A.B.C
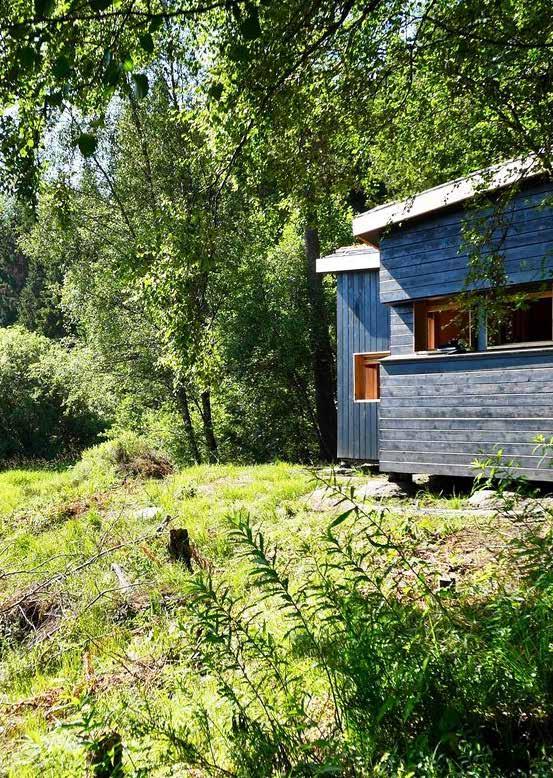
Alexander Baldwin Cole Architect

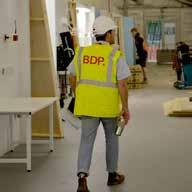
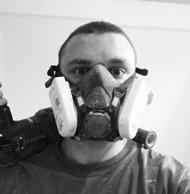
Alexander Baldwin Cole Architect
My name is Alexander Baldwin-Cole. Born in Essex, England, 23/06/1993. I know it sounds like the ultimate of cliché’s but “As long as I can remember I have wanted to study Architectural Design”. It’s probably the same old story but its mine. A father in the construction business, a mother in the creative side. Put 1 + 1 together = Architecture or something similar within the design field. Unlike many of my piers having a pretty strong concept of the field I wanted to progress into made things easy when university began to loom.
I ended up Studying my Undergraduate Architecture Degree at University of Kent’s Canterbury Campus and stayed in Canterbury for my Part I placement year. I worked for small architectural firm called Clague. During which I worked through a variety of projects across various RIBA stages of work.
Towards the end of my year out I decided not to delay and looked to return to studying for my Masters in Architecture. The only issues were that I was looking for a change from Canterbury, looking at my original University Applications I found an old favourite in the pile, Newcastle. A few visits and a successful portfolio and interview later, the next chapter in my career began. Two years on, having learnt a lot about design and myself I started to gain a clearer idea of the path my future could take. The most important project to me was that of Linked Research – Live Build project, its realistic nature drew me instantly and became all that mattered in my eyes.
After some time away from Architecture I decided to relocate my life to Bristol based on finding employment at a Design & Build Architecture firm called moon. Here I worked not only in the office as a Part II Architectural Assistant, but also gained experience on-site before moving to the Internationally known BDP. I’m currently still at BDP, but having passed my Part III examinations under their watchful eyes I feel it’s time to move on.
Over the past 11 years I have worked on and led projects throughout all RIBA Work Stages, across numerous project types and at varying scales. I’ve learnt how to work efficiently within large project groups, use my own initiative to progress work individually and to lead project teams.
I’ve always been a keen fabricator and have strived to gain in my opinion vital on-site experience. I’ve worked in a restoration garage, on a gas rig, part of a maintenance team at a grand hotel and as a builder throughout gaps in my architectural career. I’ve actively sought-after education and career placements which offered me the opportunity to construct my own designs. I feel all designers would greatly benefit from similar experiences, as it’s this variety of skills which has made me a proficient designer. Due to my skillsets, interests and experiences exceeding that of a standard Architectural designer, I’ve often found I’ve formed far stronger relationships with builders and other external parties (e.g. Engineers, Contractors and Fabricators) than that of my peers.
Throughout the portfolio you will find a range of projects which indicate the broad range of design, fabrication and building experience I’ve obtained from a variety of placements and projects.
Thank You for your consideration
RCHT-Orthotics - Technical Design & On-Site Coordination
Project Architect - Stride Treglown
August 23 -Current Position
3/4 HART STREET- Feasibility
Private Work - During Part III Placement
June 23 - Augustl 23
WHILTSHIRE CABIN - Hands On Design & Fabrication
Private Work - During Part II Placement
March 21 - April 21
RGH-PHARMACY - Feasibility & Technical Design
Architect - BDP
March 19 -August 22
CARDIFF FIELD PARK HOSPITAL - Technical Design & SIte Coordination
Part 2 Placement - BDP
March 19 -August 22
SHAPLAND - Planning, Technical Design & On-Site Coordination
Part 2 Placement - Moon - Architect & Builder - Bristol
July 18 - March 19
SUNNYMOUNT - Feasibility
Part 2 Placement - Moon - Architect & Builder - Bristol
July 18 - March 19
This project has been my main focus for the last 8 months as I’ve been facilitating the role of Lead Project Architect on this new healthcare extension project based in Penzance, Cornwall. A constrained project programme caused a split project timeline, with some of packages being pushed through to manufacture while other elements were held to assess redesign opportunities due to the client’s needs changing since commencement of Stage 4B.
The fire Strategy and detailing has been a specifically complex element of this project, as it often is with all Healthcare projects and is a serious topic on the lips of all concerned Architects currently post Grenfell. The MMC / Pre-Fab ambition of the project to minimise on-site disruption to the existing hospital has caused some complex details needing to be thought through, while the delivery order / phasing of install has tied our hands from being able to utilise standard solutions.
Owning this project for the past few months has been a highly stressful period of time, while simultaneously has allowed me to step up into a role of higher responsibility and prove to myself, my colleague and those within the Project Design Team that I have every right to be in this position of responsibility. I’ve learned a great deal and have been lucky enough to experience new methods of collaboration and intricate on-site management of problem solving.
• Yeovill-Therapies (Healthcare Refurbishment and
• Extension) RIBA Stages 2-4
• Newquay & Launceston School (Modular conversion to Traditional Construction) RIBA STage 4
• Derroford-Ward Extension (Healthcare Refurbishment and Extension) RIBA Stages 1-4
• Spur-Interior Design (Commercial Office) Stage 2-3
I was approached by a Private Client to explore some internally remodelling options for a private residential property, initially looking at feasibility options and then assisting with detailed the detailed design stage and being a defacto project manager once a builder had been appointed.
Minimal impact on the existing home and cost were a key factor of the project. The aim was to utilise a rear sunroom currently being underutilised as an office and convert it into a utility room. Access directly off the kitchen was planned while looking to update the kitchen and bring some contemporary elements into their home. The clients had two large dogs which they loved deeply but had nowhere to wash them down, so wanted a buffer zone between outside and the warm zones of the house.
Full Person Shower in Raised Tray, with some half height tiled walls to enable dog washing aswell // Utility Door Flipped to enable hanging storage within Utility room (Coat & Boot Racks) // Recessed Slidding Door built into Storage Units / Shelves. This will permit more connection to the Utility room, while remaining closeable // Full width Bi-Folding Doors. Theres multiple orientations these can be designed to. I’d suggest a system which permits one to be opened individual of the rest, while also allowing all to be folded away
Option 4 _“A Long View Through” : I looked to keep the extension behind the previous extension line, as passing this will make the new addition read weirdly in my opinion. This first option looks at having the WC / Shower alongside the wall between the Living Room. The benefits of this are that it keeps the new sanitaryware adjacent to the existing drainage. A Raised floor around the shower room is to help minimise excessive groundworks and enable the required drainage falls for the new sanitaryware. With the lean-to structure being extended, the location of the breakthrough to the kitchen is more flexible in terms of location.
At the beginning of spring 2021, a close friend approached me to help kit out a heritage Sheppard’s hut for use as an Airbnb / glamping accommodation. A design acquaintance and I jumped at this idea, not only due to being able to help our friend but due to it offering up an opportunity to test some percolating design ideas we’d discussed for van conversions previously. The project was completed within 5 days across three weekends, which included everything from planning the design, acquiring the materials and commencing and subsequently finishing the design work.
We decided it was essential that we made the space as accessible to all people as possible and that the changing of the bed to a table needed to be designed to be as simple and elegant as we could. The idea of using counterweighted pulley system was chosen upon acquiring an old sash window weight, which brought an element of the unique to the design while also simplifying the process.
This forms my latest project that I’ve run at BDP, during which I acted as the lead architectural designer working through the layout and technical problems, while my associate covered the meetings with the trust and ran the Principal Designer elements of the project.
Despite the relatively small scale of the department (approx. 752m2) this refurbishment project proved very challenging. One of the main issues was the updated requirements (room sizes) of the renewed department exceeded that of the existing, so finding areas where we could double up or even derogate spaces was an instant challenge. Next was trying to overlay the production route through the irregular shaped department while incorporating the existing services cores, structural grids, windows and aiming to retain some of the existing rooms for cost reasons.
Additional BDP Projects:
• RGH-Endoscopy (Healthcare Refurbishment) RIBA Stages 1-3
• RGH-Decontamination Unit (Healthcare Refurbishment) RIBA Stages 1-3
• Centre House (Commercial Residential New Build) Stage 4
• Thames Valley Police Station (Civic Refurbishment) Stage 4/5
• Transport for Wales Bus Hub (Transport New Build) Stage 1-3
Back in 2009 while applying for my place at university to study Architecture I never would have thought 11 years later I’d have been part of a collective effort across 25+ companies to convert a sports stadium into an emergency surge hospital to help cope with a global pandemic. It is just a staggering statement, even writing it down now it still sounds absurd, but it happened, and it happened very quickly.
This project formed the culmination of all my design experience to date. I was able to bridge the gap between the clinical design teams and the on-site sub-contractors and labourers; I worked the problems from both sides to find the most effective solution. I am not just a designer, I am a fabricator too and this project proved to me once again the value of having experiences across both those fields when it comes to success in the field of architecture.
Upon my arrival at BDP, I was thrown in at the deep end in two regards, the first was BIM. Secondly and more importantly, I was thrown into a complex Hospital project consisting of a three storey new build Therapies department and the relocation and refurbishment of an Acute Assesment Hub. I had never touched the health sector previously and soon found the complexities of its requirements far exceeded anything I’d experienced to date.
Part way through the project my role changed, with my associate moving to Cardiff to set up a new office, I became the senior architectural designer in charge of running both projects out of the Bristol office. When time came to run the technical design stage, I was the main point of call for all queries. During this period I rarely had time to produce any drawings myself, instead I became a coordinator of information packs and a manager of people. I’d often have a que of people at my desk asking for direction, to sign off of details or I would be in meetings working through cost saving options with the main contractor. It was a hectic and stressful time, but one in which I fully rose to the occasion and flourished under the pressure.
Early on at my time at Moon I was handed over a stand-alone outhouse project, it became my job to work up the Planning, Technical drawings and oversee the Project on Site, under supervision of course. It was seen as an ideal project for me to cut me teeth on in the firm, a way of getting to know how Moon worked and to test my detailed design skills. What was supposed to be a straight forward project, ended up being a tightly constrained, fast-moving project with a number of redesigns and issues. All of this made it even more perfect for me to undertake,alongside a number other concept and planning packages.
The build was approved under permitted development, which stipulated a height constraint of 3m. This along with some aesthetic requirements caused elements of the detailling to be highly complex.
One of the more aesthetic orientated constraints was the front edge detail (41.02), where we aimed to keep the leading edge of the building as elegant as possible. Initially the aluminium PFC channel specified for fabrication and construction below (46.01 - .02), was going to be a structural steel channel. Instead a series of Glulam’s we’re to be used as the primary roof and front edge structure (10.03), this both simplified and complexed the detail.
During the lengthy foundation stage, we had the site team pre-fabricate a number of the timber wall panels. This helped us for a number of reasons; firstly, it kept the client happy by letting her see constant progress. Secondly this allowed us to accurately design and issue for fabrication the roof design. We did design in elements of flexibility, by leaving out a number of panels. This allowed for elements of the project to be finalised whist work was underway on-site.
Site Photos - Roof Structure
One of the more complex elements of this projects has for the start been the roof & front channel detail. An early agreement with the client to keep the front edge as elegant as possible, with the roof only stepping down to its full thickness 400mm passed the windows internally posed a number of intricate details. Eventually hanging a number of Posi-joists off the central running glulam proved to be the answer. This allowed depth of roof structure for a series of gym mounts to be installed on the ceiling, while keeping the internal head room sufficient and the overall building height under the 3m constraint under permitted development.
The clients asked Moon to explore replacing an existing timber lean-to conservatory at the rear of their property, with an intervention more in keeping with the classic styling of the house. The immediate issues associated with the client’s ambition to completely block any view of their neighbour’s extension, was that it pushed the size of the proposed to a scale unsuitable to tie in with the existing.
During the lead up to the initial concept presentation meeting, myself and the architectural director worked through a number of alternative options. Still innkeeping with the overall brief presented to us by the clients, we began to explore alternative options at a subtler scale.
In addition to the extension attached to the rear of the property, I was asked to explore a variety of options for a garden pavilion. The idea being that eventually the designs of both the extension and pavilion would begin to coincide.
This project, run over both years of Masters in Newcastle, consisted of Researching, Planning, Technically Resolving and then finally Constructing a number of leisure / education pavilions. The structures form part of a wider Bakethin Masterplan, for Kielder Water and Forest Park Development Trust and were designed in conjunction with Kielder Art and Architecture. The project was funded by Heritage Lottery Fund North East, while the high level of spec was assisted by the labour coming from our group of students and transport costs being covered by Newcastle University APL. We were asked by the client to provide a coherent design package, which together would form a journey for visitors starting at the castle carpark and then heading towards Kielder lake. Thus, providing not just a bird watching experience but additionally aimed to meet the needs of many and reinforce the Kielder Ethos of Education Through Experience.
In order to provide options for the clients, we as students divided into three groups of three. The aim was for each group to explore differing design concepts, thus offering the clients a number of design approaches to choose from.
The existing hide was hidden away and rarely visited except by those who knew to seak it out. To revitalise the bird hide under the concept of Framed Views we aimed to create a new special experience, the form and orientation of the hide is focused on framing four significant views across the site. The wrapping design is expressed in the roof creating a permanent protective cover to the structure.
The design has an intentionally bold, striking form, which opposes the verticality of the tall pine trees that cover the site. The wrapped monolithic form, a theme continued from the bird hide, developed as ribbons that would fulfil the various functions required in the proposed brief. The ribbons of timber interlink forming benches, shelter, bike lock up spaces as they flow between the trees. Openings in the sheltered portion highlight the distinctive views to the canopy above.
After the initial presentation, the detailed design stage was undertaken following the feedback issued by the clients. My first job during this stage was the detailed design of the Viewpoint, making sure to design in the necessary features for the constructing of the installation.
My most challenging task of the entire live Build project was the detailing, or rather more engineering required to create the roof. A main issue included the creation of a 6.4m long beam out of maximum deliverable 4.8m beams. Then design how the beam would connect to a column and the foundations for the column. Finaly the actual roof had a very tight design ambition of showing no screws, while being top hung and over sailing the wall line.This would involve an number of intense discussions with our assigned Engineer Artem.
Due to having other responibilities during this year I couldn’t always be on-site, so during the period of time that the roof was going up I had to produce a series of construction sequence diagrams for people to continue the work on site without me. This was one of the challenging tasks of being the sole designer of the roof, in that all questions could only be directed at me. I had to constantly micro manage the construction team during this stage, while also working myself. It was nothing short of exhausting but very exhilerating when the roof all came together.
Learning from the previous Live Build Project, we learnt the value in Pre-Fabricating Elements Off-Site. This was required for the central beam due to its length and complicated design, it allowed us to acurately and cleanly construct the beam. While the use of Cut Lists throughout the project was vital to keep track of the various elements, Reduce Wastage and help us remian within our Tight Budget.
Due to confusion while on-site and one vital dimension being left off of the working roof construction drawings, elements of the Oversailing Roof would require to be pre-fabricated at both the University Workshop and the Kielder Workshop. A Scissor Joint was required to allow the roof to overhang at the ends of the birdhide, while resting on the wall line and being connected with a number of smetal plates.
This was the primary design and research module of my last year of academic study at Newcastle University. The brief had a basic outline of Investigating a Craft and then developing an Investigation Strategy to define and create a Realistic Brief. Due to my previous experience and interest in wood working I choose to investigate honest detailing with timber. My prior relationship with the area of Kielder Forrest due to my Linked Research Project, along with further research into the diminishing industry and materials available in the area led me to investigate a project based on the Cross Laminated Timber.
The Bakethin Weir, a middle point within Kielder Lake had the potential to enable a dramatic yet settled intervention into the landscape. Due to its position within a natural amphitheatre, elements of the program could be hidden away from wide views, while other aspects of the surrounding landscape can be designed into and expressed through the intervention.
Northern Industrial Axis VS Souther Leisure Axis All stages are Expressed Along the Public Facade
Leisure Elements Create Enclosures and Frame Visitors Attention Towards the Landscape
Access is Mitigated Depending on Programme
Above are serious of diagrams showing the developing of how I planned to interconnect the two main functions of my project across the site e.g. Industry vs Leisure/Education
My intervention within the site of Kielder looked to tie in with both parts of the sites existing program of Industry & Leisure / Education. Firstly, I looked to connect into the existing timber industry present within Kielder, by producing a program that consisted of the following: Raw Milling of Kielder logs, Fabrication of CLT panels, Design & Prototyping Studios for the creation and testing of new joints and systems and Testing of CLT’s tectonic and fire resilience. Thus, hoping to restablish the diminishing industry in the area & beyond. by creating a centre based on putting the UK at the forefront of a New Age of CLT Design.
Matter
Analysing the existing CLT factories of Austria and SE Germany, I looked to design the project around the factories production Line, while also considering how the Education / Leisure program can be intertwined.An example of this is the Glass Front which expresses the Stages of the Production Line. The quality control/storage points of the production line are located to the public front of the facility, enabling people in the forestry tower and the external CLT pavilion garden to understand the processes undertaken within the building by merely studying the facade.
Exploded Axonometric - 1 : 250
The form of the facility came from setting the industrial elements of the program to the industrial axis of the northside of the lake and the leisure elements to the leisure orientated axis of the southern side of the lake.
The Tower and Public Installations were designed to express the Sculptural Opportunity of CLT and the potential of my proposed structural system. While the testing facilities design bridges the gap between the needs of the program and the joy of the site opportunities.
Framing and expressing the Landscape
Production line stages expressed along glass fronted bays
Production line control points are hung from the roof structure
I created a New Destination for visitors based on Education & Experiencing the Landscape, while drawing from the Existing Design Language of Kielder Art & Architecture Installations. This formed the decision for the tower which possesses carefully designed views, aimed to educate the visitors about how the park is managed but also to draw people to specific parts of the landscape.
Care has been taken as to when the visitors should be emersed within the Fabrication & Testing Program, and when to draw their attention out of the facilty towards the surrounding natural amphiteathre of the Bakethin Weirs Northern Lake Side.
Foyer (View to North Peak)
Level 1 (Site Layering)
Level 2 (Small to Large Scale)
Level 3 (Site Scale)
Cafe (North Lake View) a
Level 4 (Forrestry Management)
The firest view of the facility is of the Tower dominatly protruding from the tree canopy on the North Side of the lake, with the bridge leading you across
Tectonic Testing (Shake Plate)
Testing Facility Roof Top
Fire Testing (View Through Skylight)
Roof Top View-Point
Education Pod Entrance
Factory Observation Pod
Education Pod End
Tower View - Level 2
Level 2’s view is all about showing off the site, the view directs you down to the shore line, then to the opposing shore and finall to the mountanous peaks beyond
Visitor Discovery Routes
Visitor Routes Public Access & Observation Pods
Visitor Routes Public Access & Observation Pods
Pods
Pods
Off of the Education Pod is access to two Observation Pods, which allow the public to overlook part of the factory floor, enabling them to engague with the production line safely
Education Pod - Observation Point
At the end of the Education Pod is an Observation Point, directing visitors attention to the prominent peal to the NE and to one of the workers Circulation / Release Pods
In order to mitigate these issues, the lowest floor level was sunken into the basement and a light-well was developed to improve light and air qualities in the space. While frosted glass windows on the ground and first floor, sky lights/lanterns and two enclosed second floor courtyards reduced light pollution and overlooking into neighbouring houses while creating light and airy spaces. I feel that these constraints provided the necessary restrictions for a stimulating scheme to emerge, one which I am rather proud to put my name to.
A private client asked me to investigate the possibility of extending their Victorian House, they wished to open up the kitchen, create a better dining room and to produce a seating area with a view out into the garden. I worked on this project in my spare time for two weeks when first starting my year’s placement. Site width issues and the location of the first floors windows reduced my options in terms of design. In the end I looked at a single pitch roof leaning against the existing external wall, in order to retain the doubles to the back the extension area. I also raised the floor level to create a level threshold access between the extended and existing.
Building Fabric - MArch - 1st Year - January 16 - December 16
1:50 Sectional Model & Technical Section
Urban Hacking - MArch - 1st Year - October 15 - December 15
1:100 Section - Hacking Production Line & Street Visual
Urban - BaHons - 3rd Year - January 14 - July 14
Streetscape Design Apporach Models & Test Visuals
Urban - BaHons - 3rd Year - January 14 - July 14
Dusk Street Sceen Visual
Modular - BaHons - 2nd Year - September 12 - December 12
Rear Courtyard Visual