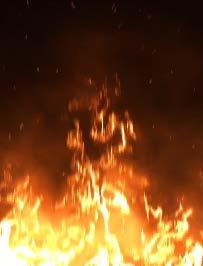
5 minute read
CIRCULARITY Waste heat to electricity
Circular Economy in Energy: WASTE HEAT TO ELECTRICITY
In this article we highlight the opportunities in a waste stream often overlooked – waste heat. While not a traditional commodity we would think of under the waste label, it is nonetheless just as important to recycle and perhaps even more economically viable to implement.
Advertisement
BY CHRIS WHYTE, ACEN*
This waste stream is found in multiple sectors like water, energy, manufacturing and agriculture. Waste heat is a vast, underutilised, and sustainable source of energy that has been largely overlooked in the past due to technological constraints and financial barriers. Heat sources can vary from waste heat escaping up flue stacks from coal-fired boilers through to hot water or steam from diesel engines in ships, mining applications, steel furnaces, boilers, and manufacturing industries.
Heat is an essential ingredient to many processes and the key industries contributing the greatest emissions and carbon footprint are those associated with the bulk of our electricity from burning coal, the petrochemical industries, steel manufacture, cement production and other manufacturing industries. Huge energy reserves are used to create the heat required for these processes, so it simply makes sense to catch the waste heat off the end of the process and get it back into the grid.
The latest technological innovations and systems are extremely efficient. When we think of the extremes of waste heat production one visualises the old ’80s movies of mid-western steel workers in the USA sweating over furnaces of molten steel. The reality now is that escape temperatures as low as 70°C can be harvested for conversion back to energy and this would service most conventional manufacturing facilities.
Also, recent innovation and development in the application of organic Rankine cycle (ORC) and axial turbine systems allows for smaller-scale systems that can have modular energy outputs of anything from 75kW to 500kW with a return on investment at 36-48 months producing energy cheaper than current coal-based electricity. Benefits are that this energy is more reliable than renewables (the sun does not always shine, and the wind does not always blow) and provides reliable base load electricity.
The additional extension of this technology is that one can integrate these systems with your own heat source from incineration of problematic waste streams such as agricultural and forestry residues, plastics, and tyre waste. ORC systems can be used as small-scale concentrated solar power plants thus dramatically reducing the capital expenditure of the larger systems conventionally deployed globally.
Simply put, the organic Rankine cycle and axial turbine systems capture waste-heat from different manufacturing processes and like a steam turbine turn this energy into electricity. As the ORC system uses a refrigerant gas that boils and expands at very low temperatures, the system will operate at temperatures between 70 and 150°C, which is a fraction of the heat required for conventional Rankine cycle and steam turbine systems.
Another great feature is that this is a closed loop system so no contaminants can enter the system, and this extends the life of the plant. ORC systems produce emission-free clean power from waste-heat – it’s as simple as that. The waste-heat-to-energy market is set to exceed $30-billion by 2025 and yet the uptake is still low. This is largely due to a lack of knowledge of available technologies and the incorrect perception that this is only applicable to large-scale waste heat applications like steel manufacturing and coal power.
The Rankine cycle is a thermodynamic cycle that converts heat into work. The heat is supplied to a closed loop, which typically uses water as a working fluid. The Rankine cycle based on water provides approximately 85% of worldwide electricity production. Steam-to-electricity has been around since modern industrialisation, but even ORC systems have been around for over 100 years. However, the latter have only really been deployed at any scale since the turn of the century.
A resurgence of interest in the research and development of ORC as a viable small-scale solution for electrical production developed after the successful completion of the 1MW APS Saguaro PT plant in Arizona, USA in 2006. Since then, our 21st century engineering skills have continued to refine and develop these systems to the current applications where we can harvest low-volume, low-heat outputs with compact modular units with a footprint as small as 4m2 and outputs of up to 75kW.
As the ORC and axial turbine systems use this waste-heat, it adds to the cooling of the hot water or air, and this helps the industries where they need to cool processes and less heat will go into the atmosphere. Coolingto-power is an effective means of increasing energy efficiency due to these systems consuming the waste heat as fuel, which significantly reduces the cooling load (70-100%). This means, in addition to generating emissionfree power, the parasitic cooling load also is reduced or even eliminated, further reducing costs and increasing efficiency.
Companies looking for clean affordable power that have a waste-heat source should consider implementing these systems for their power generation. Being modular, this decreases financial risk and allows for scaling. Some companies that I work with will provide free evaluations and even financing options allowing the customer to avoid any initial capital cost with the ability to buy the power from their own waste heat at cheaper rates than grid-based options.
Increasing energy efficiency is the single easiest step in pursuing a carbon-neutral future. Using an existing resource – heat – to provide power and cooling reduces fossil fuel consumption and reliance on the grid. ORC and axial turbine power generation is a sustainable technology that reduces the amount of energy consumed (fuel) and energy wasted (heat). Energy efficiency will always play a role in combatting climate change because no matter the process, the more efficient it is, the less impact it has on the planet.
With the reliability and cost-effectiveness of modern systems, waste- heat recovery solutions such as cooling-to-power are both profitable and practical. With the world eyeing ways to shift toward clean energy and with the help of incentives promoting sustainability like the local Carbon Tax (Act 15 of 2019), cooling-to-power is primed to be a disruptive technology in the energy efficiency and commercial cooling market – effectively changing the way corporations see and use waste-heat.
Don’t miss The Circular Economy Show every Wednesday at 1:00pm. Chris Whyte discusses all things circular with Gordon Brown and guests. Each episode provides an in-depth discussion based on sectoral topics.