement and others respond well to neutral, alkaline or acidic treatments. One of the most common and problematic floors we are most often exposed to are variations of porcelain tiles which require a really disciplined maintenance cleaning programme and implementation of a periodic intensive cleaning schedule to optimise the appearance of the tiles.
Cleaning hard floor surfaces is, in fact, a specialised function performed by our industry with a no one size fits all solution. However, Prime Cleaning Suppliers aim to guide operatives irrespective of their experience to address this function with precision.
Diversey Europe, a leading provider of hygiene, infection-prevention, and cleaning solutions recently published a study to demonstrate the importance of floor disinfection in reducing risks associated with floor hygiene. The authors of the study suggest that commercial facilities wanting the best hygiene outcomes and using manual floor mopping as part of their facility hygiene programme should consider the use of biocidal floor products with either launderable or disposable flat mops and avoid the use of cotton string mops and neutral cleaners.
Built on Diversey’s prior research into floor hygiene to study the differences in hygiene outcomes associated with the choice of mopping materials when manually cleaning, sanitising or disinfecting a floor, the peer reviewed study published in the Infection Control Tips journal investigated the removal of Staphylococcus aureus from a floor when inoculated, and how the selection of floor cleaner or disinfectant and the choice of floor mop impacted the hygiene outcome, which resulted in statistically significant differences. The study further found that mopping with a neutral cleaner was inferior to using a biocidal product and using a traditional string mop was inferior to using launderable or disposable flat mops.
The authors of the study found that
the use of launderable and disposable flat mops significantly reduced the level of bacteria that were cross-contaminated when compared to the cotton string mop, regardless of product used, demonstrating that mopping substrate may also play some role in the level of cross-contamination that can occur through manual floor mopping.
Floors are the largest surface routinely cleaned in commercial facilities and are typically contaminated with higher levels of bacteria than surfaces that receive routine hand contact. Studies in healthcare have shown the potential for bacteria on the floor to migrate to surfaces where hand contact frequently occurs, suggesting floor hygiene may play a role in infection risk. When cleaning/disinfecting the floor in a
commercial facility, the facility staff may choose between using a floor cleaning machine or manual mopping methods. When manually mopping a floor, the facility staff may choose between traditional cotton string mops or flat mops with either launderable or disposable pads. Additionally, the facility would select either a cleaner or a cleaner/ disinfectant to use with the floor mop.
Prior to this research, little was known about the difference in hygiene outcomes associated with the range of choices available for floor hygiene. All Diversey funded research is geared towards providing leading hygiene, infectionprevention, and cleaning solutions.
For more information on the research visit: www.infectioncontrol.tips journal
Outdated battery technology often leads to restrictive cleaning. The 3045NX is part of the NX300 Pro Cordless Network, with a 1-hour fast charge and up to 70 minutes runtime, providing consistent cleaning performance.
Compact machine, big results
Most compact in its class, the 3045NX has a 450 mm scrub width, ensuring a compact design for maximum accessibility, with a working area of 1,215 m²/hr.
Extended long-life power
Made for the long haul, the NX300 battery won’t let you down, engineered and tested for commercial use delivering up to 2,500 charge cycles. A 3-year battery warranty provides complete peace of mind for you and your Pro Cordless Network.
Constant cleaning with battery hot-swapping
Being part of the NX300 Pro Cordless Network provides the opportunity of continuous cleaning through hot-swapping batteries between other machines in the NX300 Network.
Unlock cleaning potential by utilising the NX300 battery technology’s 1-hour fast charge. Providing on demand cleaning for any user. Clean and charge when you need to, increasing productivity and flexibility.
The NX300 Pro Cordless Network brings the convenience and performance of professional cordless cleaning across our growing battery range.
Support at your fingertips, straight from your mobile Access a wide-range of multilingual help and support, including troubleshooting and maintenance videos, through the Nu-Assist App. Want
As a customer, guest or patient of a facility, the state of the floor can be one of the most telling things about the business you’re entering. Not just because of the special glisten that a clean floor can have (that’s great, too), but because it’s a sign of so much more: a cleaning team using quality cleaning equipment consistently, appropriately, and effectively. And if the floor is clean, it’s likely that the other surfaces within the building are too.
To have a clean floor free of debris, dust and other detritus, you need reliable cleaning tools. And while these tools don’t fit in a neat little toolbox, they are extremely important for making a positive first impression in your facility, according to Tennant Company, a leading cleaning equipment manufacturer.
Nobody wants to carry around the variety of cleaning supplies needed to truly clean a space, which is why a cart with wheels that can hold all your cleaning solutions, rags, PPE, and cleaning tools will ensure you have all of the necessary items in one place at all times.
No toolkit would be complete without these basics. The broom is such a common floor cleaning tool that there’s not even a single inventor you can credit for it. All these years later, a dry mess on a hard floor still does not stand a chance against a broom. Dust mops (also known as dry mops) and wet mops also serve vital roles in floor cleaning to help with pre-sweeping areas, gathering up dust and debris, or getting wet stains cleaned up in a jiffy. And don’t forget the dustpan!
Where hard-floor tools like brooms and mops lose their effectiveness, vacuums and carpet extractors come in. Residential, commercial and industrial vacuums agitate carpet to loosen any dirt and then promptly suck it up. Today’s vacuums come in all varieties –ones you strap to your back, ones you ride, or ones that look like the vacuum you have at home, but clean like they’ve
consumed too many energy drinks. There is a vacuum out there for every type of facility.
And for the times when you need a little more power behind your carpet cleaning, extractors are up for the task of cleaning and drying carpet with minimal downtime. From handheld, portable spot extractors to ride-on dual technology extractors that perform interim and deep cleaning, if your facility has carpet, one of these powerful machines should be part of your cleaning toolkit.
Sometimes a vacuum can’t cut it. As you might guess, floor sweepers use brushes and a vacuum system to pick up and remove dry debris from hard or soft floor surfaces. Exactly how they do that depends on your needs, whether you’re cleaning compact or large floor areas, if you want to walk behind the sweeper or ride on it, and more. The many options make this another great option to have in your toolkit.
Floor scrubbers are the bread and
butter of many cleaning programmes and are irreplaceable when you have hard floors that require frequent, thorough and hygienic cleaning. They use water to deep-clean hard floor surfaces and have a wide range of features and optional technologies depending on your specific needs.
Finally, for large facilities with lots of ground to cover, sweeper-scrubbers combine scrubbing with a vacuum system for a quick-drying deep-clean. These powerful machines can often offer one-pass cleaning that leaves floors sparkling without using excess staff time to get there.
These are just some of the items to include in your facility cleaning toolkit. Not every facility needs all of these, and some facilities may need even more specialty cleaning tools to get the job done. Some of the tried-and-true tools that have served cleaning crews well for decades or longer, or those that utilise newer floor cleaning technology that only continues to improve. The more of these options that you have in your toolkit, the better you’ll be able to clean floors of any kind.
Whether in retail or the hospitality industry, in small workshops or public facilities – wherever floor surfaces are heavily used – daily cleaning is a must. Designed for surface areas up to 2,500 m2, the Scrubmaster B25 delivers exceptional performance and ease of use in a compact form.
Equipped with a disc-brush-unit cleaning system for brushes and pads, the Scrubmaster B25 thoroughly cleans different types of floors and various degrees of soiling in a very short time. High-level specifications include a working width of 43 cm, a 25 l tank, and cleaning performance of up to 1,700 m²/h.
Innovations include Hako’s energysaving, noise-reducing Eco mode for low levels of soiling, and Hako-AquaControl, which saves up to 50 percent of water usage during operation.
Hako is taking the cleaning of smaller surfaces to a new level with the Scrubmaster B25 walk-behind scrubberdryer, giving customers access to German-engineered quality and cleaning performance in a smaller machine – at a highly competitive price.
An adjustable handlebar makes it easy to move away from walls and allows for cleaning underneath furniture such as tables. The handlebar is also foldable to facilitate transport. User-friendly features include a clearly arranged control panel with intuitive operating elements; the individually adjustable handlebar to ensure back-friendly working; and easy access to all components to simplify daily maintenance.
These specifications and features, combined with a budget-friendly price tag, makes the Hako Scrubmaster B25 the supreme value-for-money investment in cleaning excellence.
For more information, please contact Wouter Niemann at BHBW on 065 650 3839 or email WNiemann@bhbw.co.za.
The International Facility Management Association (IFMA) has released a new report, Experts’ Assessment, Vol. 2: Future Working Environments and Support Functions Toward 2030. The association’s report provides an analysis of what the facility management industry has learned since the IFMA’s inaugural Experts’ Assessment study was conducted in 2020.
The association surveyed more than 200 subject matter experts from around the world on their perspectives on five main themes:
• Facilities in demand toward 2030
• Technology, work, and workforce development
• Workplace management and strategy
• Environmental, social, and corporate governance (ESG)
• Facility management (FM) in 2030. The report re-visits the challenges, projected effects and recommended actions outlined two years ago, examining choices made and lessons learned, and identifying the implications for future work environments and support functions.
“The subject matter experts who contributed to this study are industry leaders whose foresight and well-considered actions have
sustained their organisations through unprecedented change,” said IFMA President and CEO, Don Gilpin.
“Understanding the decisions they’ve made to adapt and prepare their organisations for the future will help any FM gain clarity in forming their own strategies, as well as a solid base from which to gain buy-in on projects and policies that will mean the difference between sink or swim.”
Laurie A. Gilmer, PE, CFM, FMP, SFP, LEED AP, and chair of IFMA’s Global Board of Directors, said the new report identifies the most crucial focus areas for resilience, both for FM professionals and their organisations.
“It shows that facility managers face several new realities requiring new mindsets, business models and technologies. With remote and hybrid work becoming the norm and organisations still struggling to
entice workers back to the office, it is increasingly important for FMs to create more experiential spaces,” said Gilmer.
“FMs are no strangers to change. We are attentive to varying conditions in our facilities and the business world. We plan for possible scenarios so that we are ready to pivot for the safety and productivity of our people and the endurance of our organisations. To be fully prepared, we must be fully informed. The Experts’ Assessment is a shining example of how our industry has remained forearmed and flexible, supported by IFMA’s initiative in identifying emerging trends, preparing FMs for the impact of change and guiding us through challenges with critical information and insights.”
For more information visit: www.ifma.org
Self-sustaining laundry services for underprivileged nursery schools could soon be the norm.
KT Wash, a detergent manufacturing company located in Nigel, east of Johannesburg, has recently explored a pilot project that could see a breakthrough in laundry and washing powder market dynamics, targeted at over 26,000 nursery schools across the country.
The company has launched its revolutionary SmartFill machine that changes the laundry experience for customers by making laundry detergent affordable. This machine is an eco-friendly, sustainable, and cost-effective solution that allows customers to refill their laundry detergent containers at a fraction of the cost of purchasing new bottles.
Through research and insight, it was established that most nursery schools handwash items used by children which takes up a lot cleaning time. Through this, the company saw an opportunity to present a laundry solution that is both viable and affordable, and that fits into the daily routine of schools.
The idea is to empower nursery schools through offering self-sustaining laundrette services. KT Wash has, since the inception of its pilot project, donated washing machines and laundry detergent supplies to three nursery schools in Alexandra, Gauteng. A SmartFill dispenser was also provided to manage the distribution of packaging free hand- and/or machine washing powder, as well as shelving and storage to help manage the laundrette service.
“It’s exciting to see a project that has the potential to not only uplift a community but to change the dynamics of a market. Once this project takes off,
it would be the beginning of a much bigger programme to provide laundrette services through more creches,” says Marc Wetselaar, COO of SmartFill.
Nursery schools can use the provided washing machines and detergents for their own needs and sell the laundry offerings to the community from R2 per load. The laundry powder stock levels are managed via SmartFill’s cloud services and trigger replenishment when stock levels are low.
KT Wash CEO, Ayman Abdelmeguid added, “not only is this ground-
breaking but also transformative. This could change the way laundry is done in township nurseries which are underfunded and overlooked by the community.”
Additionally, the SmartFill Machine is environmentally friendly as it reduces packaging waste when customers refill their detergent containers. By using this machine, customers are taking a crucial step towards a more sustainable future.
For more information, visit: www.ktwash.co.za
It was originally said that cleaning and maintenance of photovoltaic systems was not necessary. However, it has become apparent that weather and air pollution do leave their mark. The energy crisis in South Africa has seen proliferating numbers of solar panel installations in order to keep the lights on and maintain productivity in facilities. In order to use solar power as efficiently as possible and to keep the electricity yield at the highest possible level, regular professional cleaning with the correct equipment is necessary, according to Kärcher, a global leader in cleaning technology.
All types of photovoltaic systems should capture sunlight for as many hours as possible and withstand external influences. These include rain, storms, and hail, and, depending on the location, soot, pollen, dust from road traffic, leaves, needles or bird droppings.
Why should solar panels be cleaned?
Clean the panels regularly, not only because of their appearance. Contamination can reduce the electricity yield by up to 30 percent. Thorough, professional cleaning is necessary, and this does not only apply to the surfaces of the solar collectors. Deposits build up at the junctions between the glass and the frame, which over time can lead to the formation of moss and lichen over a wide area.
Proper cleaning of the solar panels requires the correct cleaning technique due to heavy soiling. The modules are often mounted on roofs at a steep angle of 45°, so take measures to ensure operator safety.
When should you clean photovoltaic panels?
Solar systems should be cleaned using the right technology and, depending on the location, using professional service providers.
Panels that are exposed to less pollution from the environment can be cleaned once a year or every two to three years. In this case, green electricity can be generated even more sustainably – a topic that will become increasingly important in the future.
A professional high-pressure cleaner in combination with a brush attachment or a roller brush and a telescopic lance are among the best ways to clean solar panels efficiently and ergonomically. With the correct cleaning technique, it is possible to clean a solar panel area of up to 1,500 m2 per day.
Brush attachment
Kärcher recommend an attachment with two disc brushes that reach a working width of 800 mm. The effort required is reduced because the system neutralises the drifting movement with the help of the counter-rotating movements of the two brushes.
In addition, the large working width ensures a high area output, which reduces the amount of work required for solar cleaning. The disc brushes have ball bearings and are driven by the water from the high-pressure cleaner. Low-pressure operation with cold water and a delivery rate of 700 to 1,000 l/hr is sufficient.
A nylon bristle ensures scratchfree cleaning to protect the sensitive surfaces of the solar panels during cleaning. Models with harder bristles on the outside of the plates also ensure very good cleaning results on the module frames.
It should be possible to control the amount of water comfortably via a lever on the lance while the brushes are guided in paths over the solar modules. Turning the water up a little at the beginning creates a sliding layer that makes it easier to move the brushes on the surface. A self-adjusting, articulated joint to which the brush head is attached can help compensate for different working angles.
Choose the length of the telescopic lance to match the size of the system or use an infinitely extendable lance. Longer lances made of carbon or carbon composite are lighter and, therefore, more comfortable to handle.
If you value more flexibility and have to clean large façades in addition to photovoltaic systems, you are better off with a variable lance system. Pole systems that are suitable for vertical and horizontal surfaces are available and can be combined with different attachments. Use a high-pressure
nozzle for spot cleaning, an attachment with disc brushes for working on horizontal PV elements or a rotating high-pressure roller brush, which is also suitable for vertical façades.
The advantage of roller brushes is that they are driven by high pressure and work their way up independently –meaning you need to be holding them with significantly less force. The roller brushes can work with water flow rates from 350 l/hr. Brushes with soft or hard bristles are available for different surfaces. It is recommended to use soft brushes for cleaning photovoltaic systems.
Use cleaning agents and a water softening system for the best results When using cleaning agents, these should be suitable for removing stubborn, greasy soiling and mineral
residues. If the water film breaks down quickly, streak-free drying without limescale stains is possible. Soaking time and rinsing, therefore, shouldn’t be needed, facilitating the cleaning process. In order to clean the photovoltaics sustainably, Kärcher recommend a cleaning agent that prevents further soiling.
If the water hardness range is greater than medium, Kärcher recommend a water softening system. This prevents staining despite the high lime and mineral content of the tap water. The water softener contains a resin filter with an ion exchanger that retains limescale and minerals.
The position of a system determines from where and with which tools the solar panels can best be cleaned in a way that ensures the safety of the employees. On roofs that are difficult to access, use a cherry picker. If the roof is easily accessible, work from the roof ridge or with the help of fall protection attached to the roof. The prerequisite for this is that the necessary safety hooks are located on the roof ridge. The fall protection consists of a harness around the pelvis and shoulders that is connected to a core rope. In an emergency, the harness immediately hooks on and safely catches the user. Some safety systems also include a strap fall absorber to reduce the impact in the event of a fall.
Dry Ice Blasting can be compared to sand blasting, bead blasting or soda blasting, where 3 mm dry ice pellets are accelerated in a pressurised air stream to impact the surface to be cleaned. Once in contact with the surface, the dry ice evaporates. This process is called sublimation and is a unique characteristic of dry ice, which makes it ideal for cleaning a variety of industrial equipment, especially in food processing facilities where it renders a quick and easy clean of different surfaces to get these back into production straightaway.
Traditional cleaning methods are time-consuming, labour-intensive and costly. Manual scraping or scrubbing with wire brushes and water or chemicals can take up to several hours, can cause damage to equipment thereby shortening asset lifetime, and results in extended downtime. Dry ice blasting does not create secondary waste or chemical residues, is non-abrasive, non-conductive, non-flammable, and non-toxic. It reduces
temperature of -78.5 °C. Dry ice blasting utilises ice pellets, which are accelerated in a pressurised air stream and subsequently directed at the surface to be cleaned. The dry ice freezes the dirt on impact, then rapidly sublimates while the CO2 gas removes the frozen dirt without causing damage or abrasion to the surface. Because of the temperature difference between the dry ice particles
The dry ice pellets are accelerated by up to 300 m/s with compressed air and then blasted onto the surface to be cleaned. The second part of the cleaning process is the impact of the kinetic energy.
Dry ice cleaning is applicable to many industries including mining, electrical, food processing, pharmaceutical, and automotive.