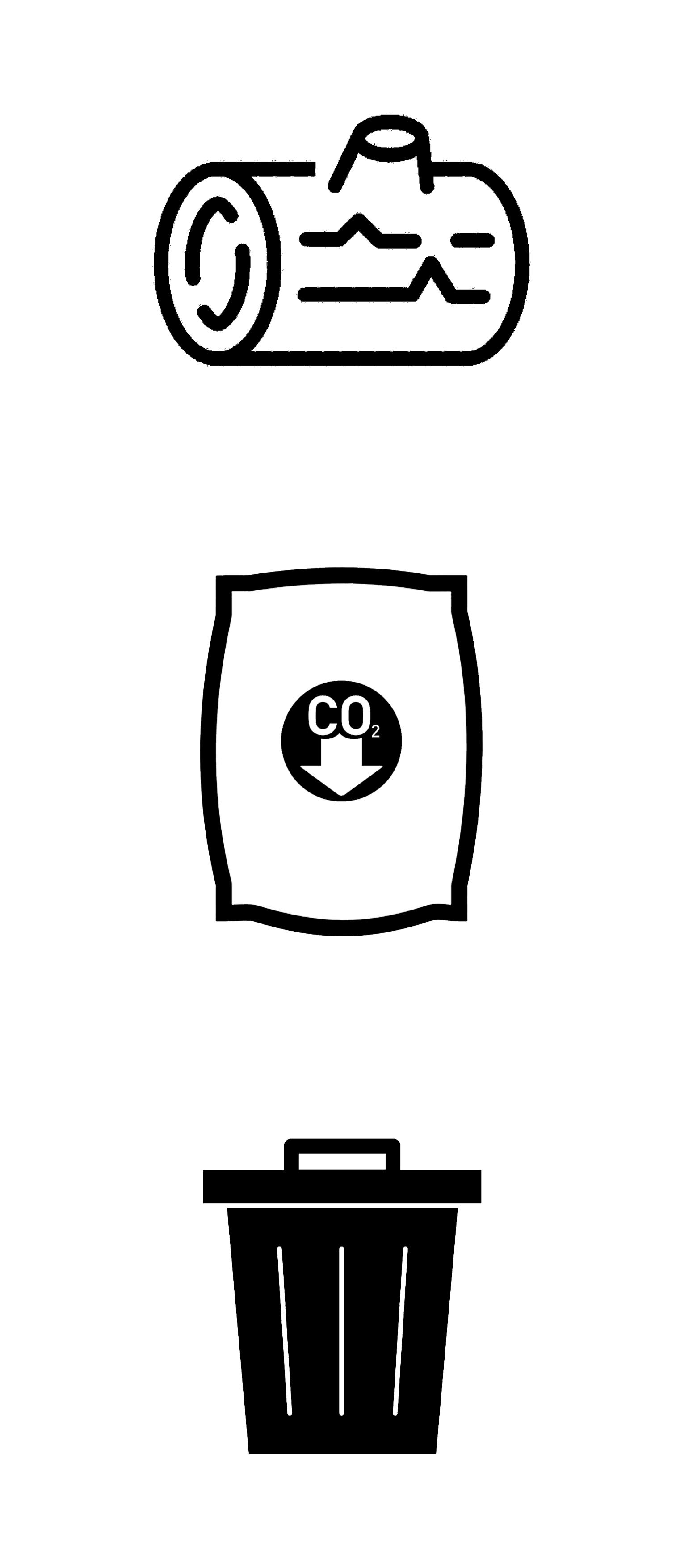
2 minute read
CARBON ANALYSIS REDUCING AND OFFSETTING CARBON EMISSIONS
There are various ways to offset and reduce the carbon emissions produced by a building. One is to focus on reducing the operational carbon such as using renewable technology within the domestic household or in creating the building. Another is to use low carbon and sustainably sourced materials. The main way of reducing carbon emissions is by repurposing or reusing existing buildings and materials.
For this project, the main way of reducing carbon emissions is the use of structurally insulated panels (SIPs). SIPs main benefits are their airtightness and insulation, with the main aspect of reducing carbon through reducing the energy consumption for heating and cooling.
Advertisement
Timber has a lower embodied energy than all other mainstream construction materials. Curing, cutting and sourcing timber and using it in construction requires only basic tools and very little energy compared to materials such as brick, metal or plastic which must be heated to extract the raw materials therefore by mainly using timber-based materials like SIPs and OSB will reduce the carbon emissions.
Another way to reduce carbon emissions is by using low-carbon concrete mixes. In this case, the foundation calculations specified 3 different concretes, one standard cement with no mix, concrete with fly ash mix and concrete with blast-furnace slag mix. By using the concrete with either fly ash or blast-furnace slag, it reduces the embodied carbon for the foundation drastically.
SIPs can drastically reduce the waste generated during construction by using advanced optimization software and automated fabrication technology to ensure the most efficient use of material. From the OSB production process to the use of the insulation, all materials used for the SIP are recycled or can be recycled. Offsite manufacturing results in less waste on-site, reduced build time and better quality.
Carbon Analysis Foundation Embodied Carbon
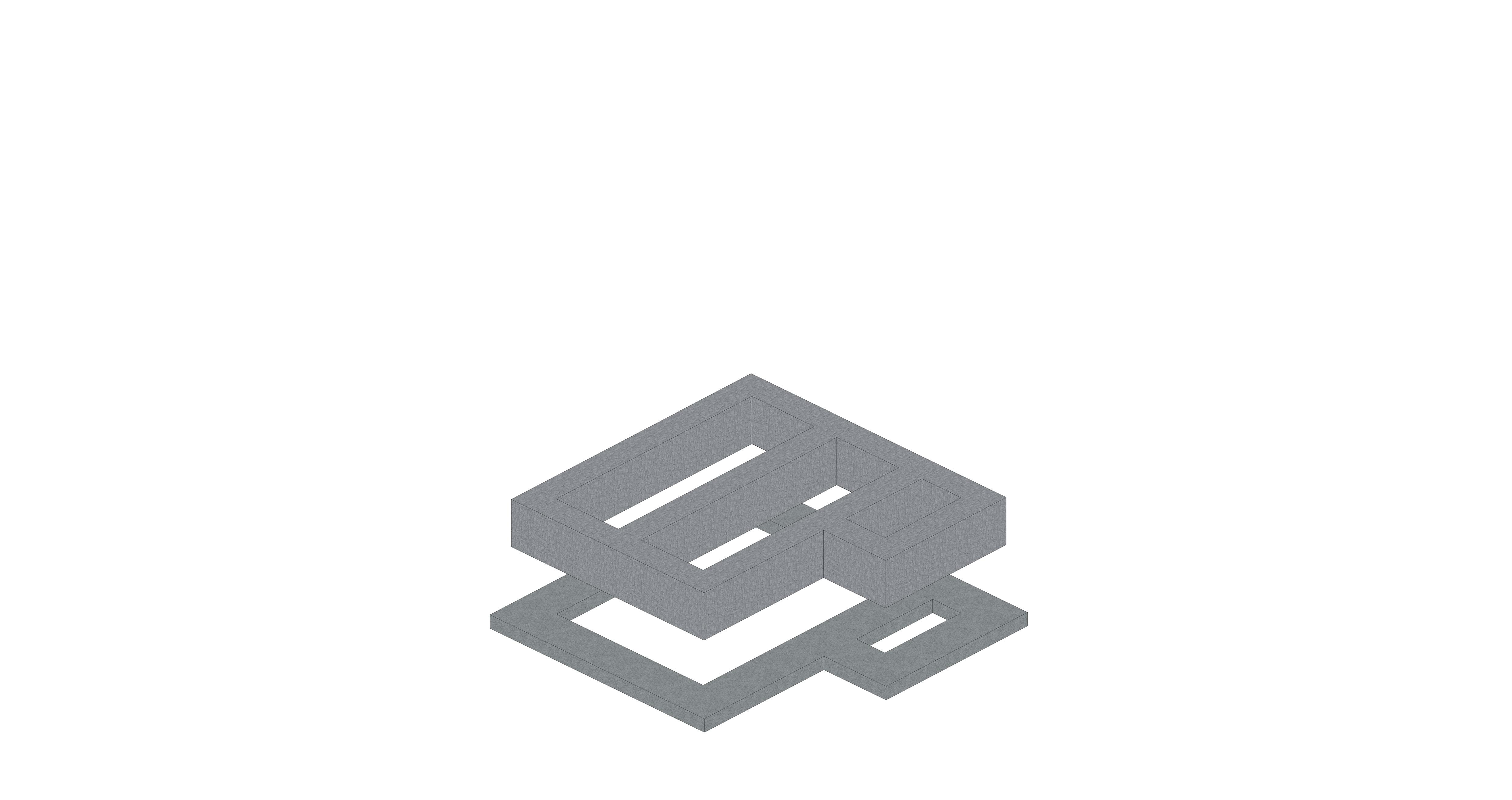
The foundation uses 20/25 MPa concrete for the foundation walls and 25/30 MPa concrete for the foundation footing which brings the carbon emissions to 2228.35 Kg of CO2. To reduce the embodied carbon (EC) of the foundation, it can use concrete that has either a percentage of blast-furnace slag or fly ash mixed into the concrete.
By using Concrete mixed with 70% blast-furnace slag, it reduces the material emissions from 0.112 and 0.119 to 0.053 and 0.056 which brings the EC to 1052.595 KgCO2/Kg. However GGBS concrete takes longer to set than traditional concrete.
By using Concrete mixed with 40% Fly Ash, it reduces the material emissions from 0.112 and 0.119 to 0.088 and 0.093 which brings the EC to 1747.82 Kg of CO2.
There are different thresholds on the upper limits of the replacement materials of blast-furnace slag and fly ash. The thresholds are linked to the strength class of the concrete. Fly ash has lower embodied energy and carbon but is limited to a 40% threshold, blast-furnace slag has a higher embodied carbon than fly ash but is able to replace up to 70-80% of the concrete which brings the overall embodied carbon lower.
Despite the advantage of GGBS, fly ash is encouraged to be used as the replacement material as fly ash is abundant in supply and large quantities are land filled each year.
Therefore to make the foundation as low carbon as possible while still considering sourcing the replacement materials of the concrete, choosing concrete mixed with fly ash is more suitable considering the material is more abundant and available. The EC of the foundation would be 1747.82 Kg of CO2.
The chart below shows the calculations of each concrete type.
The data calculations only include material sourcing to the end of the factory processes and not the transportation but the average delivery distance of ready mix concrete is 8.3km by road
The Foundation calculations exclude the EC of the Rebar of Reinforced Concrete