
4 minute read
The Board Handling System
3. Fall From Heights
Employees conducting work above 4 feet must be protected by a railing or must wear a fall-arrest system. The former is preferred over the latter as there are many variables to a fall-arrest system, including the fact that the user must put it on. Areas of fall exposure in the corrugated industry are as follows:
Advertisement
Mezzanines
Where product is loaded or staged on overhead platforms, mezzanine safety gates should be considered instead of removable rails or chains. Flip gate systems provide 100% protection during this task.
Loading Docks
If above 4 feet, dock doors must be closed when the dock is empty. All unprotected areas of the dock should be equipped with an approved railing (42-inch top rail, 21-inch midrail).
Roof Work
Roof work performed within 6 feet of the edge on a flat roof requires a fall-arrest system. When working 6–15 feet from the edge, a warning line must be installed. When working on a pitched roof, a fall-arrest system is always required.
Fixed Ladders
Fall protection systems are required to be installed on fi xed ladders greater than 24 feet in height. Existing fi xed ladders are grandfathered until 2036, at which time they must also be equipped. Self-closing safety gates are recommended at the top of each fi xed ladder.
Scissor And Aerial Boom Lifts
While OSHA mandates the use of fall-arrest systems only when operating an aerial boom lift and not a scissor lift, falls frequently occur from scissor lifts when occupants climb onto the protective railings. It is strongly recommended that company policy mandate the use of fall-arrest systems when working within scissor and aerial boom lifts.
Cleaning On Top Of Machinery
If cleaning tasks at heights above 4 feet are not contracted out, physical protection or a fall-arrest system must be considered. If installing a fall-arrest system, it is recommended that an expert in the field be consulted as there are many variables.
4. Confined Spaces
Confined spaces are rarely discussed within the corrugated industry, yet they present a significant risk if handled improperly. Confined spaces in the corrugated industry often include storage tanks, pits beneath machinery, manholes, dust collection systems, and more. Almost all confined spaces can further be defined as “permit required” as they contain an internal hazard (atmospheric, physical, etc.). Dabbling in confined space entry is a recipe for disaster. Therefore, after assessing and labeling the space, the following should be considered.
Prevent The Need To Enter
In many cases, pits beneath machinery are entered for cleaning purposes. Many companies have fi gured out ways to minimize scrap from entering these pits. In addition, they have utilized manual “grabbers” to pull out larger pieces of scrap and have implemented vacuuming systems to extract the remaining portions.
Contract Out Confined Space Entry
Permit-required confined space entry can be complex and costly. Infrequent entry usually results in improper entry with varied levels of compliance. It is recommended that confined space entries be preplanned and contracted out using a company that specializes in confined space entry.
Temporarily Reclassify The Space As Nonpermit
A permit-required confined space containing physical hazards, not atmospheric hazards, can be temporarily reclassified as nonpermit through proper LOTO procedures. Th is can occur only if a series of atmospheric tests have been conducted to determine there is no risk. It is common for pits beneath machinery to contain a physical hazard from moving machinery. In most cases, the pits do not present an atmospheric hazard and can be safely entered once lockout is performed to de-energize the machinery that presents the risk.
5. Combustible Dust
Combustible dust explosions can occur under specific circumstances, producing catastrophic results. The perfect storm includes the “fi re triangle”—combustible dust, heat, oxygen—and the dispersion of dust in a confi ned area. Dust particle size must be fi ne enough for it to be combustible. Don’t bother testing the dust at your plant because all corrugated plants produce combustible dust through one or more of the following processes: trimming, die cutting, shredding, baling, and more.
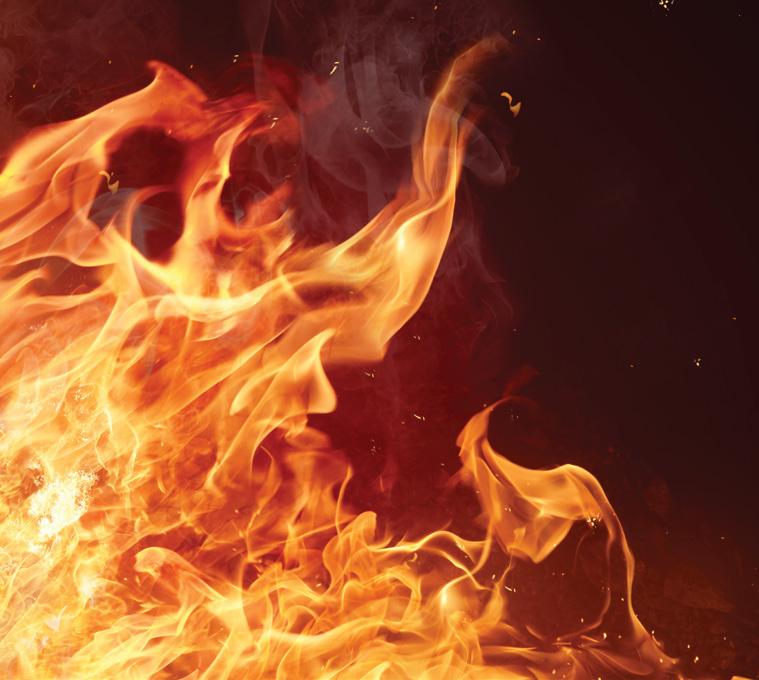
Dust Collection
Good housekeeping throughout a plant is the most essential element of a combustible dust prevention program. Th is includes capturing dust at the source through a dust collection system. When designing a system, utilize a manufacturer and installer with combustible dust expertise so all OSHA and National Fire Protection Association standards are incorporated within the system. In addition to dust collection systems, many within the corrugated industry are incorporating air dust fi ltration systems to capture the smallest dust particles that escape traditional dust collection systems.
Plantwide Cleaning Schedule
Dust in fine particle size will not only settle where it is produced but will travel throughout buildings and settle on any available flat surface, including machinery, piping, rafters, etc. OSHA has been known to issue citations under its “general duty clause” for dust accumulation that is the thickness of a dime. Setting up a plantwide cleaning schedule is imperative in preventing dust accumulation. When conducting the cleaning in-house, explosion-proof vacuums must be used.
Training And Education
Compressed-air hoses are located on most production lines in corrugated plants. The air hoses, if used incorrectly, present the opportunity for dust dispersion, which is one of the elements leading to combustible dust explosions. Employees must be educated on how dust explosions occur and must be informed that the air hoses are not to be used in a manner that allows dust to be blown into the air. The common practice of “blowing out” a forklift must occur outside and away from the building. Machinery that commonly accumulates dust should be frequently vacuumed rather than blown out.
Stay Vigilant
While frequency trends deserve continued attention, severity exposures often catch companies asleep at the wheel. Make time with your safety committee and management team to individually address each of the top five severity exposures. As you do so, utilize the AICC network for best practices as safety and risk protocol within the corrugated industry is quickly evolving.
John Kiefner, CSP, ARM, is vice president of risk control at Johnson, Kendall & Johnson.
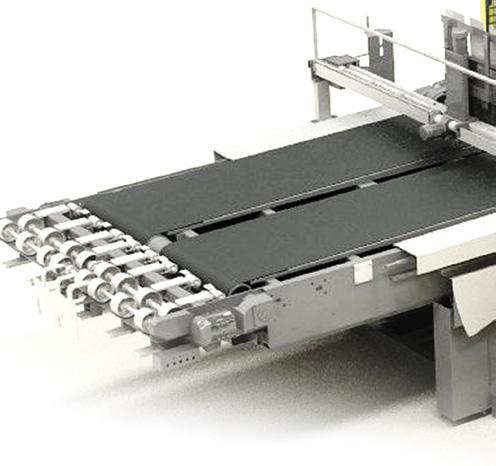
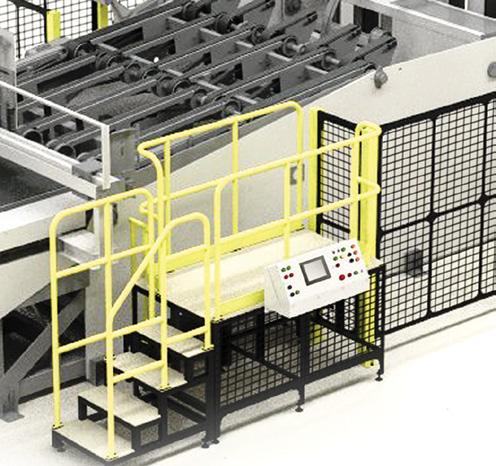
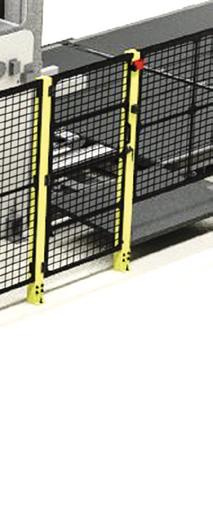
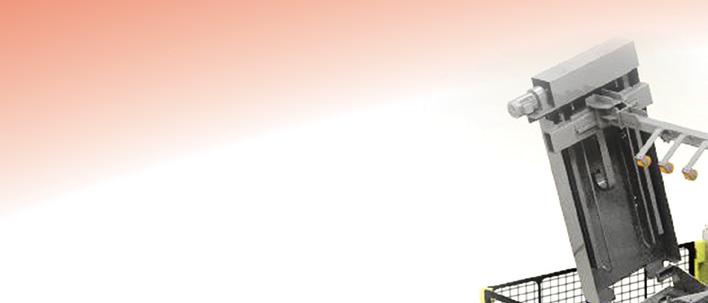
