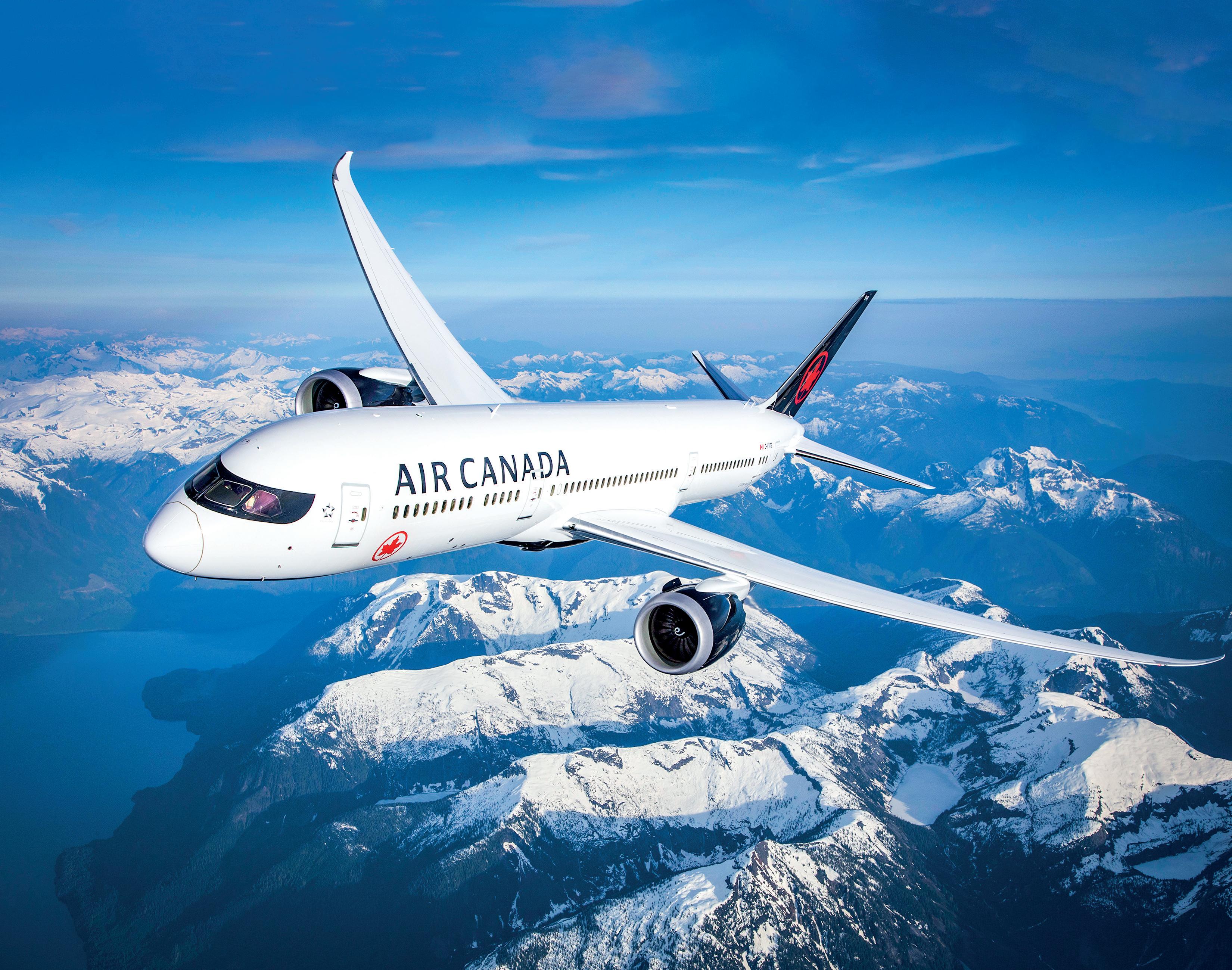
12 minute read
CASE STUDY: Managing and synchronizing devices of all types at Air Canada
Managing and synchronizing devices of all types at Air Canada
Keith Dugas, Director, Maintenance AI & Connected Operations, at Air Canada shares how significant operational gains and cost savings were achieved using a device management platform.
As technology becomes increasingly integral to the way we work, it also becomes important that the various technologies in a business communicate with each other and work with the same information. This article is about Air Canada’s evolution from paper to digital as part of our overall strategy to ensure that all devices are well managed and synchronized.
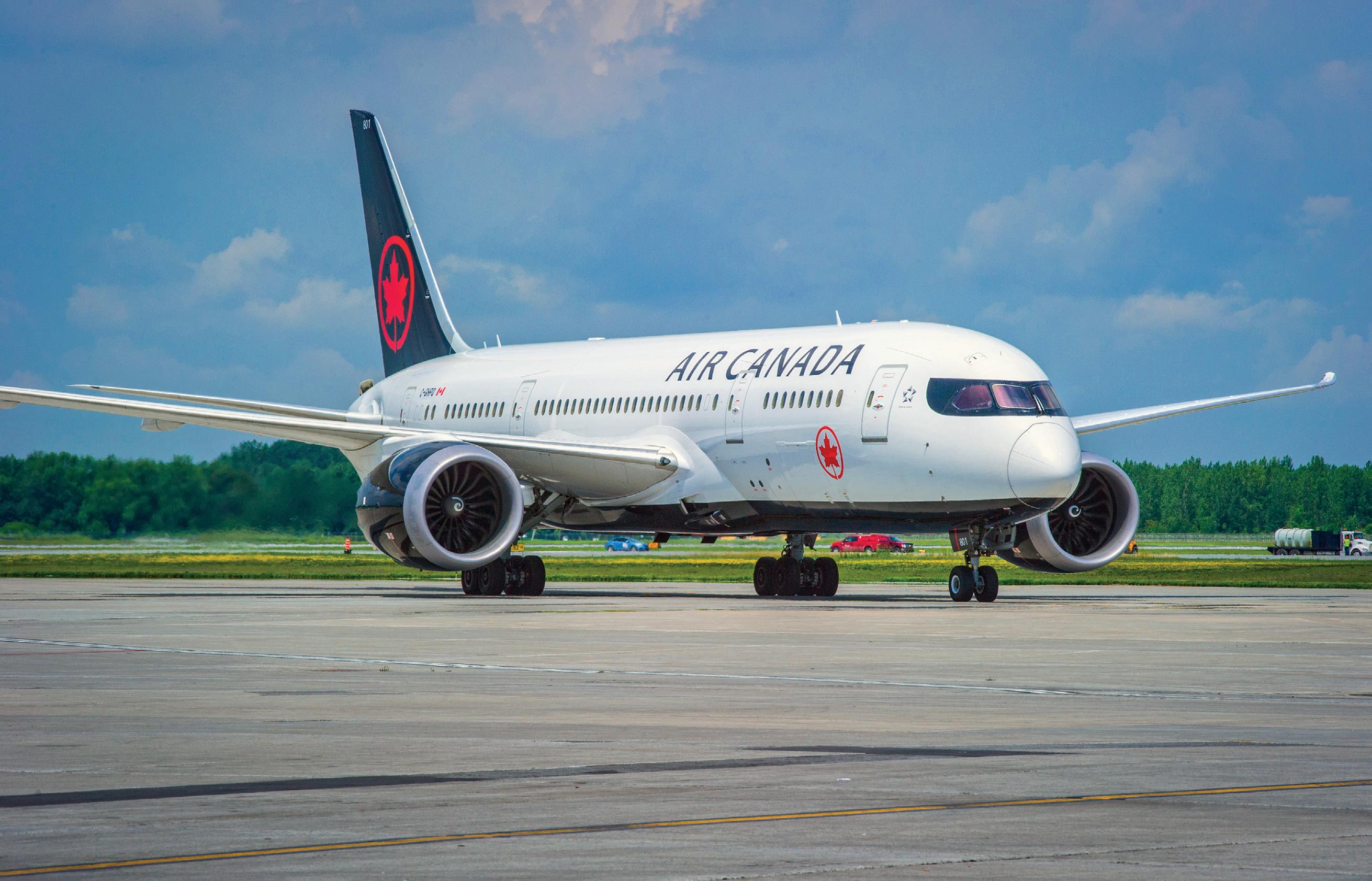
OVERVIEW
Air Canada is the largest airline in Canada by fleet size and passengers carried. Keeping aircraft in optimal condition is a critical part of everyday operations. For that, the Maintenance team must optimize aircraft maintenance procedures to ensure security and meet regulatory requirements while minimizing turnaround time between flights to limit the costs of having an aircraft grounded. Essential to meeting regulatory requirements is ensuring that maintenance engineers have mobile tools with the latest documentation always available plus achieving optimal aircraft security. However, maintaining synchronicity across all devices throughout multiple sites presents numerous challenges which can add significant costs and delays that can result in longer aircraft turns. “With the challenges of managing mobile devices, Air Canada looked for a partner to help ensure that their teams always had up-to-date and ready-to-use devices. The best match identified was M3 Solutions…”
With the challenges of managing mobile devices, Air Canada looked for a partner to help ensure that their teams always had up-to-date and ready-to-use devices. The best match identified was M3 Solutions and this case study explains how that worked. Of course, different airlines will have different needs but this article highlights the fundamental reasons for having a solution to manage devices, how one such solution works and was implemented plus, of course, what Air Canada gained from implementing the solution.
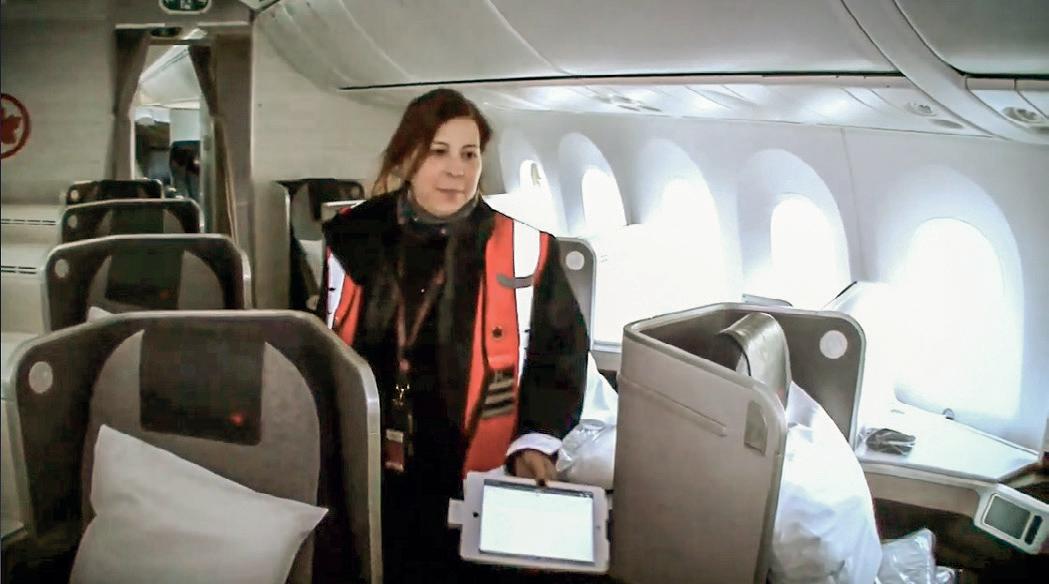
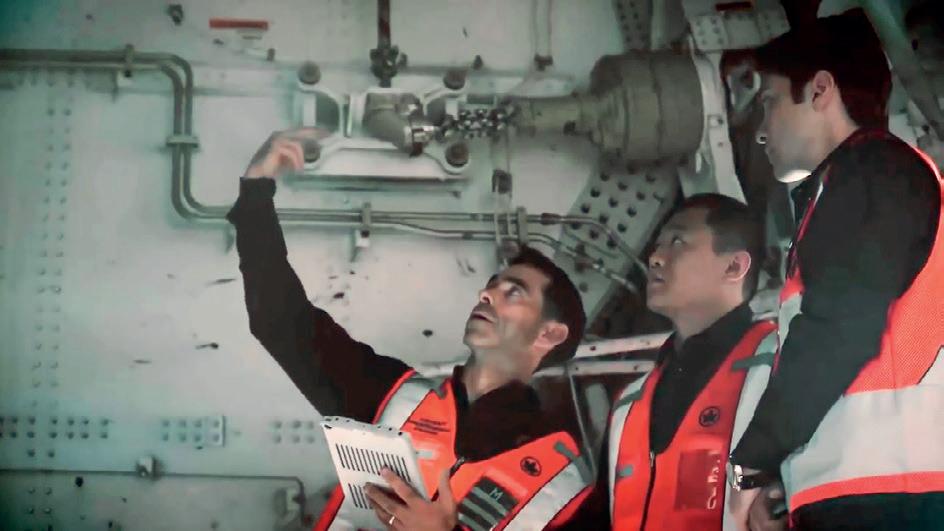
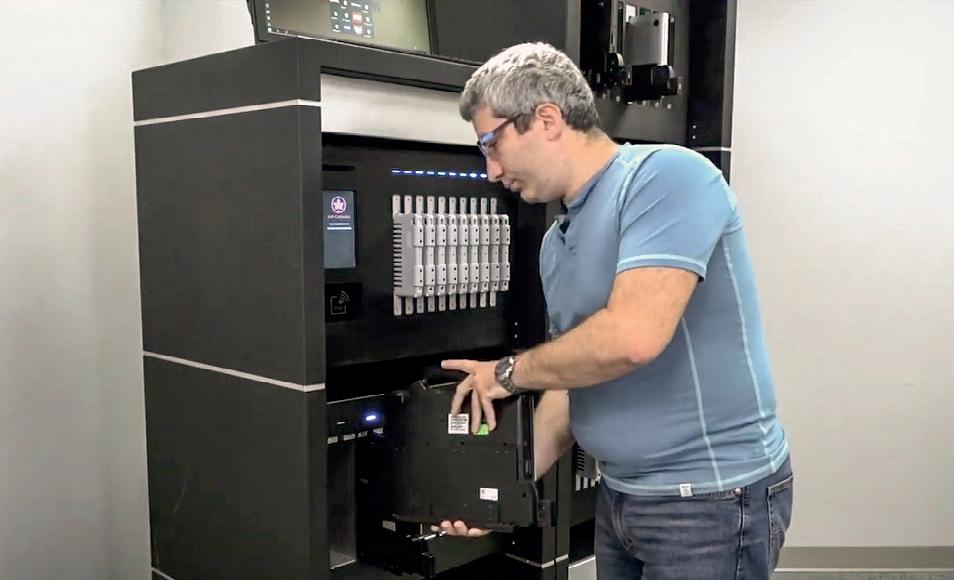
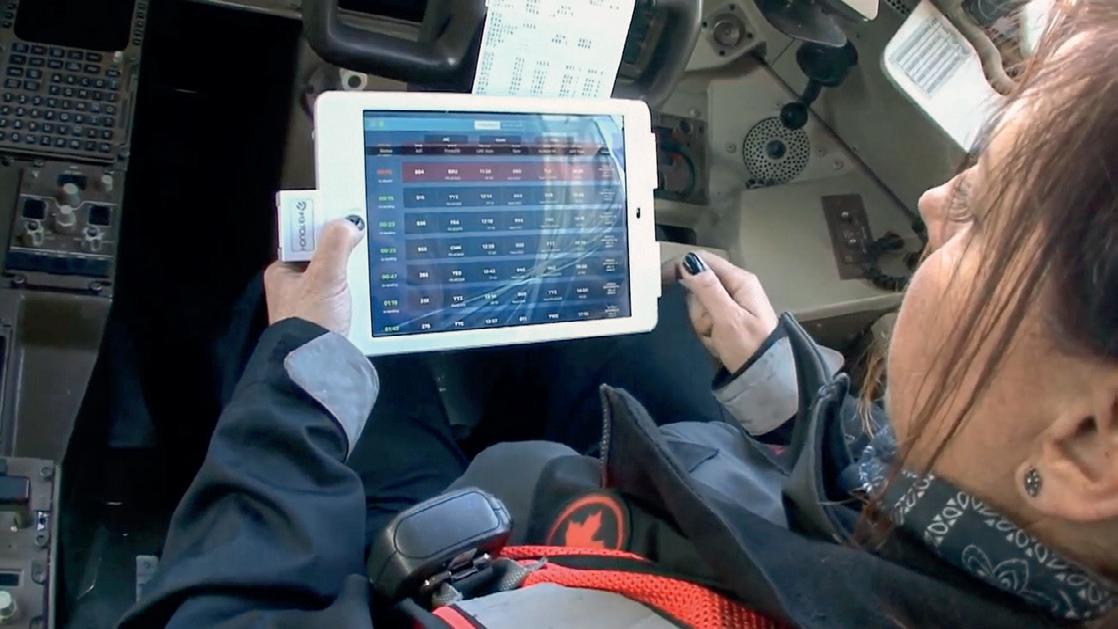
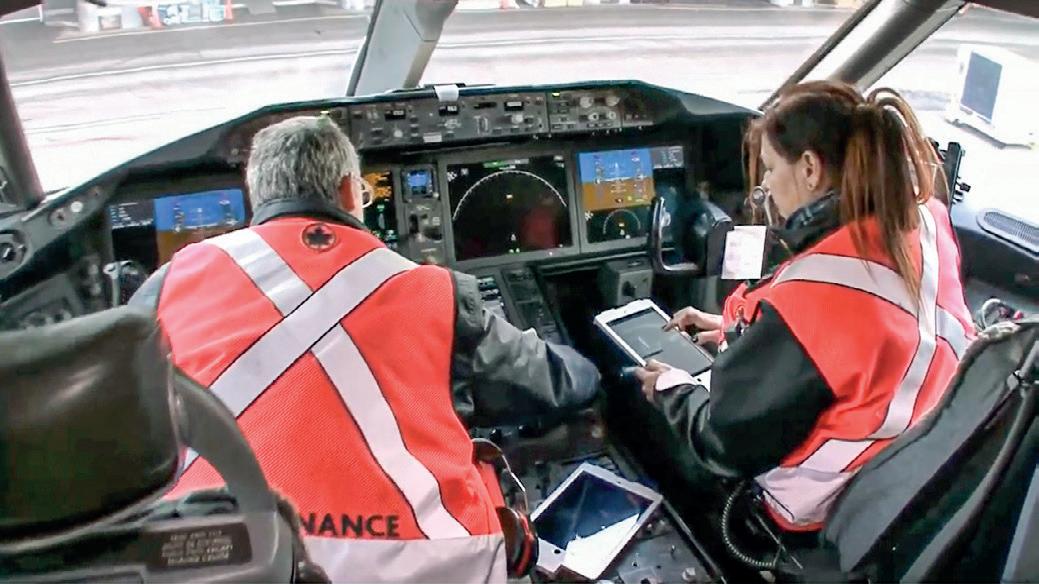
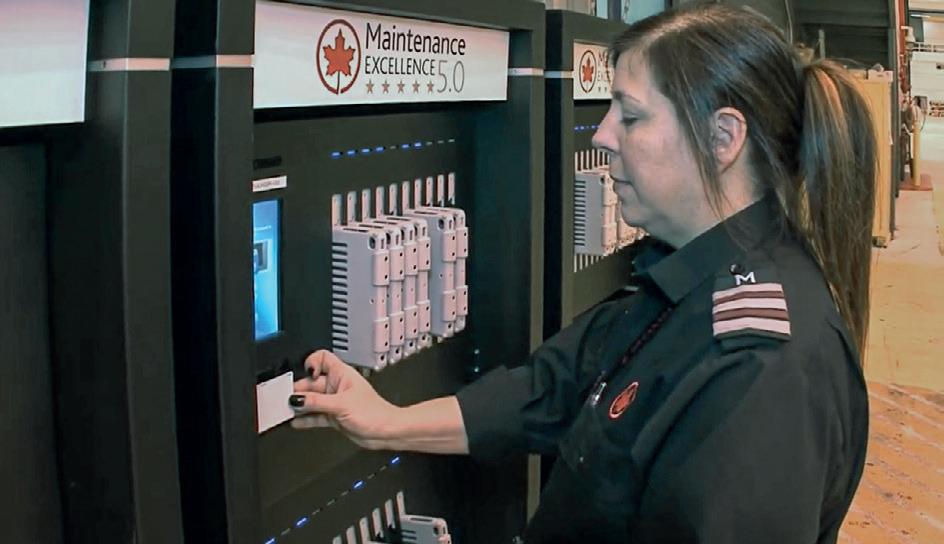
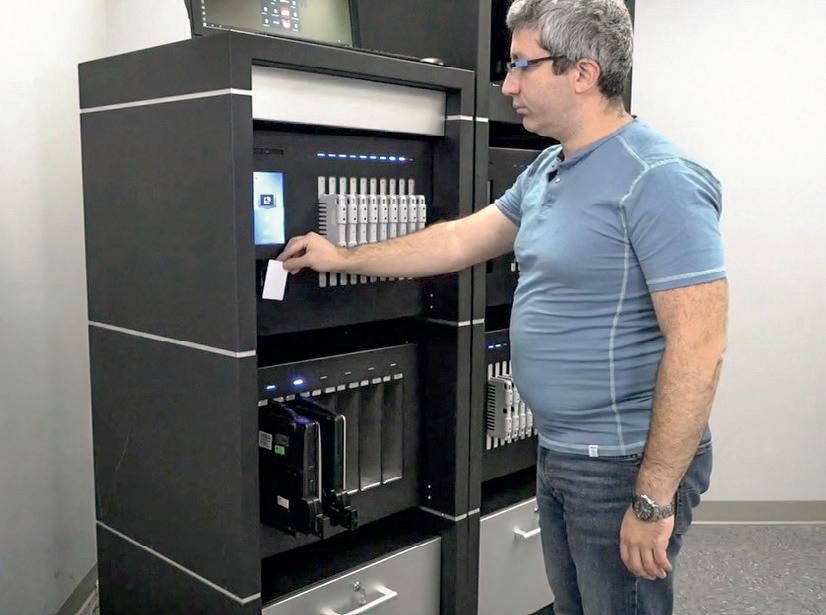
THE MOVE FROM PAPER TO MOBILE
Air Canada first introduced iPads on its Boeing 787 Dreamliners for their entry into service. The goal was to maximize flying time for the 787, which meant maintenance turnaround time needed to be the lowest it could be for any widebody aircraft. To achieve that, gaining as many efficiencies as possible was essential.
Prior to the introduction of iPads, when an aircraft landed, the engineer would take the aircraft defect paper logbook to the closest desk-top terminal to look up the applicable references and determine whether the defect could be deferred and the aircraft dispatched or whether the aircraft would have to be grounded until that defect was resolved. Mobility allowed the adoption of Apps to access information pertinent to the airworthiness of the aircraft; and offered the flexibility to complete all maintenance tasks safely on board the aircraft (as images above) without having to disembark or lose time walking to a desktop computer. It has allowed engineers to fix or legally defer defects faster, which has led to an increase in ‘first-time fix’ rates and a reduction in deferrals into the planning process; ultimately improving aircraft reliability.
The 787 represented a step change in aircraft technology and was well suited to the introduction of a proof of concept for new technologies and processes. As a result of successful implementation of the proof of concept, Air Canada rolled out these new technologies and solutions to all other aircraft types.
As an entirely new concept in aircraft design and the ‘smartest’ aircraft to date at its time, the 787 presented a challenge in the maintenance turnaround and, as Boeing acknowledged, Air Canada achieved the highest levels of reliability among operators of the type. Much of that has to do with the amount of time that has been given back to the aircraft maintenance engineers who can now stay with the aircraft throughout a turn as opposed to spending time on a desk-top terminal.
The Proof of Concept
Initially, the Proof of Concept (PoC) was to showcase the benefits of having all maintenance procedures/recordings done on the wing. The benefits were clear, but the PoC helped iron out several core issues.
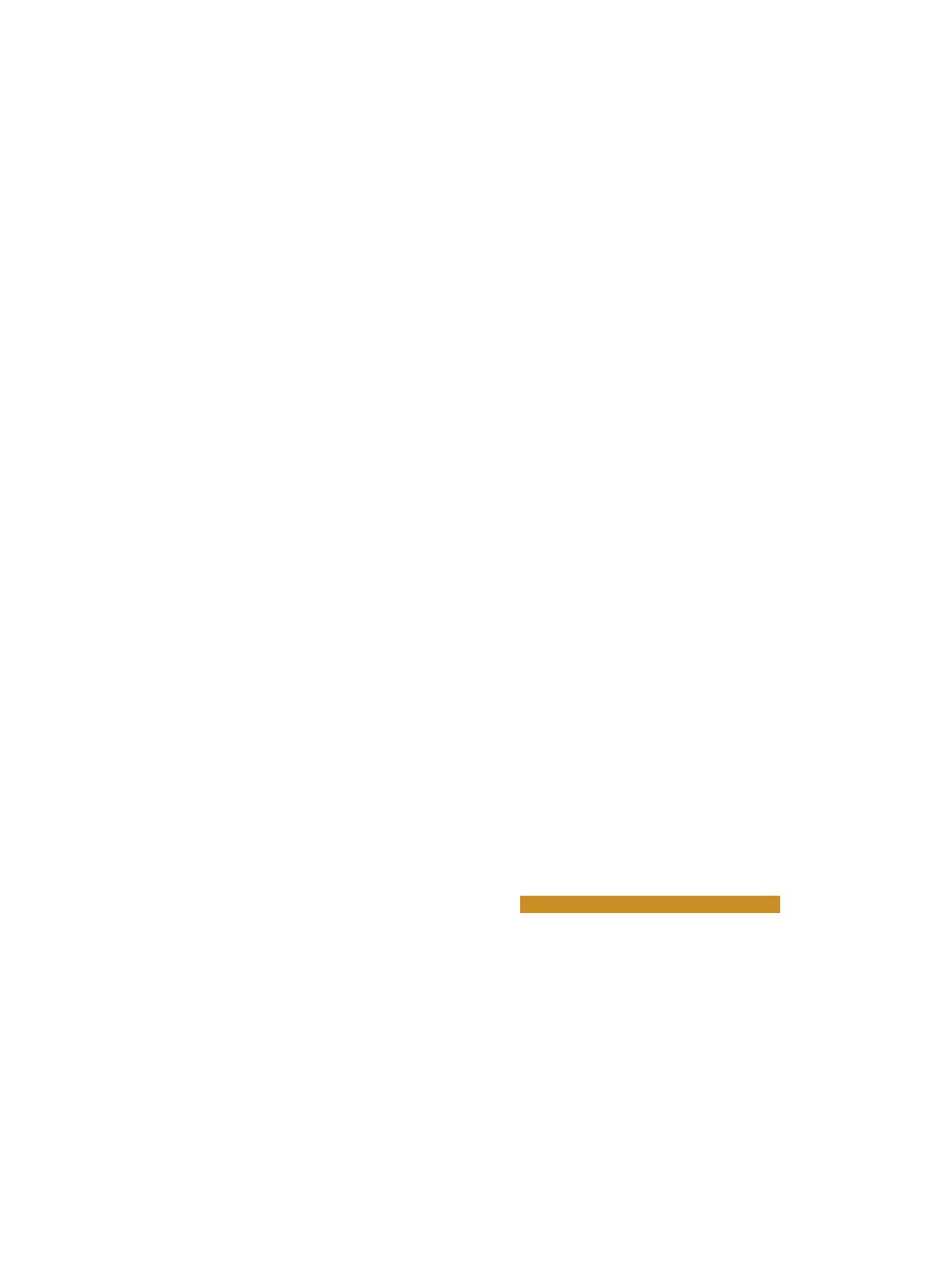
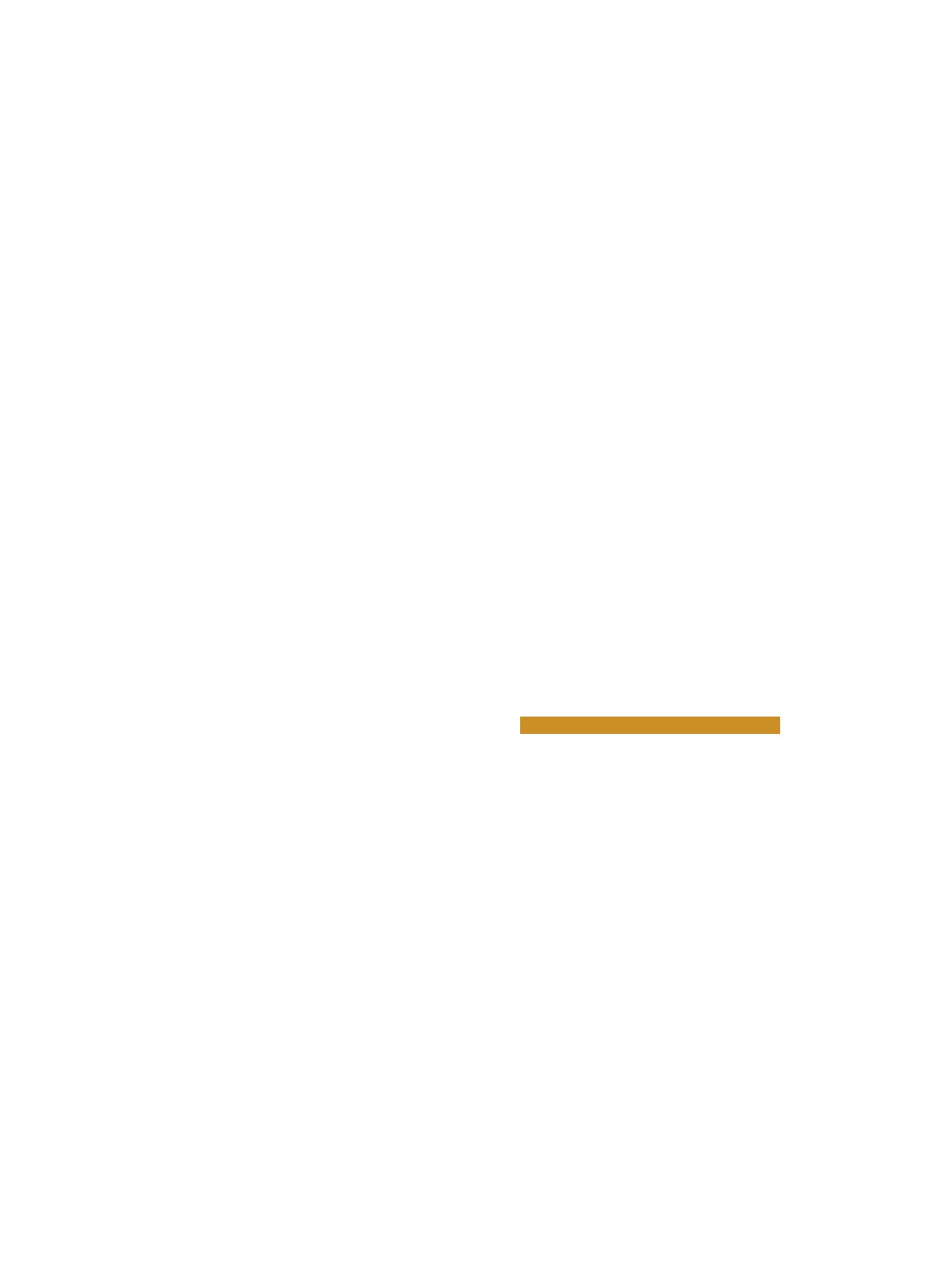
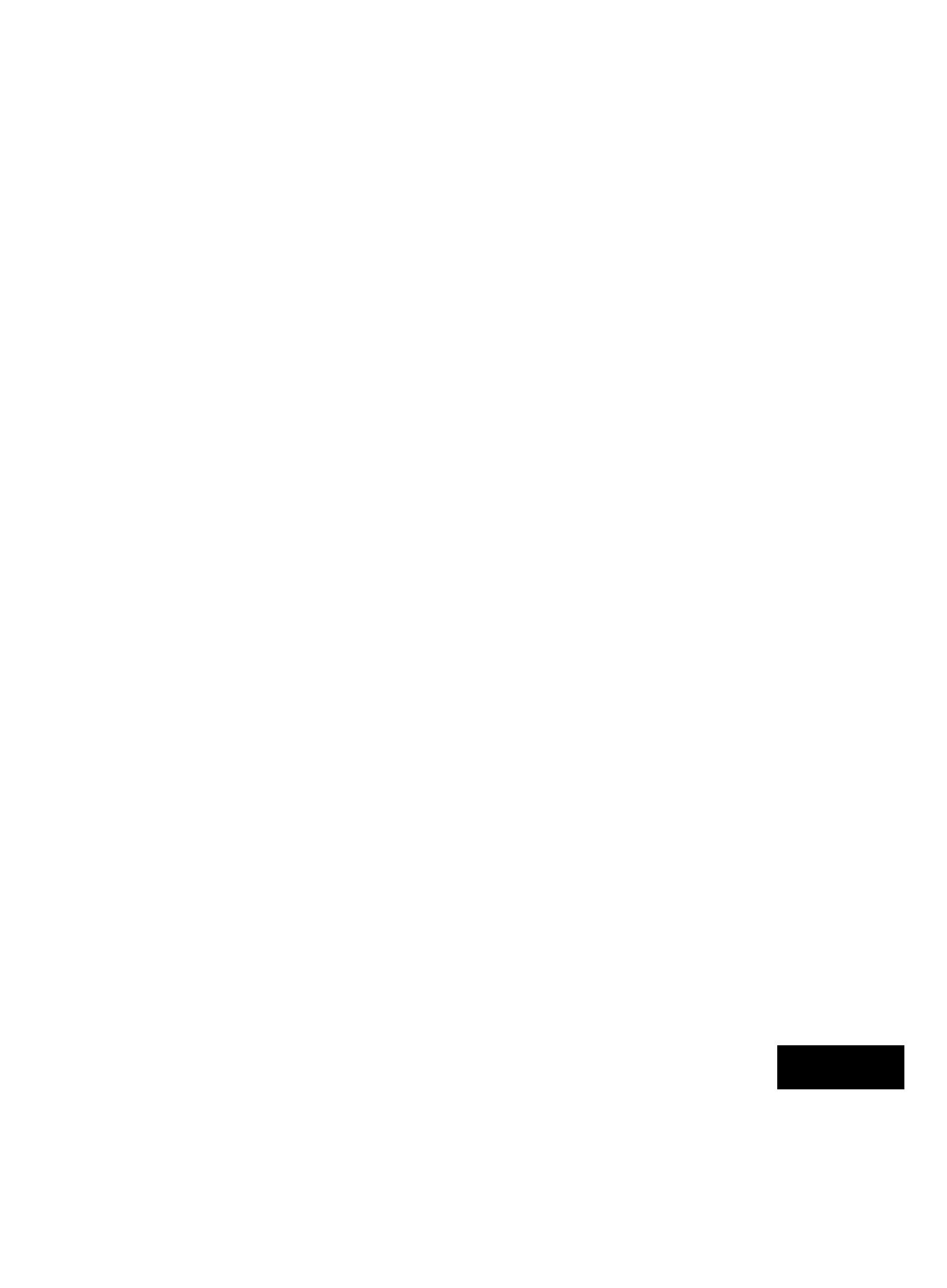
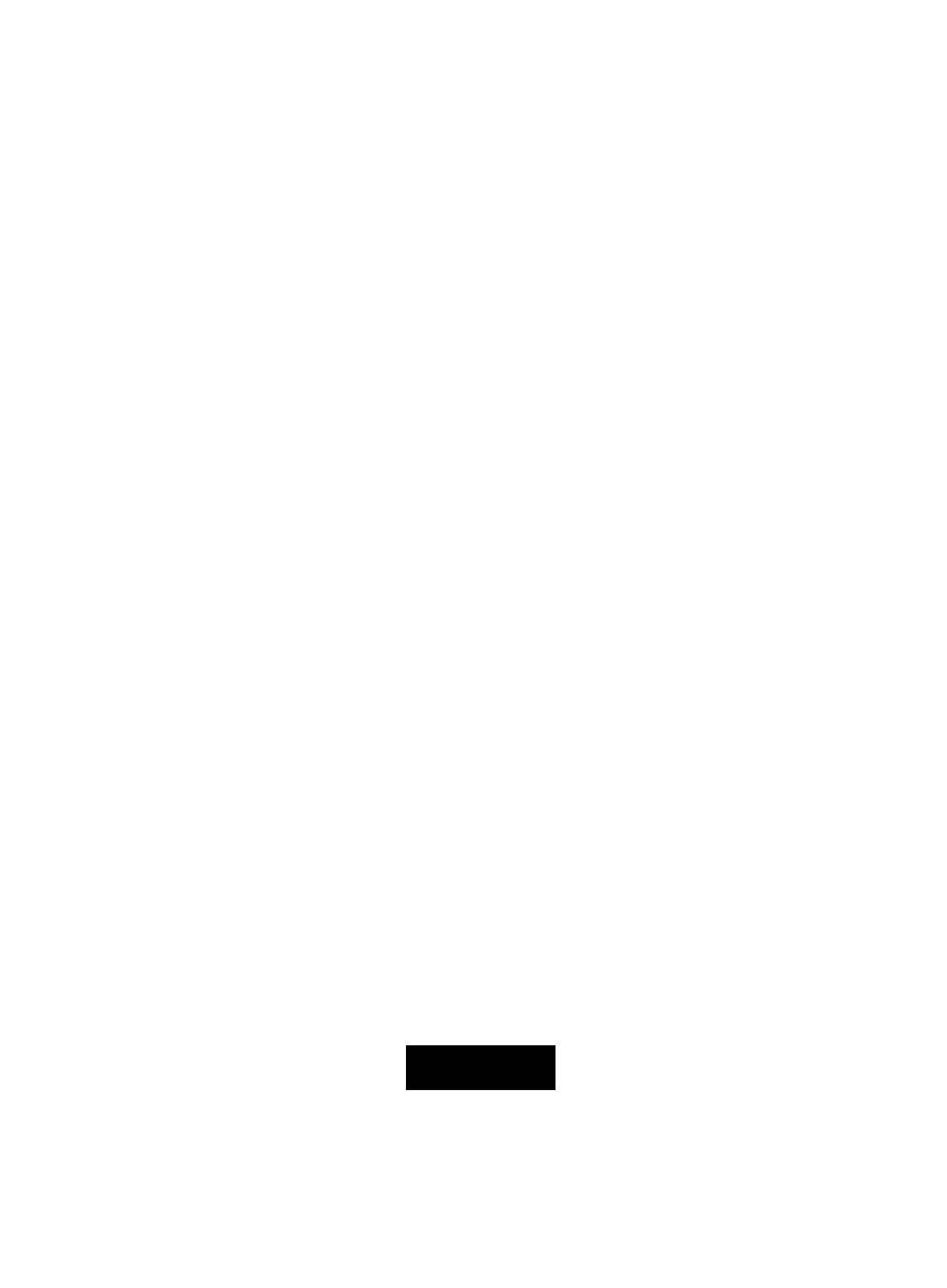
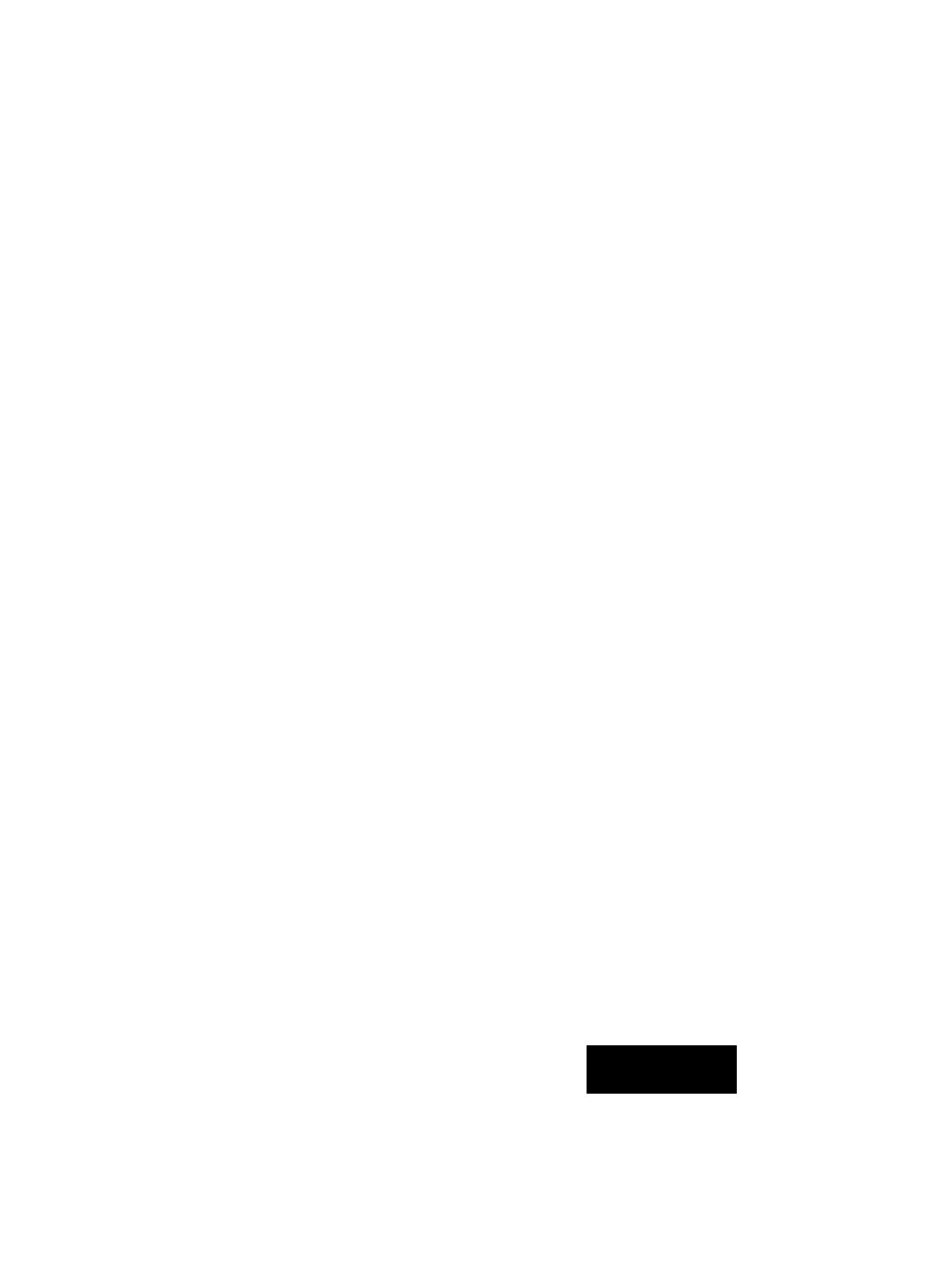
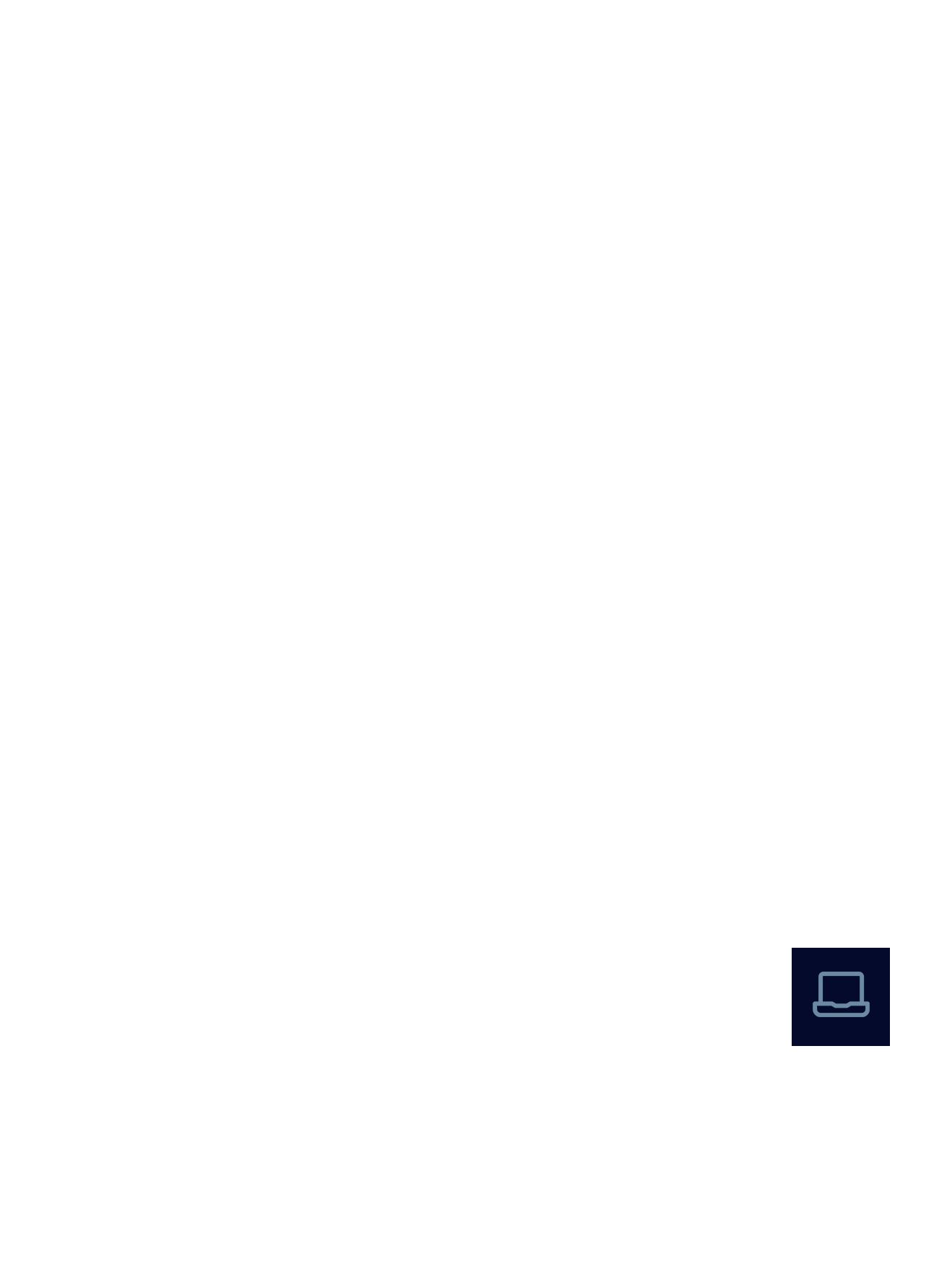
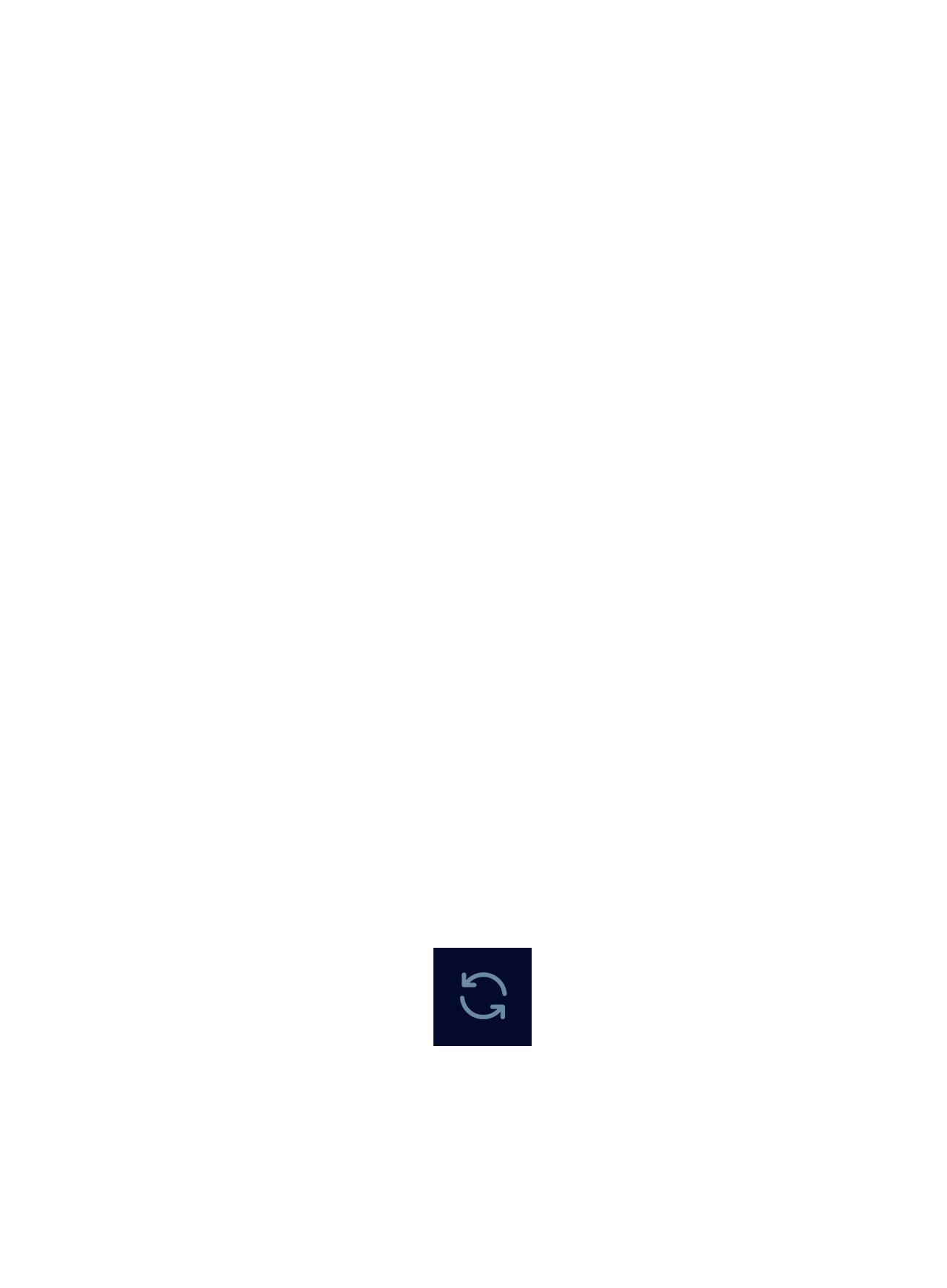
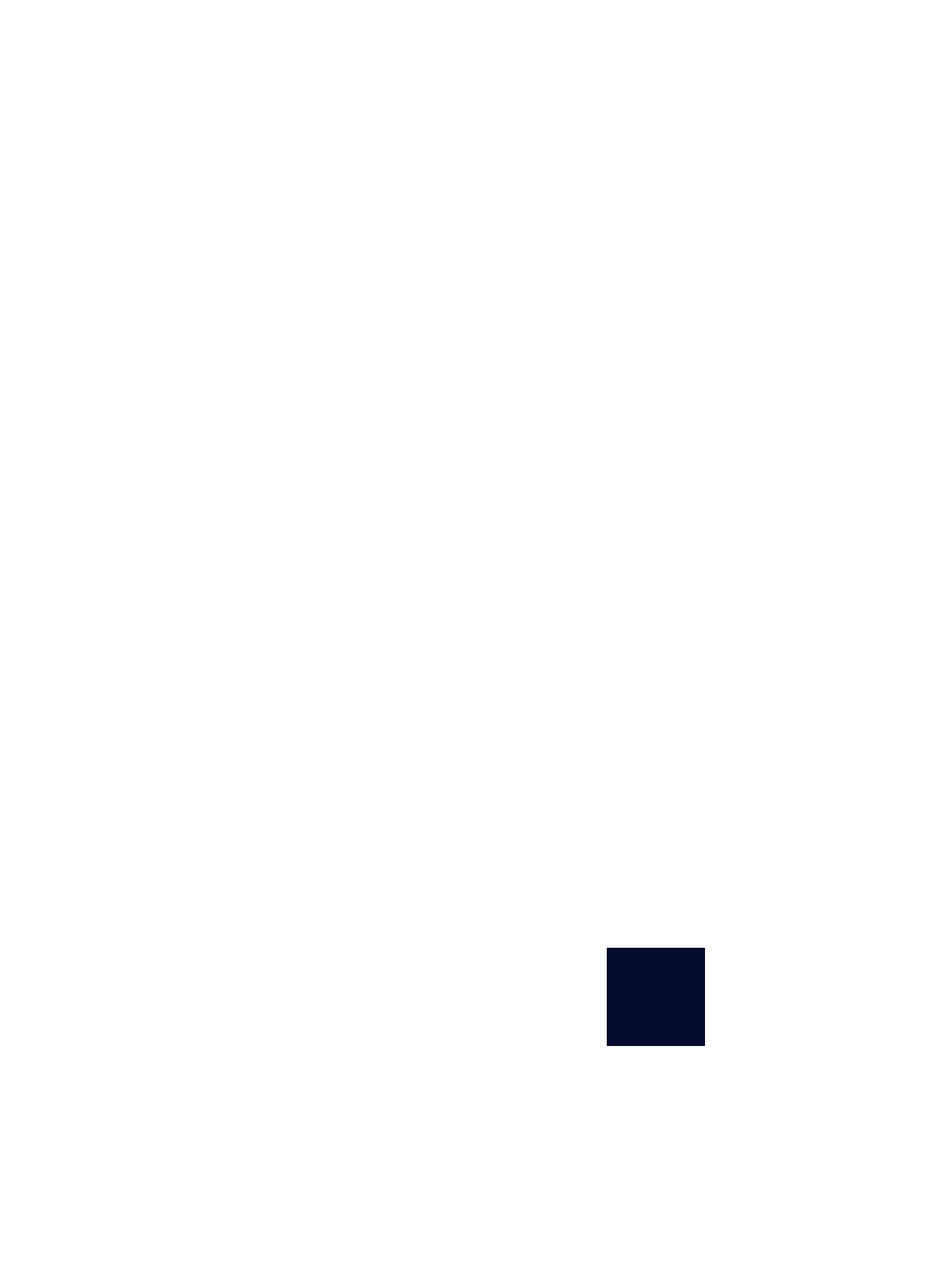
One of the biggest criteria for any aviation regulatory body is to maintain synchronicity across all technical publications. Working from the latest and same documentation is a requirement of Transport Canada. Once the OEM publishes a revision to the aircraft maintenance manual, it would be impossible for the revision to be adopted across every platform that an airline operates that same day. When those revisions are sent, operators will also add airline specific content to the revisions and then publish them. This set of documentation can be as large 35GB, making it virtually impossible to synchronize a large fleet of devices seamlessly and efficiently. With the 787’s entry into service, Air Canada found that maintaining synchronicity on all iPads in the fleets was much too cumbersome. In addition, the IT team needed to plan the OS update and the application update, and ensure their compatibility. This is where the partnership with M3 Solutions and their Platform was introduced. It fully automated all of these processes.
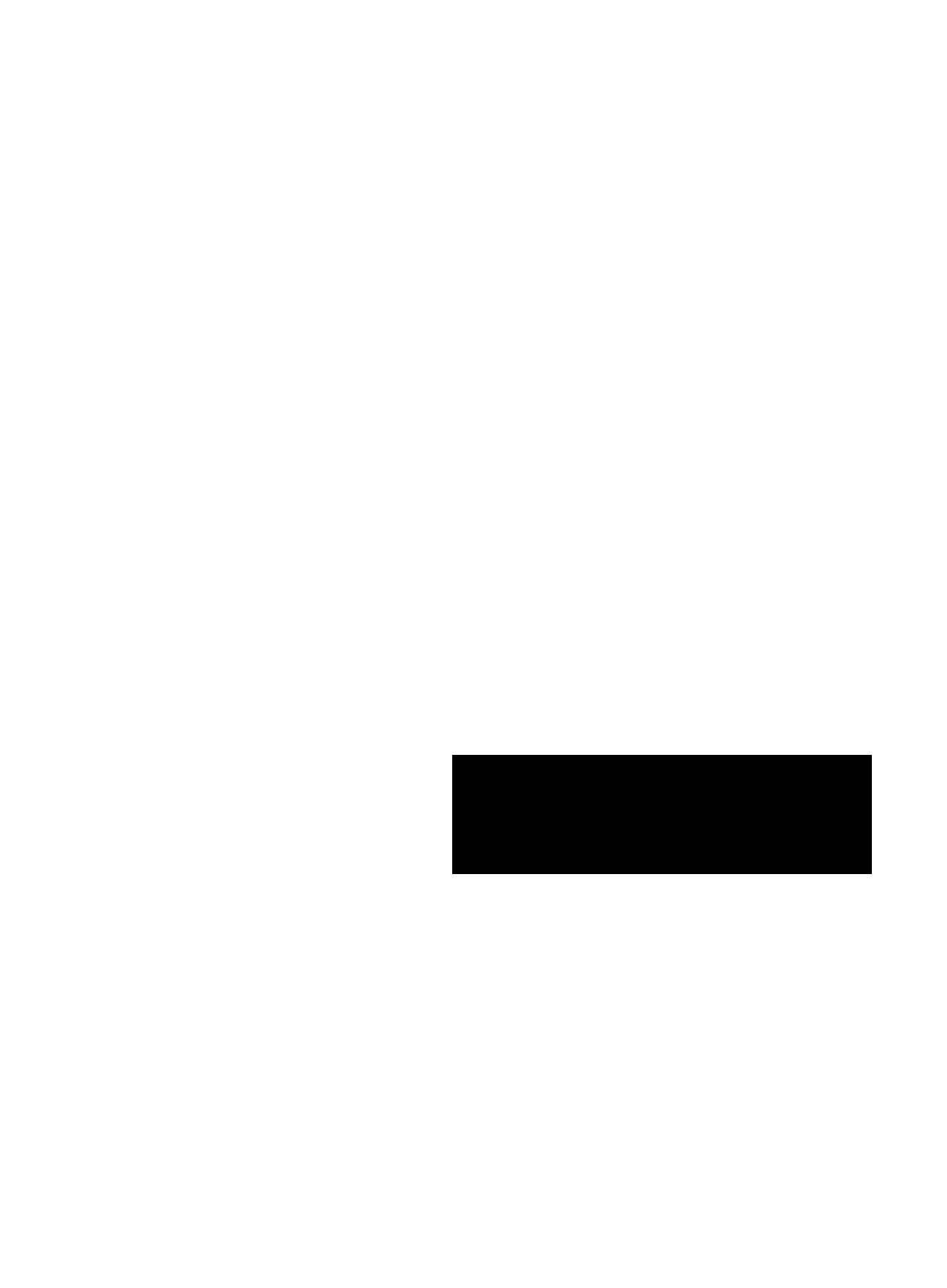

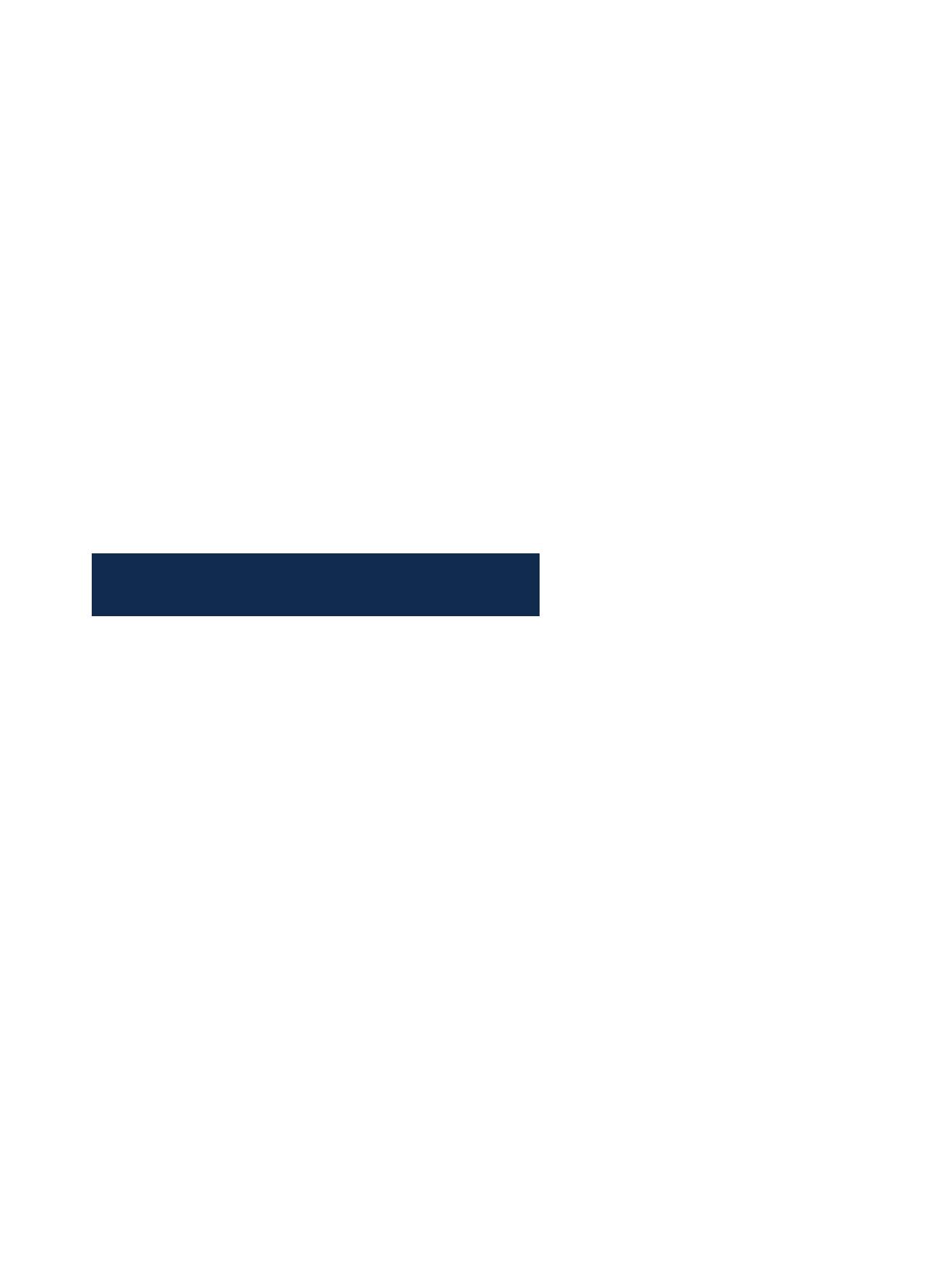
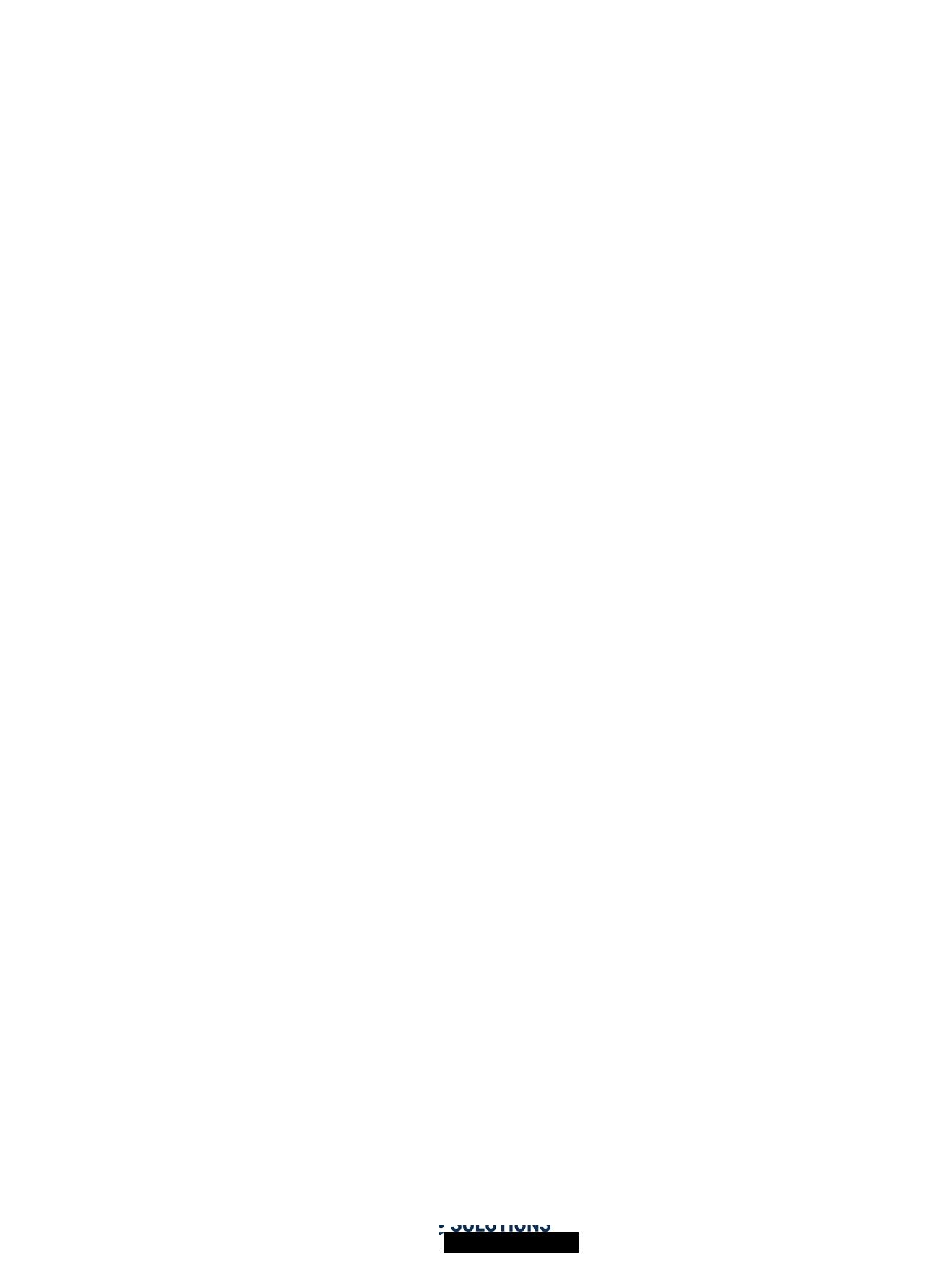
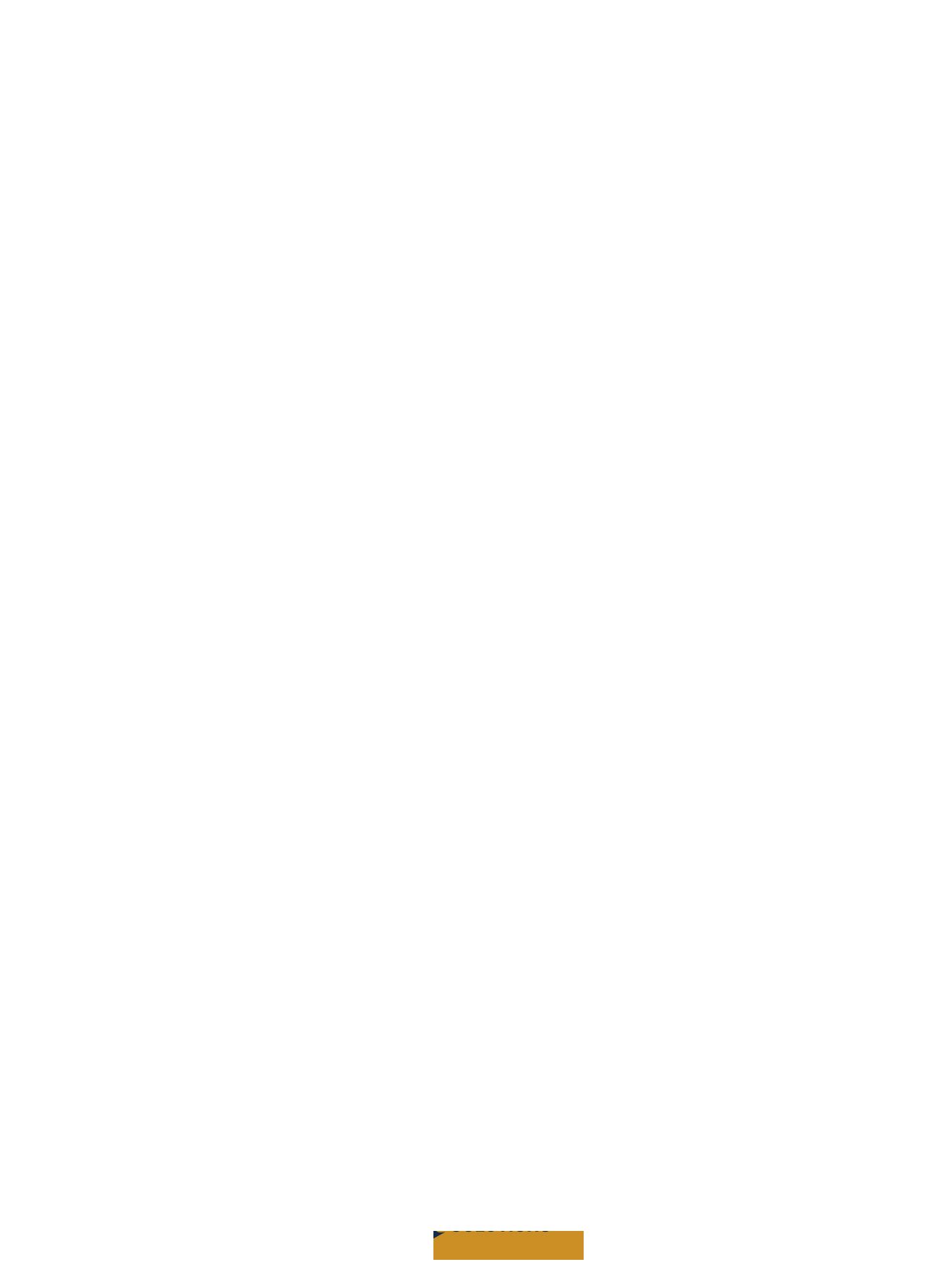
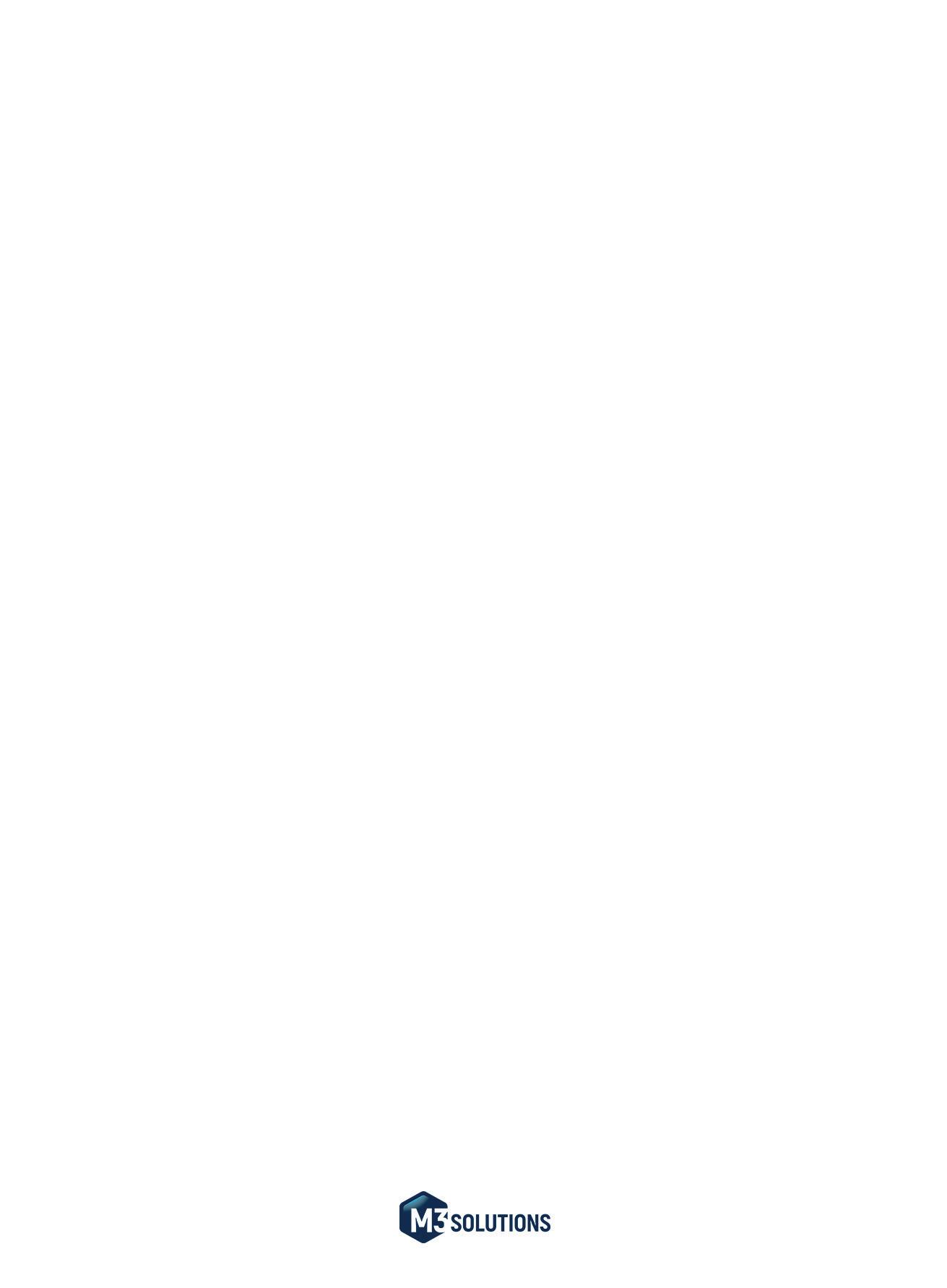
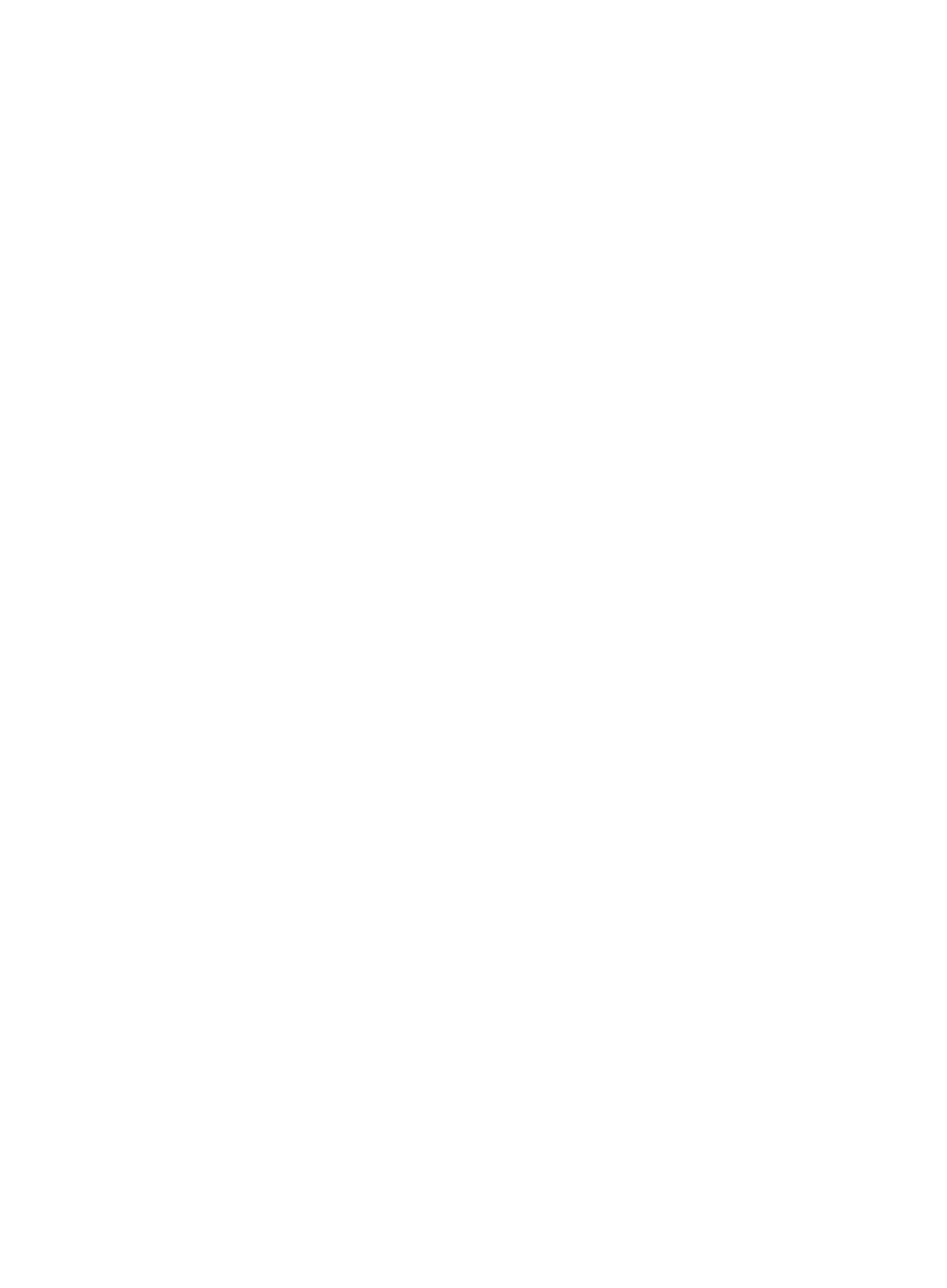
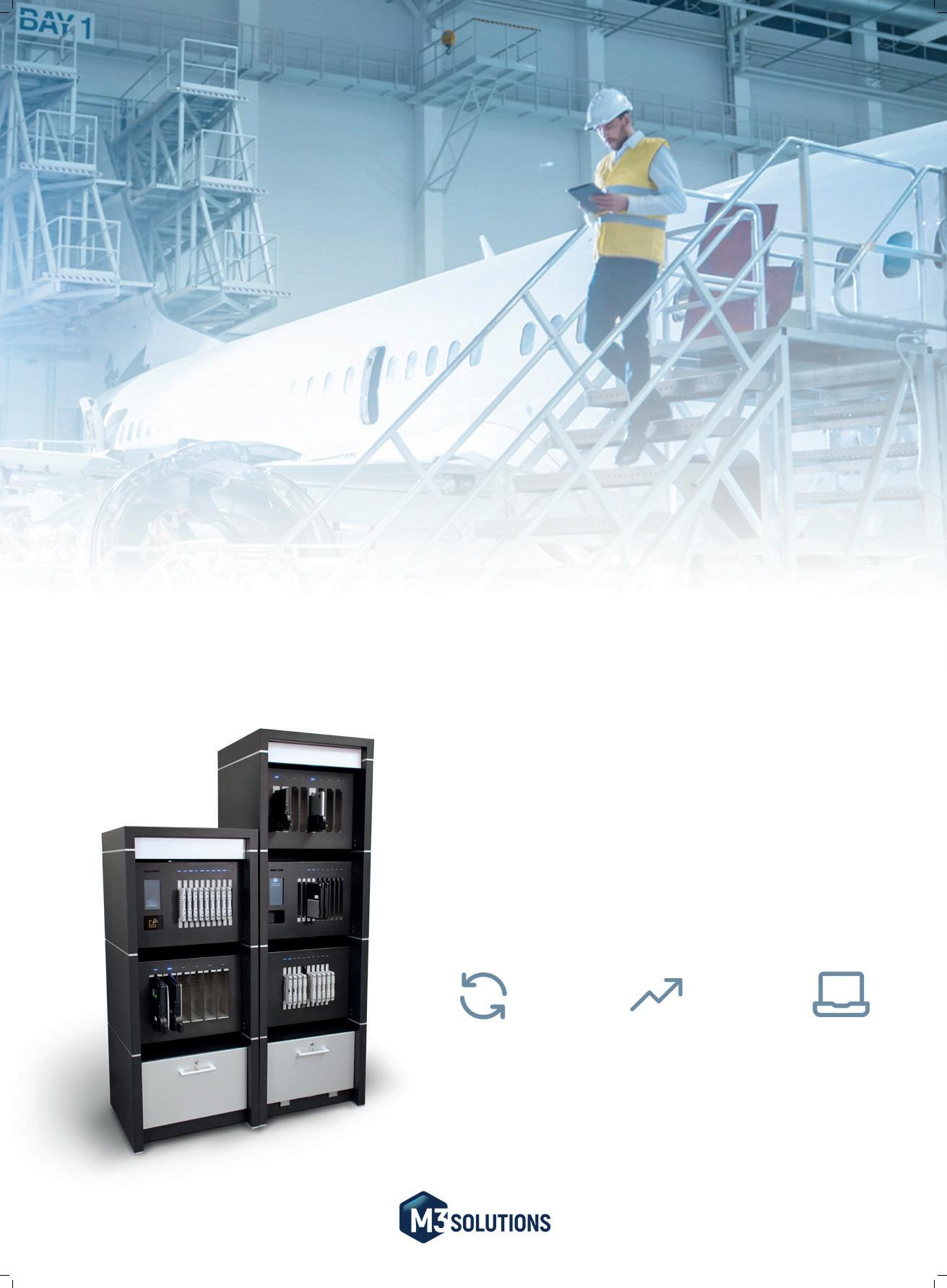
HANDLING DEFECTS
Notwithstanding that, the original business case was proven in the sense that our technical dispatch reliability improved. Engineers no longer had to spend time returning to the desktop computer to ensure compliance when deferring defects: now, everything can be done on wing. Engineers have all the maintenance manuals in their hands, with the ability to action a defect on wing which has increased our proficiencies.
M3 PLATFORM
Device management is complex, M3 Solutions makes it simple.
Bring your fleet of devices together with one platform for a holistic IT solution to ensure all your mission critical tools remain up-to-date, compliant, certified, and ready for business.
REVISIONS AND UPDATES
We discovered that it would take an IT resource one week to implement revisions or updates on just 25 devices. Air Canada sees approximately three revisions per month (36 per year) for different fleets. That fact alone supported a good business case to introduce third-party management of the devices even before taking account of the regulatory aspect.
Today, Air Canada Maintenance has more than 500 iPads in operation making it simply impossible to manage that large a fleet without appropriate automation enabled by the M3 Platform. Also, although this article refers to the Technical
Synchronicity across all devices Increase operational efficiency Maximize device readiness
www.m3-solutions.net
publication updates, there are, of course, many more to consider such as the software suite of Trax (Quickturn and Task Control), updated daily, as well as iTIMS which is an app built by Interfacing to allow for the housing of our component maintenance manuals as well as our engineering authorization work flow.
THE CHALLENGES
Running several fleets of different devices poses several challenges for IT management.
Safety and compliance
Today’s aircraft are increasingly sophisticated and technically advanced. The amount of documentation needed to outline every aspect of an aircraft’s maintenance has increased tenfold since the days of printed maintenance manuals. Aircraft manufacturers are constantly updating their maintenance documentation to ensure compliance and adherence to safety regulations. In addition to monthly technical publications which are regularly supplied by aircraft manufacturers, there are also unscheduled releases as often as required to catch critical maintenance deficiencies in the equipment and prevent any failures. In both instances, the challenges surrounding how the information is transmitted and how quickly it can be distributed across MRO teams, in every location around the world, to ensure proper compliance across the entire fleet of aircraft, become critical.
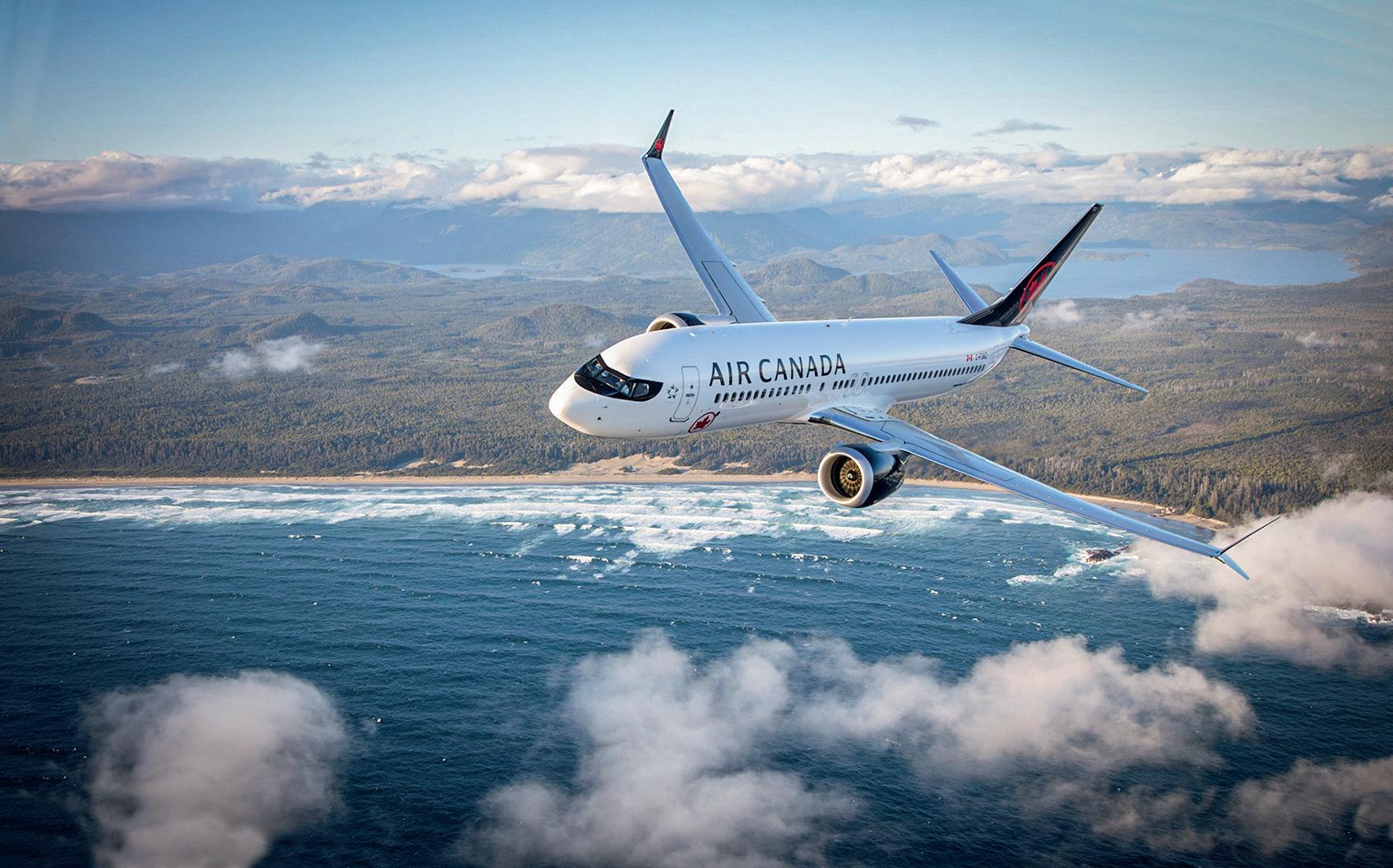
Maintaining synchronicity
With Air Canada maintenance crews operating in multiple locations worldwide and servicing several aircraft models, maintaining synchronization across all of their mobile devices can pose a significant challenge. This is not only to ensure the aircraft’s maintenance documentation is up to date, but that the devices’ OS matches the requirements of the mobile app which provides that information, most often provided from the aircraft manufacturer. If different tablets have different OS versions, then errors may occur which can impact the smooth operation of maintenance teams and result in longer aircraft turns, not to mention added strain on IT resources tasked with resolving those errors.
Maximize IT resources
Updating every device so they have the right operating system, app version and latest documentation is often a time-consuming process. Doing this manually can put an enormous strain on any I.T. department and require multiple people to achieve it in a timely manner. Furthermore, because of the delays associated with this update process, ensuring that maintenance crews all have synchronized documentation on their device, right when the update is scheduled for release, is virtually impossible.
Security and control
It’s easy to imagine how sensitive the information regarding an aircraft’s inner workings can be. As such, the devices used to communicate this information need to be secured in the most efficient way. The airline’s administrators must also be able to track each device and have detailed reports of where it was used and by whom.
THE SOLUTION
M3 Solutions’ innovative technology eliminates the legwork involved in synchronizing a mobile device ecosystem by streamlining content deployment, complex data structures and installations required for maintenance crews to perform their jobs. The platform hosts each device and is uniquely tailored to process updates, install certificates, wipe clean after each use, charge the devices, and much more. The moment a user picks up the device they know it will have the same installations and same version of technical documentation that any other user would have in their organization. Within the M3 platform, access is controlled to devices via RFID, barcode and NFC readers – ensuring all devices are physically secured and traceable (figure 1). Ultimately, it’s a platform that bears the load of an IT team, with a worldwide support network ready to troubleshoot from anywhere.
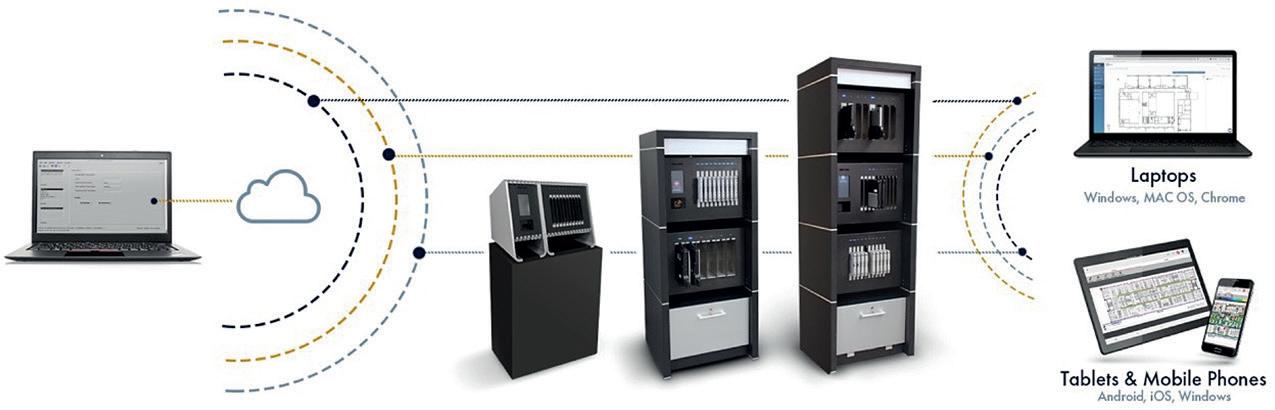
CONCLUSION
In addition to physical security, access control, and inventory tracking capabilities, deploying the M3 Platform significantly helped streamline Air Canada’s maintenance operations by eliminating delays to synchronize all devices for various teams to use. We would be hard-pressed to find another industry where the adage, ‘time is money’ is as applicable as it is in aviation. For Air Canada, the M3 Platform helped us save both time and money.
THE RESULTS
Air Canada saw significant gains as a result of using the M3 Platform, including current functionality: • Seamlessly manage multiple device-types including tablets and UMD running different OS, in the same installation. • Deploy new OS or configuration images remotely and unattended, across the entire network. Manage the content on all devices and ensure it is complete and always up to date. • Gate the deployment of new revisions of apps to ensure compatibility with the OS version deployed. • Physically control access to portable devices, monitor the users and their usage with administrator permissions and the system management dashboard. • Schedule or deploy content in real-time, to some or all devices, anywhere in the world, within minutes and without IT resource intervention (remote and unattended content deployment). • Retrieve accurate device and system monitoring, ad-hoc reporting, and transaction auditing. • Reduce IT and device inventory costs immediately. Overall system ROI (return on investment) was achieved within months of installation.
THE BENEFITS
The requirement to maintain synchronicity with technical publications and the latest reference documents is a Transport Canada requirement. With 35 gigabytes of monthly updates, we quickly discovered it would not be possible to maintain synchronicity unless we had a controlled mechanism such as the M3 Platform.
KEITH DUGAS
Keith Dugas, Director, Maintenance AI and Connected Operations has the current mandate to build AI solutions for Air Canada’s Operations. Keith has worked for Air Canada for 14 years, where he has had business lead responsibility for Air Canada’s Supply Chain transition to Trax from the airline’s legacy maintenance system, as well as responsibility for deployment of logistics and operations continuous improvement initiatives. Most recently, before AI, Keith was the business lead to digitalize Air Canada’s line maintenance paper-based processes, having started his career in AOG operations and progressed into management from there.
AIR CANADA
Air Canada is Canada’s largest airline, the country’s flag carrier and a founding member of Star Alliance, the world’s most comprehensive air transportation network, celebrating its 25thanniversary in 2022. Air Canada provides scheduled passenger service directly to 51 airports in Canada, 51 in the United States and 86 internationally. It has a fleet of more than 332 aircraft (179 mainline, 39 Rouge and 114 Express), which is also one of the youngest, most fuel efficient and environmentally friendly in the world. It includes, Boeing 737, 767, 777 and 787 types; Airbus A220, A319, A320, A321 and A330; Embraer 175; Mitsubishi CRJ; and De Havilland Dash 8-400.
INTERACTIVE GIVE US YOUR OPINION
CLICK HERE TO POST YOUR COMMENT
INTERACTIVE SUBSCRIBE HERE
CLICK HERE TO READ ALL FUTURE EDITIONS