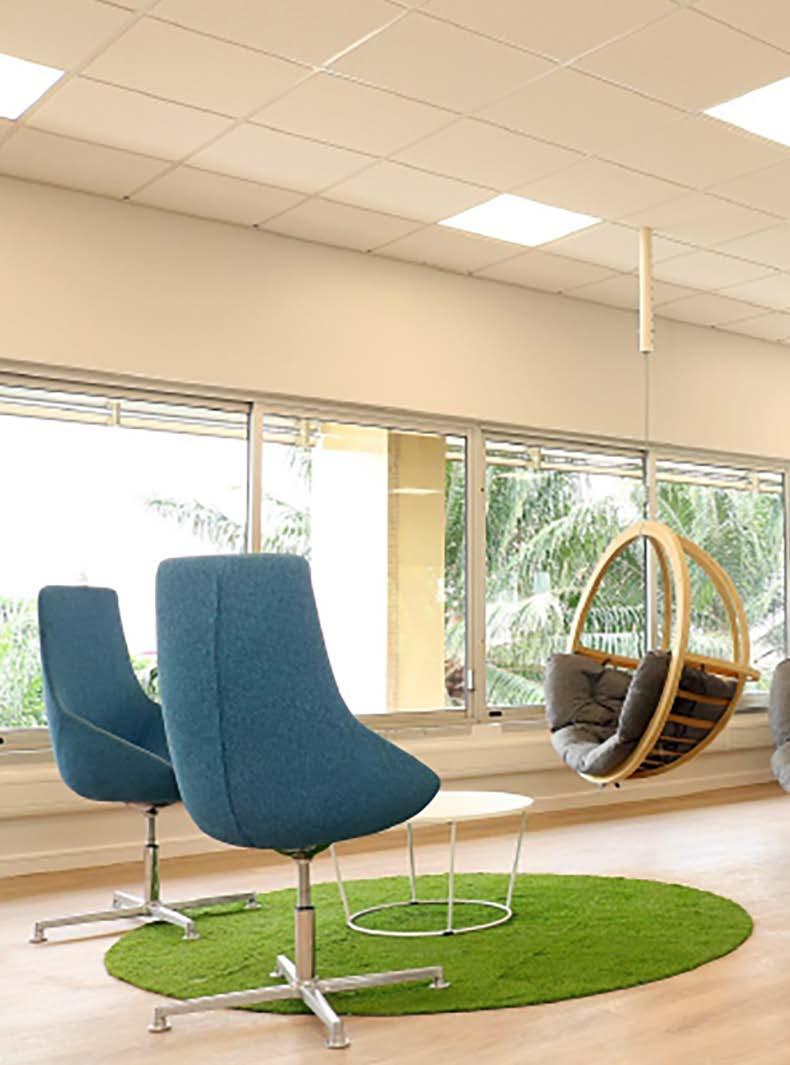
10 minute read
AFRICA INSIDE A look at Nigeria’s first Green Star
A look at Nigeria’s first Green Star rated interiors AFRICA INSIDE
Two office interiors projects in Nigeria recently became the first Green Star rated interiors projects on the continent outside South Africa. We investigate the processes involved, the contextual challenges and the sustainable office spaces that emerged.
Advertisement
WORDS Melinda Hardisty

Ecocentric
Unilever’s playful pause areas provide staff with areas of respite.
Nigeria is the most populous country in Africa and is home to over 206-million people. In turn, Lagos is the country’s most populous city with over 14-million residents (some estimates have this number closer to 21-million). It is a coastal city, extending from the mainland onto a collection of islands and land reclaimed from the sea. It has a tropical climate with two distinct rainy seasons and average temperatures of 24°C to 33°C and an average annual relative humidity of 85%. Both temperature and humidity levels are expected to rise as the result of climate change. It is in this context that we find Africa’s first two Green Star rated interiors projects outside of South African borders.
UNILEVER
Project nutshell
Project dates: August 2020 (certified) Green Star rating: 4-Star Green Star (Interiors v1) Location: Ikeja, Lagos, Nigeria Type of building: Office Interior Project size: 1980m² GLA
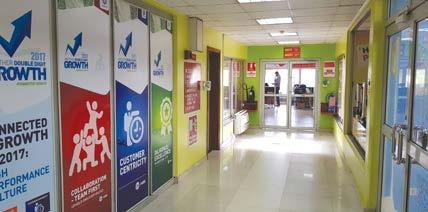
The Unilever offices in Ikeja, Lagos were the first offices to target a Green Star rating. Unilever, as a global brand, already had its Unilever Sustainable Living Plan (USLP) in place, guiding the sustainable standards and targets for all developments and operations, explains Praveen Sharma, programme manager at Unilever. “The driver to pursue a Green Star rating came from Unilever and also my passion as a project lead to do the right thing when it comes to building environmentally friendly workplaces,” he adds.
Unilever was already housed in an existing office building and wanted to update two office floors and their reception area. DNA Interior Design, based in Durban, South Africa, was commissioned to design the new offices. DNA’s Julie Anderson describes the brief as being “to transform the existing outdated, visually cluttered, closed floor plan office into an open plan office interior that met Unilever’s global workplace standards and attained 4-Star Green Star accreditation”.
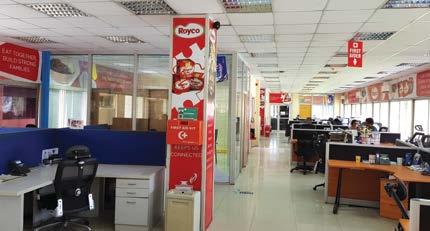
ADAPTING FOR CONTEXT
Ecocentric’s Jutta Berns, who was the sustainability consultant on both projects, explains that the first project targeting Green Star rating in a new context has to pave the way for others to follow. The team had to draw up a Local Context Report (LCR), using the proposed Unilever project as a case study in order to pursue certification. The report assesses the rating tool in the new context and proposes any changes to the criteria that may be required in a new setting. Berns highlights that the LCR development process allowed for multiple workshops and review sessions with the local Nigerian team, which helped to clarify the intent and the requirements to achieve the sustainable goals.
Unilever’s old offices with partitioned offices and garish billboard style branding.
Julie Anderson
Unilever’s new open plan offices are light and airy with pops of colour.

Ecocentric
One of the biggest adjustments that needed to be made in this context was around materials and their ratings. In the South African context, materials ratings are heavily based on international standards like South Africa’s Green Tag. In Nigeria, it is difficult and expensive to source these products. The team developed a specialised ranking tool to be able to assess locally available materials and products in terms of sustainability. “Just because something is local does not mean it is sustainable,” adds Berns, so the tool assists with the assessment of environmental and life-cycle criteria without the requirement for international certification. The tool interrogates material sourcing, emissions, disclosure, end-of-life/ disposal plans, local industry support, knowledge transfer and material transparency to be able to rate a product’s environmental impact. Berns highlights that it was invaluable to have a client willing to invest the time and money into developing the framework required not only for their own project but for others to follow suit.

OFFICES REIMAGINED
The existing Unilever office plans were housed in a building that was over forty years old and had outdated cellular office arrangements. “A major interior transformation was required with the central focus being employee wellbeing and creating a healthy environment for occupants,” says DNA’s Anderson. Climatic and local needs were addressed when envisaging the fresh, bright, and crisp interior. Newly launched global brand illustrations added pops of artistic colour throughout and provided a clear linkage to Unilever’s brand identity. “Efficiency of space usage was also essential to create a new, agile work environment,” says Anderson.
Almost 95% of paints, sealants and adhesives are low VOC. According to Anderson, this was one of the location specific project challenges as these products are hard to source in Nigeria, but credits the contractor’s local knowledge and experience with being able to source the right products. Another challenge was the tracking and recording of recycled materials as part of the project’s waste management strategy. Though recycling, especially of building materials, is extensive in Nigeria, it is largely informal, making it harder to monitor.
Other sustainable building features include LED lighting, lighting and HVAC occupancy sensors, low flow plumbing fittings and improved fresh air rates. Energy and water is sub-metered, and CO2 and humidity sensors are linked to a visual display in reception, keeping occupants aware of how well the building is performing. Indoor plants help to purify the air and connect office staff to nature.
Sharma expresses Unilever’s satisfaction with the end product, “The transformation improved the overall employee experience and their performance in the office.” He adds that staff working in the office especially appreciate the open plan layout, maximised natural light, vibrant interiors, improved indoor air quality, better control over thermal comfort, visible greenery and improved ergonomics in the office. The team developed a specialised ranking tool to be able to assess locally available materials and products in terms of sustainability.
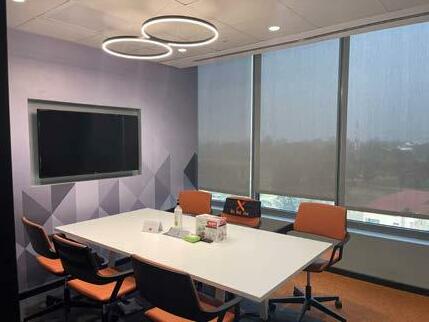
Unilever’s bright meeting rooms incorporate colourful, fun brand art into the décor.
MASTERCARD
Project nutshell
Project dates: April 2021 (certified) Green Star rating: 4-Star Green Star (Interiors v1) Location: Ikoyi, Lagos, Nigeria Type of building: Office Interior Project size: 645m² GLA
MasterCard’s Lagos office is also housed in an existing building and required an upgrade to update the aesthetics, functionality and environmental performance. The 645m² office plan needed to accommodate approximately 45 staff in a comfortable and functional space. As with Unilever, the Green Star certification requirement was part of MasterCard’s global sustainability strategy and the green requirements were built into the brief.
Ecocentric
MasterCard’s meeting rooms have natural light and outside views.
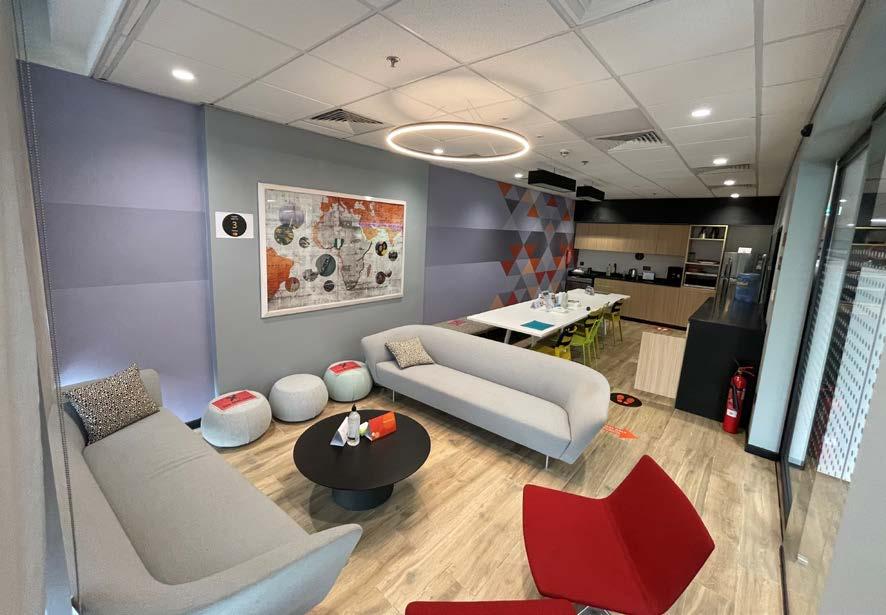
MasterCard’s Breakout spaces are colourful, modern and clean in design.
Swiss Bureau Interior Design, based in Dubai, were commissioned to create a contemporary, light, comfortable office space that would meet the operational requirements of a modern office and also the sustainability standards required for a 4-Star Green Star rating. This project was able to utilise the legwork already put in on the Unilever project in terms of the Local Context Report and the materials ranking tool. All the furniture, flooring, and assemblies had third party certifications, had recycled content or were manufactured in ISO14001 manufacturing facilities and easily met the rating tool requirements.
Indoor plants help to purify the air and also, along with extensive external views, connect the occupants to the natural world, contributing to their physical and mental wellbeing. Blinds control internal glare. Sensors were installed to monitor Co2 levels within the offices and trigger fresh air intake when levels reached certain maximum levels.
A total 87% of construction waste was diverted from landfill and operational waste is sorted at source and recycled where applicable. All the usual energy and water saving devices are installed and a physical display in reception, detailing the fit-out’s performance in terms of water and energy consumption keeps occupants aware of their own impacts on the planet. Bicycle parking was not supplied as, in the context, this is not a common mode of transport. But car pool bays were provided, encouraging people to share transport. The location also assists in lowering
Ecocentric
occupants’ carbon footprints as it is close to many amenities. Video conferencing facilities reduce the need for travel for meetings, either abroad or locally. This is particularly important in a city with such a high population and a high dependence on road travel.
BLAZING THE TRAIL IN LAGOS
Berns and other team members highlight some of the main project challenges as being those relating to the unfamiliarity of the ratings tools and sustainability concepts in context. This was the first time most of the local consultants and contractors had had to engage with the stringent requirements. The remote management of the project with consultants scattered around the globe also didn’t aid with the initial vision casting and collaboration.
The strict monitoring on site is also more difficult at a distance, but systems were put in place to be able to meet the various requirements. Sharma highlights the importance of “first projects” as trailblazers for change, “This was a great opportunity to inspire others to see that, even with all the social, economic and cultural challenges faced in new contexts, especially in Africa, it is very important and relevant that we embed sustainability in our workplaces.” In the end all the targets were achieved and the challenges experienced on these projects should be minimised in other projects following their lead in the rest of the continent.
“Interiors projects are small and replicable,” says Berns, “lending themselves to quick knowledge transfer over a short period of time, making learned concepts and techniques easy to apply again on other projects.” Requirements should become better understood and easier with each project, enabling building performance to be pushed further, and for sustainable building practices to be prioritised in more African settings.
NEW RELIABLE UNDERLAYMENTS MAKE A DIFFERENCE

The quality of an underlayment makes all the difference between a smooth flooring system application and a troublesome one. Sika South Africa self-levelling screed, the Sikafloor-200 Level meets and exceeds all the latest standards and requirements for both new work and refurbishments.
Sikafloor®-200 Level is a very low emission, cementbased, self-levelling compound which provides customers with peace of mind by providing a high quality and reliable underlayment for most hard and soft surface floor coverings.
Suitable for interior and exterior residential and nonindustrial applications, Sikafloor®-200 Level is ideal for filling, smoothing and levelling of suitable substrates; before applying parquet, ceramic tiles, seamless resin floors, textile and elastic floor coverings.
This flooring system has applications in manufacturing industries, institutional, residential and domestic buildings as well as levelling of pre-cast concrete planks and pre-levelling for roof membranes.
WHY SIKAFLOOR®-200 LEVEL?
Two competitive edges of Sikafloor®-200 Level are the pot life of approximately 40minutes at +20°C, and its foot-traffic readiness after about 4 hours. Other valuable product and end-result features include very low emissions, improved surface finishes, increased durability, enhanced safety, and improved appearance.
#flooring #reliableunderlayments #sikafloor-200level
Sika South Africa Durban, South Africa Phone: +27 31 7926500 Email: cloete.romaine@za.sika.com
TAKING YOU TO THE NEXT LEVEL OF PERFECT FLOORS
SIKAFLOOR®-200 LEVEL
SELF LEVELLING SCREED
Sikafloor®-200 Level is a very low emission cement-based self-levelling compound, suitable for interior and exterior areas.
■ Low shrinkage ■ Filling, smoothing & levelling ■ Moisture resistant & rapid hardening compound ■ Layer thickness up to 60mm with aggregates ■ Suitable for application on subfloor heating sytems ■ Pumpable ■ Suitable to build bonded screeds under ceramic tiles on cementitious substrates
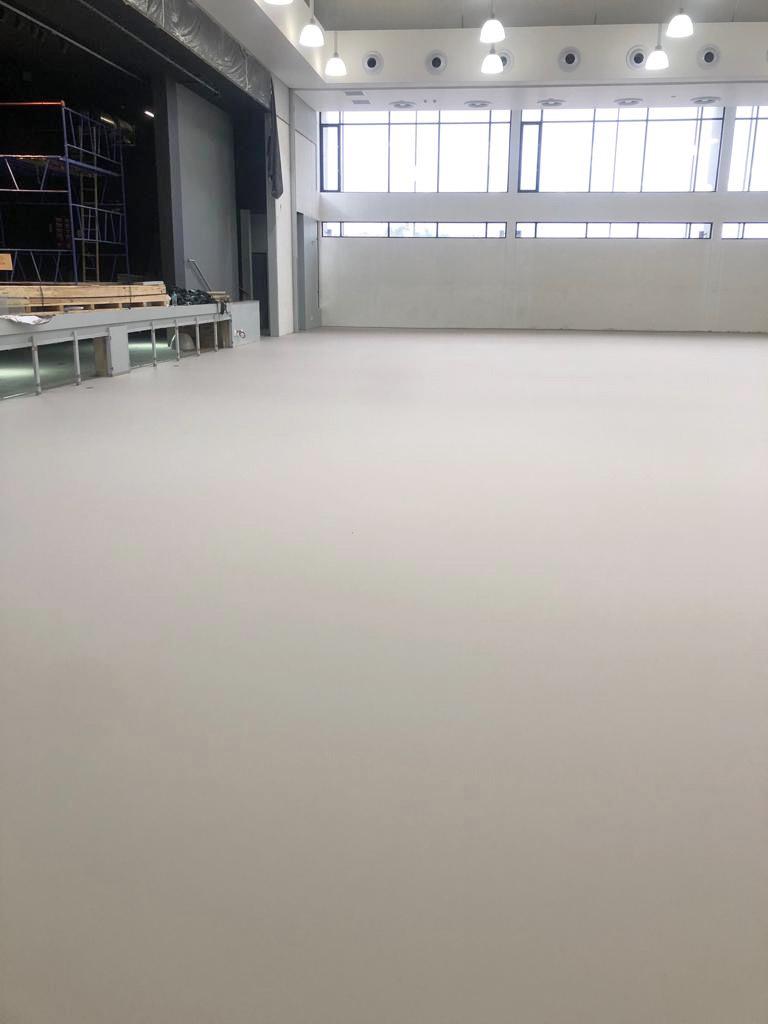
Open your phone camera and point it here to view on our website Call us for more info: 010 823 8688