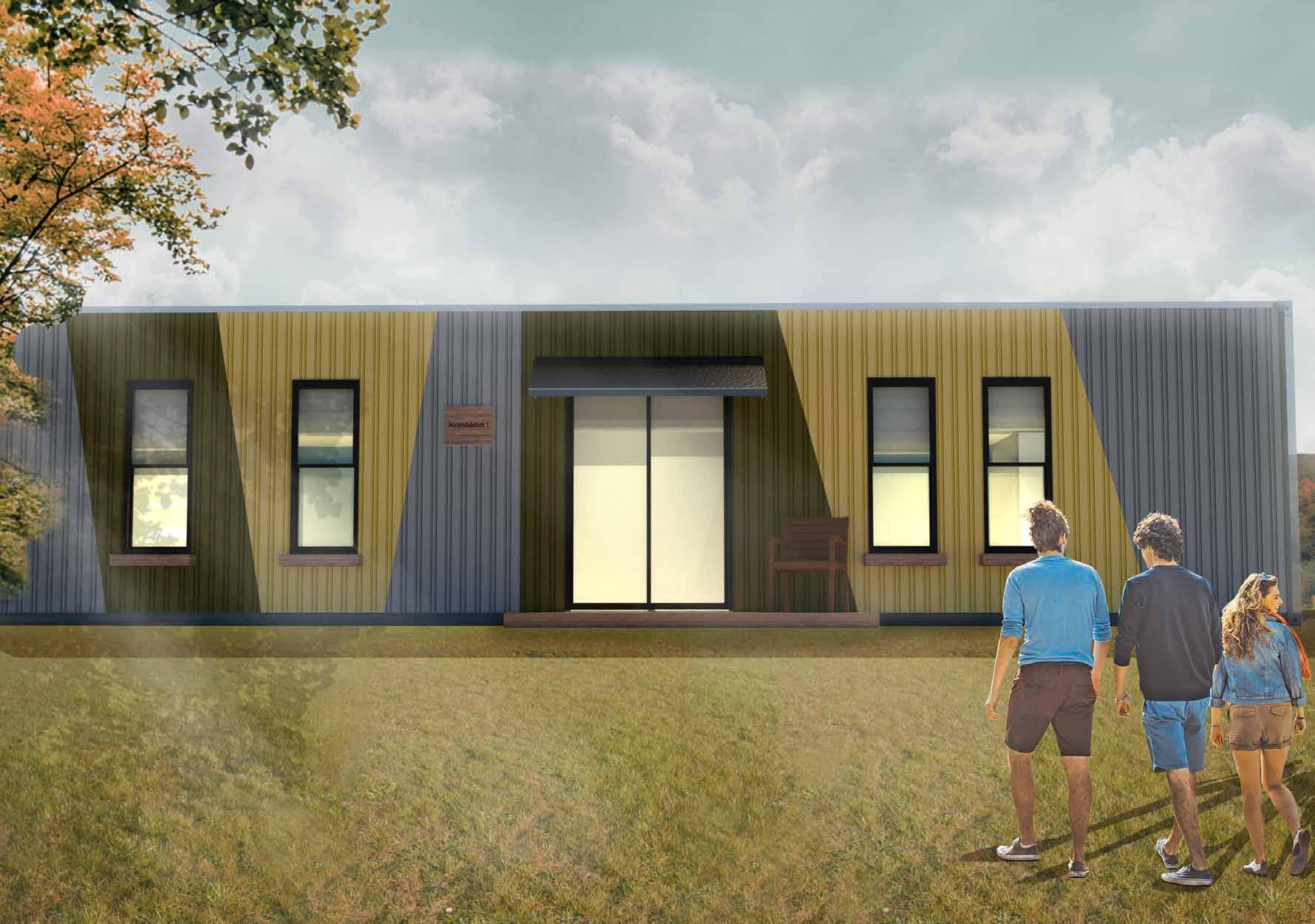
4 minute read
REBUILDING INFRASTRUCTURE THROUGH THE CIRCULAR ECONOMY
The development of shipping containers as a form of compact housing in multi-unit and single dwelling modules is a concept which is currently being investigated for application in Australia. The Circular Economy strategy demands the minimisation of waste, repurposing of existing assets and the avoidance of landfill and one such option as we look to the other side of the post pandemic crisis, is salvaging and repurposing shipping containers for use as offices, amenities and housing.
HAVE YOU EVER THOUGHT OF WORKING OR LIVING IN A SHIPPING CONTAINER?
I’m sure you’ll be thinking ‘steel’, ‘rigid and strong’; but I’m sure the words ‘embodied energy’ won’t spring to mind. Embodied energy means in a broader definition “….. the energy consumed by all of the processes associated with the production of a building, from the mining and processing of natural resources to manufacturing, transport and product delivery”.
In other words, and in the case of a shipping container, the term embodied energy means: the process of creating a shipping container requires a significant amount of energy to manufacture the steel shell.
Not only does the repurposing of containers build support for the Circular Economy by recycling an asset with high embodied energy, it also provides an employ ment value via the minimisation in disruption to property owners due to off-site fabrication.
It is a type of building practice, which is commonplace in Europe, whereby containers as dwelling modules are built off-site, mobilised and efficiently lifted into place.
The perception I’m sure we all have of a shipping container in its latter life, is a ‘rusted’, ‘dented’ hulk sitting on the docks or discarded in a paddock. This is often the destination for a container past its use by date as a viable asset on the open seas, either rusting in an industrial estate or dumped into land fill.
However, a shipping container has considerable viable life past its estimated 20-year service on the open seas. Research indicates a further design life of 50-years for a well maintained, repurposed shipping container build.
LOOKING TO THE OTHER SIDE OF THIS POST PANDEMIC CRISIS
The recent bush fire recovery program is an excellent opportunity for this type of building product to be introduced as a viable, cost effective and time efficient solution within the Australian landscape.
The world is now facing a new global challenge which is having wide reaching implications on our lives and the economy. The repurposing of shipping containers destined for the scrap heap, into comfortable, energy efficient workspaces and respectful accommodation solutions, is just one example which needs to be considered as a worthy response to rebuild confidence through the Circular Economy on the other side of this post pandemic crisis.
This was particularly demonstrated during the days and weeks post the 2011 earthquake in Christchurch, New Zealand. The government quickly deployed repurposed shipping containers as an immediate response for the re-creation of a shopping precinct within the centre of the city. The containers were brightly coloured, vibrant and workable spaces.
They fulfilled a critical role in the re-engagement of people whilst also providing a muchneeded retail, creative arts and community hub. Their use became a symbol of urban renewal and recovery and even more importantly they brought enjoyment back into the centre of the city.
THE ULTIMATE GIANT-SIZED LEGO BLOCK
Fixed dimensions, rigid, robust, few moving parts, water-tight and with a near perfect industrial quaintness, its egalitarian and industrial look is in fact the furthest thing from reality.
The process of container repurposing needs to satisfy building standard requirements to ensure they are weathertight, comfortable, and accessible whilst also meeting the requirements of the Building Code in terms of classification.
But we shouldn’t only think, although importantly, of just the requirements to achieve a building permit. We should also look at the amenity of a container.
Of course, colour is not the only method used to soften the industrial quaintness of the giant Lego building block. Repurposed containers can be delivered finished with wall frames and an internal lining. Pod roof structures are creatively packaged inside the container as a prefabricated kit to assemble after the container is positioned onto site.
Containers can be painted brightly, as per our Christchurch cousins, or alternatively they can be finished in a ‘drop down menu’ of cladding types, either with timber sourced from a sustainable growth plantation, or with panels of recycled timber sleepers. Even solid or patterned Corten steel panels can be carefully designed to be installed by invisible clips or screwed into place with copper spacing bars.
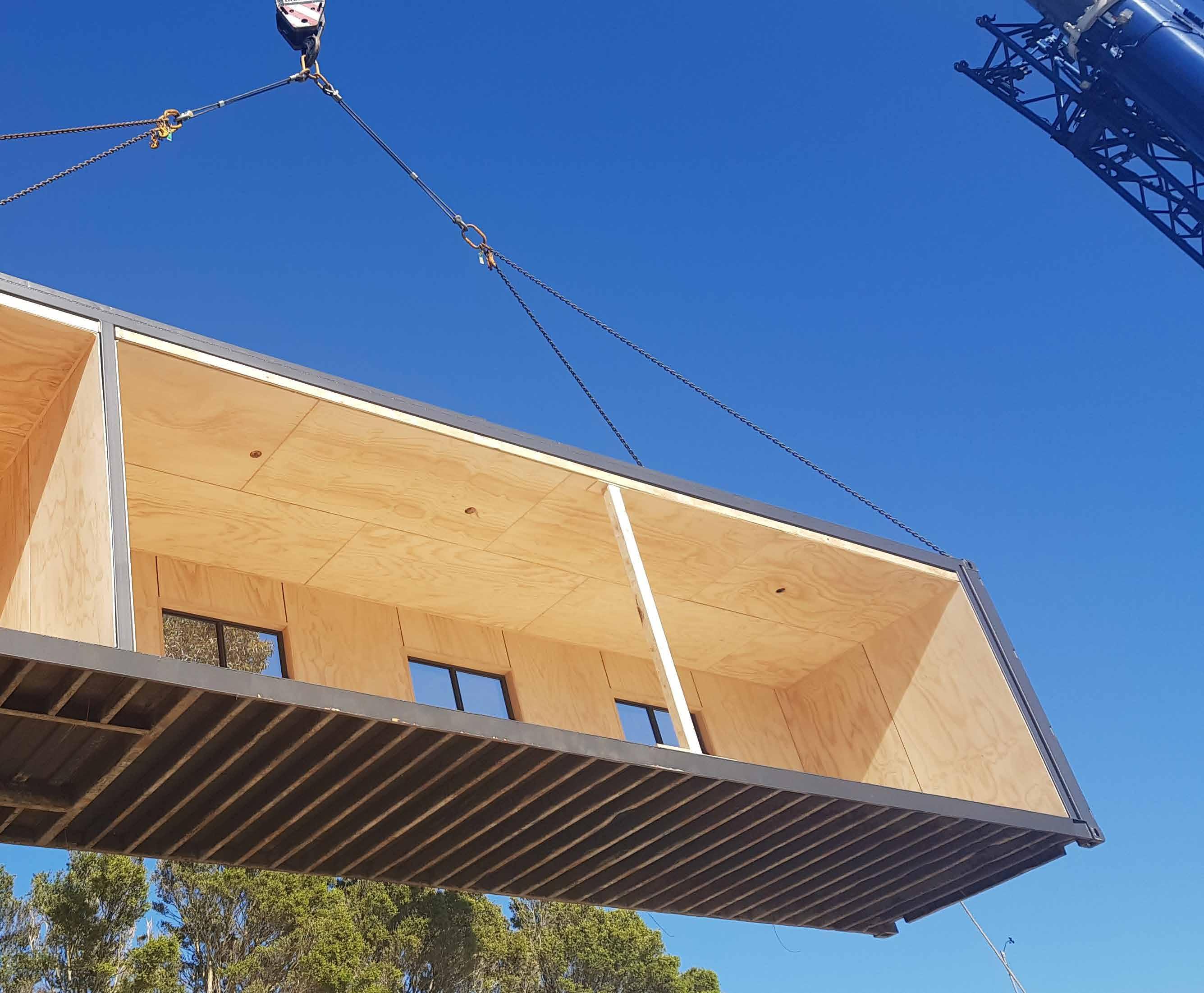
As we look towards the future and how we can build ourselves out of the COVID-19 period, thinking outside the box becomes all the more important – or should I say living inside the box.
Author: Gerard Coutts is a Certified Practicing Project Director and a Fellow of AIPM. Gerard has a long history in the delivery of sustainable built outcomes and is especially interested in the Circular Economy and the minimisation of waste and the process of recycling. His organisation is heavily involved in the repurposing of shipping containers for both industrial, recreation and residential uses.