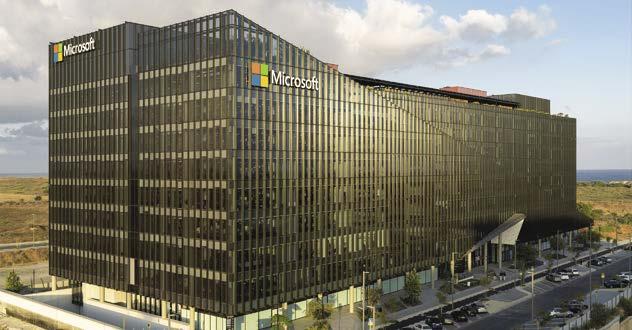
31 minute read
Global Update
by AIRAH
ISRAEL
H2O FROM AC
Advertisement
Microsoft is using the waste condensate from air conditioners at its Herzliya, Israel office to irrigate the landscaping at the corporate campus and to help cool the 46,000m2 building.
The tech titan uses similar systems in its offices in Twycross in the UK, and Hyderabad, India. “We are also considering its inclusion in other Microsoft buildings depending on HVAC design, regional climates and other factors,” says Microsoft senior sustainability program manager Katie Ross. The innovation saves the Herzliya office three million litres of water – enough to meet the annual water needs of several families.
At the moment, air conditioner condensate reuse systems don’t scale efficiently to use in most homes and other small spaces. Yet such systems may prove in the near future to be a useful tool to help make buildings more efficient in terms of water use.
The UN has suggested that water is the “primary medium” through which we will feel the effects of climate change. ■
USA
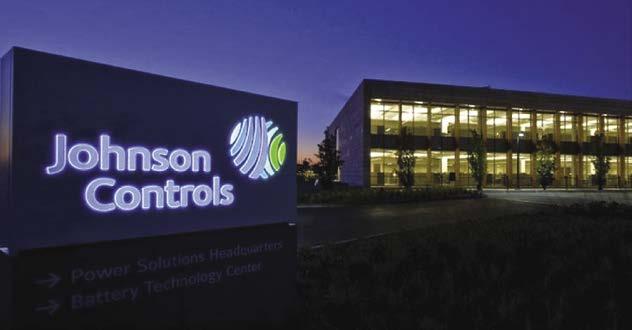
PLAN B
Johnson Controls has opted to use R454B to replace R410A in its ducted residential and commercial unitary products. The low-GWP R454B will also be used in air-cooled scroll chillers.
Johnson Controls evaluated several low-GWP alternatives on a variety of performance and market metrics, such as safety, capacity, efficiency, reliability, availability and longevity.
This decision was made as the US industry prepares to phase out high-GWP refrigerants under the recently passed American Innovation and Manufacturing (AIM) Act.
“Utilising R454B was a clear decision, but one that took years of in-depth research, testing and evaluation,” says Johnson Controls’ Chris Forth. “This decision maximises environmental benefits, which will help to avoid, if not completely avert, a second, near-term transition for the unitary sector. As the AIM Act phase-down schedule progresses, higher-GWP fluids such as R32, while viable today, have the potential to be eliminated as an option due to their high GWP values.” ■
CHINA
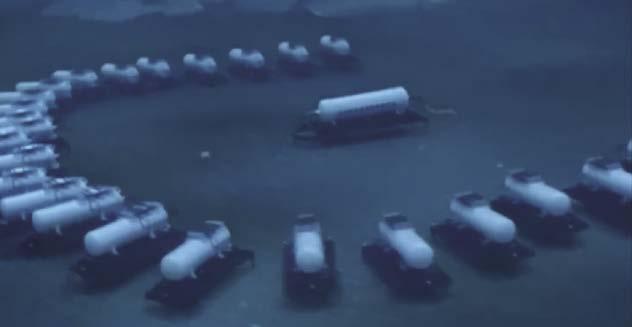
UNDERWATER DATA
The massive free-trade port of Hainan in China is planning to launch a commercial undersea data centre, based on a prototype tested earlier this year. The facility will operate in 100 airtight pressure vessels on the seabed near the Changjiang nuclear power station.
The project aims to install racks of data centre equipment in pressure vessels, which will be sunk to the seabed at offshore locations. The tiny data centres will be operated through a combined power and internet cable, and cooled by the surrounding seawater. Microsoft tested and successfully ran a 12-rack data centre off the coast of Scotland for two years, but has no plans to commercialise the technology.
By placing data centres underwater, the idea is that they can be kept cool without using as much energy as traditional above-ground data centres. And if low-carbon energy from the local Changjiang nuclear power station is used, the project could be carbon-neutral. ■
UK
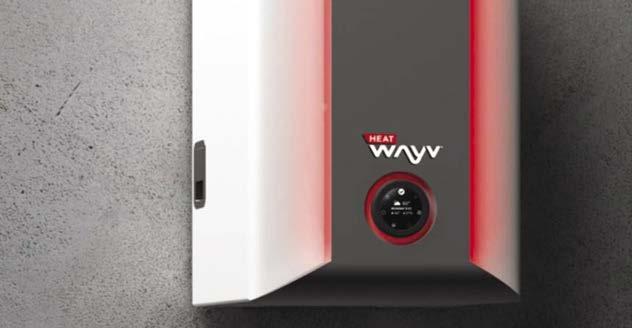
BIG PROMISE FOR MICROWAVE?
UK energy technology company Heat Wayv has unveiled the world’s first microwave boiler intended as a zero-emissions replacement for gas boilers. Originally developed as a portable cooking device for the military, the technology has now been applied to heating.
Set to be trialled in 2022, the new boiler is said to offer a range of benefits such as zero emissions, plug-and-play installation and silent operation.
“The end of the [natural] gas boiler is inevitable and scheduled,” says company founder Phil Stevens. “But the proposed replacement technologies do not work for consumers, as they are either too expensive to install or too expensive to run. We looked for a clean technology where the boiler would cost the consumer the same to buy, same to install and same to run as a gas boiler.”
iQC & NiQ – energy saving motors
a new look to efficiency.
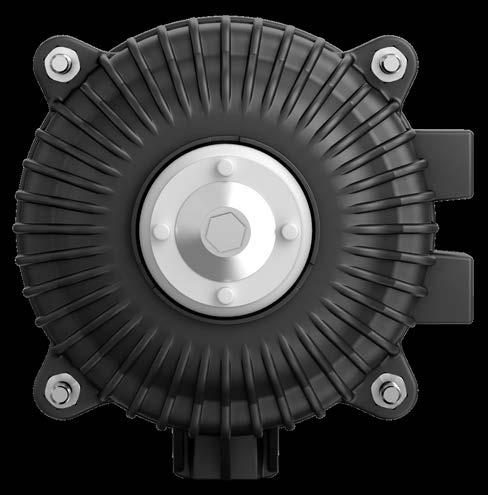
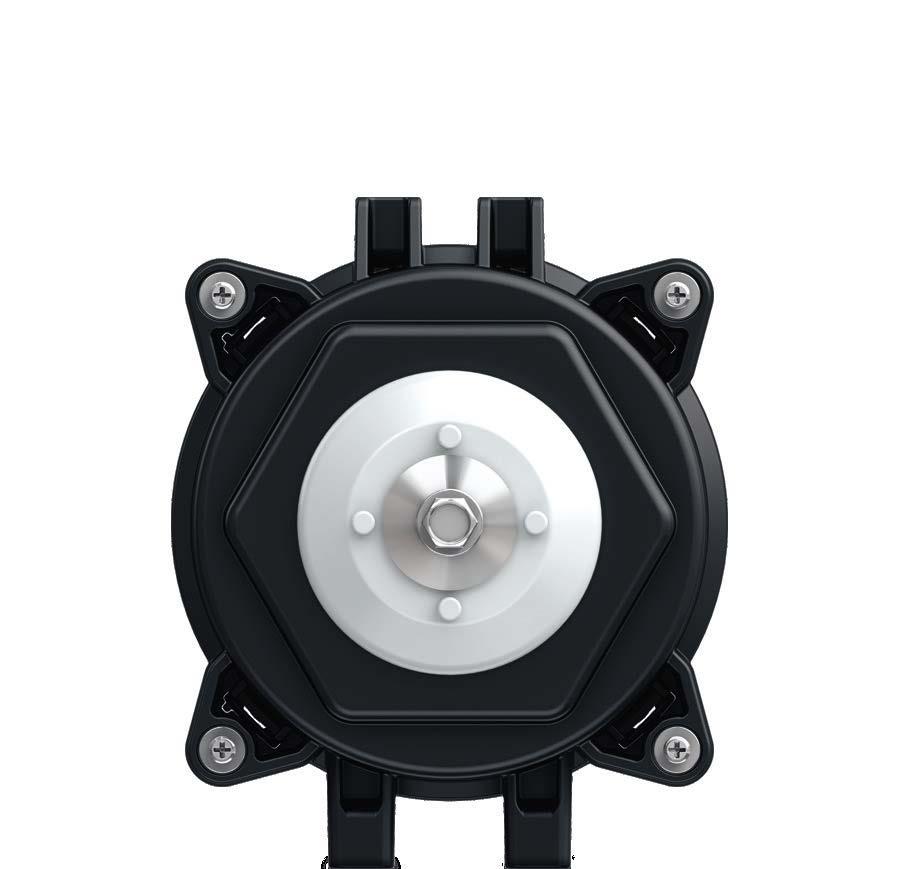
ebm-papst pioneered energy savings in refrigerating systems with the release of its iQ series motor over 10 years ago. With proven application in harsh conditions all over the world in both new and replacement installations, the iQC and NiQ now improve on the tried and tested iQ series motors. The iQC and NiQ have enhanced the existing advantages by reducing environmental costs.
Benefits reliable and durable.
Designed to achieve high performance in a wide range of tough environments, the iQC and NiQ are able to handle wet and dusty applications. The high efficiency of the motor means that less waste heat is generated, resulting in improved refrigeration performance and longer service life than typical shaded pole equivalents in cold side applications.
Benefits of upgrading.
As with all ebm-papst motors in the iQ range, the iQC and NiQ are a direct one-to-one replacement for existing Q and shaded pole motors. With huge cost savings when compared to outdated AC technology and ease of replacement, the iQC and NiQ are the smart choice for retrofitting existing applications.
Benefits cost effective.
Higher operating efficiency means reduced power input, resulting in lower operating costs and longer life time. As both the iQC and NiQ motor replace a range of shaded pole motors, this means having the right product for the application on hand when you need.
UNLOCKING BETTER BUILDINGS
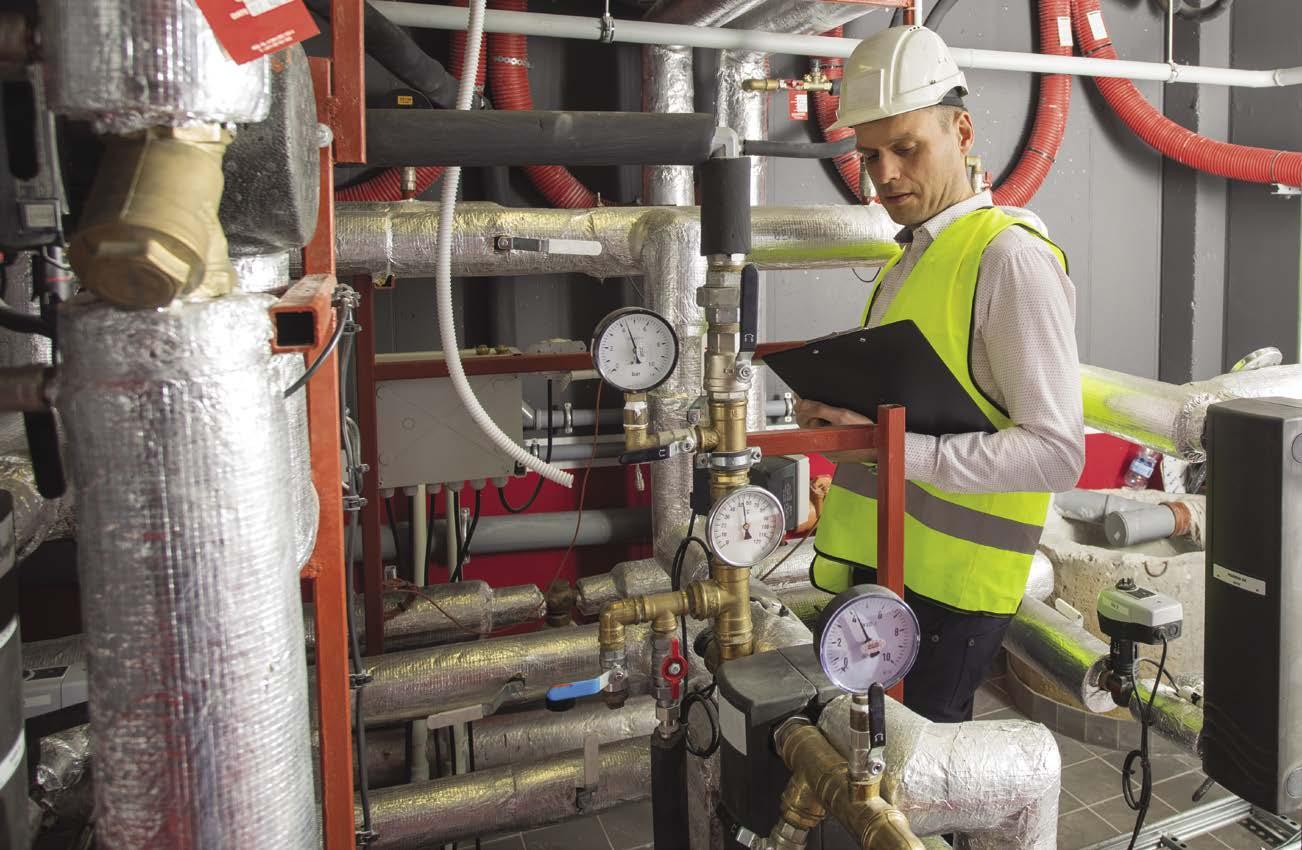
According to a landmark Australian survey, HVAC&R technicians hold the key to more efficient, sustainable and comfortable workplaces. Willow Aliento reports.
The majority of Australians who work in an office do not work in a premium-grade CBD commercial tower. Instead, they work in older, smaller and poorer quality buildings, which represent about 80 per cent of Australia’s commercial building stock. These buildings are known as the mid-tier.
It’s a sector we don’t know much about. Although NABERS ratings, Property Council of Australia data and other sources have a lot of information about the top end of town, there has been a real lack of insight into the mid-tier and how these buildings are performing.
A multi-disciplinary team from the University of Wollongong and commissioned by the federal Department of Industry, Science, Energy and Resources has been trying to fill this gap. They have conducted research into the sector by surveying the people who are closest to the action when it comes to building systems – the HVAC&R technicians. The project is called Better Ways to Work. Understanding and improving energy performance involves both technical and human factors. Accordingly, the UOW team brought together engineers and social scientists from its own Sustainable Buildings Research Centre and Australian Centre for Culture, Environment, Society and Space.
Researcher Dr Daniel Daly says that because the ownership of buildings in the mid-tier is quite fragmented, and it is a known challenge to engage owners in this sector, the research team decided speaking with the contractors, tradespeople and facilities managers was the best way to gather data.
WHAT IS THE MID‑TIER AND WHY DOES IT MATTER?
The mid-tier comprises about 50 per cent of all office space in Australia, and about 80 per cent of commercial buildings, according to Bruce Precious, M.AIRAH, property sector expert and principal consultant at Six Capitals Consulting.
It ranges from the small commercial office block in Dubbo to the outer suburbs accountant’s office building, the bank building in Bunbury, an administration block attached to a manufacturing facility, or a hospital’s administration building.
Precious noted at an AIRAH webinar launching the research, “Opportunities to Create Value through HVAC Maintenance”, that the mid-tier is characterised by older plant and equipment. This can mean the HVAC systems are using phased-out refrigerants, and they generally have less integration of sensors or automation. On top of this, they often lack an onsite facilities manager.
UOW researcher Dr Chantel Carr, co-leader of the Better Ways To Work research, says the complexity of the sector extends to building ownership. While premium buildings are often owned by a major fund as part of a portfolio, a mid-tier building may be owned by single offshore investor, a small self-managed super fund, or a local professional like a lawyer or doctor. The business case for these small investors in terms of what motivates them to want to improve their building and its performance is different to the premium office market, where NABERS ratings and competition for tenants drive momentum for improvement.
Precious says that often in the mid-tier, expenditure on building maintenance is managed from a “zero baseline”. “That means there is no budget for routine maintenance, and no budget for breakdown maintenance,” he says, “and that presents its own problems.”
Carr says that most contractors have a very good sense of the business case for proactive maintenance, but it can be hard to get this point across. “Contractors reported lack of budget and interest from owners as the biggest barriers to better maintenance, and FMs reported low levels of capex discretion,” says Carr. “So owners in this market are clearly sensitive to costs, and don’t think a lot about their HVAC systems until something goes wrong. “We’ve known this anecdotally for some time, but being able to put some numbers behind it [from the survey] really helps us to get these issues onto the policy radar.” Daly says another key barrier that often comes up in the researcher team’s interviews is difficulty in getting in front of the owner to explain the benefits of an alternative approach – particularly when the owner is a trust or international investor.
These barriers mean that maintenance or replacement takes a “like for like” approach rather than aiming for betterment.
“The point of upgrade or replacement is really key to installing more efficient systems, because decisions are being made that have life-cycle ramifications of 20–30 years,” says Carr. “And these decisions are often being made under time pressure where a system has completely broken down and tenants are complaining.
“We know that technology improvements mean new kit is likely to perform much better than an old ‘heritage’ system that’s limped along and been patched up over the years, but one of the big issues contractors raised is that even like-for-like is often not available due to model changes.
“We’re going to spend a bit more time digging into point of upgrade decisions, and lots of survey respondents indicated they’re keen to help us with that, which is terrific.”
FMS DON’T KNOW WHAT THEY DON’T KNOW
Business development manager for Airmaster, Pat McManus, also spoke about the mid-tier issues at the “Opportunities to Create Value” webinar. He flagged a crucial issue around lack of knowledge on the part of FMs and building operators around the testing regimes required to ensure fire and smoke control protection systems are functional.
In many cases, he said, these were made part of the HVAC system design in the original building. But many older buildings have been renovated or reconfigured to reflect changes in tenancy or occupancy, and this can impact the performance of the fire and smoke protection systems. Without an understanding of the original specifications or access to the original building documentation, the FMs are not well positioned to understand the testing and maintenance required.
According to Ellis Air Senior Contracts Manager, Gary Ward, M.AIRAH, FMs in mid-tier buildings generally don’t have the knowledge to look after the building correctly. Many are ex-tradies, he explained, and they know their own trade extremely well. “But there’s a massive amount of components in a building that it needs to function properly,” he says.
Ward believes the knowledge needs to be “channelled up” from the trade experts to the FM and then upwards to the building owner. This must occur across the board.
“It’s all about the awareness,” he says, “good reaching out and getting the FMs aware, making the building operators aware.”
There are multiple benefits to be gained from improving the mid-tier, Precious says. It not only offers environmental benefits in terms of reduced energyrelated emissions, but also has the opportunity to deliver economic benefits and broader community benefits. “There is an opportunity to make them safer buildings not only for the people who work in those buildings but equally, safer for the technicians and service personnel that visit those buildings and make their away around to the plant rooms. They’re safer through having guards on equipment, safer by eliminating confined spaces, safer by ensuring switchboards are kept locked. “There are a whole range of ways that buildings can be made safer. They can be made more comfortable and more productive by ensuring the air conditioning is performing effectively and allowing people to get on with their work.”
Precious says the task is to divert the money currently being wasted on problems like excessive energy use into the maintenance function.
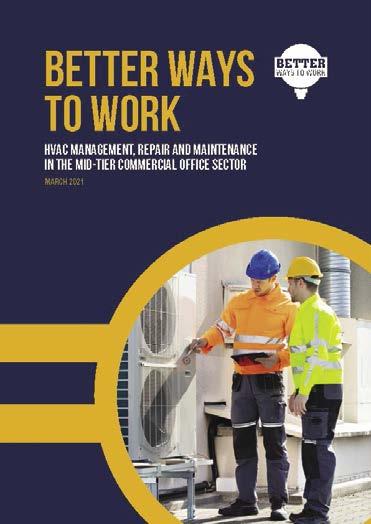
www.regulatorautomation.com.au
HVAC Control, Made Beautiful Intelligent Connected
Meet the newest member of the ECLYPSE Series: the ECLYPSE Connected Thermostat!
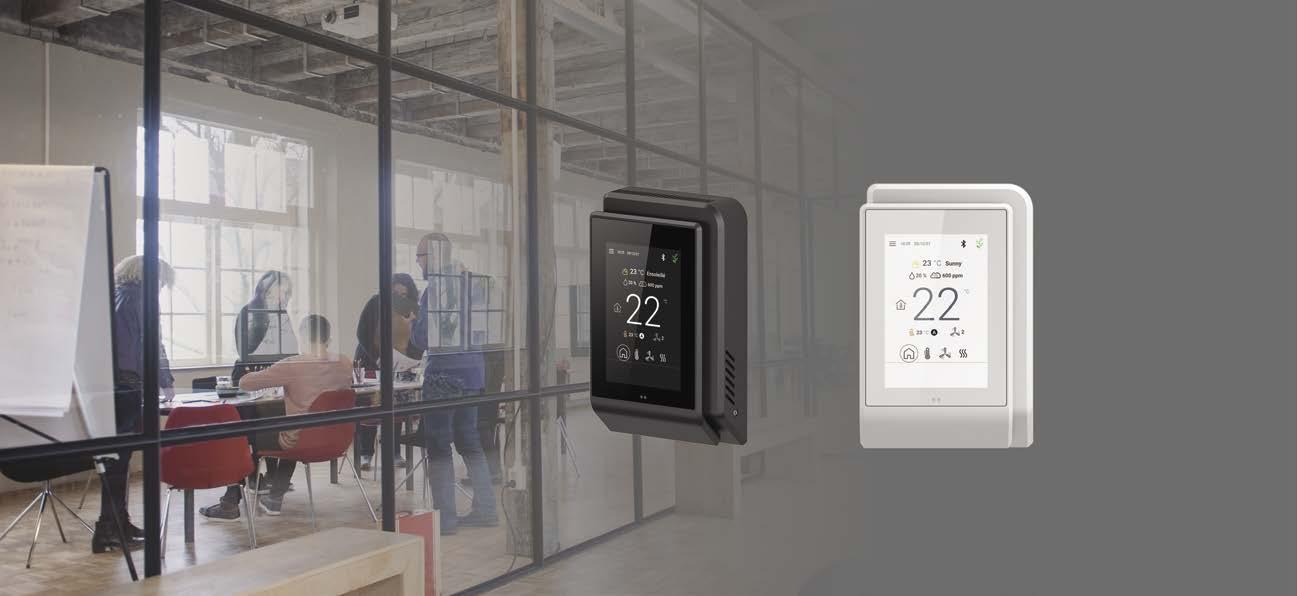
For all your HVAC product, design, installation and servicing needs: Call (02) 9804 6366 or visit www.regulatorautomation.com.au
POWER TO THE TECHNICIANS
The Better Ways To Work research found that the HVAC contractors and trades do hold a significant amount of power to effect change, because of their depth of knowledge.
Some quick facts from the research: • HVAC is the largest end use of energy in commercial buildings – when it works more efficiently, energy bills go down. • The majority of contractors in commercial building HVAC are small and medium enterprises, and the average contractor or tradesperson has more than 11 years of experience in the sector.
Most also hold trade qualifications. • Close to half (42.7 per cent) of all mid-tier buildings survey respondents work on have the original HVAC system in place, with no significant upgrades carried out since installation. • Central plant is only slightly more common than a mix of central and split systems, and many buildings have only split systems, indicating that splits may be
“patching up” under-performing systems. • Cost is a deciding factor when it comes to upgrade and maintenance – but while contractors focus on up-front cost, the majority of facilities managers reported being more concerned about life-cycle cost. • The majority (81 per cent) of maintenance or repair callouts are initiated due to tenants’ reports that the system is not providing the level of heating/cooling required, or that it has broken down. • Contractors rely on their own experience, their peers and industry associations for knowledge and ongoing learning – FMs rely on the contractors to provide information.
The opportunity for contractors is to educate FMs and building managers about the benefits of improving systems, according to the researchers.
“There is a lot of expertise in the sector, but [HVAC&R contractors] can be their own worst enemy with a lowest cost approach,” UOW’s Dr Carr says.
She says contractors should see what they do as providing a service that includes building manager and tenant education, maintenance and providing comfortable buildings.
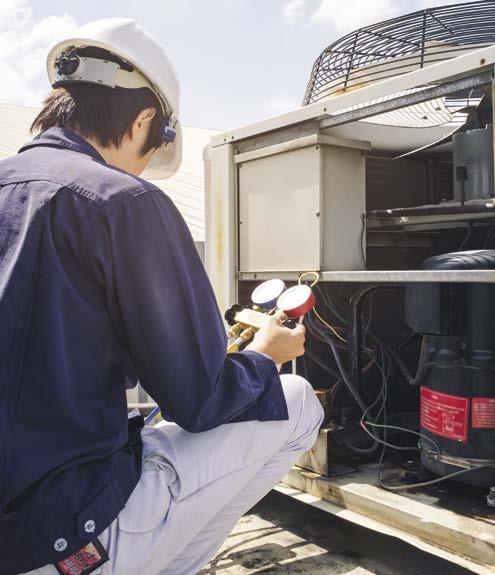
“Tradies are at the centre of this question,” she says. “And contractors are really important in regional locations.”
Dr Daly from UOW says that at the start of the research the team was aware that a lot of contractors and FMs knew what they should be doing to improve buildings, and many also knew what they wanted to be doing to their buildings. But it is the technicians who go onsite who “know what good maintenance looks like, and what a good job looks like”. “We did ask (survey) respondents to tell us about a time where they had been able to do better than like-for-like replacement,” says Daly. “The most common reason to improve a system was that the existing system was obsolete and therefore an alternative solution was required.
“However, the second most common reason, and the most common reason for the FMs we surveyed, was that the life-cycle cost was more favourable for an upgraded system.
“This suggests that contractors have an important role to play in communicating the full life-cycle costs and benefits of different strategies, and that FMs and owners are receptive to this information. Other common reasons given were contextual factors, such as HFC refrigerant phase-down, or changes to the building’s use over time.”
EXPERIENCE PLUS KNOWLEDGE IS A SUPERPOWER
The Better Ways To Work survey recorded more than 1,500 survey responses across all parts of Australia.
Carr says the human capital of experience-based knowledge is often under-rated.
“There is a lot of knowledge in trades, we can forget that,” she says, “especially when it comes to HVAC. It is an electromechanical system – it is right up there as far as complexity goes.” She says that having a sector with such a wealth of knowledge and experience is an asset, and the task now is to equip contractors to better communicate the benefits of improved maintenance that increases efficiency to owners and tenants.
As she points out, it is the tenants who bear the cost of poorly maintained, under-performing systems, both in loss of comfort and in their energy bills.
“The key is really getting that message out there that preventative maintenance is a better value proposition in the long term.”
The federal government is looking at resources it could develop to help with this, Carr says. This could also involve some form of training for contractors around communicating the benefits of improvements to owners and FMs. She notes that ideally, this kind of training would fit with existing workloads and commitments and build on the kind of information-sharing that already happens within the industry.
“We want it to work in with the ways people are already doing things, not work against it.” Another aspect to the lengthy experience of many survey respondents is it raises an issue around ensuring knowledge is passed on to the incoming generation of tradies.
“The survey highlighted that there are some concerns around an ageing workforce in the HVAC sector, which has implications for bringing people into the trade and how contractors keep up with their professional development,” Carr says.
“This is really important as we begin to see a positive shift in looking at energy efficiency. “The demand for comfortable buildings isn’t going anywhere, and there is potential for HVAC contractors to become seen as an expert workforce, but this can only happen if we keep building the industry’s skillsets. “We’re currently working on a project in the training and skills space to look at what’s needed here, and the experience of organisations like AIRAH and FMA are key to this work.”
WHAT HAPPENS NEXT?
Daly says one of the research team’s biggest takeaways was that contractors in HVAC are “really engaged.”
“They are keen to have their voices heard. The survey got a fantastic response rate, which shows a lot of engagement and a lot of interest in doing things better.”
The research team now is continuing to look at how to equip the HVAC sector to help improve mid-tier building performance.
“We’re now working on three projects where we’re spending a bit more time with those respondents who said they were available to talk in more detail about the issues they see and what options are on the table for doing things better,” Carr says. “One of those is looking at key points in the procurement process, like the point of upgrade. A second project is looking at how the findings might translate across other building types like aged care and the retail sector. A final project is looking at training and skills, and how we can work with the way the industry is structured to understand how to best target upskilling.
“So, the project is still very much active, and we’ll be looking to keep these conversations going, keep shining the light on the plant room for a while yet. We’ll be publishing our findings along the way on the Better Ways to Work website.” ■
CHECK OUT THE SURVEY RESULTS
UOW has created a detailed report and also an interactive dashboard with information about the roles of those working on HVAC&R systems, where they work, maintenance routines, and barriers to better maintenance. It’s a treasure trove of information.
PROUDLY SPONSORED BY
AIRAH Skills summary
■ What?
A guide to inverters in modern air conditioning units and some common problems you may encounter in the field. ■ Who?
Relevant for HVAC&R technicians and anyone involved in installing, commissioning, and maintaining air conditioning equipment.
INVERTER
DIAGNOSTICS AND TESTING – PART 1
One of the most common ways to modulate the cooling capacity in air conditioning systems is via inverter technology. An inverter controls the speed of the compressor to change the refrigerant flow rate. The turndown ratio depends on the system configuration and manufacturer. Inverter technology is commonplace in today’s air conditioning systems, from commercial units through to residential split systems. Often, issues with the inverter will cause the system to stop working. This Skills Workshop looks at common causes for these issues and describes how to fix them.
Background
The world has changed very quickly in a short period of time with air conditioning. There have been several factors governing this rapid change: • A doubling of air conditioning sales from 2000 and continuing steady growth • Increasing energy demand and the subsequent increase in carbon emissions • A mandate for energy efficiency in household appliances with the original minimum energy performance standards (MEPS), and greenhouse and energy minimum standards GEMS, which came into effect in 2012 • Refrigerant phase-out, phase-down and replacement as per the
Montreal Protocol, which has had various amendments since 1989, bringing some phase-out dates forward • Customer needs and keeping up with technology, such as home wi-fi and internet-based control, plus indoor air quality enhancements made with unit design.
The average technician now has more demand placed on them to manage and work effectively with these new technologies that are commonplace in domestic and commercial systems. The evolution of air conditioning design has seen some very good old and tested designs disappear forever. Just like those old Kelvinator round shoulder refrigerators, some older design air conditioners are still in service today. Although the manufacturer got it right with those types, they could not evolve using those older designs. Original design split system air conditioners (high-wall types) presented technicians with rudimentary simple logic and control interface. Inverters were not in use then. There were three very common types: 1. Simple direct-switched (240V AC control) with five-wire interconnect and contactor-started permanent split capacitor (PSC) motor. The five wires comprised active, neutral (earth), compressor start, reversing valve signal, and outdoor fan control for heating mode governed by the indoor unit. 2. Direct-switched (240V AC control) cooling only with three-wire interconnect. Yes, you guessed it – only need on signal wire for the compressor. These also used contactor-started PSC motors and a current transformer (CT) in line with the contactor coil. This would create a fault call if it did not detect coil current. They were very simple but easy to work on and diagnose. 3. The model everyone liked. This generation saw the introduction of the three-wire interconnect in which direct AC switching was replaced by communication and each indoor and outdoor has a PCB. The contactor and reversing valve power, fan motors came from the interface connections off the PCBs with very simple protections such as a motor overload, thermistor control and, in some models, a dedicated high- and/or low-pressure switch. The indoor fan was a phase control AC motor type, which was the first real variable speed used and not requiring speed tap windings. Unfortunately, these designs ran constant speed compressors and used a simple on/off logic for temperature control. The result of this design saw efficiency at only one peak condition. Constant stop/start of the compressor added mechanical and electrical wear, and temperature control was an unwanted oscillation, giving rise to deviations far from the set-point. These design types would not survive in the marketplace today, given the energy-efficiency needs and demands placed on refrigerated appliances. The answer to efficiency with air conditioning came from aligning a system to part-load conditions while removing the temperature swing oscillation effect. In order to do that, mass refrigerant flow had to be controlled at changing conditions while preventing the temperature swing from causing erratic on/off. Changing mass flow rates to match load keeps the suction pressure at design, and maintains the volumetric efficiency while reducing power input through lesser demand at a more friendly low-compression ratio scenario. The temperature swings are smaller because capacity is controlled. In the perfect world, the compressor does not turn off; rather it gently oscillates to load change like a fine-tuned PID. Enter the variable speed compressor. The diagnostic needs for former air conditioning design systems were relatively straightforward and required a technician really to be equipped with minimal electrical tools such as ammeters and multi meters. The logic of these systems seemed simple, so it was not questioned too much. It did, however, require a new understanding for working with printed circuit boards, and gave many an insight into communication needs between indoor and outdoor systems.
Common scenarios
It is useful to discuss inverters and some of the components, plus common scenarios. This is not a specific reading of a service manual or exact descriptive nature for fault finding. For that you can use the manufacturer-provided service manuals and technical support services. The aim is to provide guidance on the things to look out for and consider onsite. Remember: • Contact your service agent/manufacturer for specific service and repair requirements for your unit. This is best practice. • Electrical work is for licensed and competent tradespeople relative to the field of work and licence requirements inclusive of restricted licenses. • Where a test or diagnosis involves resistance measurements, these are first option over any live-testing alternative. Regulations for this vary from state to state. So, let us have a look at some of the key areas with split systems and how these designs affect the way you approach servicing issues onsite. Just note the figures and information provided are not deemed completely accurate, but are likely in range.
Thermistors vs pressure switches
Our world is a binary system, and we use YES/NO in decision-making processes. This process is a pure digital response and everything that happens on modern air conditioning systems follows these rules. An analog response sees changes over time, but regardless of how much time or how much variation it can deviate to and from, the end result is a digital outcome. If you consider a voltage between 0 and 10V where 0 = off and 10 = on , the analogue deviation between these points can be seen and measured but the digital outcome is fixed at only two points. These points can be shifted; however, the outcome is the same. An analogue to digital converter ADC is used to convert analogue signals to a digital response or outcome. The value is converted into a simple digital on/off action. For the humble thermistor, which is analogue in operation, it is simply taking its time to get there. Let’s compare a very simple and familiar ADC with another.
The pressure control on the left is the simplest form of ADC, but it has a finite range of operation and it cannot be modified. The microprocesser can work with both analogue and digital signals with many variant rules applied to produce the required outcome. This makes the split system very powerful. It is easy to incorporate multiple decisions all at once based on processing speed and the number of controlling points. We will look at the logic behind the decisions further on, but for now, appreciate that even the simplest sensors and inputs can have a huge impact on operation and control. Pressure switches are basically unused in many domestic systems with the thermistors replacing their duty. When a pressure switch is added in a design, it is typically the last line of safety with the analogue systems in control of the main decisions. Here’s how this was done …
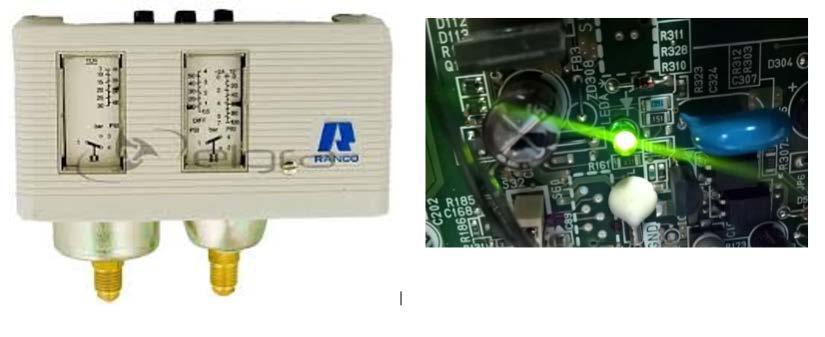
Analog to digital converter. Uses incremental pressure changes to enact an open or closed switch. Micro-processor controlled, uses both analog and digital decisions from multiple sources to enact outcomes. Indoor coil heat exchanger thermistor
In cooling mode acts as a low-pressure control by stopping operation below freeze conditions (0°C). In heating mode acts as a high-pressure control by keeping coil temperatures below 55°C by regulating outdoor fan operation first and then stopping the compressor as temperatures exceed 60°C (approximate).
Discharge pipe thermistor
The enthalpy of the refrigerant being used is already known to the system at pressure through mathematical operations associated with that refrigerant. Target superheats are set with the discharge thermistor from other operating thermistors depending on operation mode. Maximising performance is not to just run things flat out, but rather keeping a watch on the operating limits and superheats. The discharge pipe thermistor is one of the most important sensors in the system and responsible for many of the protective modes being activated with the compressor. Discharge pipe protection modes are the ones that surface during high load, high ambient in summer, and overload conditions over time. Protective modes are not just to stop operation – that is usually the most extreme of conditions – but rather to reduce the condition that is being caused to prevent further overload. This is why compressor frequency speeds vary during these modes and performance drops off. Unless there is more sensor data input to prove a genuine fault condition, logic systems act on absolutes and parameters of operation because the current problem experienced may be temporary. Rather than shut off all operation, the system gives time for conditions to improve, gradually stepping down operation if it does not and stepping up when things improve until it fully releases back to normal operation. Next time you are surfing the service manual, look at what thermistors do and what operations they are responsible for. The rules of operation logic for any such protective mode is usually well documented and as those conditions are absolutes. You can compare that with your communication interface tools that give real-time readouts. Thermistor inputs create certain problems when they are faulty. Usually, these problems seem to be almost identical across brands. For a thermistor to be faulty, the logic must see that it is out of its design operating range. Things have improved a lot here. Other thermistors can judge each other faulty if one is reactive (changing) while the other is not, depending on operating mode. Heat exchanger thermistors tend to be problematic if they experience excessive heat or if they breach their outer seal. Operation in any mode can stop, units do not start, compressor speed is being limited constantly creating low performance, indoor fans do not operate at full speeds, or they are going very slow. It’s the logic conundrum where the rules of operation are being applied and not contested, nor creating any fault code or fault response. In some cases, things don’t work but are quite normal. The outdoor air thermistor on heating mode will lock out the system if the ambient is above a set temperature. Even on a cold morning, direct sunlight or reflecting radiant heat and the perfect install facing the right way for sunrise can create a situation because of radiant energy on the sensor. This is fixed by waving a book to stir up air around the thermistor, but it does show that faults are not always accurate, and yet they are obeying their programmed logic rules. Indoor air sensors are the next most important sensor. Inverters operate in many ways, but the simplest rules require a compressor frequency to be set by a differential from set-point and current room air on condition. It is very important to check the unit’s design operating ranges in all modes. Continuous operation is shown by manufacturers for both indoor and outdoor conditions. Working outside these ranges for too long can create overload or cause protective modes to activate. The indoor air sensor location may be fixed on some models. The location and installation are important, especially if there is radiant energy from direct sunlight or the unit is recirculating air from obstruction. In the case of ducted units, wall remote sensors can be a real issue if they are not in a good monitoring area since in heating mode there is more reliance on the wall controller due to heating stratification effect. There are settings to switch the controller sensor out if it is not in a good monitoring area or enclosed. Fresh air intakes can also create problems in extreme weather on very hot days with return air in ducted systems. Squashed ducting can create vortex or eddy current patterns in return air boxes through air favouring one side (as shown in picture). These can create poor movement around the sensor.
Negative pressure zone when left-side duct is restricted, a vortex around the sensor can be created – as an example, around the return air sensor – which prevents correct air sampling.
Left return air duct squashed in by some force in the ceiling.
Example of impinged airflow.
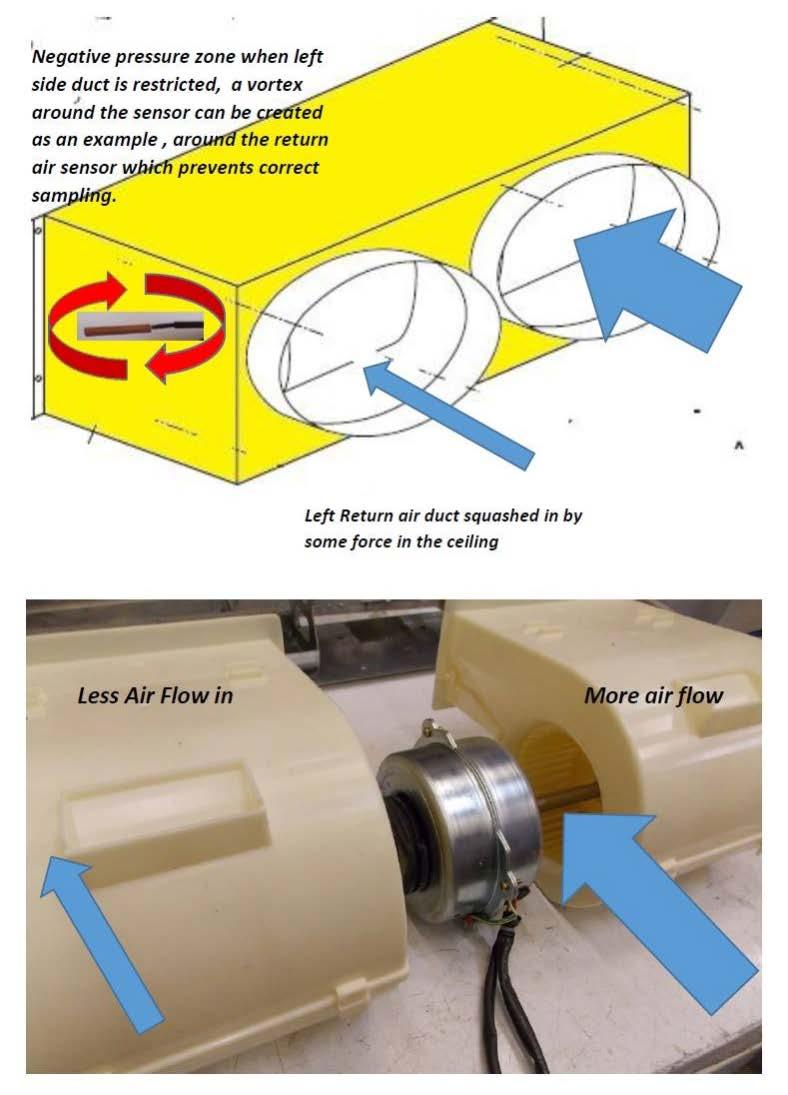
All these situations create conditions that the system must adjust for and that may affect operation. Technicians in many cases need to look outside the square rather than just look at the split system as being faulty due to some ongoing fault or performance issue. Temperature resistance checks can be done to prove functionality. The live readout tools are probably the best since some can fail mid-operation at certain temperatures over time with cases of erratic or intermittent faults suddenly occurring for no apparent reason. The simplest heat pump usually only contains indoor air temperature and heat exchanger sensors; outdoor units are the same and a discharge pipe thermistor. Domestic multi systems can have an extra indoor sensor for subcooling control and outdoor suction line thermistors. Electronic expansion valve opening/closing control can operate from more than one sensor during operation. Once you go up to variable refrigerant commercial systems, they can be everywhere, including branch control. Without knowing the functionality of these thermistors, it can be overwhelming trying to pinpoint an issue. It is a good idea to read up on the control of thermistor grouping per unit or device.
Pressure transducers
Pressure transducers are simple, and easy to test and diagnose. A 5V DC supply voltage is provided across the two wires (red/black) and the reference or feedback voltage is sent through the third wire to a ground reference (white/black). On heat pumps and commercial variable systems, you might see two types: 1. Dedicated high- and low-pressure transducers (independent) 2. Universal transducers that work with high- and low-pressure (suction line located). There is usually a given formula to work out the exact pressure it is reading from a given reference voltage; however, a more user-friendly chart is supplied to determine what the pressure transducer is reading currently. The advantage of transducers is the ability to use their analogue range and apply it to differing needs with refrigerants. Digital gauges are quite easy to transpose to other refrigerant types. These are critical devices responsible for many operations and fault determinations. The transducers by default take the place of first-stage pressure detection and monitoring for both high and low pressure. Unlike a conventional pressure switch, these will perform a pressure limit function through logic control and prevent unwanted pressure rise by controlling compressor speed. In the case that pressure does overload, they will halt operation and allow for retries over a period of attempts rather than just call it time for a sudden problem. If the pressure is overloading constantly, the system typically will call an error. The transducer’s best role is the ongoing control of both heating and cooling pressure/temperature design operations. For example, 6°C cooling and 46°C heating saturation temperatures. The compressor will be regulated to control and allow for other staging in a larger system for example. These do their best work in variable refrigerant systems in complement with other systems connected as one multi-unit. In single heat pump systems, the universal transducer does much the same. In general it is quite a reliable device. These also call changeover of reversing valves with needed pressure displacement differential and in some cases control EEV opening control from first start. Typical problems with these are quite easy to find, but they can cause unusual faults to occur. Use a service gauge, a DC voltmeter, and a reference chart to investigate, unless you have a live service diagnostic tool. The following faults with pressure transducers do occur, but may not show up in service manuals: • Non-start of unit – failure to run or load up compressor speed (low and high) • Non-start of unit due to false high pressure but transducer not out of range for an error code generation • Failure of reversing valve to changeover on heating or back to cooling operation • EEV on indoor unit does not open • An error code for low refrigerant is generated, but no refrigerant has been lost. In this example the fault priority is beyond our control. Once the transducer reads less than 1 Volt DC, its time to have a good look at the system charge. If it reads 0.5V DC, it will be in real trouble. Manufacturers have really improved on these in the commercial side with multi-type units having sub-error codes to identify which condensing unit and which sensor is failing. These units must be out of their operating range to be faulty. Because that range is quite generous, it is possible for them to operate in error from current pressure if they experience some malfunction. Read the manual to check where the specific brand and model operates, and what needs to be tested. Nothing is impossible with erratic components. ■
Pressure transducer with common wiring colours
Pr essure in MP a
DC Voltage
Pressure/Voltage graph – example
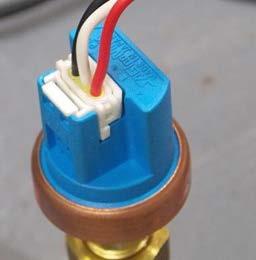
This month’s Skills Workshop was provided by Dennis Kenworthy, Affil.AIRAH, lecturer at South Metropolitan TAFE, WA and administrator of the website What Would Dennis Do? www.whatwoulddennisdo.com
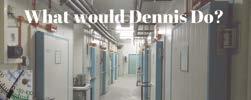