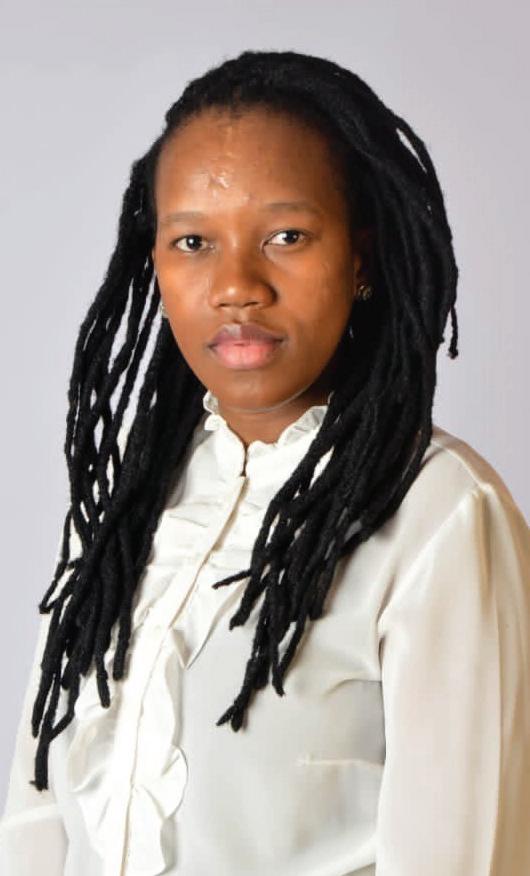
10 minute read
How The Pandemic Gave Birth to SA’s latest 4IR SaaS platform
CHANGING TIMES: How the pandemic pivoted this SA engineering consultancy into a 4IR SaaS platform
By Daniel Mpala
South African industrial engineer Katlego Malatji believes that when it comes to manufacturing, Africa is lagging so far behind with technology that it is making the continent less competitive globally. “It’s really sad because we are one of the richest continents in terms of raw materials, but we are not doing a very good job in terms of processing that raw material into value added goods and then selling them,” she says.
She explains that, for example, South Africa’s manufacturing industry is operating at a comparative disadvantage relative to countries like China who are actively using Fourth Industrial Revolution (4IR) technologies like automation, robotics, AI and the Industrial Internet of Things (IIoT). She says as a result of the efficiencies realised by these technologies, China is selling goods at a fraction of the cost, while local manufacturers on the other hand are losing out — despite working twice as hard — as their processes are much more labour intensive.
Malatji — who’s over the past six years built a name for herself as an international 4IR implementation specialist working for automative manufacturer BMW — points out that globally, the manufacturing industry is generally “moving in the direction of 4IR”. She strongly believes this is the trajectory Africa should be taking too.
This need for African 4IR solutions is what inspired her to start her own consultancy — ProjectOne Engineering. Malatji studied Aerospace, Aeronautical and Astronautical Engineering at Wits University for three years ending in 2014, thereafter she took up an Industrial Engineering diploma at Tshwane University of Technology (TUT) before attaining her BTech in Industrial Engineering at the University of South Africa.
“My expectations going into studying engineering were that we were going to be working on 4IR. I didn’t know the name at the time, but I had the idea that engineering is finding the solutions for the future - the robotics of it, the system optimisation — but that wasn’t the reality of it, at least not then in South Africa,” she says.
Her first job saw her work as an Industrial Engineering trainee at a company in Brits which specialised in supplying electrical protection and factory automation solutions. She remembers that during her stint there in 2015, she noticed that there was not much tracking of data going on at the company. “Data wasn’t seen as gold, which already at the time I thought ‘We need data, we need much more data than what we have’,” she recalls.
Later that year Malatji joined BMW South Africa (SA) as an intern focusing on quality management, and particularly on optimising processes to minimise defects. She says she learnt a lot from that role. “It felt like I was at a a new university because they had automation —to a level, they had systems that were in place, standards that were in place, and data was gold there,” she explains.

ProjectOne Engineering founder Katlego Malatji
However, despite this, within six months Malatji began seeing opportunities for implementing 4IR techniques. Some of the suggestions she made included improvements like using cameras to detect defects. She says at the time the responses she got were always around “budgets and business cases”. “They had processed that had been going on for years and years, and those processes were working, they were good processes that were working. My ambition was for there to be more new technology put into place, not just for the sake of technology, but for the sake of seeing us move from one level of production to the next,” she explains.
In 2017 Malatji made history in the company by becoming the first South African to be independently hired from a BMW SA plant to work at BMW US. In her new role as a Logistics Integrator at BMW Manufacturing in Greenville, South Carolina she chose a project which allowed her to work on the full-scale introduction of automated guided vehicles (AGVs) — something she said had never been done at any other BMW plant at the time.
In essence the project entailed taking normal-sized fork lifts and tuggers and outfitting them with hardware and software which effectively made them autonomous.
“At the time I didn’t know it, but when I got to the US it was apparent that it was a very big deal,” she says.
On the successful completion of that project, Malatji then applied to join another project with BMW UK, this time working on logistics material flow and supply chain. This was around peak Brexit, with the company trying to figure ways to optimise its supply chain — particularly routes and truck loads —in case the borders shut down.
“There was a lot of innovation, there was space for innovation, space for free thinking,” she says. The objective of the project Malatji worked on during her stint with BMW UK involved making £1-million in savings per year. Within six months the South African engineer had managed to save the company £1.2-million through the use of route-optimising algorithms.
Her managers, she says, told her that the company had had trouble with that particular objective “for quite some time”. “I asked them what had been happening in the previous year, it was six months before I quit. Because immediately then I was like I’m ready to go start my company.”
Starting ProjectOne IoT
In September 2019 Malatji moved back to South Africa and registered her consultancy. Initially she was working with two contractors. “I was the only full time employee. The first project that we got was a construction company that needed AI to optimise their material, the second one was a yoghurt production company that wanted to increase their production capacity — they had more orders than they were able to fill — so they needed to design a process that would help them optimise the resources that they had.”
“Then the third one that we had was a supply chain project, it was an online store that wanted to digitise the way that they were tracking their material and storing it. We had those projects, the first one from December 2019, and the others from February 2020 and then in March we were still talking to larger manufacturers about their processes. We were talking to a mining company in Germiston that wanted to improve their bearings. But when COVID hit, all those projects just slowly came to a halt. Some of them are still talking about resuming, while some of them were paused indefinitely,” she says.
Malatji says when these projects came to a halt, she realised in May that the pandemic would affect her business. “How do you consult for a company that’s closed? This is three months after I’d started ProjectOne and already there was a global crisis.”
At the time Malatji says she had been working on an AI platform that would optimise systems in manufacturing and she heard about an opportunity for South African startups with IBM. Malatji applied for the initiative — the IBM Tech Accelerator run in partnership with Tshimologong Digital Precinct— and was selected of the programme along with 13 other companies.
Malatji presented the AI platform to IBM and then spent three months talking to the company about it. “It was basically pitching to them but over incubation. They didn’t focus on ‘Oh you’re just pitching for us’, but they focused on how do you actually style your ideas and pitch for other people and grow from there.
“ProjectOne came out second and was awarded R300 000 towards the building of the platform and then they also partnered with ProjectOne to supply some of the software to the value of over R500 000. From there I realised that given Covid19, manufacturers have to change their approach to how they do business,” she says.
She explains that the pandemic made manufactures see the importance of 4IR and the need to move away from traditional systems where you needed everyone on site for anything to happen.
“They started to really see that there are processes that you can automate to keep your business going if anything happens. Companies who had that already, or an element of that already, did better than ones that didn’t have any automation at all. But overall, really when you talk to manufacturers now its a whole different conversation because 4IR used to be a nice to have - we are already doing so well in business, why change what’s working. Versus now, now they see it as a critical part of running business,” she adds.
The SaaS pivot
She explains that the same way that manufacturers had to change, so too did her company. “We weren’t just consultants being able to go to a company one-by-one. I was able then to focus on the platform which would then change into a software-as-aservice (SaaS) product,” she says. Malatji says she’s still working with IBM on the SaaS platform, which is called ProjectOne IoT. “I have two go-to-market partners who are interested in offering the platform to their clients once it is ready. We are working on getting two manufacturers in the FMCG sector on board who can be proof of concept partners,” she points out.
ProjectOne’s approach, she explains, is a proactive one which relies on data analytics. “So we take big data processing and data analytics to identify the critical areas where waste, problems or defects might occur, and we are able to provide solutions before those costly problems or de-fects occur,” she says.
“A better example is where there are recurring defects. Recurring defects are a huge, huge source of loss. There are even defects that are accepted now because they (manufacturers) have done several projects on them, and it’s cost a lot, but there’s a control that you can put in there to say ‘Ok we put someone to inspect every single one of them,’ and when there’s a defect fix it on sight. Now we are saying, ‘Ok let’s go two steps back, the problem that you are seeing could even be another symptom.’ So the in-depth root cause analysis of an engineering problem using data is what puts the answers in the factory owner’s or managers hands.”
“Any sustainable solution should still be in use in the future. We are not saying we are going to solve every problem with 4IR, but if there’s a problem that we can solve, and there’s a 4IR solution that fits that problem, it makes more sense to go for that solution that is sustainable than to go for a temporary solution,” she says.
Malatji wants to launch ProjectOne IoT to the manufacturing industry in Q2. “It’s going to be part of an engineers toolkit — especially the consultants. It shortens the problem discovery part of their engineering project by using data and analytics. Because it’s a platform and it’s SaaS, we definitely want to go into the rest of Africa,” she says.
This 4IR approach to manufacturing, Malatji believes, will “definitely” put South Africa and the rest of the continent in a place where it will be globally competitive. “They (developed countries) are a little bit ahead of us, but we are all at the starting line of 4IR. Or at least of using AI specifically for manufacturing,” she adds.
Malatji however acknowledges that there’s a fear of AI and 4IR technologies in South Africa which she believes is driven by a misunderstanding of what these technologies and what they can do. She believes that there’s need for education and awareness on these 4IR technologies.
She explains that her company is focused on educating society on how 4IR technologies like AI do not actually exclude people from industry. The company recently held a webinar — in partnership with TUT’s Directorate of Research and Innovation and Pretoria North Regional Innovation Networking Platform — to introduce the benefits of 4IR in business.
Malatji explains that her company is — in conjunction with some academic institutions — working on an introductory course, which is likely to start in June, aimed at those who work in manufacturing. “It’s about the basic core steps of what goes on in 4IR. It answers the question why anyone should be interested in 4IR,” she says.
“ProjectOne is talking about the practical application of 4IR. We are talking about going on the ground and taking a system that used to be labour intensive and improving it,” she says. She adds that it’s also important to open up dialogue on 4IR with the government. “ It’s no use having a company like mine being afraid that people will say you’re taking our jobs and stopping the conversation there. Government should also be backing up AI by bring excited about AI and 4IR and showcasing the technology so that we don’t have the same problem that we have now that there’s a shortage of skills in this area,” she adds.