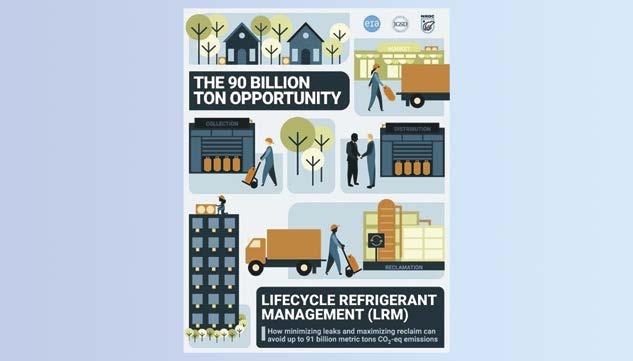
16 minute read
Global Update
by AIRAH
USA
INVISIBLE CLIMATE CULPRIT
Advertisement
Fluorocarbon emissions equivalent to 90 billion tonnes of CO2 could be avoided through minimising refrigerant leaks and maximising recovery and reclamation, according to a new report from US agencies.
The report, The 90 Billion Ton Opportunity: Lifecycle Refrigerant Management, estimates that better life-cycle management can prevent fluorocarbon emissions equal to nearly three full years of global energy-related carbon dioxide emissions. Report co-author Christina Theodoridi says refrigerant releases are “an invisible climate culprit”.
“Life-cycle refrigerant management provides clear and tangible interventions that can prevent the release of billions of tonnes of CO2e emissions across the refrigerant value chain to help us stave off the worst impacts of climate change,” she says. The report proposes six “pillars” of life-cycle refrigerant management: enhance product stewardship; increase refrigerant recovery, reclaim and reuse; reduce leaks; better reporting and enforcement; workforce development; and installation and servicing. To read the report go to us.eia.org ■
UK
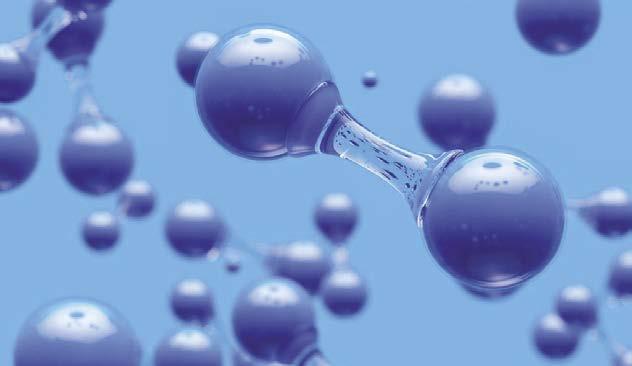
HYDROGEN HOPES DASHED
A review of independent studies on the use of hydrogen for heating has delivered a damning verdict for the idea that we may one day replace our existing gas network with a hydrogen network.
Completed by energy influencer Dr Jan Rosenow, the evidence review looked at 32 independent studies.
The review excluded reports carried out by or on behalf of a specific industry, because the results might reflect vested interests.
“The evidence assessment shows that the widespread use of hydrogen for heating is not supported by any of the 32 studies identified in this review,” says Rosenow. “Instead, existing independent research so far suggests that, compared to other alternatives such as heat pumps, solar thermal, and district heating, hydrogen use for domestic heating is less economic, less efficient, more resource intensive, and associated with larger environmental impacts.” ■
GERMANY
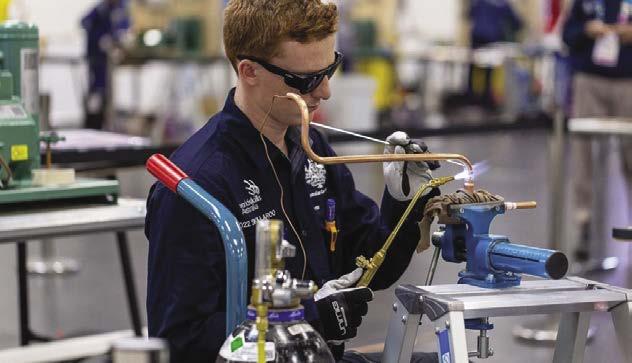
SKILLS THAT THRILL AND CHILL
The WorldSkills international competition for Refrigeration and Air Conditioning has been run and won in Nuremberg, Germany, as part of the giant Chillventa HVAC&R trade exhibition.
Sixteen young technicians from around the world competed in the event as part of the WorldSkills Competition 2022 Special Edition. The event was organised after the international competition planned for Shanghai earlier in the year was cancelled due to the pandemic.
Representing Australia was Tom Clancy from Western Australia, who was supported by WorldSkills international training manager and expert Carl Balke, Affil.AIRAH. “Tom proudly represented Australia on the world stage after nearly three years of dedicated training and commitment,” says Australian Skill Competition Manager Noel Munkman, M.AIRAH. He added that Clancy performed well despite not claiming a medal.
The gold medal was awarded to Chia-Cheng Tien of Chinese Taipei. The next competition is slated for Lyon, France, in 2024. ■
JAPAN
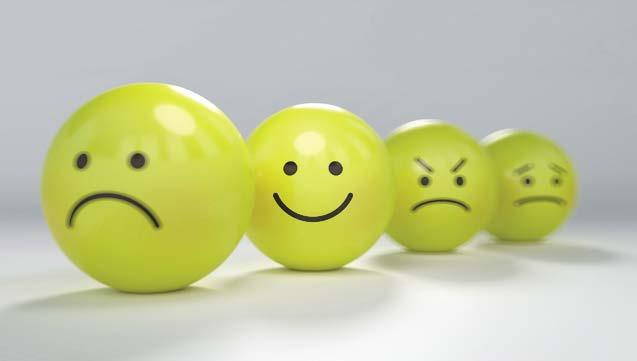
IN THE MOOD … FOR AC
Air conditioning that automatically adjusts to suit your mood? Now that is what could be called intelligent tech.
Introduced by Mitsubishi Electric and set to be launched in February 2023, the new addition to the firm’s Kirigamine Z series splits are said to be able to remotely measure someone’s pulse wave without contact. The Kirigamine Z are designed to analyse the state of the central nervous system (i.e., brain activity) and autonomic nervous system, and then determine human emotions from the data.
Using this information, it automatically adjusts room temperature, sensible temperature and airflow, and attempts to create as comfortable an indoor environment as possible.
PEA-M HAA
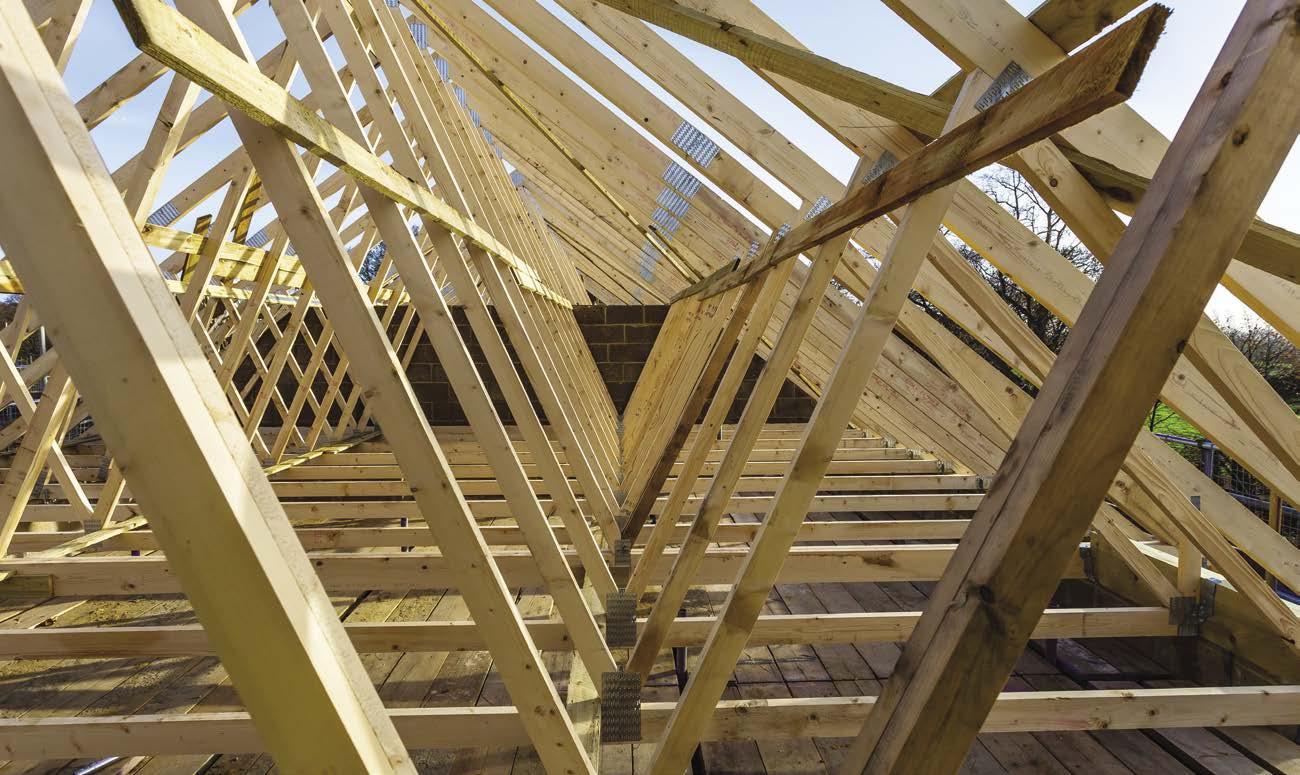
Two-Piece Ducted Unit
The PEA-M HAA Ducted has a two-piece construction*1, which allows for the separation of the indoor unit heat exchanger and the fan deck assembly. This is beneficial for installation into the roof space, for greater room capacities and increased variation in airflow; ensuring operation that suits most room layouts.
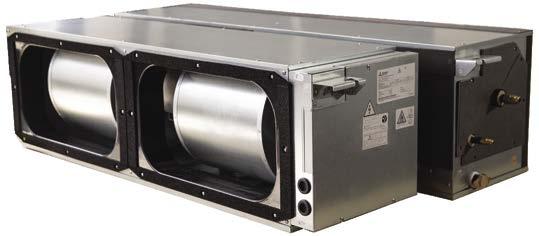
Ideal for Remodeling of Existing Houses
» The unit can be installed in roof trusses thanks to the two piece structure.
Two-Way Maintenance Access
» Two-way access to the fan desk assembly and to the drain pan*2 . » Even when the unit is installed near the ceiling and inaccessible from the bottom, the unit is accessible from another side.
Easier Installation
» The fan deck section and the heat exchanger can be separately transported and assembled in the ceiling space.*3
*1 The distance between the fan deck part and the heat exchanger part cannot be extended using a duct *2 The drain pan cannot be removed from the side. *3 Requires an access panel large enough to pass each part through.
For more information on our products please visit www.mitsubishielectric.com.au
Phone:1300 280 625
THE PRICE OF NEGLECT
How much does poor HVAC&R installation and maintenance cost? A study based on real-world data has revealed the most common equipment faults, as well as the energy penalties associated with them.
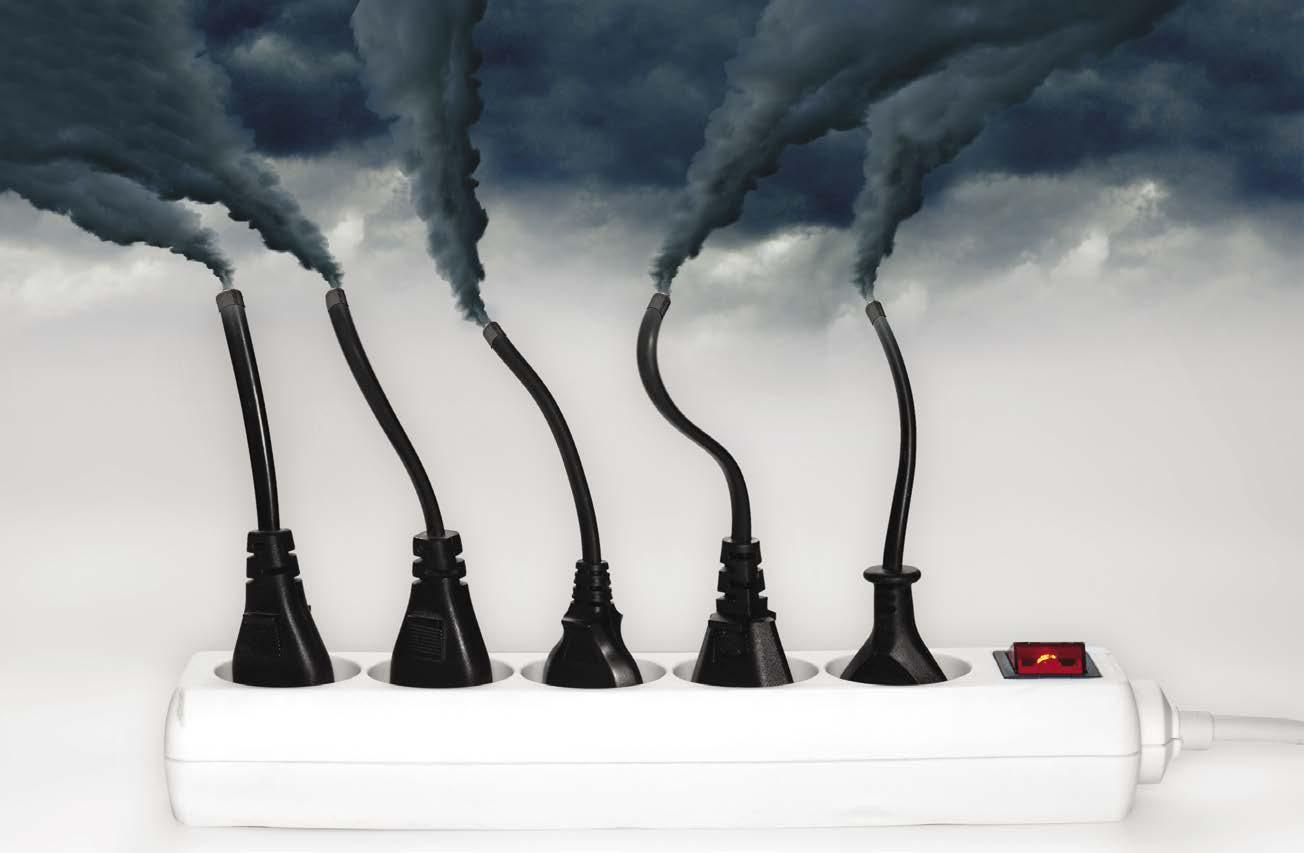
For some time now, the Australian government has understood that the HVAC&R sector offers big opportunities for reducing CO2 emissions and costs for end-users.
The review of the Ozone Protection and Synthetic Greenhouse Gas Management Program in 2014–2016 recommended working with industry to develop information to better inform equipment owners of the benefits of proper installation of equipment and regular equipment maintenance. This would hopefully lead to reductions in both refrigerant leaks and energy use. Key to the initiative was quantifying the benefits of HVAC&R maintenance. The major task was broken down into three distinct projects.
FAULT FINDING
The first, conducted by the Expert Group, was a global desk study that identified the most common and preventable faults found in refrigeration and air conditioning equipment. It also looked to quantify the energy penalties of these faults.
The resulting report, Leaks, maintenance and emissions, was published in early 2021. It found that the most common faults in HVAC equipment were incorrect refrigerant charge (over or under due to leakage); dirty condensers and associated mechanical issues; and dirty evaporators and associated mechanical issues. Following the release of this report, real-world Australian data relating to faults and energy penalties was sought.
“When undertaking research for the maintenance study we uncovered one of the largest, centralised databases of air conditioning maintenance work orders, developed and maintained by Grosvenor Engineering Group (GEG),” says Peter Brodribb, M.AIRAH, Managing Director at Expert Group.
The extensive database, established and run by GEG since 2000, contained millions of assets across tens of thousands of buildings involving in excess of 1,300,000 work orders.
“We realised that this invaluable data would shine light on the prevalence of HVAC faults in Australia,” Brodribb says. “So we approached the key stakeholders and negotiated access to the data and funds to undertake the research.” To ensure customer, building and employee confidentiality was protected at all times, the dataset was cleansed of all customer- and employee-specific information before being accessed by Expert Group. All building locations were also removed, other than identifying the state in which the building was located.
Once refined, the dataset used for analysis contained more than 260,000 repair work orders, reflecting more than $250 million in repairs on over 100 air conditioning asset types.
From this data, the maintenance study created an “encyclopedia” of commonly encountered faults or fault groups.
Air Conditioning Faults – An Australian Analysis was published in late 2021 and confirmed the prevalence of a number of the frequently occurring faults that result in energy penalties to equipment owners.
The report also provides good insight into the prevalence of faults that do not cause energy penalties but do cause interruptions to service and costs to repair.
“Around a third of the faults do not result in an energy penalty, only a cost to the end-user,” says Brodribb.
THE COMMON FAULTS
Using the GEG dataset, Expert Group determined the most commonly encountered faults or fault groups for all asset types. Electrical faults (power loss to system or component) represented 16 per cent of service calls, as did controls faults (faulty sensors, actuators, algorithms or settings). Airflow faults (fan faults, ductwork blockage, duct leakage, poor air distribution) followed, representing 14 per cent of service calls. Thermal comfort complaints (with no fault identified) represented 8 per cent of service calls. Other faults of significance (resulting in service calls) included dirty air filters (7 per cent), fan or pump faults (5 per cent), refrigerant faults (5 per cent), issues with condensate drainage (5 per cent), mechanical component fault or failure (4 per cent), dirty equipment (3 per cent), fault on pipework system (3 per cent), miscellaneous faults (3 per cent) and waterflow faults (3 per cent). To find the faults that incurred the largest energy penalties, some fault groups were disaggregated and/or combined into others. Some were removed completely, given the focus of the research was on air conditioning repairs. This review left a top 10 of fault areas that impact energy consumed and energy productivity that can be addressed by maintenance.
THE SQUEAKY WHEELS
Remarkably, the top five energy penalty faults account for nearly 90 per cent of all work order/repair activity, with HVAC hygiene accounting for almost 35 per cent of faults that result in an energy penalty. Control faults represent over 20 per cent of faults resulting in an energy penalty, followed by airflow, refrigerant and waterflow. The “other” group of faults, including chiller, compressor, boiler and insulation faults, accounted for approximately 15 per cent of faults resulting in an energy penalty.
35% 30% 25% 20% 15% 10% 5% 0% HVAC hygiene Controls Air ow Refrigerant fault Water ow Others
Figure 1: Most frequent faults that result in an energy penalty.
The refrigerant fault group contains three problem sources: refrigerant leaks, refrigerant charge level low (no leak detected), and refrigerant charge level high. The most common fault reported in this group is refrigerant leak (85 per cent), followed by refrigerant low (12 per cent), and refrigerant high (3 per cent). “Without examining individual work orders in detail, it is not possible to determine what proportion of the leak faults discovered were catastrophic leaks and which were slow or partial leaks,” says the report. “Similarly, without examining work orders in detail, it is not possible to determine the charge level for the 12 per cent refrigerant low (no leak detected) faults discovered. As such it is impossible at this time to determine what portion of the reported leaks incurred long and accumulating energy penalties.”
BY EQUIPMENT TYPE
A more detailed examination of data was able to identify the six main equipment types that make up the vast majority of installed air conditioning equipment: chillers; ducted air conditioning (split); ducted air conditioning (packaged); VRV/ VRF systems; close control (CRAC) systems; and single split non-ducted systems.
Chillers – The most common chiller faults were associated with waterflow (23 per cent), controls (22 per cent), electrical (16 per cent), line/pressure (12 per cent) and refrigerant (9 per cent).
Fact: 80 per cent of all chiller faults were energy penalty faults. Figure 2 shows the top energy penalty faults in descending order.
35% 30% 25% 20% 15% 10% 5% 0% Water ow Controls Line/pressure Refrigerant fault Coil blockage Mechanical Air ow Design, install, docs
Figure 2: Top chiller energy penalty faults.
Single split ducted systems – The most prevalent faults were associated with airflow (19 per cent), electrical (17 per cent), filter (15 per cent) and controls (14 per cent).
70 per cent of all split ducted system faults were energy penalty faults. Figure 3 shows the top energy penalty faults in descending order.
35% 30% 25% 20% 15% 10% 5% 0% Airr ow FilterControls Refrigerant fault Mechanical Line/pressure Coil blockage Design, installation… Other
Figure 3: Top single split ducted system energy penalty faults.
Packaged ducted systems – The most common faults were associated with electrical (19 per cent), airflow (14 per cent), filter (13 per cent), controls (13 per cent) and refrigerant (8 per cent).
69 per cent of all packaged ducted system faults were energy penalty faults. Figure 4 shows the top energy penalty faults in descending order.
35% 30% 25% 20% 15% 10% 5% 0% Air ow FilterControls Refrigerant fault Line/pressure Mechanical Water ow Coil blockage InsulationOther Design, installation… VRV/VRF systems – The most prevalent faults were associated with electrical (26 per cent), controls (17 per cent), refrigerant (13 per cent) and airflow (8 per cent). 63 per cent of all VRV/VRF system faults were energy penalty faults. Figure 5 shows the top energy penalty faults in descending order.
35% 30% 25% 20% 15% 10% 5% 0% Air ow Controls Refrigerant fault Line/pressure Coil blockage Filter Mechanical Water ow Other Design and installation
Figure 5: Top VRV/VRF system energy penalty faults.
Close control air conditioner (CRAC) systems – The most prevalent faults were associated with airflow (21 per cent), electrical (18 per cent), controls (11 per cent) and refrigerant (11 per cent). 69 per cent of all CRAC system faults were energy penalty faults. Figure 6 shows the top energy penalty faults in descending order.
35% 30% 25% 20% 15% 10% 5% 0% Air ow Controls Refrigerant fault Line/pressure Water ow Filter Mechanical Coil blockage Other Design and installation
Figure 6: Top CRAC system energy penalty faults.
Single split non-ducted systems – The most prevalent faults were associated with electrical (18 per cent), condensate/drain (15 per cent), airflow (15 per cent) and coil blockage (9 per cent). 61 per cent of all single split non-ducted system faults were energy penalty faults. Figure 7 shows the top energy penalty faults in descending order.
35% 30% 25% 20% 15% 10% 5% 0%
Air ow FilterControls Refrigerant fault Line/pressure Mechanical InsulationCoil blockage Other Design and installation
Figure 7: Top single split non-ducted system energy penalty faults.
Airflow was also found to be in the top three faults for all equipment types, except for chillers where waterflow (the equivalent of airflow) was the most common fault.
“Airflow and waterflow faults impact the heat transfer and heat distribution within these systems, directly impacting energy productivity,” says the report. “Proactive maintenance that routinely inspects and cleans airflow and waterflow components of air conditioning systems (and refrigeration systems) would almost certainly avoid energy waste attributed to these faults.”
Controls were also found to be in the top three faults for all equipment types, impacting the feedback and outputs from the system control elements. “These faults tend to cloud or disable the system intelligence and its sensors, reducing a system’s ability to react correctly to the environment being controlled,” says the report. Some controls faults, such as simultaneous heating and cooling, can be intensely energy wasteful. Refrigerant was found to be in the top five faults for all equipment types. “Most refrigerant faults (over 85 per cent) relate to refrigerant leakage and either operation on low charges or catastrophic loss of all refrigerants,” says the report.
AT FAULT
Unfortunately, Brodribb believes only a small part of the HVAC industry has a clear understanding of the impact of the maintenance practices on energy penalties and associated greenhouse gas emissions.
“These faults can result in compounding emissions, escalating operating costs and increasing total cost of ownership,” says Brodribb. As an example, he says refrigerant faults can account for around 12 per cent of all work orders/repairs that result in an energy penalty.
“We were surprised by the impact an annual leak rate of 5 per cent per annum, left unrepaired on a ducted split system, can have – resulting in an additional 200 per cent energy consumption over the lifespan of the equipment.”
One of the challenges the industry faces in addressing such issues is that building owners and operators generally seek the lowest cost solution – influencing the predominant maintenance model and creating a lowest cost paradigm. “Air conditioning maintenance service delivery is a highly competitive business in Australia,” says Brodribb. “The vast majority of clients adopt a reactive-only approach to maintenance – fix it when it breaks.”
Although acknowledging that some clients adopt a scheduled approach to inspections and minor maintenance work, he says very few adopt a truly proactive approach to maintenance.
Analysis by Grosvenor Engineering Group has shown that for specific sites and specific portfolio owners that move to a proactive and automated approach to maintenance, they will – in the medium term – reduce the overall costs of ownership of the system.
Due to the low number of clients that actually adopt such an approach, however, the research was unable to test this hypothesis for a significantly large representative group of buildings within a typology or of system types. Thus, it remains unproven.
“Industry contends that significant improvements can be made in the performance of the installed bank of equipment by focussing on correct sizing, installation, service and repair of equipment,” says Brodribb. “Undertaking these tasks will lead to cost-effective energy reductions and greenhouse gas abatement.”
INCREASING AWARENESS
“It is generally accepted that poor installation and lack of regular maintenance can have lifelong negative impacts on the efficient operation of HVAC&R equipment,” says Patrick McInerney, Director of International Ozone Protection and Synthetic Greenhouse Gas Section at the Department of Climate Change, Energy, the Environment and Water (DCCEEW).
“However, there does not appear to be more than anecdotal evidence available in the public sphere to support this understanding.”
McInerney says both industry and governments support the approach to increase the awareness and evidence around the benefits of routine maintenance practices on HVAC&R equipment.
At the recent ARBS 2022 conference, a joint panel with industry leaders and the Australian Government presented on quantifying the benefits of routine maintenance of HVAC&R equipment.
A bench testing project undertaken by the Australian government to measure the impact of four identified common faults found average energy losses were between 14 to 20 per cent across most tests.
The findings are now available on the DCCEEW website.
“In terms of proactive maintenance outcomes related to this project, the Australian government will work with the HVAC&R industry and the community – households and businesses – to better inform and increase the awareness of the benefits of proper installation and routine maintenance,” says McInerney.
“The results from the work undertaken to date will help provide reliable and accessible information to target the different audiences.
“It is important to note that there is no one solution to address this issue and working together with businesses, technicians and facility managers, contractors and retailers, governments and the industry as a whole, would provide the best outcome – including behaviour change, which is key.” ■
Airflow was found to be in the top three faults for all equipment types.
SELLING EFFICIENCY
Instead of lowest cost driving the maintenance model, Air Conditioning Faults – An Australian Analysis reveals that the “selling of efficiency” must become core to the maintenance business model if change is to occur.
Other changes to the status quo could also drive improvements in system reliability, efficiency and energy outcomes, including industry education and mandatory maintenance.
“Even a half-day online training course to assist contractors or provide them with the data and tools on how to do this would help industry undertake this in a consistent and professional way,” says Brodribb.
As far as mandatory maintenance goes, Expert Group believes there is merit in introducing mandatory maintenance for commercial applications above certain capacities.
This could include routine leak checks for certain classes and sizes of HVAC&R equipment to reduce emissions, like those mandated under the European Union F-Gas Regulations.
“These requirements could be a framework to include other maintenance practices that target high frequency faults that result in an energy penalty,” says Brodribb. ■
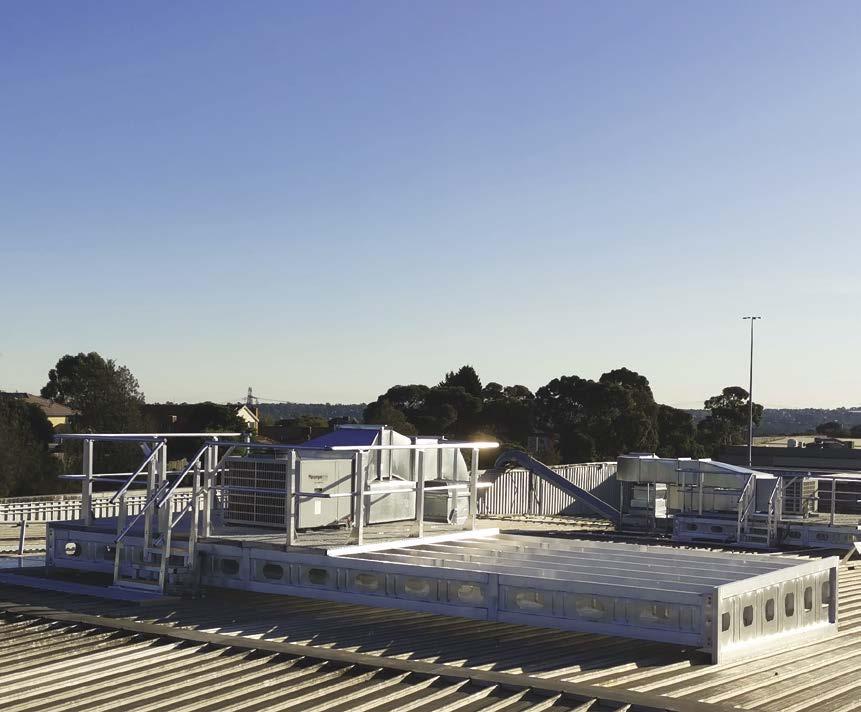
Switch to the recognised leader in air conditioning control systems.
Our installation contractors vote iZone the easiest, fastest and most reliable air conditioning control system to install.
National Supply Chain
Our systems are designed and engineered in Australia to suit the Australian and New Zealand market. We have a robust supply chain and expansive distribution network which means our systems are readily available, all year round.
Return on Investment
Our systems are compatible with all the major air conditioning brands and pre-configured in the factory, making installation easier and faster, saving you time and money. Plus, our competitive pricing means you get value for money.
Contractor Servicing and Support
We’ve built and maintained successful partnerships with contractors and installers nationwide for over a decade.
We provide resources and training to get the job done right.
Innovative Products and Solutions
Our commitment to continuous research and development enables us to supply a best in market control system that uses the latest technology, is of the highest quality and almost never needs any support. We’re so confident about this, that all our systems are backed by a 10-year warranty.
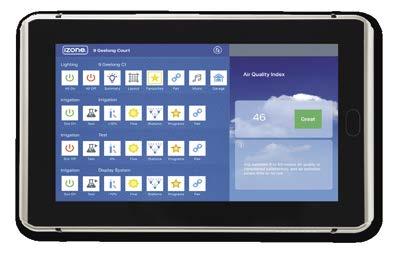
Talk to us about becoming an iZone contractor and make the switch today!
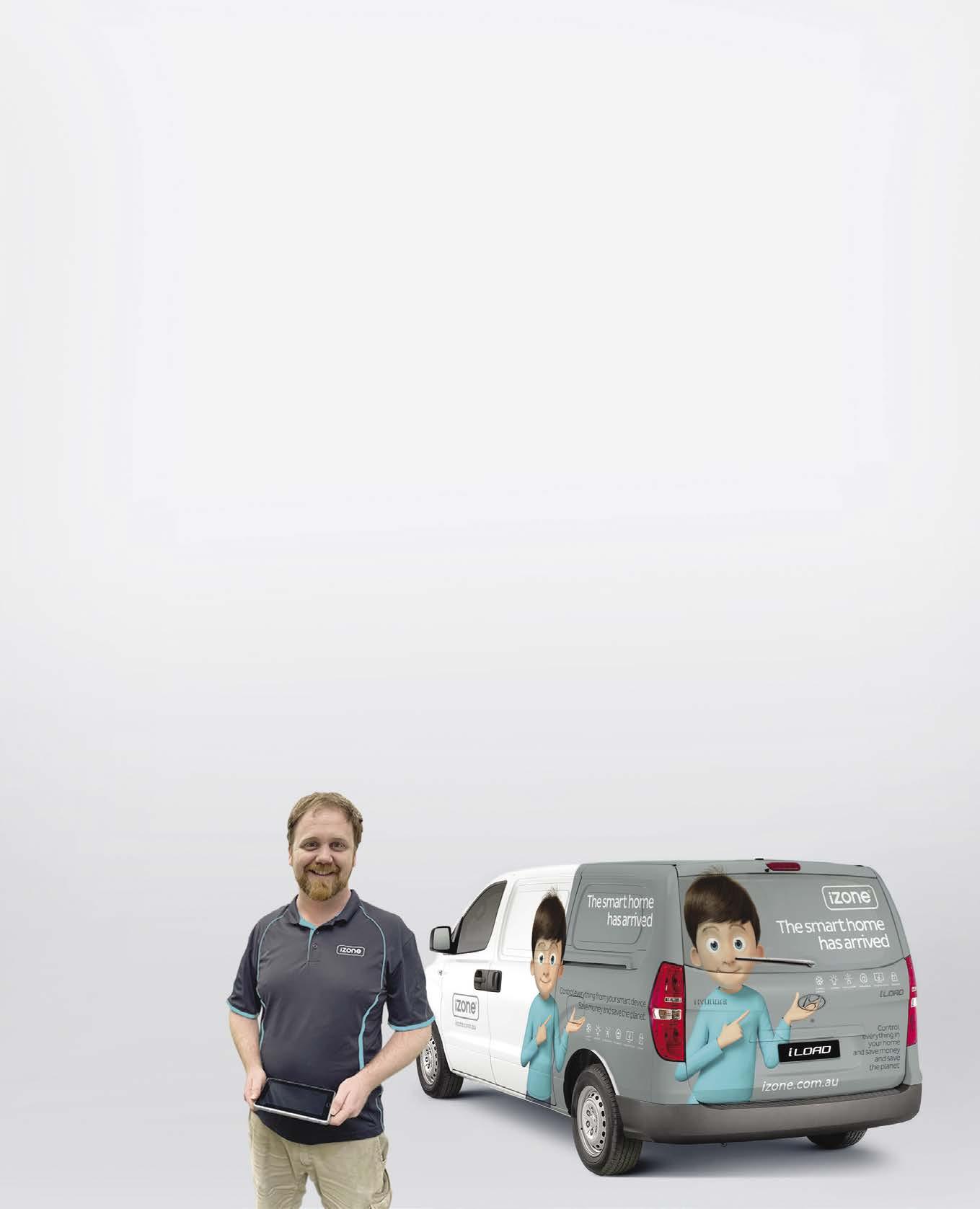

Conditions Apply
salesdesk@izone.com.au | +61 8 6556 6415 | 40 King Edward Road, Osborne Park WA 6017 www.izone.com.au/smart-partners