
2 minute read
What the Tech? The Benefi ts of Inkjet Printing
BY CHRIS BURDICK
Data proves that by investing in single-pass digital printing technology for corrugated packaging, a plant can generate additional benefits by increasing manufacturing capacity.
Advertisement
EFI has published a case study showing how incorporating a digital industrial printer into a corrugated packaging plant expands total manufacturing capacity, thereby accelerating the return on digital investment.
The case study is not about the new possibilities of the disruptive technology or about future business, but an analysis in a real plant, with actual order data. Th is in-depth analysis was conducted in collaboration with the management of a North American converting plant and demonstrates that investing in digital technology adds capabilities and flexibility by:
• Allocating jobs to the equipment that produces high-quality graphics more efficiently based on the characteristics of each order,
• Leveraging existing analog capacity without the need to invest in new flexo presses,
• Maximizing overall equipment effectiveness and overall plant profitability, and
• Proving to be an attractive capital investment with rapid return on investment.
For this study, data was collected from a converting plant equipped with eight flexo presses from one to five colors and a total production of 1.6 million msf per year. The study focused on two flexo presses with a total production of 560,000 msf per year. Production data was collected over a period of more than three months for further analysis.
The analysis began by calculating the break-even point between digital and analog printing. Th is made it possible to determine the average order size for which digital printing technology was most cost-effective. In this case, the average set the break-even point at 65,000 square feet. In other words, orders up to that amount were more profitable in digital printing than in high-quality flexo.
Based on 90 days of order-level data, orders above and below the break-even point were grouped to measure the direct savings from using digital where it is most efficient. These are savings or efficiencies generated by producing orders below 65,000 square feet with a popular digital printer instead of with the analog equipment used until now. By comparing the printing costs of one technology with the other, we identified savings of $1.2 million per year.
Next, the extra capacity generated by transferring orders under 65,000 square feet from the current analog equipment to the digital single-pass printer was calculated.
To do so, the average production times from analog manufacturing and the times from digital manufacturing were considered; the difference between them gives the available overtime. These overtime hours can now be dedicated to orders over 65,000 square feet, which, for the case analyzed, meant an additional capacity of 249,725 msf. Th at is, with digital printing, analog capacity increased by 42%.
The last part of the analysis was the profitability measurement that showed how the payback on the investment in certain digital technology can be realized in less than two years.
It is worth doing this calculation exercise and considering now the investment in technologies that are a reality in the market and are providing a competitive advantage, efficiency, and extra capacity. And they do so with unprecedented flexibility because digital printing makes it easy to serve orders of any size.
Th is methodology can be applied to any corrugated packaging operation to identify the profi le where the impact of incorporating single-pass digital inkjet printing technology will be greatest. Thus, we can anticipate that digital printing will have a greater impact in plants that produce a significant amount of high-quality work with complex processes (fl atbed die cutters, folder gluers) and diverse types of materials.
For plants that do not currently manufacture value-added packaging, digital printing technology should be considered because it is the most efficient way to add high-quality printing capabilities while presenting opportunities for improvement.
Chris Burdick is sales director of packaging at EFI. He can be reached at 310-741-8768 or chris.burdick@efi.com

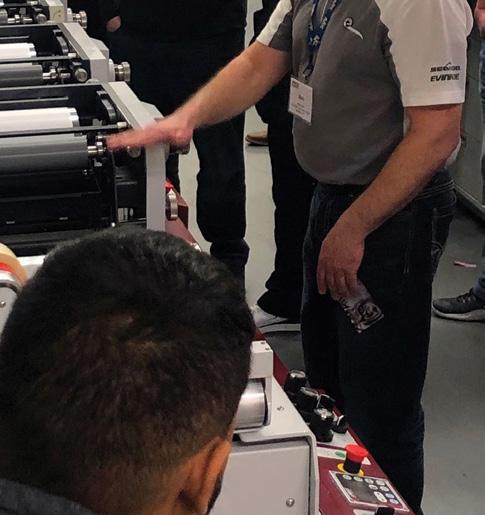
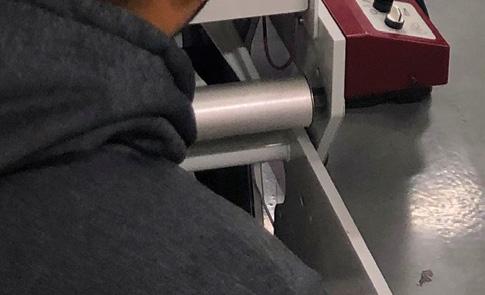