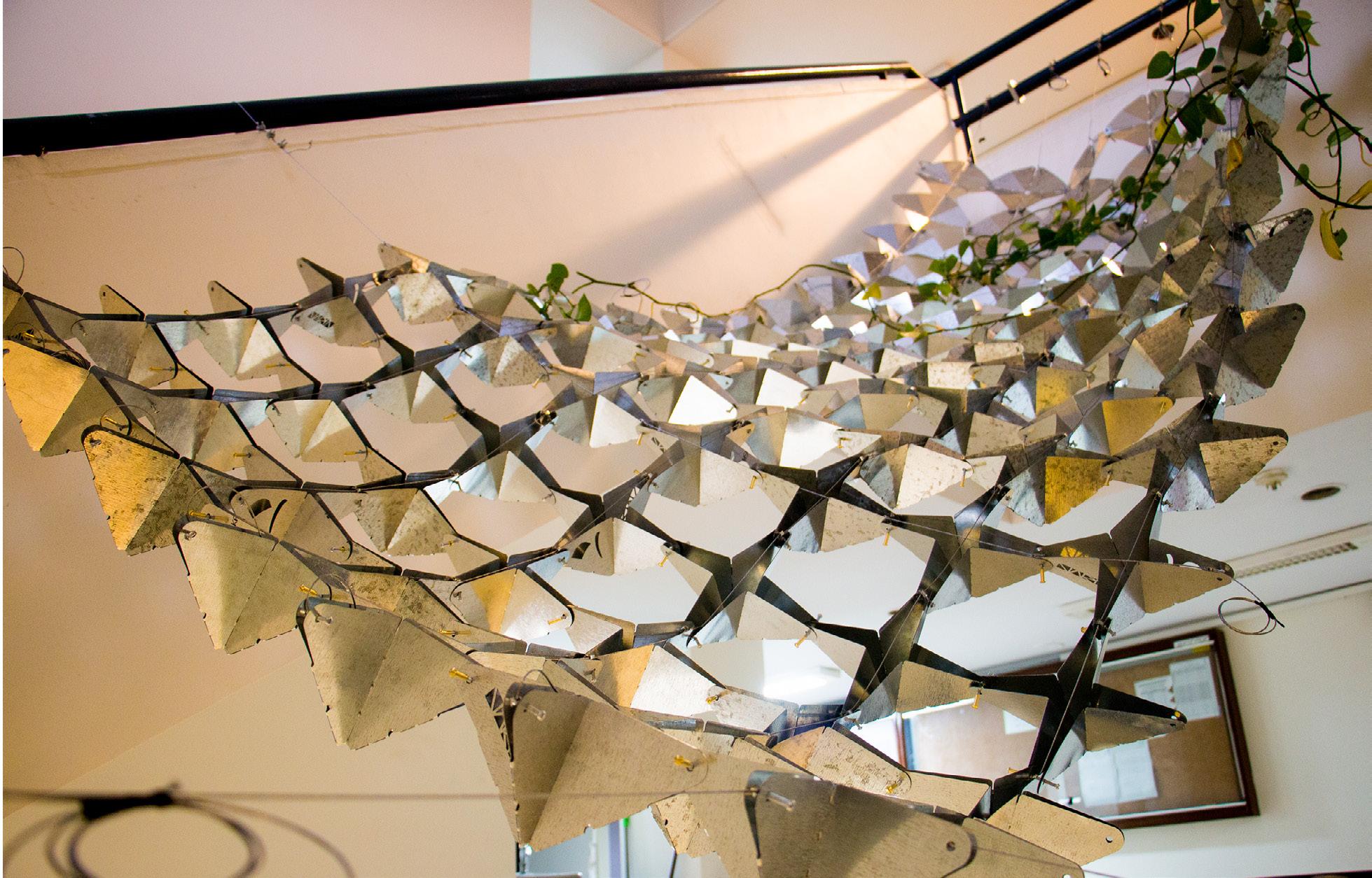
2 minute read
Transformative Modular Structure
Winter 2017 / Building tech design / University of Arts, Tehran (UoA)
Supervisors Prof. Dr. Mojtaba Mahdavinia Team Asal Shirvanian, Ehsan dehghani, Iman Tavakoli, Sajjad Yazdani
Advertisement
The project was carried out in technical design studio that led to the construction scaled in 1:1. The aim of the course was using modern construction technologies and getting involved with technical details in order to build the project in real size.The final solution was the use of modular and tensile structure.
Final instalation at faculty of architecture and urbanism building of UoA.
The Challenge
When it comes to building a model in 1:1 scale, we have to consider various kinds of different issues from the exact size of a screw to funding strategies like finding a sponsor.
Starting from structural aspects, we intended to use 25cm*25cm modules to form a fluid surface. After testing numerous prototypes we finally came up with the idea of using an origami star-shape module, which opens and closes in different pressures in a tensile system. To supply this force we have connected all of the modules by a grid of cables, passing in each module. This will enable the structure not only to act as a contilever structure, but also to provide us different forms in different tensions.
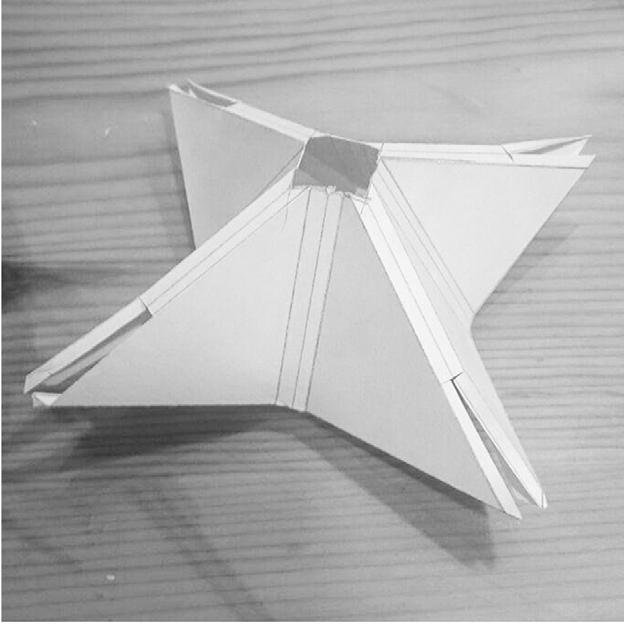
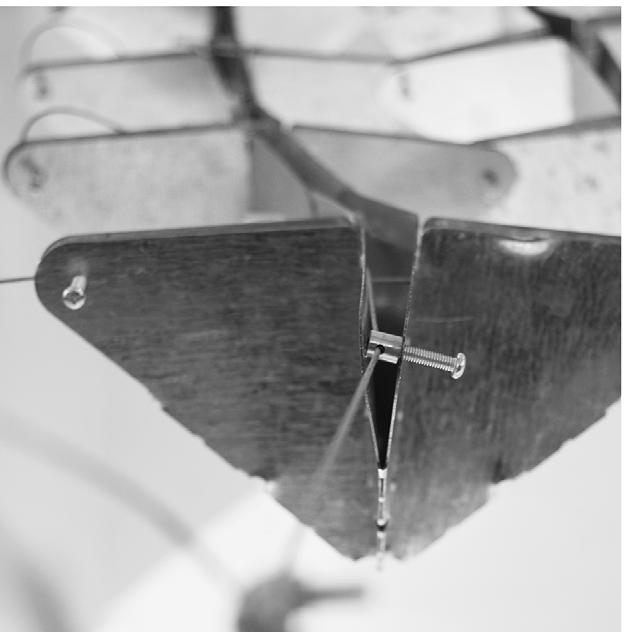
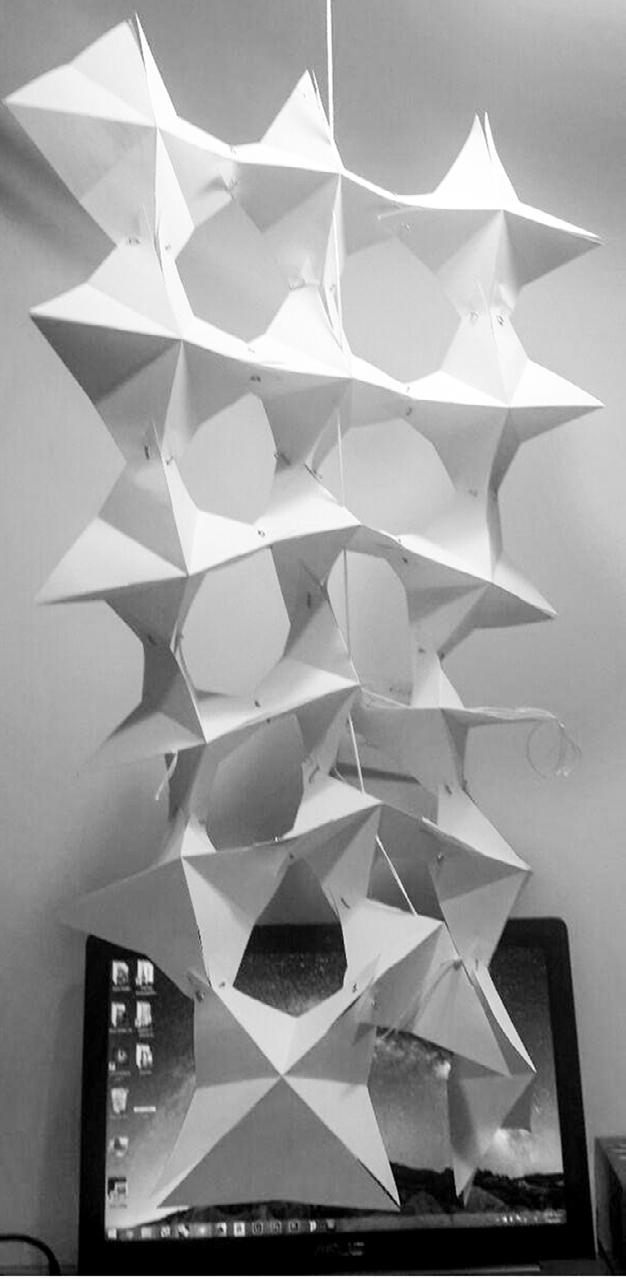
Initial prototypes made by paper and finally by galvanized metal sheets.
Module folding process
Module dimention changes in response to appleid pressure or tension
Cables and modules position according to eachother.
After finalizing the initial idea, we did a quick research on materials to find the best one. The main factors in choosing it was firstly, its ability to be folded, since the module form was based on a folding process. Second, it had to have high shear stress, because every module had to connect with others via a small screw. And third, its cost might be low so that we could afford it.
Lastly, we chose to use 0.5mm galvanized steel and CNC method to cut it in predesigned shape. Although it costed too much, fortunately we found a sponsor named, NarinTechFartak. Cooperation with a company which is active in the field of design and construction of industrial machinery and ATM machines was an incredible chance to achieve great experiences.
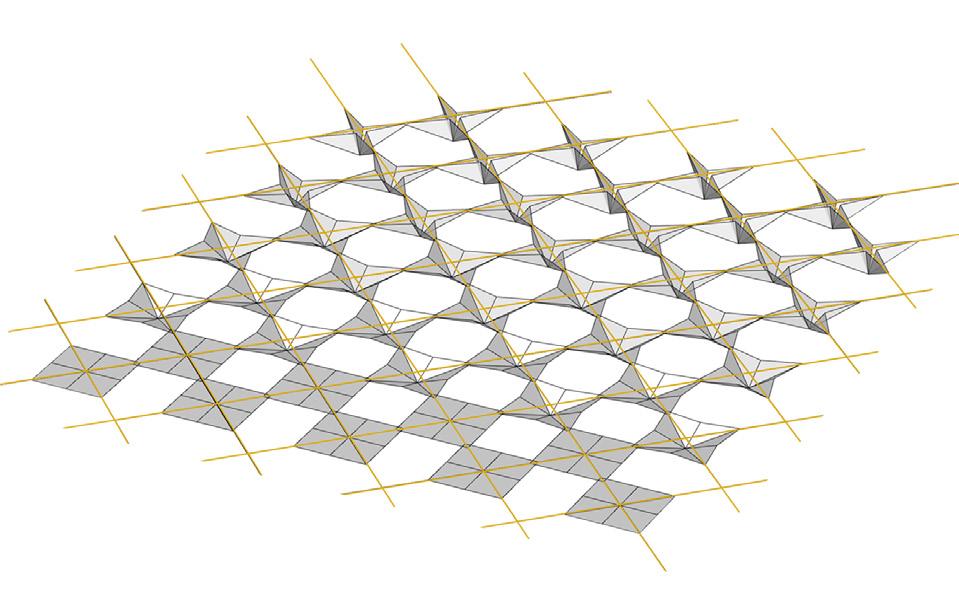
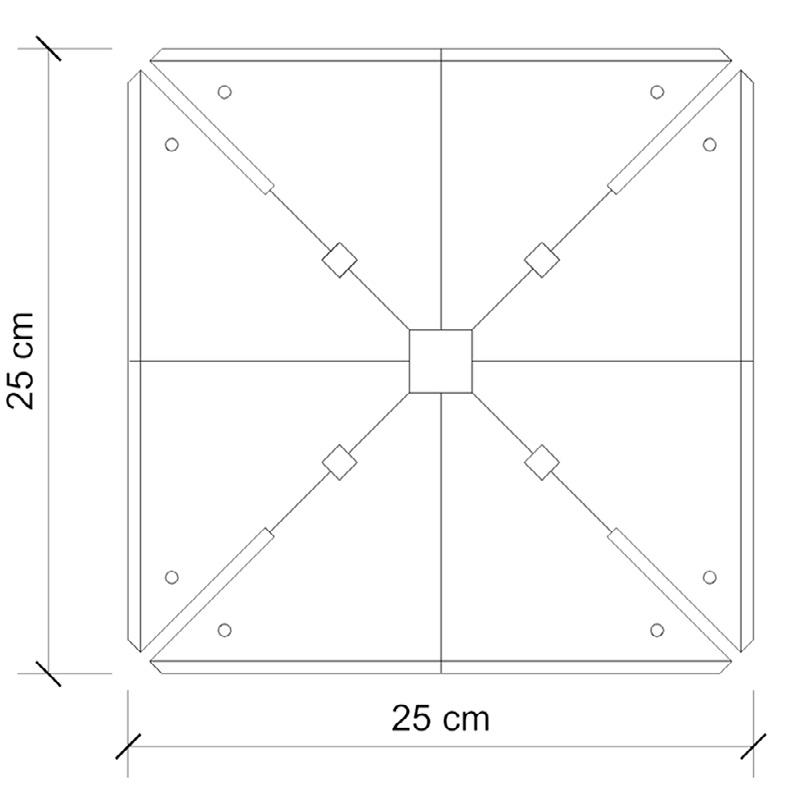
Technical plan of one module.
Modules technical plan
The number of modules and their dimension was considered due to the size of installation space and the optimal use of the galvanized sheet. The modules cut the square shape and each modules would bend from the axis of the symmetry to ensure eight equal triangles. By cable passage from the diagonal of each modulus, the capability for opening and closure of each modulus has been provided.
Assembly of the parts on site. Laser cutting machine.
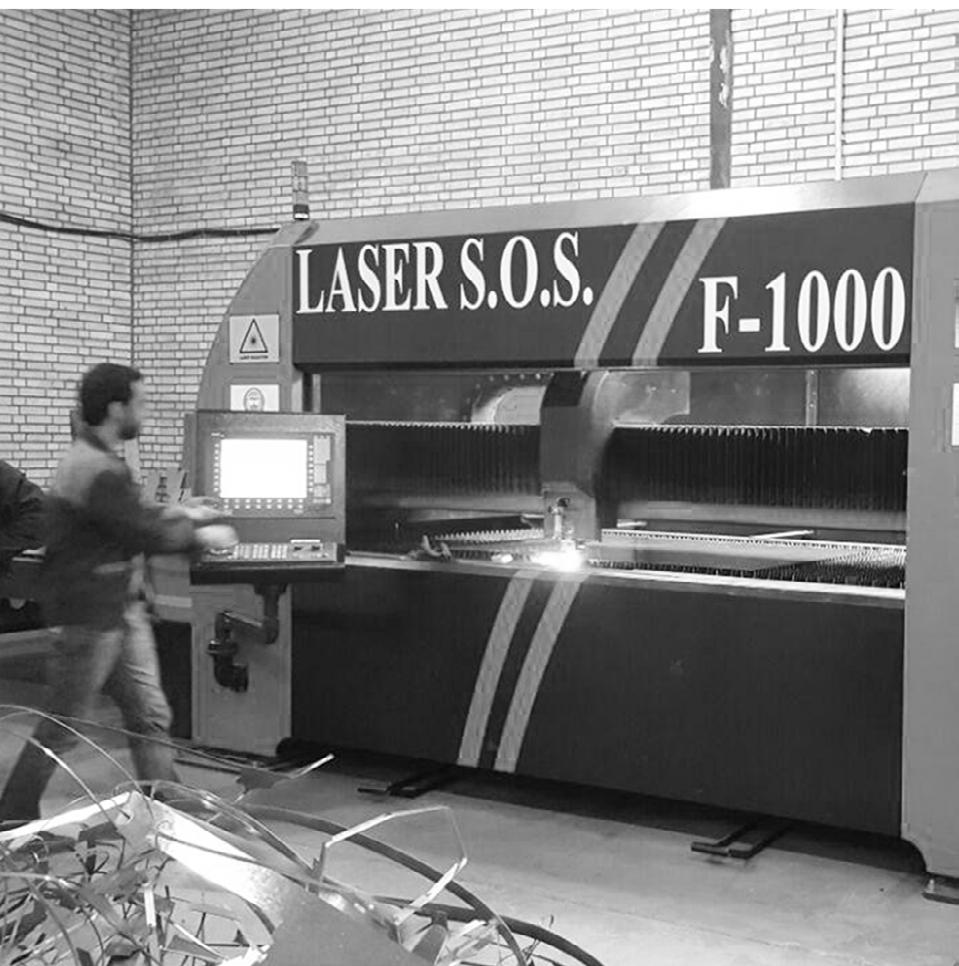
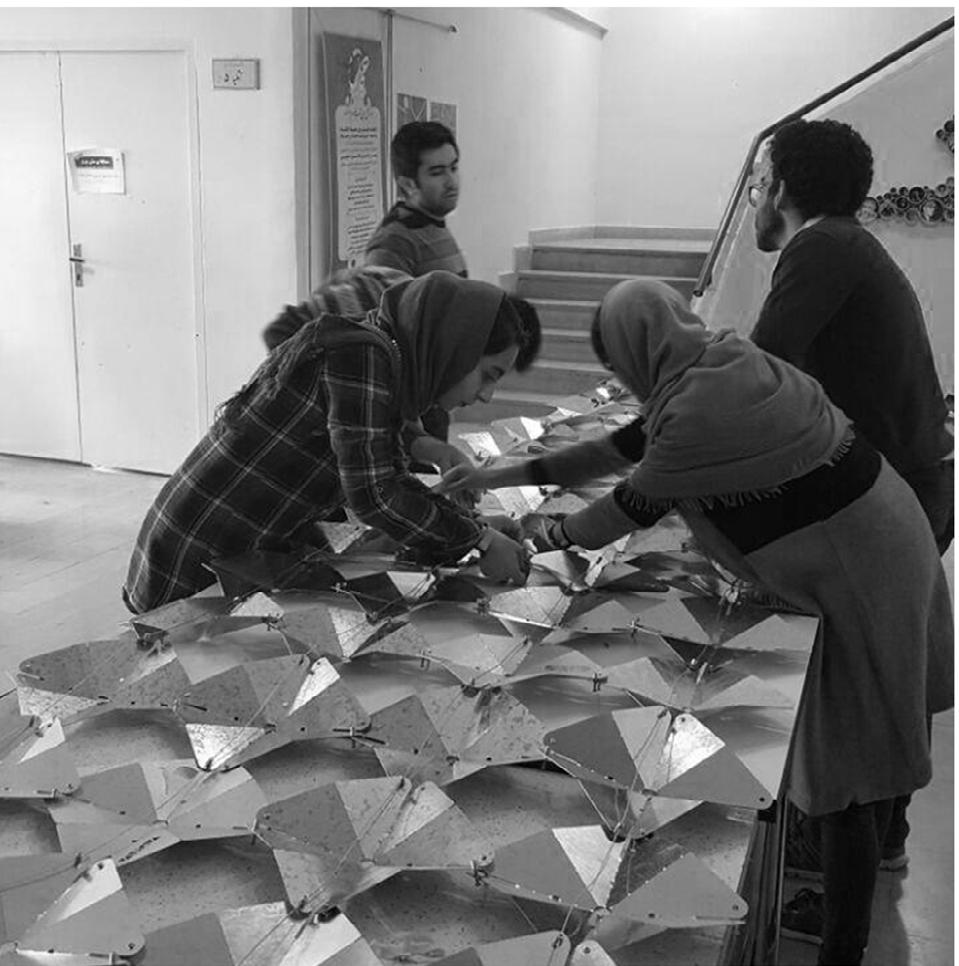
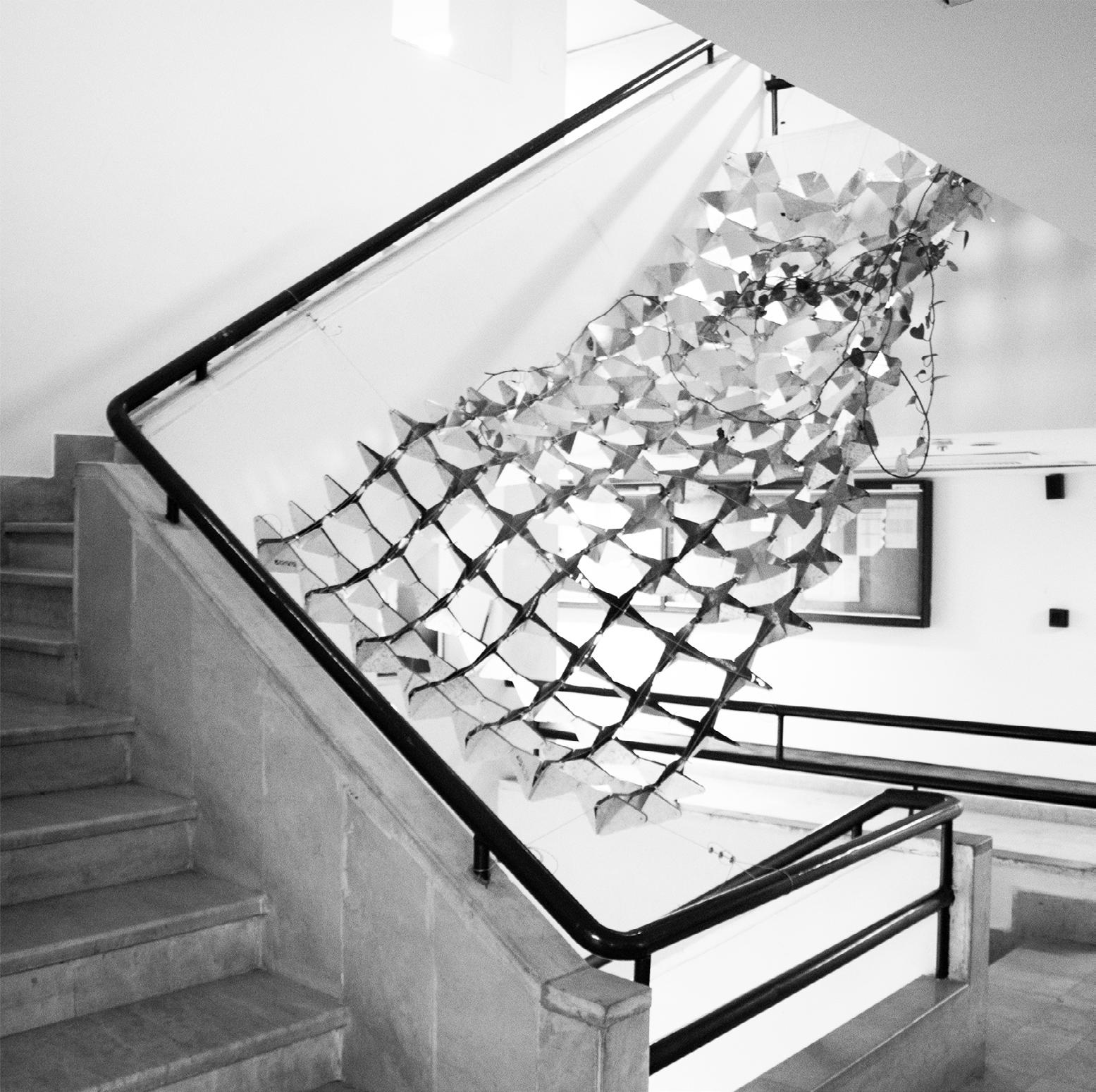
Final instalation at faculty of architecture and urbanism building of UoA.