
4 minute read
HOW GS1 AUSTRALIA PIVOTED TO SUPPORT PPE MANUFACTURERS
WITHIN A WEEK, AN IDEA BECAME A REALITY, AND GS1 AUSTRALIA WAS ABLE TO SUPPORT PPE MANUFACTURERS TO GET MUCH NEEDED ITEMS TO HEALTH CARE WORKERS QUICKLY.
While we knew something was coming, when COVID-19 hit Australia and we went into lockdown in mid-March, so many plans went out the window.
At GS1 Australia, we were not only concerned for our employees and our members, we were also concerned for the broader community and determined to find a way to assist.
THE IDEA
A GS1 staff member had seen on the news that the NSW government had issued a call-to-action for manufacturers to re-tool for the manufacture of personal protective equipment (PPE) to support the national effort. PPE includes masks, gloves, sanitiser, gowns and all manner of equipment that keeps our healthcare professionals safe when treating COVID-19 patients.
Our colleague suggested, having worked with the healthcare sector, that many of these companies would not be familiar with the requirements of the sector. Regular procurement needs include the provision of a barcode and accurate master data.
We resolved to smooth the pathway for these companies to ensure their products didn’t clog up the supply chain and were able to get to the places they were needed – the medical front line.
HOW COULD WE HELP?
After a brief meeting of the executive team it was agreed to provide free barcode numbers to any company who didn’t already have them for PPE products. However, having a barcode was only part of the solution.
Many state and territory health jurisdictions and private suppliers have built their systems around the provision of accurate data through the GS1 Australia National Product Catalogue (NPC). Communication of product recalls through Recall Health (and with the rush to manufacture, recalls were a real possibility) and Barcode Check reports are important to confirm that the barcodes scan and that the product number is unique.
As part of the solution we also needed to train and support these companies, many of whom had never used barcodes before, to ensure they did it right the first time, as there was no time to waste.
It was approved that new membership and access to the relevant services for suppliers of PPE products would be made available free of charge, at least until the end of June 2021.
MAKING IT HAPPEN
It was critical we put everything in place to support these companies as quickly as possible. Many had already begun to re-tool, while others were considering their own positions.
First, we had to make sure we could fully support the initiative. This involved updating our online membership subscription system to ensure it did not charge new members who were joining for the PPE program. Then ensure the customer support team were ready to contact those companies, understand their requirements and point them in the right direction.
Our Customer Relationship Management (CRM) system had to be updated with a new customer interest group and accounting systems were adjusted so a fee was not charged when they used services offered by GS1.
COMMUNICATION WAS KEY
A web page was built in a day to outline details of the program and display a list of all the PPE suppliers that could then be shared with healthcare providers who were desperately looking for scarce supplies.
Letters were sent to health and industry ministers in NSW, federally and in other states, to alert them of the program and allow them to direct manufacturers to GS1 who were reaching out to government for advice and guidance – keen to assist but not sure how to go about it.
A media release was shared with mainstream and trade media, with over a dozen publications circulating it. Our social media channels also shared the news. We did not know who would be needing us, but we wanted to get the message out there quickly, because the need for equipment was urgent.
An email went to each of our 22,000 member companies. We didn’t segment by sector, as we often do, because companies from all sectors were throwing their resources into the cause.
PROMISE DELIVERED
Within a few weeks, over 100 companies had joined GS1 Australia and ordered their barcodes, which would go out on products sent to the healthcare frontline.
Lark Distilling Co. was one such company. They already had barcodes for their world-famous Lark whisky, made in Tasmania, and committed to making sure the Tasmanian healthcare system had enough hand sanitiser by re-tooling their operation for production. The GS1 PPE program allowed them to put the necessary programs in place to fulfil that commitment.
said Dan Knight, Head of Hospitality at Lark Distilling Co.
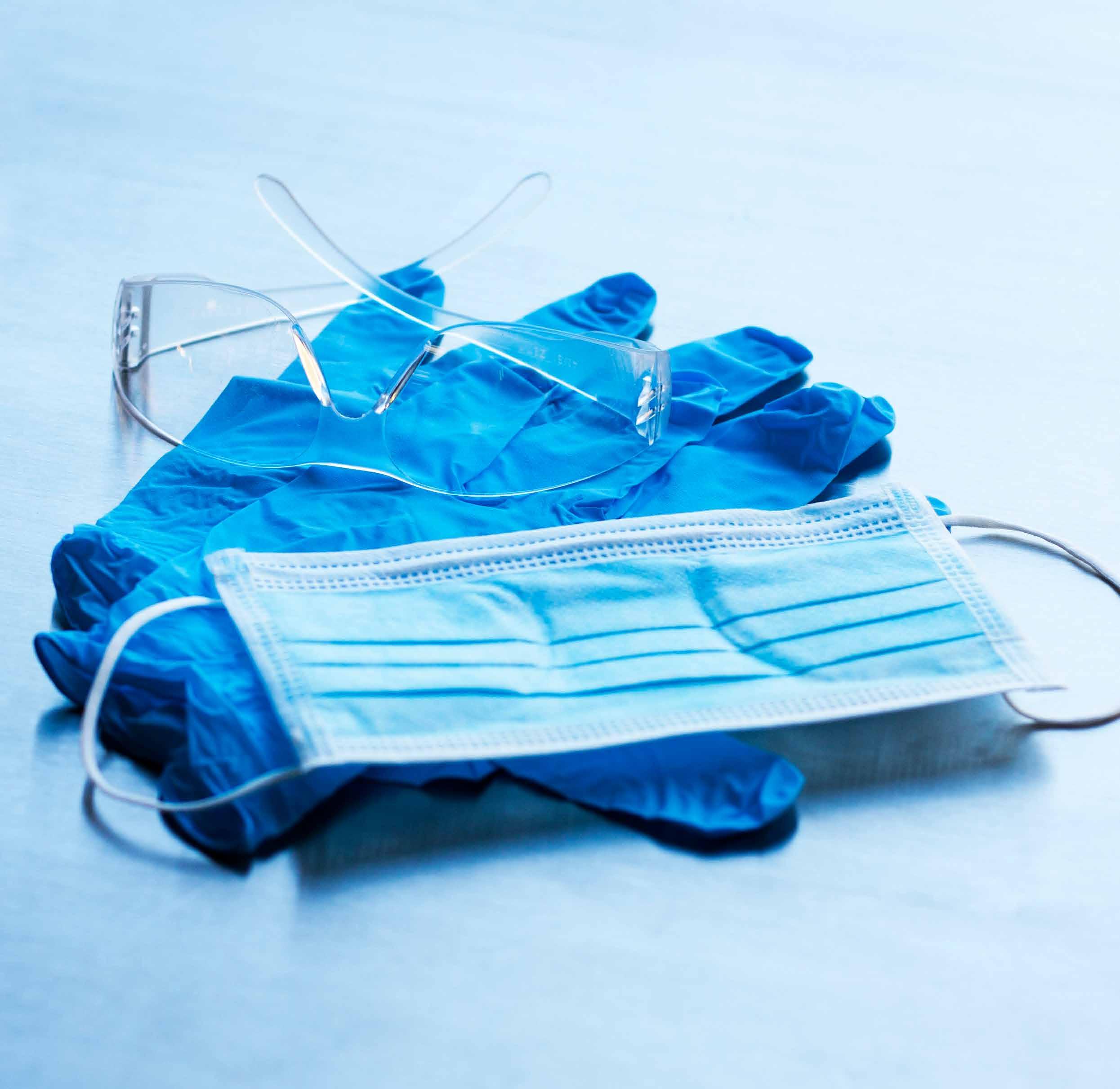
Author: Marcel Sieira is the Chief Customer Officer of GS1 Australia, a neutral, not-for-profit organisation that develops and maintains the most widely used global standards for efficient business communication.