
5 minute read
Tool Box Tips
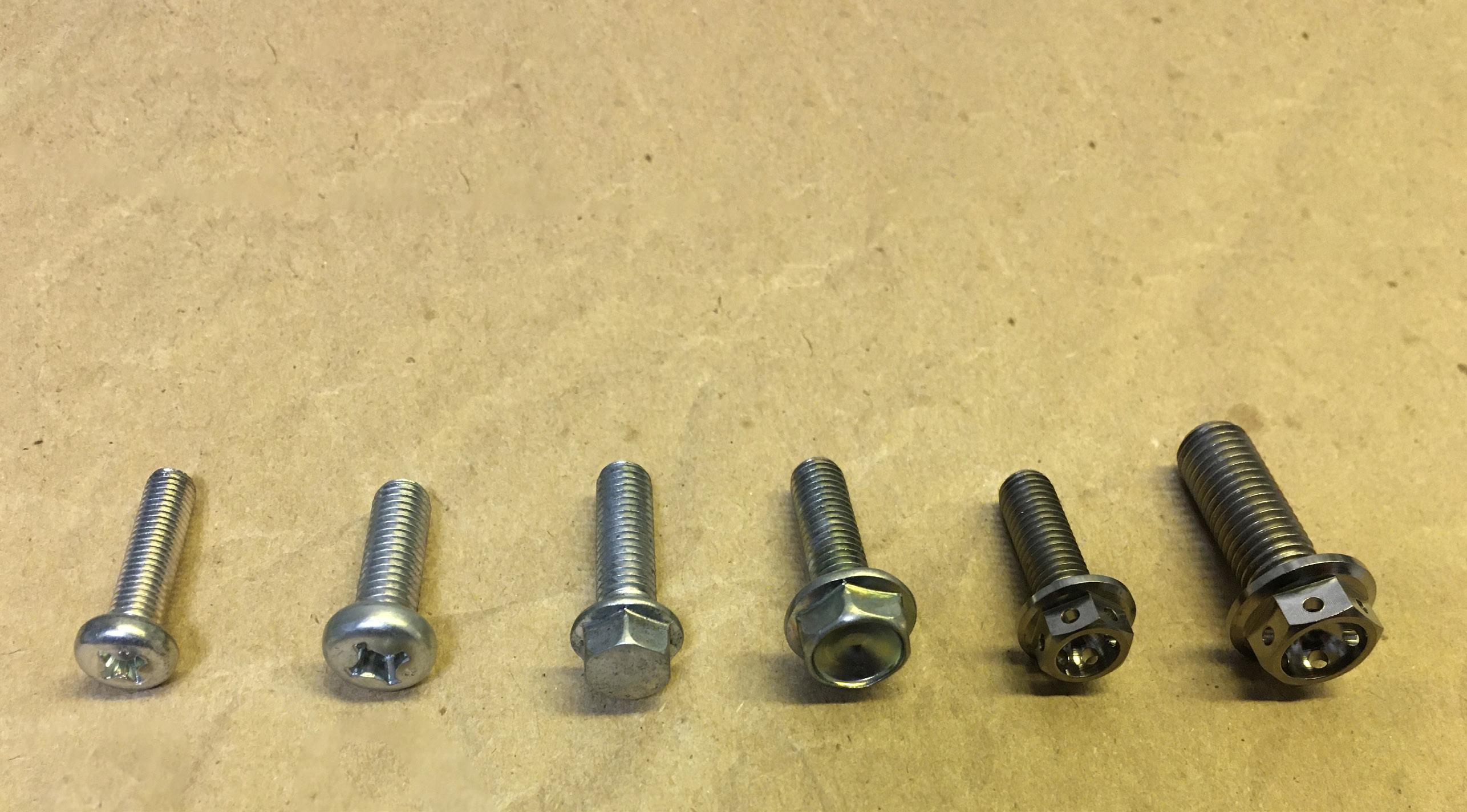
Fascinated with Fasteners and Flanges
FIGURE A
I’ve always been intrigued by the bolt thread—that rotating ramp or helical ridge responsible for clamping stuff together. Nuts and bolts. I still recall my very first attraction to the wizardry of something mechanical at around age 10. It was a buddy’s old Clinton two-stroke go-kart engine. He made it run, but it had no muffler, so I just stood in amazement watching the piston go up and down through the flaming exhaust port, smelling the premix and diggin’ all the racket. The seed was planted, and by the age of 17, I was pulling car engines and doing valve jobs. My attraction to fasteners emerged after working at a Honda shop for a few months in 1972. The fasteners on a motorcycle are noticeable and prominent, and Hondas always had attractive and nicely-finished nuts and bolts. Fast-forward fifty years and my obsession with nut and bolt form and function is alive and well. Every bike I build gets ‘the treatment.’ So, while form (the look) is cool, function is more important, especially on a vintage competition machine that spends most of its life buzzing away at high RPM. We’ve all been there: a nut or bolt takes the day off, and vanishes. I have been addicted to flange bolts for quite some time and use them for just about everything on race bike builds. (For period-correct restorations, I use the original fasteners.) Flange bolts and nuts are superior to the nut/lock washer/ flat washer stack, and dropping one thing on the floor is better than dropping three things on the floor. And, while working an all-nighter in the paddock on Saturday night,
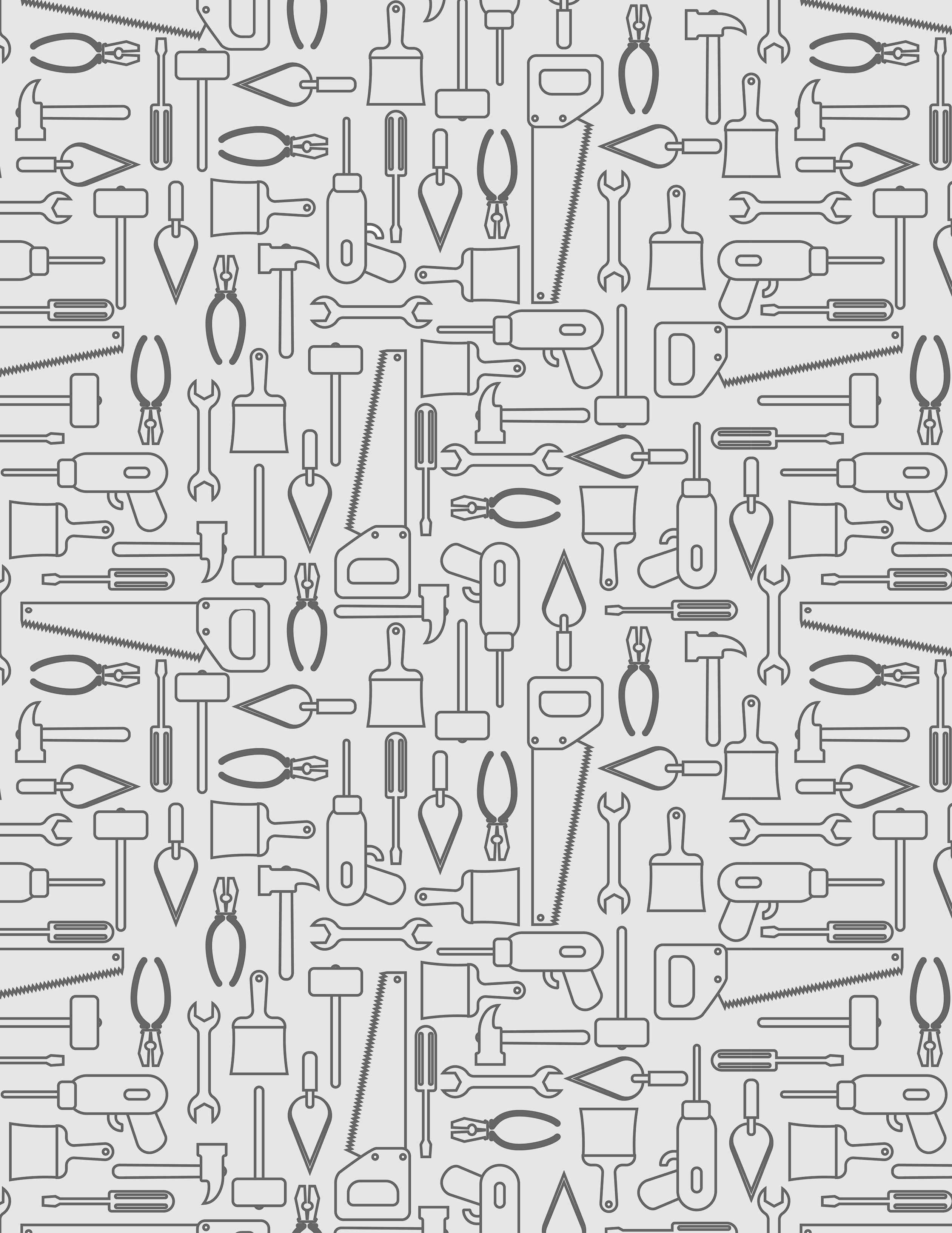
FIGURE B

the fewer parts to keep up with, the better. The flange provides a larger area of load distribution which is easier on the contact surfaces. That larger flange surface acts like a brake and keeps the fastener from loosening and spending the rest of its life in the grass outside turn nine. These flanged nuts and bolts are available in several grades and materials from a variety of sources. Here are a few I rely on. FIGURE A, above, left to right: Not flange bolts, but JIS crosshead screws, 5 and 6 millimeter. PSA: These are not Phillips® screws and using a Phillips® point will damage the screw and the driver. Next is my go-to 6 mm case bolt with 8mm hex head. They are superior to a socket head screw because of their wide flange. Socket head screws have smaller diameter heads which can dig in and deform crankcase cover castings. The fourth fastener is an OEM Honda dish-head bolt. The next two are drilled titanium with dished heads. The M6 has an 8 mm head; the M8 has a 10 mm hex head. FIGURE B left to right: standard 6 mm flange nut, aluminum 6 mm flange nylock nut, 6mm flange nut with metal locking device. I use the 8- and 10-mm versions of these metal lock nuts for securing engine mounting bolts. I like this setup (FIGURE C) for wind screens (with the rubber washer against the plexiglass) and number plates: aluminum 5 mm screw with an aluminum fender washer and aluminum lock nut.
FIGURE C
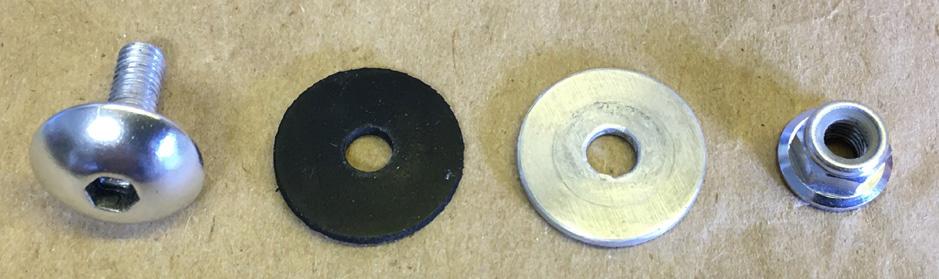
And then there are those nuts and bolts that require safety wire. I’ve successfully drilled my share of bolts and nuts but have better things to do to occupy my time, so I source pre-drilled components. There are many sources for drilled stainless or titanium bolts. I prefer the titanium bolts with the smaller, dished hex head. I like the look of these bolts, they never tarnish and are also available undrilled. Prices for these aren’t too staggering. And now, a safety wire tip or two. My first roll of lock wire was .032”. I used this size for decades until I discovered .025. This stuff changed my life. It is much easier to use, is still heavy enough for most motorcycle applications and is more suitable for hand grips (FIGURE H).

FIGURE D FIGURE E
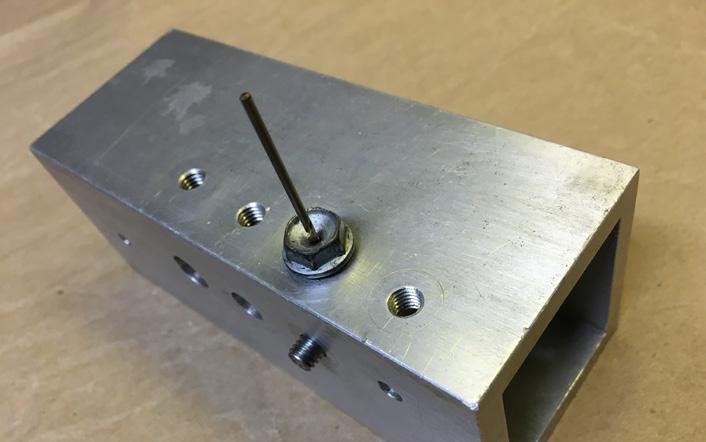
I use a Moto-D Nuthholer (FIGURE D) to drill flange nuts from flat-to-flat. This jig even works on M6 flange nuts. The Nutholers are getting hard to find though. I fabricated a jig (FIGURE E) to drill straight through bolt heads after I install, torque and mark the flats for proper orientation. Safety wire solves the disappearing bolt problem, but the wire should be installed in a position, with a tight pull, that prevents the fastener from loosening (FIGURE F, .025 wire).
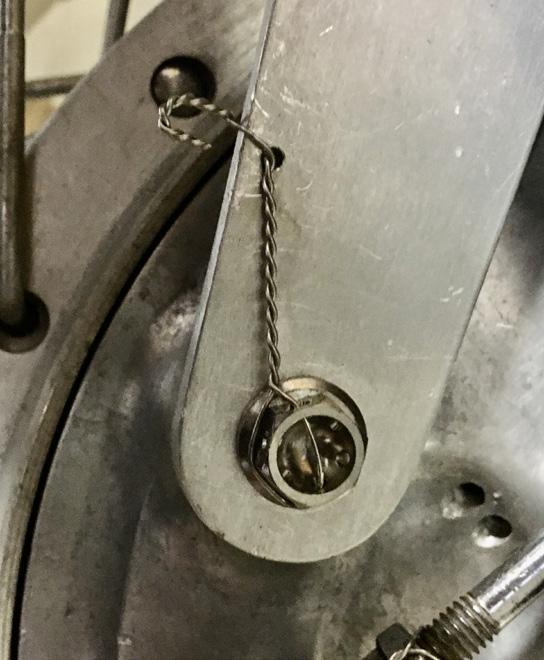

FIGURE F
I use M6X20 stainless steel coupling nuts with 13 millimeters of thread machined out (FIGURE G) and then drill each flat. (Yeah, no flange. I searched the planet to no avail.) The holes clear the end of the exhaust stud to make safety wiring the nuts much easier and more effective. Fortunately, there are sources for drilled flange nuts, 8 mm and larger.
FIGURE H
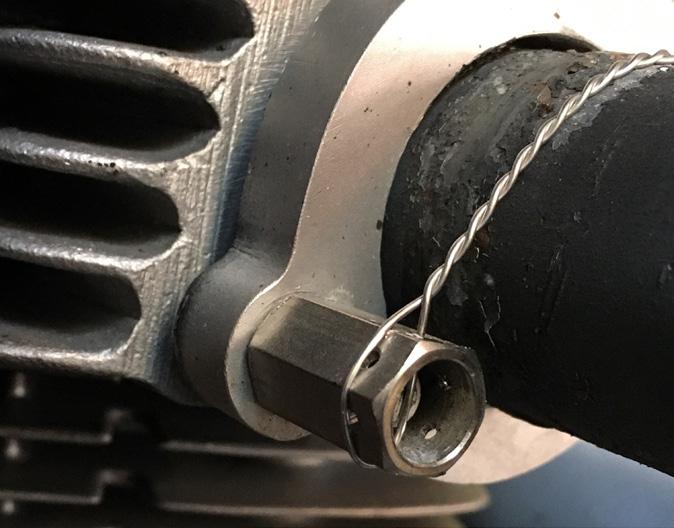
I also use .020 for many harder-to-access or lighter duty safety wiring. It works great on fuel lines (FIGURE J) and brake adjusting nuts. I use the soft and pliable OEM Honda bulk fuel hose and two wraps of the .020 is all you need to pass the AHRMA Tech fuel line pull test. I keep a small waste wire receptacle handy (FIGURE K) for wire scraps with a weight in the bottom to keep it upright. Only problem with the smaller diameter wire: punctures. You’ll need more bandages.
FIGURE J
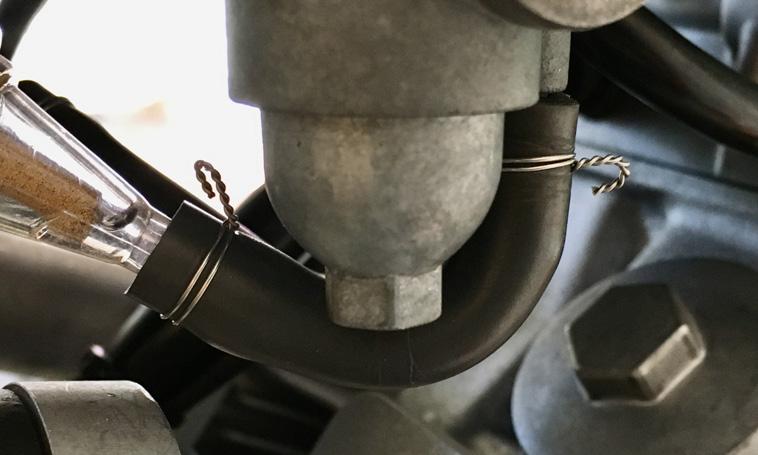
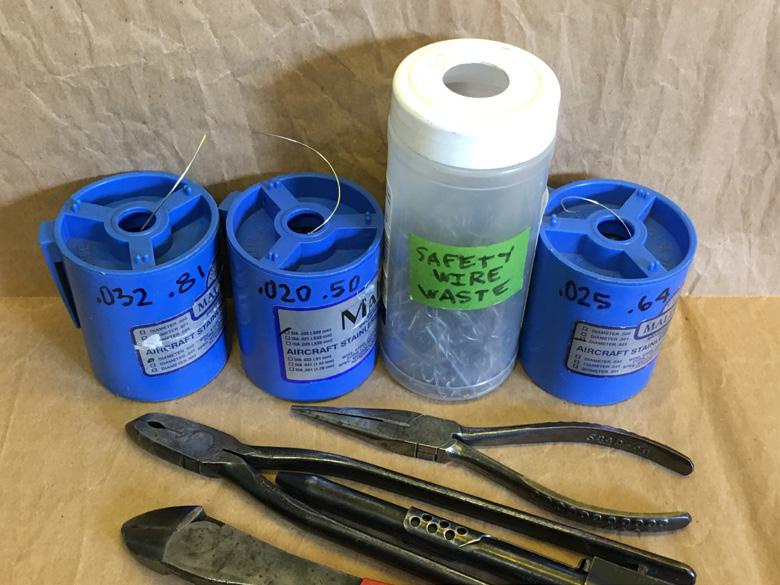
FIGURE K
I use a more modern flange nut for front and rear axles for the same reason I use flange nuts and bolts: wider load distribution. I make these safety clips with stainless rod; you just need a small torch to bend the tight retaining U (FIGURE L).
FIGURE L
I hope some of this form and function flange revelation finds its way onto your motorbike in the near future. May your nuts and bolts stay with you.
