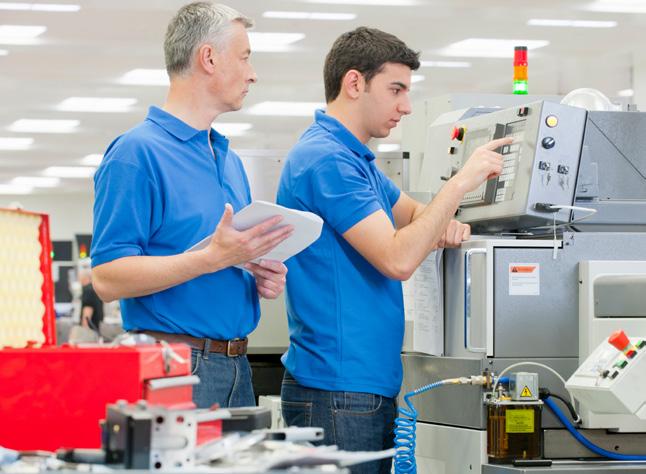
3 minute read
Supervisor Development Must Be Consistent to Be Effective
BY SCOTT ELLIS, ED.D.
Remember when your dad threw you in the deep end and called it “learning to swim”? This is the everyday experience of many production supervisors. The purpose of this article is to outline a process that equips supervisors to lead the part of the business assigned with keeping promises to your customers. Those who would pursue this further may follow the steps described here using the Individual Development Plan course in AICC’s Packaging University.
Advertisement
Most supervisor training would be best described as “drowning avoidance.” Most supervisors rise from the ranks of machine operators. In the past, a machine operator was expected to possess the technical skills to produce quality products consistently and on schedule and to direct the crew toward that objective. Today, the model operator is also expected to lead and train the crew, often on multiple machines. Entering the deep end as a supervisor, the typical operator is expected to manage attendance, triage human resources issues, expedite orders with incomplete information, and liaise with the maintenance department, while training, motivating, and holding people to account. Only a small number of these skills are gained as an operator. Is it any wonder they flail and gasp?
The responsibility of equipping supervisors is one of the most influential investments in the culture of the company. These people represent management to the bulk of the employees. Their professionalism, including their technical and interpersonal know-how, is the hinge pin of company culture. It is a big job, and you have a lot to do. So, I suggest you start small.
You could launch a training program for all supervisors in the company. To do so, you will need to overcome the resistance of incumbent supervisors who may be capable and are yet unwilling to embrace professional improvement. I usually start with the willing, regardless of capability. I inform the team that the standards and performance measures are changing, and then I invest my time with the early adopters. When the increased capability of the willing results in an opportunity for advancement, you will have everyone’s attention. Then some will become willing, and others will self-select out of the role. My patience is long for the willing learner of any level of experience or even capacity. I will waste very little time on a person in possession of technical and interpersonal skills who chooses not to employ them.
The primary ingredient for success is consistency. Your way may not include online resources or one-on-one application meetings, but until there is a better “your way,” I invite you to try mine below:
1. Revisit the job description and assess its applicability to your current expectations.
2. List your expectations for the technical and interpersonal skills of a model supervisor in your culture.
3. Download the Supervisor Professional Development sheet provided in the Individual Development Plan course in AICC’s Packaging University.
4. Customize the list of Packaging University courses to fit the supervisor. You may choose not to require some of the more basic courses, or you may add those that are a better fit for your mix of business.
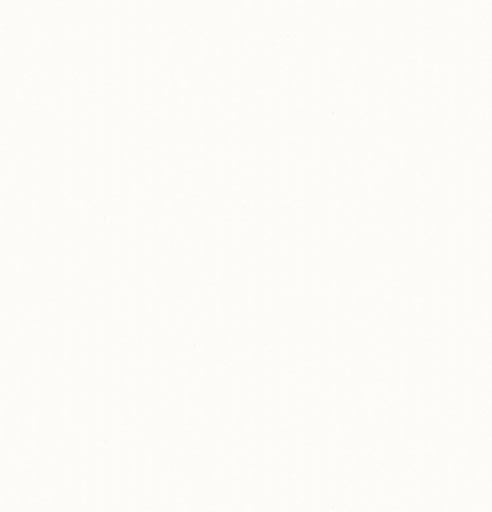
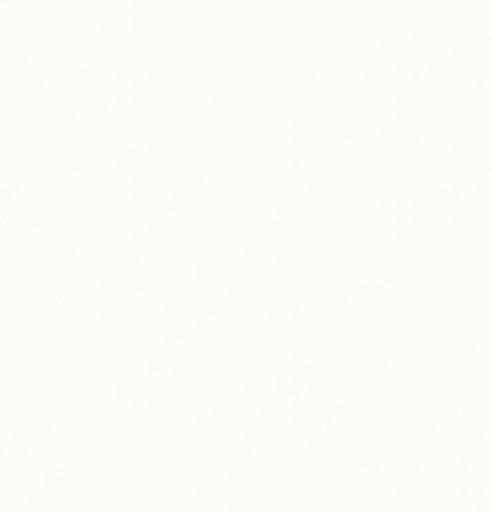
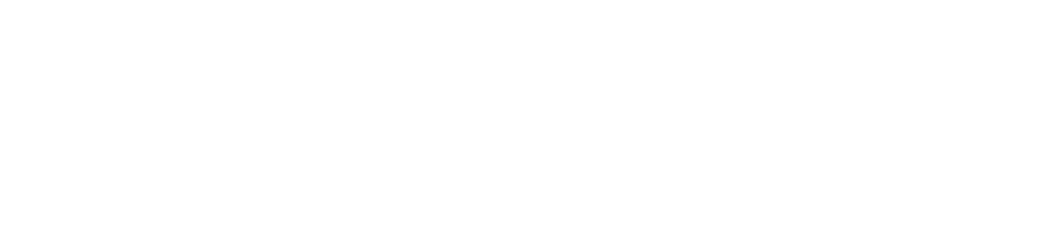
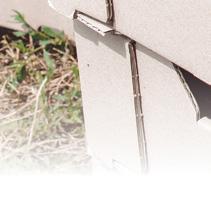
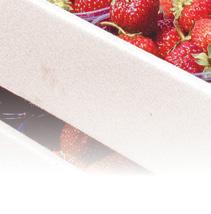


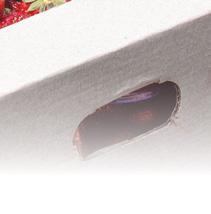
5. Add any destination courses you believe would be relevant. You may choose to add an internal experience (e.g., spend a week in scheduling or customer service) or another local offering (e.g., courses at Dale Carnegie or tech schools and community colleges).
6. Discuss the pace of learning that will fit the current workload and agree to target dates for the fi rst few courses.
7. Meet regularly to check in with questions such as:
• “What did you learn from that course?”
• “How do you suggest we apply that knowledge in our plant?”

• “What obstacles would we need to overcome to make that best practice a habit?”
8. Favor the person who proves to be willing and capable with advancement in compensation and responsibility. Concurrently, stop offering advancement to the unwilling, regardless of their capability.
9. Model willingness to gain professional and interpersonal awareness.
Your initial investment will take some time and effort, but once you have an equipped supervisor, there will be two of you to train the rest of the willing team members. Whether you model your process after the one I have provided or adopt your own, there is no alternative to investing in the capability of your supervisors. Consistency: Th is is the way.
Scott Ellis, Ed.D., delivers training, coaching, and resources that develop the ability to eliminate obstacles and sustain more eff ective and profitable results. He recently published Dammit: Learning Judgment Th rough Experience. His books and process improvement resources are available at workingwell.bz . AICC members enjoy a 20% discount with code AICC21.
Full Throttle with Full Servo
Full Servo Inline Set While Run FFG improves speed rating by up to 12.5%
The latest innovation from Latitude Machinery Corp. (LMC) features full servo, Set While Run operation providing improved accuracy and an improved speed rating across multiple sizes:
660mm x 1800mm: 450 sheets/min 1000mm x 2500mm: 350 sheets/min
1200mm x 2700mm: 300 sheets/min
1200mm x 3000mm: 300 sheets/min
Full Servo can Reduce Noise Levels by 15%
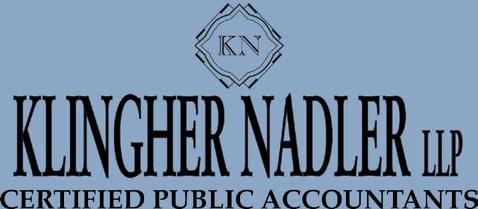
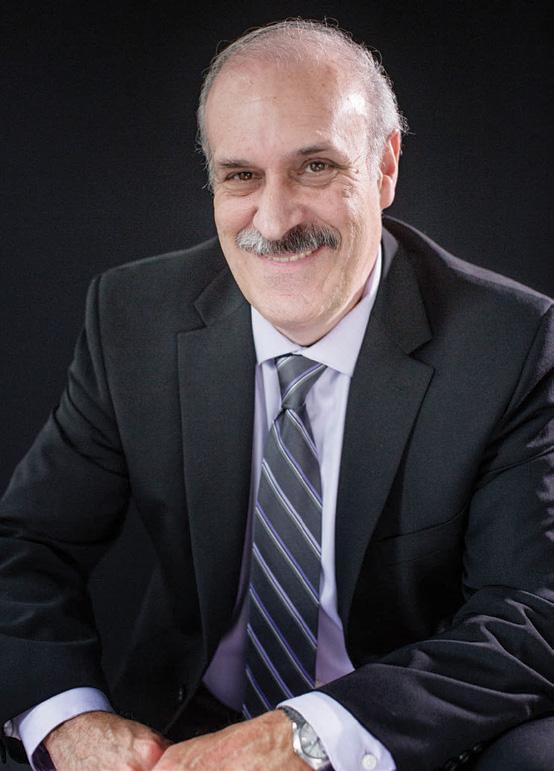
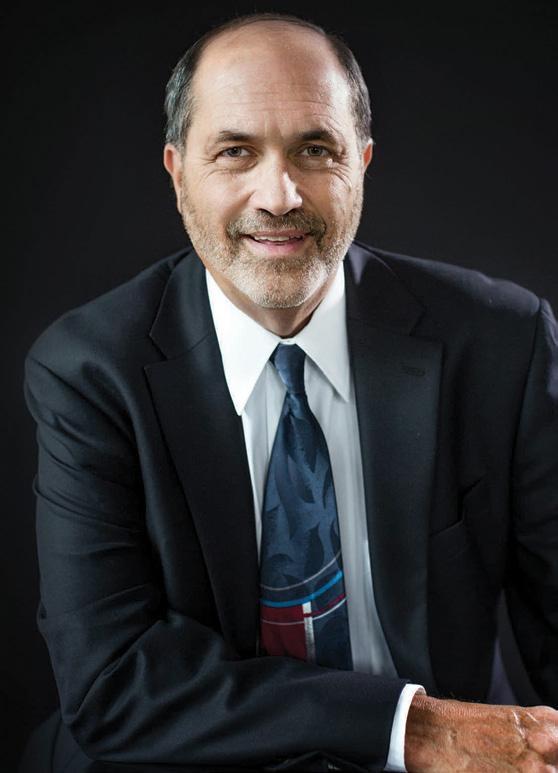