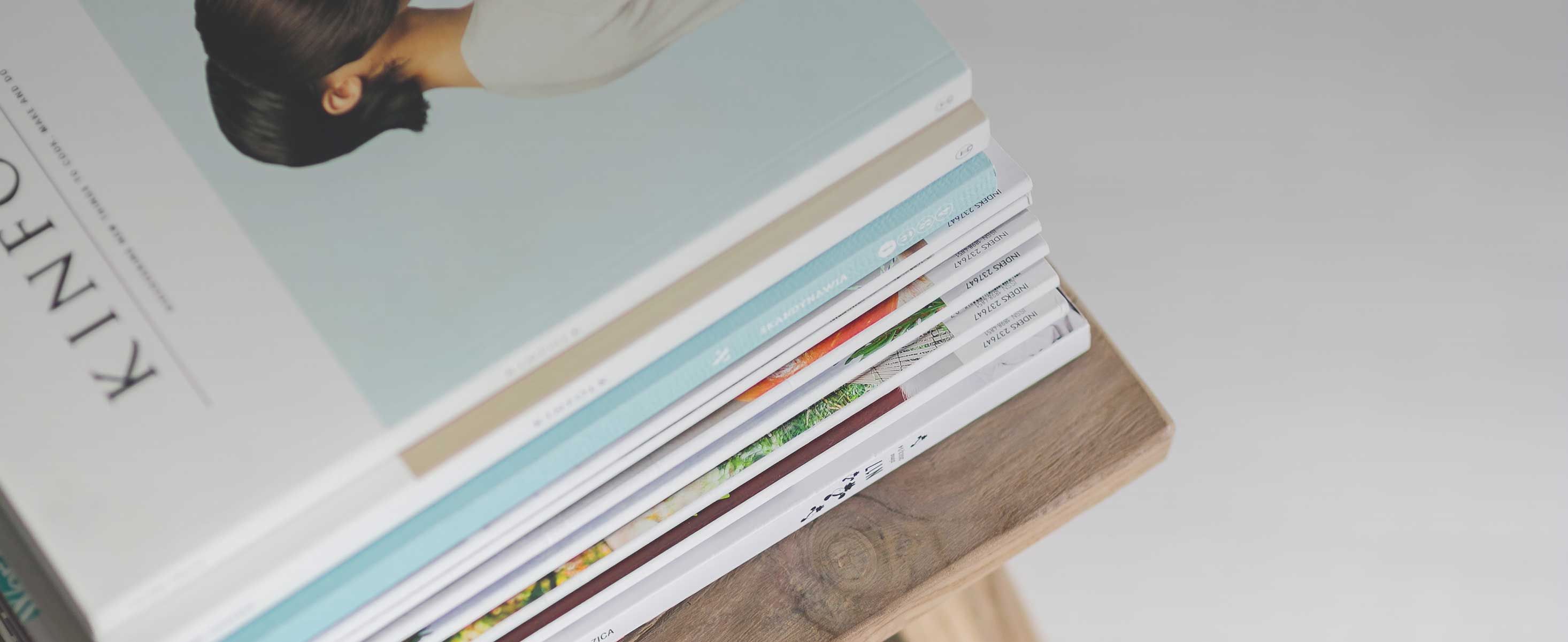
3 minute read
STRENGTH IN NUMBERS
End-of-Line Bundling Automation With Remote Monitoring, Data Sharing
BY JERRY VIVLAMORE
Advertisement
As corrugated plants continue to make major investments in technology and equipment, both in legacy and greenfi eld facilities, much attention has been rightly placed on the substantial outlays in fl exo folder gluers. In eff ect the marquee centerpiece of any plant, it shouldn’t overshadow automation investments of the supporting equipment cast further down the line.
One such area that deserves consideration is the choice of automated bundling solutions. Independent box manufacturers—and, to be sure, the integrateds—are looking for high-speed bundling or in-line redundancy features that enable auto strap changes and easy-to-program bundle recipes that can be achieved in seconds.
Many boxmakers are also opting for the latest speed and production enhancer, commonly referred to as bundle diversion technology. Th ese systems optimize the power of two squaring bundlers that connect with dual-zone conveyors to meet the extreme demands of fl exo folder gluers and operate at speeds of up to 36 bundles per minute.
It’s an elegant solution that directs all bundles to the active bundler during a coil change or while the other temporarily inactive bundler “mends itself” with the auto-refeed feature. Once the inactive bundler changes the coil, it comes back online automatically to share the line.
Ideal bundling systems are OEMagnostic in relation to the fl exo folder gluer and allow for easy transfer of data from the fl exo folder gluer to the bundlers. Th is can be achieved through an ethernet cable or through collaboration with OEMs. Remote monitoring software supplies technicians and plant managers with the insight to see how things are operating and help to shift to optimized preventative-maintenance models.
Th e end game is that the machine can alert the OEM technical staff that it’s encountering too many strap refeeds.
To cite one example, at Signode we have many tandem bundling systems in place across the United States. One particular facility had seen a large amount of turnover, causing some bundling recipes to become out of spec. Th rough data sharing, we started to see that refeeds and failures were getting high. Our programmers in the European Union were able to go online, check the data, and see where some of the bundle recipes had gotten a little off ; our service tech was on-site, and we had him make the changes immediately. Th e customer’s refeeds dropped to almost nothing.
Also, in light of the labor challenges confronting the industry, premium automated bundling technology should include an icon-driven human-machine interface that enables even novice operators to quickly set up a new recipe with just a few taps of the screen. Other technology enhancements to look for are related to the chutes. Next-generation bundlers feature segmented chutes. After several million cycles, replacing a worn chute can be costly and time-consuming. Changing a single segmented gate can take no longer than 20 minutes.
In many respects, automated bundling solutions are a small but important example of Industry 4.0 at work in real time. Th e integration of complex equipment with software platforms leads to predicting and preventing unplanned downtime, reducing losses, and driving productivity gains.
As we know in this industry, enhancing production while keeping quality foremost is of highest priority. Bundling may seem like a commodity equipment choice given the complexity of corrugated facilities, but truly future-focused boxmakers are always on the lookout for smart technology and support to improve operations.
Th e enhanced productivity, simplifi ed maintenance, production versatility, and robust design of automated bundlers and their integration with software and remote monitoring systems could be the diff erence that distinguishes and future-proofs your operation from its competition.
Jerry Vivlamore is corrugated bundler segment manager for automation and packaging technologies at Signode.