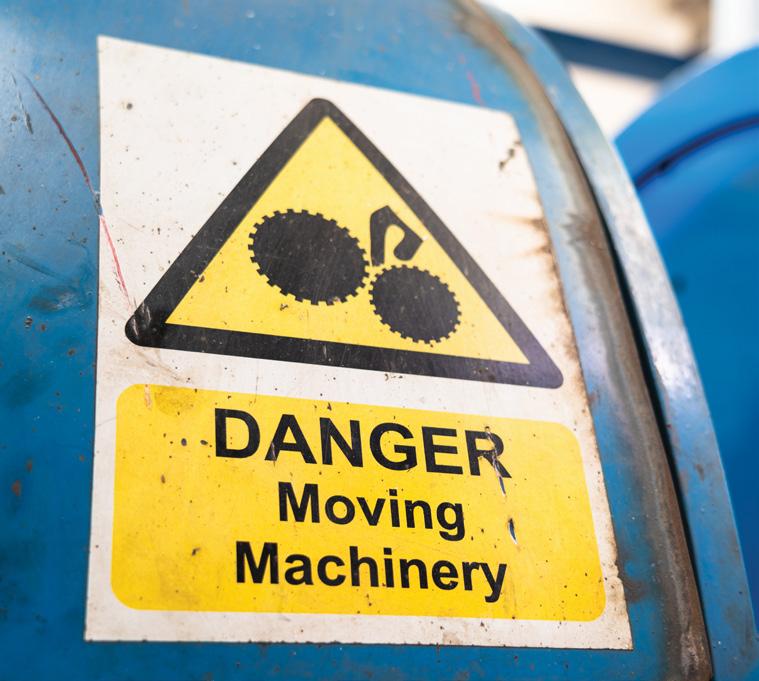
2 minute read
SAFETY IS NO ACCIDENT
A look at the top fi ve severity exposures in the corrugated industry
By John Kiefner
Advertisement
For those who have never stepped foot into a corrugated plant, it’s quite an eye-opening experience once past the front office. If I could turn back time, I would seek a safety consultant internship in a corrugated plant because no other industry offers anywhere near the variety of severe risk exposures.
While the frequency of injuries in the corrugated industry is often led by sprains or strains, trips, and cuts, the severe exposures are what keep me up at night. Rather than go through the Occupational Safety and Health Administration (OSHA) standards word for word, let’s look at some practical considerations for addressing fi ve severity exposures in the corrugated industry.
1. Caught in Machinery
Entanglement within machinery can occur in a split second when allowing any of the following items to be brought onto the plant floor: hooded sweatshirts, loose jewelry, long hair, lanyards without breakaway straps, and rags wrapped around the hand. A written policy should be in place prohibiting all of the above, and managers should strictly enforce the policy with employees and temps.
When assessing machine guarding, keep it simple. Anything beneath 7 feet that can catch clothing, hair, body parts, etc., should be guarded. Where physical guarding is used, it must be fi xed (tool used for securing) or interlocked. Other types of guards may include light curtains, pressure-sensitive matting, pull cords, etc. Although not required by OSHA, it is strongly recommended that interlocks and presence-sensing devices be placed on a testing schedule as the failure of these devices does not always lead to a fail-safe outcome. Lack of a testing schedule will eventually result in an injury or a willful OSHA violation. While conveyor rollers are not designed as machine guards, they often function as such, protecting moving parts beneath. While the focus may be placed on production machinery, do not treat missing conveyor rollers lightly. Conveyors should not be in operation without all rollers in place.
OSHA’s lockout/tagout (LOTO) standard is designed to prevent “caught in machinery”-type injuries. However, minimum compliance with the standard is not suffi cient in the corrugated industry. Th ere are complexities within corrugated machinery that the LOTO standard does not account for. Keys, rather than locks, are used to de-energize many pieces of equipment. It is essential to verify that no two keys are cut the same for other equipment or for sections of the same equipment. It is also recommended that employees be trained annually rather than just upon their hire and when new equipment is introduced. LOTO machine-specifi c procedures should be reviewed annually for accuracy, in addition to the “periodic inspection” requirement of the standard. When reviewing machine-specifi c procedures, pay particular attention to the “verify isolation” step, which ensures the lockout was conducted properly, leaving the equipment completely de-energized.
2. Struck by Forklift
Although forklift injuries are infrequent, the injury outcome is almost always severe. Aside from required training (upon hire and every three years) and pre-shift inspections, additional steps can be taken to lessen the chance of a pedestrian being struck by a forklift. Where possible, protect pedestrians from forklift traffi c with walls, protective rails, bollards, etc. For pedestrian and forklift intersections, strobes triggered by oncoming forklifts can be eff ective, as well as strategically placed mirrors. All forklifts should be equipped with blue light systems, which shine a blue dot on the fl oor ahead of the oncoming forklift. High-visibility shirts and vests can also help make pedestrians more visible to drivers. Th ere are so many variables with forklift and pedestrian interaction that a variety of preventive measures need to be considered.