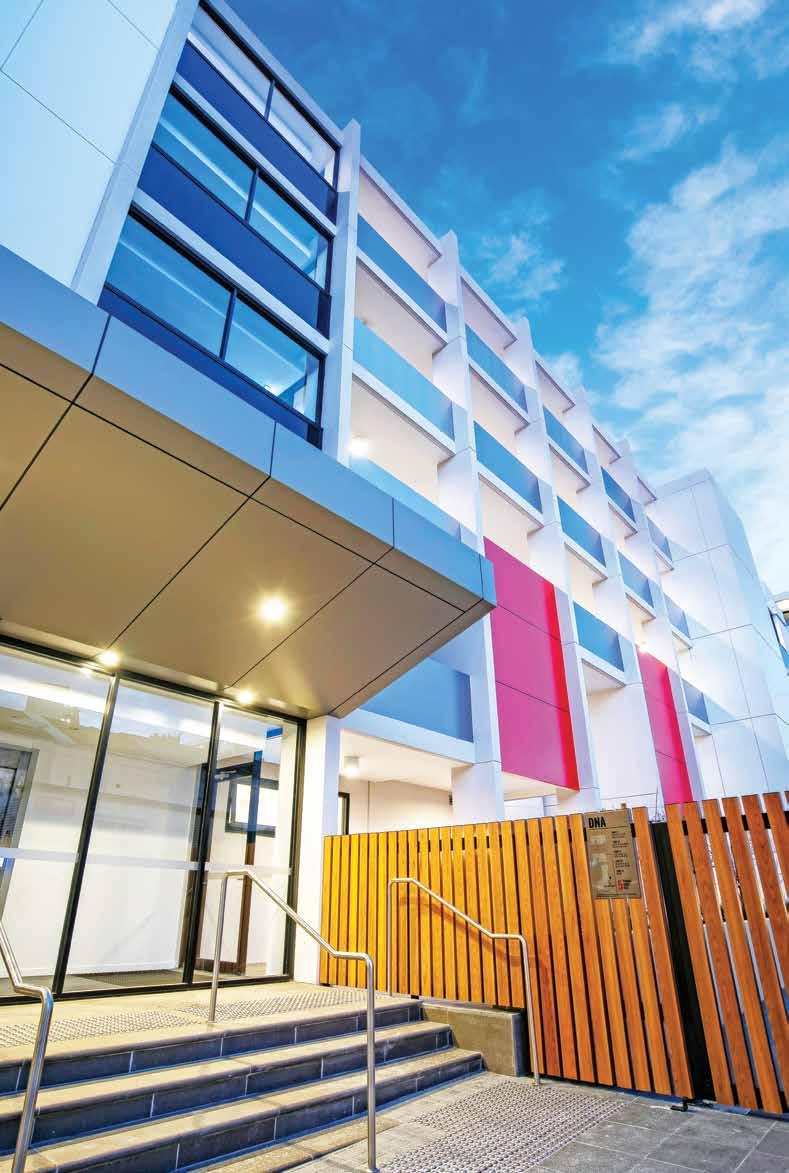
9 minute read
The Innovative and Cost-Efficient Way to Build
DINCEL THE INNOVATIVE AND COST-EFFICIENT WAY TO BUILD STRUCTURAL WALLS
Dincel Structural Walling, an Australian owned and manufactured permanent formwork system is different from traditional concrete formwork. It consists of lightweight PVC panels with a unique patented snap-lock joint for fast and easy installation, delivering a structurally sound wall when filled with concrete, that is also waterproof, fire resistant and acoustically rated. Efficient structural design is paramount in maximising the benefits associated with the use of Dincel Structural Walling. Columns can be inefficient elements as building loads are concentrated onto the column locations, resulting in increased requirements for slab thickness and steel reinforcement. Instead, multi-storey buildings should be designed with load bearing walls such as Dincel in mind. For example, typical intertenancy party walls, which consist of columns and lightweight ‘infill’ materials, could be replaced with Dincel load bearing walls in order to achieve the following benefits:
• Reduction in slab thicknesses: Slabs that were 200-250mm thick could be reduced to as thin as 150mm thick (or 175mm thick with a 25mm set down for wet areas). Transfer slab thicknesses can also be reduced by utilising Dincel walls on the level above as deep beams. • Reduction in slab steel reinforcement: Post tensioning (PT) or standard rebar can be substituted with mesh reinforcement which is economical and incredibly quick to lay. • Reduction in construction timeframes: Conventional multi-storey construction dictates that the floor cycle starts with vertical elements. The Dincel system allows floor formwork placement to take place on day one, which removes the vertical elements from the critical path and reduces the floor cycle time.
To achieve the above, it is important that architects ensure that in a multi-level apartment design, wet areas and party walls are placed on top of each other. This fundamental design requirement will result in the construction of the project being carried out in a more cost and time efficient manner. By using Dincel as your choice for load bearing walls, the following benefits can also be attained within the walls themselves: • Reduction or even elimination of wall reinforcing steel: This is possible through Dincel’s unique crack inducing technology as certified by the University of New South Wales (UNSW), which removes the need for crack control steel. • Reduction of Portland Cement content in concrete mix and water proofing membranes on Dincel walls: Dincel’s protective polymer skin allows for: • Enhanced wall durability and therefore enables the replacement of Portland Cement with materials such as fly ash, making for more environmentally friendly concrete mixes. • Ongoing hydration achieving denser concrete, which in turn can result in up to 50% less cement use.
• Reduction or elimination of waterproofing membranes on Dincel walls as Dincel’s PVC is water impermeable and its internationally patented snap lock technology has been tested and certified by CSIRO as waterproof up to 6m head of pressure at the joints.
DINCEL CASE STUDY ON COST AND TIME SAVINGS
Providing outstanding results for its customers is a key focus for Ceerose, one of Sydney’s leading property development and construction companies. Not only must all projects be completed to a high calibre, the builds also need to be delivered in a cost and time efficient manner, and the finish should be virtually maintenance-free.
In developing its cutting edge Ceerose apartments at Pyrmont Bridge Road, Camperdown, Ceerose partnered with Dincel to meet these objectives, while
achieving an extensive time saving on the projected build schedule. The project consisted of 133 units across three towers, each seven stories above the podium level with one level of basement car parking. The build used 200mm Dincel in the basement, lift, stair and service shafts and well as deep beams, blade columns and façade walls. In other areas, 110mm Dincel walls were used for party walls in between apartments supporting 170mm thick slabs.
The utilisation of Dincel as a loadbearing wall system in lieu of conventional methods achieved a cost-efficient floor system, together with a six-month time saving from the original construction program allowance of 12 months for structural work. Dincel’s use of PVC Polymer also yielded other important benefits for the project beyond time and cost savings. Other advantages provided by Dincel’s system was its suitability as basement, water tank walls and planter boxes without needing a waterproof membrane in areas other than the wall junction, as well as garbage and service rooms where mould and mildew is a common problem.
DINCEL’S COMPLIANCE TO NCC REGULATIONS MEANS PEACE OF MIND FOR YOU
Product performance claims and proof of compliance with the current National Construction Code of Australia go hand in hand.


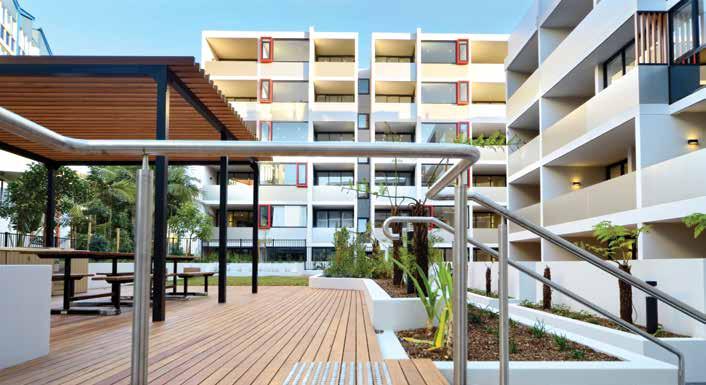
Dincel AS 5113/BS 8414 External Façade Test

Incidents such as the 2014 Lacrosse fire in Melbourne, the 2017 Grenfell Tower fire in London, and the 2019 Neo building fire also in Melbourne should serve as reminders of what complacency when it comes to compliance, can lead to. The priority for Australian State Governments has been to identify and now remove non-compliant products. However, as an Industry our priority from this point on is to ensure that the problem does not become worse. This means that every effort must be made to prevent the installation of more non-compliant products on new or renovated buildings. Changes to our National Construction Code now offer a clear path of compliance for composite wall systems including permanent formwork systems such as Dincel. Many internal walls and external façade walls comprising of composite systems with linings must meet test requirements to AS 5736.1/ISO 9705 and/ or AS 5113/BS 8414, which are full-scale tests to demonstrate fire compliance.
Dincel is one product that has been tested and certified to be compliant with the new NCC regulations for use in both internal walls (Deemed to Satisfy) and external walls (Deemed complaint as a performance solution). Tests have been independently performed by Warringtonfire to ISO 9705 and AS 5113/BS 8414 as required by the NCC and reports then assessed by Omnii Consulting Fire Engineers. Another three sets of full system tests were also carried out on the Dincel system via CSIRO and Warringtonfire to determine fire resistance levels (FRL) including:

• AS 1530.4 – Result: FRL between 90/90/90 and 240/240/240 depending on profile thickness • AS 1534.4 Penetration tests – Result: no need to cut away Dincel at penetrations joint • AS 1530.4 joints test (for when Dincel abuts to a different wall system) – Result: no need to cut away Dincel at wall joints.
Proof of compliance for waterproof applications is also important, particularly given the significant rise in building defects as a result of water ingress due to waterproofing failures as indicated by Dr Nicole Johnson and Associate Professor Sascha Reid in their June 2019 Report “An Examination of Building Defects in Residential Multi-owned Properties”. Dincel’s waterproofing capabilities have been tested and certified by CSIRO as meeting waterproofing requirements as per AS 3740 as well as ASTM E 514- 08, AS/NZS 4347.1:1995 and ASTM E 96/M 96M-05, without the need for waterproofing membranes. It is important to note that test standards prescribed by the NCC put the responsibility on designers, specifiers, engineers, builders and certifiers to ensure that a compliant product is used. Likewise, this responsibility also extends to building product manufacturers and suppliers to ensure they carry the full suite of the latest tests as required by Australia’s Building Code regulations. Only then, will the building industry avoid the issues of non-compliant products getting worse.
DINCEL’S UNIQUE POLYMER FORMULATION AND DESIGN
Dincel’s high performance hinges on its proprietary formula and patented panel design. Unlike other permanent formwork systems currently in the market, Dincel is made from a unique PVC formulation specifically created to address sustainability and health issues associated with the use of PVC raw materials. All Dincel PVC panels and accessories are BEP (Best Environmental Practice) certified, contain no phthalates and use stabilisers that are free from heavy metals. The product was also formulated with fire performance in mind, specifically, its special formula intumesces (swells and locks itself in place) in the event of a fire as opposed to melting. Tests indicate that the amount of smoke generated during a full systems AS ISO 9705 test is 7 times below the maximum allowable in our National Construction Code (SMOGRA 14), and when tested to AS 5113/BS 8414 the amount of debris generated that was PVC based ash amounted to less than 500 grams at the completion of the test with the remaining being concrete (typically the same amount you would get from a normal concrete wall). Important to note is also Dincel’s waterproofing performance. Dincel permanent formwork panels rely on both its formulation and panel design. When Dincel is filled with ready mix concrete with a minimum concrete slump of 200mm, the heat generated during
Dincel AS ISO 9705 Full Room Test
the concrete curing, the aggregate size within the concrete mix and the concrete strength generated within the formwork skin forces the joint between the panels to snap lock together in such a way that it creates a waterproof joint up to 6m head of pressure as certified by CSIRO. Dincel performance when it comes to compliance and the unique value proposition it derives from its proprietary formula and patented design needs to be kept top of mind by specifiers, builders and certifiers when it comes to substitution. Equivalence to Dincel just like any other building product in the market, can only be proven if certificates or reports can be produced to attest to it.
Swimming pool built with Dincel in Bungan Head by Waterview Constructions This is a paid advertorial. All words and photos have been supplied by Dincel Structural Walling.


NZIQS2020 CONFERENCE
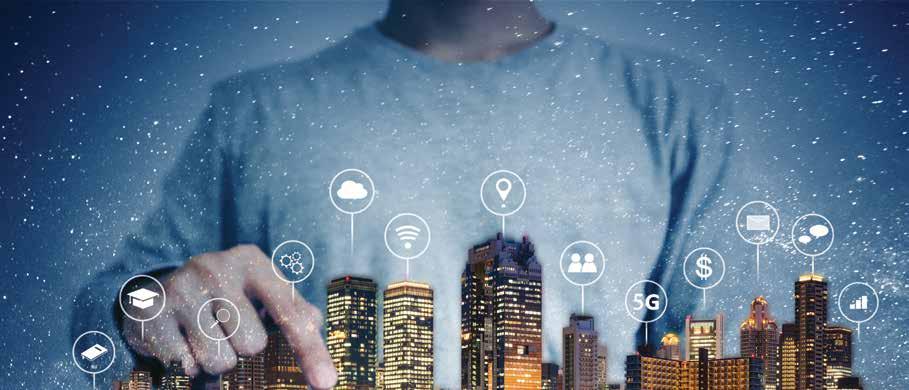
Rethinking Construction; Creating a fairer and sustainable future
• 24 – 27 June 2020 • Grand Millennium • Auckland
A sneak peek at our speaker line up
Sir Graham Henry former All Blacks Coach
One of the most successful rugby coaches of all time Sir Graham is famous for his changes he made in the All Black culture with their new mantras that included: Sweep the Sheds, Play with Purpose and the No Dickheads.
Proudly sponsored by NZ Strong
Nigel Latta renowed psychologist and TV personality
One of Nigel’s favourite sayings is “Just because the issues are complex doesn’t mean the solutions have to be”. With his fresh, no nonsense approach Nigel will take a pragmatic, thought provoking and humorous look at some modern day issues. Proudly sponsored by CMP Construction
Lisa King founder of Eat My Lunch
Lisa believes having a social purpose is no longer an emerging trend, it is becoming a requirement for every business. That social enterprise will soon become part of the norm and mainstream economy. Lisa’s mission to see no child goes to school hungry has seen her company give away over 1.4 million lunches to kiwi kids.
Proudly sponsored by Winstone Wallboards
The programme also includes • QS Funder Panel • Creating Value through Procurement • BDO 2020 Construction Survey Report • Supply Chain Panel • Plus lots of networking and social activities including a Partners Programme, Mountain Biking, Optional Dinners and more!