
14 minute read
AIRAH Awards 2022
by AIRAH
HVAC&R’S LEADING LIGHTS
The 2022 AIRAH Award gala dinner, held on November 24 at Luna Park in Sydney, paid tribute to the top people, projects and products of Australia’s HVAC&R sector.
Advertisement
Most agree that our industry is chronically underappreciated by the general public. Despite providing critical services and making modern life possible, HVAC&R is rarely noticed.
Will that ever change?
It’s a long-term challenge, but through its annual awards event, AIRAH has been working to raise the profile of HVAC&R.
“For more than a decade, even when we had to go virtual because of the pandemic, AIRAH has held our annual awards,” says Chief Executive Tony Gleeson, M.AIRAH.
“We are committed to shining a light on the critical and innovative work being done in our industry.”
And Gleeson believes more attention is coming to the HVAC&R industry, whether we like it or not.
“As the world begins to comprehend just how much effort is required to rein in our greenhouse gas emissions and prevent more extreme climate change, people are looking for sectors that can make a difference,” he says. “HVAC&R is one of those.”
Gleeson notes the 2022 Global Status Report for Buildings and Construction, released recently at COP27, shows the buildings and construction sector is not on track to achieve decarbonisation by 2050. And the gap between the actual climate performance of the sector and the decarbonisation pathway is widening.
“It’s a daunting challenge,” he says. “But looking at the winners and finalists of the 2022 AIRAH Awards, I believe the HVAC&R industry has what it takes.”
WINNERS’ CIRCLE
For more information about the finalists and winners of this year’s AIRAH Awards, go to www.airah.org.au/awards
BEST HVAC RETROFIT OR UPGRADE
McClintock Engineering Group Otto Hirschfeld Dissection Laboratory AHU upgrade
EXCELLENCE IN DIVERSITY AND INCLUSION
Cundall
EXCELLENCE IN HVAC&R RESEARCH
Conserve It Real-time model predictive control with digital twins and edge computing technologies
EXCELLENCE IN INNOVATION
AMP Capital Quay Quarter Tower
EXCELLENCE IN SUSTAINABILITY
Benmax The University of Newcastle’s Q Building
PRODUCT OF THE YEAR
Smartair Diffusion Smartemp Helical Vari-Swirl Diffuser
FUTURE LEADER
Mark Elliott, M.AIRAH
INNOVATIVE USE OF RENEWABLE ENERGY IN HVAC&R
Conserve It Optimal scheduling of air conditioning systems with renewable energy resource and thermal storage
Jason Jarvinen, Stud.AIRAH
STUDENT OF THE YEAR – TRADE
Renzo Antonio Munster, Stud.AIRAH
WR AHERN AWARD
“Best-practice energy performance benchmarked for refrigerated warehouses” by Stefan Jensen, F.AIRAH – August/September 2021
JAMES HARRISON MEDAL
Dr Stephen White, L.AIRAH
AIRAH THANKS THE 2022 AIRAH AWARDS SPONSORS
Awards Gala sponsor
Future Leader sponsor Student of the Year – Trade sponsor
Excellence in Diversity and Inclusion sponsor Product of the Year sponsor Excellence in Sustainability sponsor
WR Ahern Award sponsor
MODULE 149
REFRIGERATION PIPING – SUCTION LINES
PROUDLY SPONSORED BY
Skills summary
■ What?
A guide to the correct design of suction lines for refrigeration systems. ■ Who?
Relevant for anyone involved in designing, installing, commissioning or maintaining refrigeration systems. Since many of the operational problems encountered in refrigeration applications can be traced directly to improper design and/or installation of the refrigerant piping and accessories, the importance of proper design and installation procedures cannot be over-emphasised. In general, refrigerant piping should be so designed and installed as to: ■ Ensure an adequate supply of refrigerant to all evaporators ■ Ensure positive and continuous return of oil to the compressor crankcase ■ Avoid excessive refrigerant pressure losses, which would unnecessarily reduce the capacity and efficiency of the system ■ Prevent liquid refrigerant from entering the compressor during either the running or off cycles, or during compressor start-up ■ Avoid the trapping of oil in the evaporator or suction line, from where it might subsequently return to the compressor in the form of a large
“slug” with possible damage to the compressor. This Skills Workshop looks specifically at suction lines.
The suction line is the most critical line in the piping system. It must be carefully designed to ensure a uniform return of dry refrigerant vapour and entrained oil to the compressor. If slugs of liquid refrigerant or oil, or both, reach the compressor, serious compressor damage can result. Study Figure 1. Starting at the evaporator, the stub of pipe at the evaporator outlet must be of sufficient length to permit the attachment of the remote bulb of the expansion valve and the insertion of the external equaliser line. The equaliser line is inserted downstream from the remote bulb. This location prevents any small leakage of liquid refrigerant through the equaliser line from influencing the temperature sensed by the bulb. The suction line is dropped vertically downwards from the evaporator to provide free drainage of the tubes.
Figure 1 – Suction piping for evaporators connected in parallel
Note that the downstream, or lower, section of this horizontally split coil is connected to the common suction line using a double elbow arrangement. The double elbow not only drains the tubes but it also isolates the remote bulb and equaliser line connection from the suction pressure and temperature of the upper coil section. This prevents the upper section from influencing the operation of the expansion valve of the lower coil section. Figure 2 shows how, if the evaporator is located above the compressor, the horizontal section of suction line is pitched towards the compressor at least 12mm for each three metres of run. This promotes the movement of oil in the direction of refrigerant flow.
equaliser line
remote bulb
Figure 2 – Piping where evaporator is above compressor
Figure 3 shows the design of a suction line riser where the evaporator is below a non-unloading compressor.
pitch
Note: In Figure 3, the suction line is brought down to form a trap. The trap not only drains the riser but it drains the coil as well. This single trap will drain up to a 7.5m length of riser. If the riser exceeds 7.5m in vertical height, one additional trap is required for each 7.5 m of rise, as shown in Figure 4.
pitch The second trap allows the upper and lower sections of the riser to be drained separately. This divides between the two traps the oil drained from the riser and coil during the ‘off cycle’. When the compressor is restarted, the oil will leave the traps at a rate and in quantities that will not harm the compressor.
Compressor suction connection
The suction line is joined to the compressor using an anchored, 45-degree canted loop. As with the discharge line, this loop absorbs compressor vibration.
pitch
Figure 4 – Suction riser with double trap
Suction line velocities
As for the discharge line, suction line minimum vapour velocities are 2.5m/ sec in horizontal runs and 5m/sec in vertical risers, with the same 20m/sec maximum velocity. However, compared to the discharge line, the pressure drop is limited to a lesser 21kPa when R22 is used (14kPa for R134a). As discussed previously, excessive pressure drops within either the suction or discharge lines, or both, increase the compressor compression ratio. As the compression ratio rises, the volumetric efficiency, or the ability of the compressor to pump refrigerant, falls. Therefore, to preserve compressor efficiency, suction line pressure drops in excess of normal limits should be avoided.
Double risers
The construction of the suction line double riser is the same as that of the discharge double riser system. A suction line double riser is needed with unloading compressors where the compressor’s minimum capacity stage causes vapour velocity within the riser to fall below the minimum 5m/s. At the compressor’s minimum capacity stage, the reduced vapour velocity causes oil to drain from both risers, filling the base trap. This diverts the refrigerant flow into the small riser, which is sized to maintain adequate vapour velocity for oil movement at the minimum compressor capacity stage. When, due to increased system load, the compressor returns to a higher stage of loading, the increased vapour flow clears the trap of oil. Once the trap is clear, refrigerant flow returns to the larger riser. As in a discharge double riser system, a vertical rise in excess of 7.5m requires one additional trap for each 7.5m of rise, as shown in Figure 5.
pitch
more than 7.5m pitch
pitch
Figure 6 – Compressor suction connection
Note that the suction line is pitched towards the compressor and the loop is canted downwards to provide free drainage into the suction connection. Unlike the discharge side of the compressor, where oil entry can cause a slugging problem, oil entering the suction side is broken up by the suction strainer screen and simply returns to the crankcase.
Multiple compressor systems
The suction connections to multiple compressors should be made through a manifold arrangement to equalise the pressures at each machine. Such an arrangement is illustrated in Figure 7. In this particular application, the suction line approaches the compressors from an evaporator located at a higher level. Note that the manifold is as short as possible and installed level to prevent oil from collecting at one side of it, causing an unequal return to the compressors. The individual suction lines leave the manifold at the top. These lines have ends cut at a 45-degree angle and are inserted into the manifold with the points of the pipe resting on the bottom, as shown in Figure 7. This is done to draw oil from the base of the manifold. The inverted loop formed by the compressor suction connections should be at least 350mm in height. The horizontal runs of suction line are pitched towards the compressor as much as possible. Since the common suction line drains freely towards the compressors, this piping arrangement is suitable for use with both unloading and non-unloading machines.
pitch
pipe anchor
Figure 7
When the suction line approaches the compressors from an evaporator located at a lower level, the piping arrangement illustrated in Figure 8 is recommended. The common suction line is pitched downwards as far as the fittings permit. The line is turned downwards and divided in such a way that two traps, approximately 350mm in height, are formed. The vertical lines to the compressors are sized to
produce 5m/sec minimum vapour velocity. The maximum height of the vertical risers to the compressors is 7.5m. This piping scheme is suitable for use with non-unloading compressors.
suction line
pitch pitch
350mm min.
crankcase equaliser line
compressor
shut-off valve compressor
Figure 8
A similar piping design for use with unloading compressors is illustrated in Figure 9. To accommodate the unloading feature, double risers are used. As before, the common suction line is turned downwards into a manifold. The individual suction lines are taken from the bottom of the manifold into the traps of the double riser systems. The trap formed by the downward turn of the common suction line should measure approximately 350mm from the bottom of this line to the base of the traps of the double risers.
suction line suction line
compressor
7.5m max.
compressor pitch
350mm approx.
suction line manifold
Figure 9
Suction line accumulators
In many situations, a suction line accumulator is used to protect the compressor from damaging slugs of liquid refrigerant. In particular, reverse-cycle units and systems on ‘hot gas’ defrost may require this kind of protection. Manufacturers of small split air-conditioning systems often use accumulators to protect equipment against the many variables that may occur during installation and operation.
EDITION 05
NATIONAL RESOURCE AUSTRALIAN REFRIGERATION AND AIR-CONDITIONING This skills workshop is taken from Australian Refrigeration and Air‑conditioning, Volume 2, authored by Graham Boyle, L.AIRAH.
double risers common suction line
manifold 350mm min.
Figure 10 – Section through a suction accumulator – with its location close to the compressor also shown. Note the very small hole in the suction pipe to draw oil (and a little liquid) back to the compressor.
Suction line insulation
Refrigerant changes state in the evaporator at its saturation temperature – which is sometimes referred to as saturated suction temperature (SST) or suction temperature. Because of its low temperature, the refrigerant vapour continues to gain heat (superheat) as it returns to the compressor. The amount of superheat gained should be kept to a minimum. Higher than optimum return vapour temperature will result in excessive discharge terminal temperature, higher than necessary condensing temperature, greater heat of compression, increased bearing loads, poor lubrication effect, possible coking from overheated oil and poor cycle efficiency. It should also be noted that the greater the degree of superheat (higher return vapour temperature), the greater will be the specific volume of the vapour entering the compressor, thus reducing the refrigerant flow rate. This is contrary to best economy in system performance, which requires maximum practical refrigerant flow in order to obtain maximum benefits from evaporator cooling within the refrigerated fixture. In order to maintain a minimum superheat in the suction line, it is good practice to insulate all suction lines. Suction line insulation may be selected from various types, but the most common, and easiest to use, is flexible foam rubber insulation. For large installations,and thickness of insulation is specified and is usually installed by expert pipe laggers.
Insulation thickness
Several points must be considered when selecting insulation thickness: (a) length of suction line (the longer the line, the thicker the insulation required) (b) location of suction line (For example, if the line is in the sun, thicker insulation and a reflective sun shade will be required.) (c) saturated suction temperature (For example, freezers require thicker insulation to prevent moisture from condensing on the outside of the insulation and also due to the higher temperature difference between the refrigerant and the ambient temperature surrounding the pipe, which could increase the rate of heat flow.) Suggested insulation thicknesses are: • low-temperature systems – 25mm for short lines, 40mm for long lines • medium-temperature systems – 13mm for short lines, 19mm for long lines • air-conditioners – 13mm for short lines, 25mm for long lines. Note: Many split air-conditioners locate the refrigerant control within the outdoor unit. In this situation, the line that we normally would think of as the liquid line becomes part of the evaporator during the cooling cycle and, therefore, needs to be insulated. ■
Next month: Selecting indoor design conditions for thermal comfort
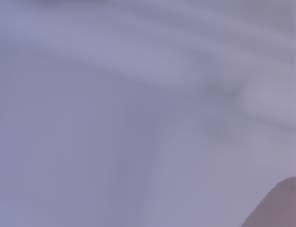
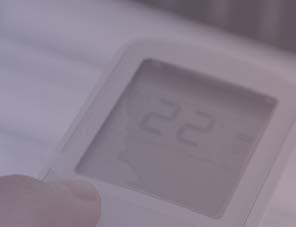
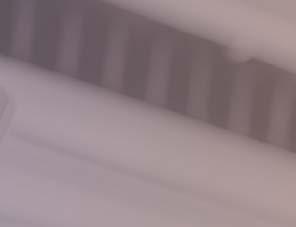
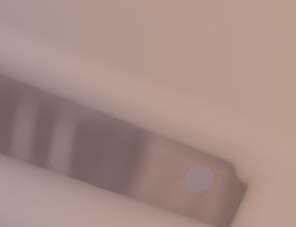
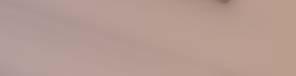
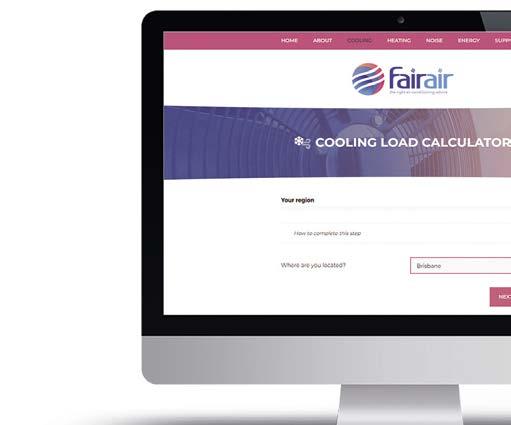

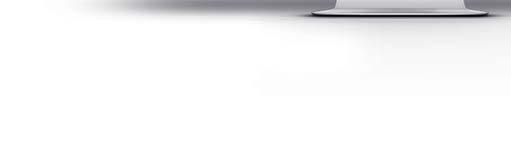

SECRETS OF A HOUSE WHISPERER
Widely regarded as the guru of creating comfortable and healthy homes in the US, Nate Adams has established a vast following of HVAC contractors who apply building science in their work. Louise Belfield reports.
In the view of Nate Adams, aka “the house whisperer”, building science is sexy. And he has built his consulting business and resulting sales process software as a service for heating, ventilation and air conditioning (HVAC) contractors on that premise.
The founder of Energy Smart Home Performance in Cleveland, Ohio (energysmartohio.com) and author of The Home Comfort Book, Adams has developed a new business model and way of looking at homes for HVAC contractors. He’s called it HVAC 2.0 and it’s based on designing and executing whole-house projects that bring a home into balance using both insulation and HVAC.
“Homes are complex systems of interconnected systems,” he explains. “Understanding how one thing may affect the performance of other things is really important in avoiding expensive mistakes.” Although he fell into HVAC “by accident”, Adams has runs on the board.
“I came from the insulation and air sealing side,” he says. “I worked in outside sales for a fibreglass insulation manufacturer and became an insulation retrofit contractor.”
After losing his job during COVID-19, Adams set himself the task of learning more about building science and then became a building analyst.
“I had several frustrating projects where I couldn’t solve problems for clients and it turned out that HVAC was the key.”
Not just HVAC, in fact, but smaller/right-sized HVAC and balance. Enter HVAC 2.0, which Adams describes as “a software-backed sales process, a guild and an ethos”. contractors that helps them solve client problems predictably and profitably, regardless of complexity. It’s strongly grounded in building science but is still fairly easy to learn,” he says.
It came about when his business partner noticed patterns in how home energy levels were testing and what issues his clients were trying to solve.
“So he had a basic process mapped out as a result of that and he taught it to me,” says Adams. “We then tweaked it and perfected it to create HVAC 2.0.”
The Home Comfort Book, designed to help both contractors and homeowners to design the perfectly comfortable home, also came out of that breakthrough. It is essentially a book about pattern recognition – the basis of HVAC 2.0