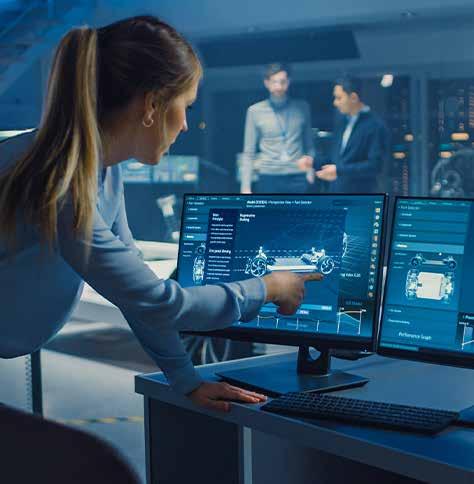
21 minute read
VOICEBOX
from AMT OCT/NOV 2020
by AMTIL
Saving Australian business COVID-19 is killing our small manufacturing businesses and ruining the economy. Flavio Romero Macau and Andrei Alexander Lux discuss what business owners and governments can do about it.
Small and medium-sized businesses (SMEs) are at the heart of our economies, employing around 70% of labour markets and keeping profits within local communities. They are also suffering the most with COVID-19. Small manufacturers have been left behind by successive governments in favour of big businesses in the resources sector, and this may well be the final straw. Our research shows that successful companies are the product of resourceful entrepreneurs and favourable business conditions – their success depends on the local business environment. We’ve come up with three things that business owners can do, and twice as many that governments can do to boost firm performance and support recovery. What you can do: Knowledge, Network, Mindset A lot depends on what you know, who you know, and who you are. The more you know, the more places your business will go. Playing it by ear and blundering your way through means making costly mistakes that are easily avoided. Business schools, polytechnics, and start-up hubs all offer targeted, practical training to help you run a business. Go to a webinar, enrol in a course, share your experiences and learn from other entrepreneurs. But competence alone won’t get you there. Who you know can make all the difference, and we’re not talking about friends and family. Improving the quality and breadth of your business network will give you privileged access to emerging opportunities and valuable resources. Pursue every chance you get to meet key people in your field and work at making a strong impression. Join the conversation in engineering, supply chain management, and manufacturing excellence. Time invested in a council or association opens opportunities for small business. One last thing all business owners know but often don’t give much credit: running a company is a psychologically challenging endeavour. To succeed, they must be hopeful and optimistic, to believe in their own potential and persevere when things go wrong. Now more than ever, they need to cultivate the kind of mental fortitude that will help see them and their business out the other end of the pandemic. As manufacturing is technical, business owners often downplay the importance of the psychological. This isn’t a call for motivational self-help, but recognition that a “can do” mindset will prevail. But this is not enough. Here’s where governments come in. What governments can do Even the most resourceful business owners can only just stay afloat when the business environment stifles their efforts. So what makes a favourable manufacturing business environment? • Access to capital. It takes money to make money.
Guarantee schemes, support to the flow of credit, relief packages, innovation grants, rebates, manufacturing stimulus packages are examples of initiatives that governments must offer small businesses on a regular basis. • Policy relief. Policymakers can support or hinder manufacturing in Australia over importing from overseas: taxes, regulations, permits, licenses, incentives … you name it. Regulatory hurdles hurt small businesses more than large organisations and often put manufacturers at a disadvantage.
Policy can level the field by commanding the same requirements from offshore that local businesses are subject to with regards to social responsibility, employee safety, and green manufacturing. • Access to mentors. Learn from other people’s mistakes.
Mentors have the practical knowledge about what works and how to get it. Governments must encourage start-up hubs and chambers of commerce that help new business owners make important connections. • Access to innovation. Universities are at the cutting edge of development, and Australian universities continue to rise in international rankings. Collaborating with businesses to convert this knowledge into products is not an easy task. Government must bridge these two worlds, bringing research expertise to industry problems that stimulate innovative solutions. Workshops, awards, grants, professional conferences, networking events … they all count and governments are in a better position to co-ordinate and organise such events. • Access to talent. You need qualified employees, adapted to the pace of work at small businesses. Now is the time to upskill, and governments must incentivise programs to help attract and maintain a highly-skilled talent pool. Retraining and reskilling workers in the age of automation is fundamental to a strong manufacturing sector in a time where Industry 4.0, the
Internet of Things, and blockchain are opening opportunities in Lean manufacturing, mass customisation, and supply chain management. • Access to professional services. Tax, legal, real estate, insurance, accounting … you can’t do it all on your own.
Business owners must be confident to outsource these tasks to trusted local service providers on favourable terms.
Intellectual property is a fundamental piece where business owners often suffer in silence while their proprietary knowledge is ripped off by foreign companies. Having specialised support with ample knowledge on how things work can save time, money, and produces better results. • Local attitudes. How people see small businesses actually affects their performance. Does your community support local manufacturers, or stick to the big brands? Governments must work to cultivate positive cultural attitudes towards local businesses. These factors will determine whether or not business owners can leverage their own resources to drive firm performance and ride out the recession. The pandemic has reignited discussions about the risks of offshore supply chains and the opportunities to boost onshore manufacturing. Governments can turn around the recession by deploying strategic resources to address local challenges and support manufacturing SMEs.
Flavio Romero Macau is a Senior Lecturer in Supply Chain Management and Global Logistics at Edith Cowan University. Andrei Alexander Lux is a Lecturer in Leadership and Organisational Behaviour at Edith Cowan University. www.ecu.edu.au
The waves of evolution in engineering Engineering has contributed a great deal to our everyday lives. Scott Philbrook looks at the evolution of the engineering industry and what innovations we can expect to see next.
Imagine where we’d be without the engineering feats we’re all too familiar with today. Hard to imagine, I know. At the end of a long day at work, we come home to comfortable and efficient living spaces, decked out with appliances that are both time and cost-effective. The pandemic would have been twice as difficult to endure if we didn’t have telephones, radios, and television to keep in touch with loved ones, receive the latest updates from authorities, or pass the time spent in isolation. Through imaging technologies, engineering has changed the way we view ourselves and the world around us. There’s no limit to where innovation in engineering might propel us to in the coming years. Engineering was first conceptualised with human ability in mind. The very first tools were invented to accommodate human sustenance. Before buildings towered over our heads, humans have been innovating tools or devices to solve problems or improve their state of living. The Egyptians, for instance, used wooden trunks to drag material across deserts efficiently, as opposed to carrying these by hand. The birth of the mechanical spinning wheel in 1775 changed industrial engineering for good. By the centenary of British settlement, a thriving manufacturing industry had matured in Australia, producing a range of goods sufficient to supply most domestic needs. From the earliest times, manufacturing’s contribution to Australia’s economic development has been immense. Australia in the 1950s enjoyed a rich and diverse manufacturing sector, with a third of the population employed in it. In the early 1990s, tariffs were cut drastically, adversely affecting the manufacturing sector, and sending Australia down the path of deindustrialisation. On a global level, the mid-19th century saw new processing methods, most notably for steel and petroleum. It reshaped transportation, construction, and manufacturing. In the 20th century, engineering electrified the world. It took us to the skies and gave us the power to explore space. It continues to help cure our thirst, cleaning and making our waters safe for drinking. It has even revolutionised the way we produce food, and has helped simplify our everyday lives. Racing to embrace digital technologies Manufacturing and engineering have come a long way since the rapid innovation of the Industrial Revolution. Operations have shifted from machine production to computerised manufacturing and design. Since then, data has been the name of the game. Manufacturers easily sift through datasets without sacrificing workflow. This wide exposure to data has helped detect anomalies and has played a huge role in making predictions, ultimately improving efficiency and streamlining processes in a more uniformed approach. Now Industry 4.0 is upon us, and plenty of people are welcoming manufacturing automation and information exchange across operations with open arms. Many are also going beyond computer automation and are shifting to cyber-physical machines. This includes game changers like the Internet of Things, machine learning, and smart manufacturing robots. Artificial intelligence (AI) is also being widely embraced in manufacturing, and is a key piece in the larger trend of fully automated production or “smart factories”. AI systems have the potential to transform the way companies run their production lines, enabling greater efficiency by enhancing human capabilities, and providing real-time insights, facilitating design and product innovation.
The impact of innovation in engineering extends beyond financial value. As the digital age continues at full speed, many industries grapple with a state of constant change and instability. Innovations such as the first generation of the Industrial Internet of Things (IIoT) have helped ease and simplify the way these industries work. Smart sensors and intelligent devices within products are easier to get a hold of today. Manufacturers today are in a race to embrace digital technologies. To remain a strong backbone of the global economy, manufacturers are adopting technologies such as Industry 4.0. Gone are the days of laborious mass production models in manufacturing. Today, integrated and seamless automated factories reign supreme. Meeting evolving needs Engineering processes began at the birth of humanity and provided solutions to the different challenges facing people. It seems safe to say innovation will continue driving engineering and manufacturing in the coming years. What we’re seeing today may very well be the early days of the next Industrial Revolution – Industry 5.0. From its early innovations, Industry 5.0 has the potential to transform the modern manufacturing processes, enabling humans and machines to work together in unison. This will pair the unique, cognitive skills of people with the precise, technical skills of robots, fostering an innovative culture in the workforce. Engineers have been and will continue to be critical in advancing technologies that will allow individuals to work, learn, and play in new and interesting ways. Engineers of the future will have to confront a society accustomed to constant change. Changes to market developments and consumer preferences will push companies to develop more innovative solutions to meet evolving production needs.
Scott Philbrook is Interim Managing Director – Australia & New Zealand at RS Components. www.rs-online.com
Do you make and sell consumer goods? No? Think again… The Federal Government has recently passed a legislative change to the Australian Consumer Law, which will broaden the definition of a ‘consumer’. Paul Kirton and Greta Walters examine the potential implications for your business.
The recent change to the Australian Consumer Law (ACL) directly impacts manufacturers and sellers of goods that are not generally used for domestic or household purposes. A buyer of an $80,000 industrial motor may now be a “consumer”. Currently, a person or business is considered a “consumer” for the purposes of the ACL if they purchase goods or services for their own use that: • Are of a kind ordinarily acquired for domestic, household or personal use or consumption; OR • Cost up to $40,000, irrespective of their kind or purpose. A person who on-sells goods or uses them up in the course of manufacturing other goods is not a consumer. But their customer may be a consumer for those on-sold goods or new goods. This definition has been amended by the Treasury Laws Amendment (Acquisition as Consumer – Financial Thresholds) Regulations 2020. From July 2021, the monetary threshold will increase from $40,000 to $100,000. This will, undoubtedly, shake up the traditional ‘business to business’ (B2B) liability landscape for highvalue industrial and commercial goods. For example, the buyer of an industrial laser or robot, for use in their factory, will be a consumer. The buyer will gain all the usual consumer law rights and consumer guarantees, if that laser or robot costs less than $100,000 and is defective or does not perform as promised or required. The role of consumer guarantees Under the ACL, businesses making or supplying goods or services to consumers are bound by consumer guarantees that are imposed by the ACL. These are a set of automatic guarantees that apply to goods and services purchased by consumers, regardless of any voluntary or extended warranty offered. The guarantees require goods to be of acceptable quality (safe, durable, without faults), fit for disclosed purpose, match any description or samples provided, meet promises of performance or quality and have spare parts available. The rights under the ACL cannot be waived or contracted out by limitation of liability clauses in terms and conditions of sale. Failure to comply with the ACL’s consumer guarantee provisions may result in a maximum infringement notice of $13,320 (or $133,200 for listed companies), or prosecution at court with penalties ranging from $10m. Impact on businesses who make or sell goods Businesses that manufacture or supply (by selling, leasing or hiring) goods or services that cost up to $100,000 will become subject to the strict provisions of the ACL relating to refunds, warranties and liability for damages. Depending on whether the problem with the goods is major or minor, the seller must repair, replace or refund a good or service if it fails to meet a consumer guarantee. The seller is also liable for any reasonably foreseeable loss or damage suffered by the consumer arising from the defect. The manufacturer of goods with a major or minor defect can be liable directly to the consumer (for compensation), or must indemnify the seller if the seller is required to provide a remedy or payment to the consumer.

Impact on businesses who buy goods If your business is a buyer of commercial or industrial-type equipment in the $40,000 to $100,000 range, you will now benefit from their newfound protection under the consumer guarantees. While you may not have realised you already had these rights for industrial goods below $40,000. This is a significant win for businesses who are ‘purchasers’ of such goods or services. Any claims against suppliers or manufacturers of these goods are easier to prosecute, and claims for damages flowing from the defect (eg. production line shutdown) may well exist. As the ACL provides a solid foundation of non-excludable consumer protection rights, this also simplifies the always contentious negotiation of guarantee and warranty provisions. Voluntary warranty requirements Manufacturers or sellers who offer their own warranties against defects are required to comply with the strict provisions of the ACL. For example, warranty documents must be presented in a certain way and include mandated statements and specific information that is easily understood by consumers. Businesses who will be newly subject to the ACL’s obligations should update their warranty statements as soon as possible. Those which are found to have a non-complying warranty face a fine of up to $50,000. Get on top of your obligations Businesses that haven’t traditionally made or supplied ‘consumers’ should review their product ranges, business practices and trading documents to ensure they are meeting their ACL obligations. Come 1 July 2021, the ACL will invalidate any businesses’ contractual terms which are inconsistent with their consumer protections requirements. Given the enhanced liability that comes with making or selling these higher value goods, businesses should also review their product insurance policies, to ensure they cover “consumer” type claims. Businesses who will be regarded as consumers should not forget that they can take advantage of this legislative change if the equipment they buy after 21 July 2021 is defective or does not perform as expected.
Paul Kirton is a principal at the commercial law firm Macpherson Kelley. Greta Walters is a lawyer at Macpherson Kelley. www.mk.com.au
Australia: Zero-emission blocks for coal-fired power stations
A new type of thermal storage material, housed in blocks, could see coal-fired power stations converted to run entirely fossil-fuel free. Named Miscibility Gaps Alloy (MGA), the blocks receive energy generated by renewables, store it cheaply and safely as thermal energy, then use it to run steam turbines at power stations. They can be retrofitted to retired power plants or introduced to existing ones. The blocks are far cheaper, safer, lasted much longer and were more scalable than a battery and are 10% of the cost of the same size, yet produce the same amount of energy. The blocks are made from non-toxic, recyclable material with high thermal conductivity. They are made of two components: one component melts when heated to store huge amounts of energy, and the other acts as a matrix, keeping the block in solid form and embedding the melting particles. This process of heating, storing energy, cooling and recovering energy can be repeated thousands of times.
University of Newcastle Australia/Sth Korea: High purity titanium with environmental benefits
Metals and rare earth processor Australian Strategic Materials (ASM) and JV partner South Korea’s ZironTech has produced high purity (99.83%) titanium metal powder through its new electrorefining process at the commercial pilot plant in South Korea. This was the final stage of the patented metal process and it confirms 50% less energy is used than traditional methods. “This will position ASM as the only integrated mine-to-metal producer outside China, providing critical materials directly to Australian and international manufacturers” says ASM MD David Woodall.
Mining Weekly USA: Nature's antifreeze' provides formula for more durable concrete
Researchers have discovered that a synthetic molecule based on natural antifreeze proteins minimises freeze-thaw damage and increases the strength and durability of concrete while decreasing carbon emissions. Adding a biomimetic molecule - one that mimics antifreeze compounds found in Arctic & Antarctic organisms - to concrete, effectively prevents ice crystal growth. This new method challenges more than 70 years of conventional approaches, where, since the 1930s, small air bubbles have been put into concrete to protect it from water and ice crystal damage. But this process can decrease strength and increase permeability. Concrete made with this molecule instead of air bubbles was shown to have equivalent performance, higher strength, lower permeability and a longer lifespan. A synthetic molecule - PVA - was used, that behaves exactly like the natural antifreeze proteins but is much more stable

at a high pH. It was combined with another non-toxic molecule - polyethylene glycol. This molecular combination remained stable at a high pH and inhibited ice crystal growth.
University of Colorado at Boulder
Australia: First Australian-made spacecraft to host foreign payload
University of Melbourne researchers have been awarded $3.95m to build and launch a small (9kg) innovative satellite called SpIRIT (Space Industry – Responsive – Intelligent – Thermal Nanosatellite) to be launched by 2022 in collaboration with multiple Australian space industry companies and the Italian Space Agency. Though small, it will be powerful: carrying X-ray sensors, on-board computers and radios, and a miniaturised electric propulsion engine. This will demonstrate that Australian-made spacecraft are internationally competitive, opening new market opportunities. Building an innovative space-ready nanosatellite comes with unique challenges and it is expected that this project will help to break new ground in nanosatellite design and manufacturing, acting as a guide for Australian aerospace research in the future.
University of Melbourne
Germany: Additive manufacturing of multi-functional parts
A Multi Material Jetting system has been developed that allows different materials to be combined into a single additively manufactured part, making it possible to create products with combined properties or functions. The new system can be used with particularly high-performance materials such as ceramics and metal and can be used to make highly complex parts such as the ignition system in a satellite propulsion engine made of ceramics. The process relies on custom micro-dosing of the metal or ceramic slurries. Thanks to its high precision and flexibility, it is suitable for more than just manufacturing multi-functional components, but could for example be used to make blanks for carbide parts.
Fraunhofer
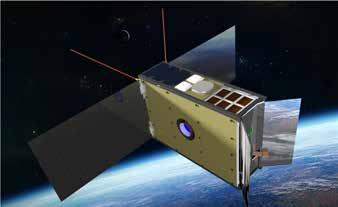
USA: Record speed with advanced spectroscopy technique
For the first time, researchers have used an advanced analytical technique known as dual-comb spectroscopy to rapidly acquire extremely detailed hyperspectral images, with the potential to greatly advance a wide range of scientific and industrial applications. It uses two optical sources (optical frequency combs), that emit a spectrum of frequencies that are perfectly spaced. Spectral interrogation of a 2D object in just one second was demonstrated, more than three orders of magnitude faster than previous demonstrations. This fast acquisition time enables dual-comb hyperspectral imaging of fast or dynamic processes for the first time. The technique was used to acquire hyperspectral images of ammonia gas escaping from a bottle. An optical resolution of 1 GHz (0.0033 cm-1) at video
rates of 25 frames per second was achieved, with each frame containing 327,680 individual spectral measurements. This allows easy distinction between different gases and 100 times better than current commercial equipment.
The Optical Society
France: Hydrogen powered train enters service in Austria
Following successful trials in Germany, the Coradia iLint – a hydrogen fuel cell powered train developed by French rail giant Alstom – has begun carrying passengers on Austria’s train network. The cell generates electrical energy for propulsion, generates zero emissions and is capable of a top speed of 140 km/h. According to Alstom, as well as being completely emissions-free, the Coradia iLint boasts a number of innovations including clean energy conversion, flexible energy storage in batteries and intelligent management of motive power and available energy. Alstom has already sold 41 of the hydrogen-powered trains in Germany.
The Engineer
Tesla has taken delivery of the world’s biggest casting machine. The aluminium caster, reportedly built by Italian die casting company IDRA, is about the size of a small house. With the Model Y electric SUV, Tesla has introduced some important underbody engineering and manufacturing improvements - turning what was originally 70 parts in the Model 3’s rear underbody into just two - facilitating body assembly and creating fewer failure points. Molten aluminium will be injected into the “Gigapress”, moulded, and removed by robots - effectively bypassing riveting and gluing. Traditional stamping results in a large amount of scrap residual while with the Gigapress, 100% of the raw material is used. There are plans to make the entire underbody in just one part by the end of the year. In Tesla’s factory in Germany, there are plans to replace hundreds of robots with the casting machines.
Reuters/Tesmanian/Electrek
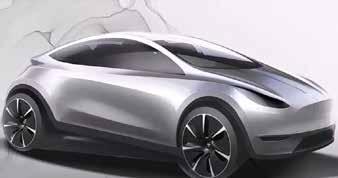
Australia: Funding for technology to detect wildfires in minutes
Fireball International - based in Queensland - has been granted $500,000 to roll-out its detection system across Australia and overseas. The system allows for fires to be reported to emergency services in as quickly as three minutes and it has already been successfully identifying blazes and alerting authorities in the US. Using the ALERT Wildfire sensor network, Fireball applies powerful machine learning combined with satellite imaging to detect and evaluate wildland fires early. The satellite used by Fireball detected the Kincade fire in California 66 seconds after a falling power line ignited it last October. The tower sensors confirmed the alarm within 3 minutes, even though it was night and the fire was in a canyon, and thus not directly visible to the sensor. Authorities were immediately alerted and a town 10 km away was evacuated 20 minutes after ignition. In San Diego County alone, Fireball reported 494 fires in October and November last year.
Industry.gov.au/Fireball.International
Singapore: Fruit peel – Turning old batteries into new
Scientists have developed a novel method of using fruit peel waste to extract and reuse precious metals from spent lithium-ion batteries in order to create new batteries. Traditional methods of recycling battery waste generates harmful pollutants. The team found that the combination of oven-dried orange peel ground into powder and citric acid can achieve the same goal. In lab experiments, the team found that their approach successfully extracted around 90% of cobalt, lithium, nickel, and manganese from spent lithium-ion batteries – a comparable efficacy to that of using hydrogen peroxide. The key lies in the cellulose found in orange peel, which is converted into sugars. These enhance the recovery of metals from battery waste. Solid residues were non-toxic. New lithium-ion batteries were assembled from this process, which showed a similar charge capacity to commercial ones.
Nanyang Technological University
USA: Real-time 3D printing quality assessment

Researchers have developed AI software (named Peregrine) for powder bed 3D printers that assesses the quality of parts in real time, without the need for expensive characterization equipment. The software uses a custom algorithm that processes pixel values of images, taking into account the composition of edges, lines, corners and textures. If Peregrine detects Peregrine detects an anomaly in a component being an anomaly that may affect the additively manufactured on a quality of the part, it automatically powder bed printer. alerts operators so adjustments can be made. During the printing process, problems such as uneven distribution of the powder or binding agent, spatters, insufficient heat, and some porosities can result in defects at the surface of each layer. Some of those issues may happen in such a very short timeframe that they may go undetected by conventional techniques. It can be installed on any powder bed system.
Oak Ridge National Laboratory
“We could well say that we will be building a tiny robotic spaceship” - Associate Prof. Michele Trenti of Melbourne University’s School of Physics and the lead investigator of the SpIRIT satellite program which obtained a grant. The program will generate wider benefit for Australian businesses and the next generation of the space workforce and the grant reflects the excellence of the researchers.