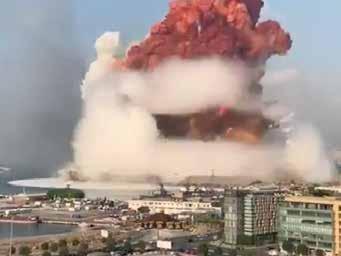
18 minute read
AMTIL FORUMS
from AMT OCT/NOV 2020
by AMTIL
Ammonium nitrate in Australia
The recent ammonium nitrate explosion in Beirut has generated questions and concerns. What are the risks in Australia? Laura Whiteman explains.
There have been a number of ammonium nitrate (AN) explosions throughout the world, with four major incidents occurring within the last 10 years. These include a fertiliser company in the US, a rolled truck in Queensland, the Tianjin explosion in China, and the latest explosion at a port in Beirut. Some of the incidents linked to ammonium nitrate are accidents, while there have been others which are labelled as suspected terrorist attacks, such as the Oklahoma City bombing in 1995 and the Hyderabad blasts in India in 2013. The question is then asked – what is ammonium nitrate used for, can it be safely handled and stored and should we have it in Australia at all? Ammonium nitrate is typically sold in pellets, also known as prills, and is a commonly used fertiliser in the agricultural industry and explosive in the mining industry. It is produced by neutralising nitric acid with ammonia, and was first discovered by a German chemist in 1659. The chemical itself is not an explosive but requires a combustible material to be present for it to explode. More than 20 million tonnes of ammonium nitrate are produced and stored worldwide each year, with Australia importing close to 112,000 tonnes. It is estimated that of the close to 2 million tonnes each year that Australia produces and stores, over 90% is produced locally. There are three main producers of ammonium nitrate in Australia, and their typical volumes as stated on their websites are:
CSBP Wesfarmers
Kwinana, WA (780,000 tonnes pa)
Orica
Kooragang Island, Newcastle (360,000 tonnes pa) and
Yarwun, Gladstone (500,000 tonnes pa)
Queensland Nitrates JV
Moura, Qld (222,000 tonnes pa) Each of these producers indicate that they generate the majority of their ammonium nitrate for the manufacture of explosives in the mining and quarry industries. According to Primary Industries & Regions SA, mining use makes up approximately 90-95% of all ammonium nitrate use in Australia, with the rest used in fertilisers. In accordance with national security objectives, in June of 2004, the COAG developed a national approach for Security Sensitive Ammonium Nitrate (SSAN). SSAN can be defined as ammonium nitrate, ammonium nitrate emulsions and ammonium nitrate mixtures containing greater than 45% ammonium nitrate by mass, excluding solutions and Class 1 Explosives. Each State and Territory in Australia has adopted their own relevant legislation for the restriction, use, manufacture, transport and storage of SSAN. Typically, this includes a legitimate reason for access to SSAN, the person being over 18 years of age, a license, agreeing to report any loss or theft of the product and a security clearance. It also prohibits the movement of SSAN into or out of any State or Territory without permission. For transport throughout Australia by road and rail, ammonium nitrate can be listed under different UN numbers in the Australian Dangerous Goods (ADG) code, depending on the concentration and other impurities in the product. The ADG code sets out the conditions in which they must be transported, including restrictions on load sizes, and that they must not be transported with any sensitising or initiating agents. One of the main types of ammonium nitrate used in Australia is classified as a Class 5.1 Oxidizing
agent, UN 1942 – Ammonium Nitrate with ≤ 0.2% combustibles. Ammonium nitrate can be listed as a Class 1 Explosive (although any information in the ADG for explosives is advisory only, and should be read in conjunction with the SSAN legislation for each State and Territory). Where ammonium nitrate is used as a fertiliser, it is typically a Class 5.1. Australia has been using ammonium nitrate for decades, with very few incidents. In SA, 170 locations store ammonium nitrate. In other states, much larger amounts are stored, sometimes close to residential areas, and resident groups are campaigning to have them moved. In a statement put out by Orica, they indicated their “team is trained to stringent accreditation standards associated to AN storage, and all AN storage areas at Kooragang Island are fire-resistant, built exclusively from non-flammable materials, and have designated exclusion zones around them”. With such stringent regulatory requirements and the conditions needed for an explosion to occur, the risk becomes minimised. The States and Territories are well aware of the potential issues and determined that it was better to regulate its transport, use and storage, rather than banning ammonium nitrate. So what does all of this mean for ammonium nitrate in Australia? Are there any alternatives? For fertilisers, the University of Missouri has been researching suitable plant-friendly, nitrogen-rich alternatives to AN. They are investigating ammonium sulfate as well as Urea, with both offering a source of nitrate. There are also studies presented at the 43rd Annual Conference on Explosives and Blasting Techniques, into the development of ammonium nitrate-free mining explosives. Some of the initial work conducted has identified three possible alternatives, although further research needs to be undertaken. While suitable alternatives are being evaluated, strict regulatory control around ammonium nitrate has led to a relatively low number of incidents in Australia.
Laura Whiteman is a senior regulatory specialist at UL Materials & Supply Chain, which provides innovative material and regulatory data solutions for a transparent and sustainable product supply chain. With fully automated chemical compliance software platforms, industry-leading data resources and a global network of regulatory expertise, UL removes barriers and solves critical challenges to help companies stay one step ahead of global regulations. customerservice.anz@ul.com Ph: 03 9846 2751 msc.ul.com
Why using an insurance broker makes good business sense
With millions of individual insurance policies offered through multiple brands, it can be difficult to find the one which works best for you. It is for this reason that insurance brokers are a valuable guide, as explained by BMS.
As a business owner, it can be tempting to seek short cuts to find your best-fit insurance cover. The internet offers you an overwhelming range of options, but it can be tricky to work out the right cover to suit your business needs (and cheaper is not always the best). You could have then taken out a policy because it was quick and ticked most of your boxes. Maybe the impact of COVID-19 has belatedly made you take to the fine print with a magnifying glass. For example, did you have a chance to check the independence of the comparison website? Social proof might have weighed in on your decision-making too, rather than doing your usual due diligence. Spoilt for choice With millions of individual insurance policies offered through multiple brands, and distribution channels across Australia, insurance brokers are a valuable guide to help businesses determine which policy offers the best fit for their needs. It can be hard work finding the right one. A quarter of sole traders have no insurance, according to an Industry Council of Australia report. Meanwhile, one in 10 businesses underinsure their business assets, saying: • “I can’t afford to pay more for insurance.” • “Premiums are too high”, or • “You can never be adequately insured.” Maybe you’ve thought or said the same about your own business? DIY insurance cover is not your best bet In short, businesses need to protect their assets, customers, employees, business owners, and earnings. There’s plenty more that companies might need to insure, including compulsory coverage. If you’ve gone for the Google ’quick-fix’ option, you could be paying higher insurance premiums after an initial honeymoon period. Chances are you’ll need to renegotiate with an insurance company for a better rate or elect to take a higher excess to reduce your premiums. This will need to be repeated for each of your policies. Would it make better business sense to deal with the same person for all of your business insurance policies? Someone who’ll guide you when your policy needs reviewing, provide regular updates and take the stress out of insurance for you. This is where we come in. Insurance brokers manage more than 90% of commercial insurance transactions in Australia. What insurance brokers do As insurance brokers, it’s our business to navigate the information tsunami. We offer professional advice with expertise in insurance and risk management. Our aim is to scaffold business growth - and support you in selecting your best-fit insurance cover. Once you’ve purchased the policy, we keep tabs on it, your circumstances, and how it relates to you. We drill down into insurance products and policies for insights into the finer details such as the: • Terms and conditions in the policy • Benefits (also known as optional inclusions) • Exclusions (these are critically important to ensure you don't have nasty surprises when you need to make a claim)
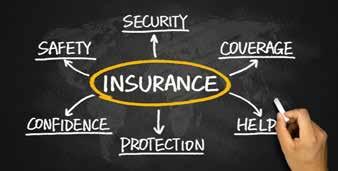
• Costs of a diverse range of competing insurance policies, and • Validity of the insurance cover when there are changes in the business. We’ll also advocate for you when making a claim, seeing that process through and allowing you to focus on running your business. A licence to broker To become a broker, we’ve each undertaken training and must successfully apply to the Australian Securities & Investments Commission to secure an Australian Financial Services Licence. We can also do this work as a representative of a licence holder. This licence compels insurance brokers to provide “efficient, honest and fair financial services” and to comply with the Corporations Act 2001. We must also follow the Insurance Brokers’ Code of Practice. Safety (and savings) in numbers Licencing, laws, and the code of practice give a broker’s client great peace of mind. Once we’ve discussed your insurance needs and risk management issues with you, we could suggest bundling policies together to offer you savings. But, if you prefer to spread your policies among different insurers, you’ll still do well to use a broker. In fact, that process helps pre-qualify you for a policy in the eyes of an insurance company. They see you as a lower risk because you’ve taken on board your broker’s expert advice. That’s why brokers can access better rates for their clients than if a business dealt directly with an insurance company. Having a broker on your side helps make you more savvy about risk management in your business. It’s a proven way to ensure you have sufficient cover for your risk exposure, leaving you to get on with what you do best - running your business.
BMS is a dynamic global broker that provides specialist insurance, reinsurance and capital markets advisory services. The company was established in 1980. Today, $2.6bn of premiums are placed each year and more than 450 people are employed worldwide. BMS is growing fast and has 19 offices around the world in key hubs including London, New York and Bermuda. The BMS team is highly experienced and respected in the market. We value our strong personal relationships with clients and contacts which – together with our entrepreneurial flair – enable us to get the best solutions for our clients. ph: 1800 290 978 amtil@bmsgroup.com www.bmsgroup.com
COVID-19 and its impact on manufacturing supply chains – force majeure?
Nathan Cecil looks at the force majeure framework likely to come into play as a result of the global supply chain disruption caused by COVID-19.
The COVID-19 outbreak signifies an unanticipated and overwhelming event, so far infecting approximately 27.6 million people worldwide and resulting in the death of at least 898,000 (these figures will tragically be materially out of date as soon as this article is published). Naturally, the primary focus is on the human impact, with measures being taken by governments to limit the spread of the virus. Actions by government authorities in quarantining areas and shutting down businesses and restricting movement have caused significant disruption to supply chains around the world. As a result, manufacturing and distribution have been significantly impacted. The extent of supply chain disruption Supply chains the world over have been adversely impacted by the impacts of the COVID-19 crisis in two significant ways: • Workforces have been impacted by infection and workplaces have been impacted by mandatory worker limitations and shut-downs as a result of infection incidents and/or mandated closure. • Procurement supply chains have been impacted as a result of the above impacts on the businesses of suppliers (impacting their ability to provide supply of input materials and components) and also through the interruption to logistics networks as a result of border closures, both hard and soft. The situation and its impacts are mercurial, sometimes shifting beneath our feet on an hourly basis. Faced with these circumstances, the immediate questions for manufacturing businesses include: • What remedies are available to me in respect of the delay or failure of my suppliers to supply me? • What relief is available to me in respect of my delay or failure to meet my obligations to customers? Unfortunately, most supply arrangements did not foresee anything like the COVID-19 situation arising and so do not contain any clear roadmap as to how businesses are to navigate their contracts in the current circumstances. As a result, most businesses are looking to their contracts (e.g. supply agreements, distribution agreements, manufacturing agreements, transport and logistics agreements) to see whether ‘force majeure’ provisions may be used against or by them and whether there are any other ways to avoid the adverse impacts facing them. Force majeure A force majeure (literally ‘superior force’) clause allows one or both contractual parties to cease or suspend performance of a contract following the occurrence of a pre-defined ‘force majeure event’. If successful, the party will not be liable for failing to perform its obligations under the contract. It may also give rise to termination right, usually where the force majeure event continues for an extended period. In most common law countries, such as Australia, there is no independent legal concept of ‘force majeure’. As such, it is a creature entirely of contract and the scope and effect of any such clause is dependent on its particular terms. In most cases, they contemplate acts of God, extreme weather events, riot, war or

invasion, government or regulatory action including strikes, terrorism or the imposition of embargo as being ‘force majeure events’ in respect of which a party may be relieved of their liability for failure to perform. Many such clauses also extend to include pandemics or epidemics, which may apply in the current circumstances. It is also important to consider whether the clause in question applies only to ‘direct’ impacts of a force majeure event or also extends to ‘indirect’ impacts. Unfortunately, many manufacturing arrangements drafted from the ‘buyer’/‘customer’ perspective exclude failure to secure supply of materials or components from being a force majeure event. If a business is seeking to invoke force majeure, it must consider carefully whether it is able to do so under the relevant contract. A party could be in breach of contract, risk termination and potentially damages claims if it fails to meet its obligations and cannot rely on force majeure, or if it invokes force majeure and ceases to perform when it is not entitled to do so. To successfully invoke force majeure, a business will also need to ensure compliance with any other contractual obligations that may include providing prompt and correct notice and seeking to mitigate any loss that might otherwise be suffered (e.g. by seeking alternative sources of supply or alternative ways to perform the contract). It is equally important to proactively consider whether your counterpart might be able to rely on a force majeure clause to delay or avoid its performance obligations, so that you can prepare for this possibility and assess in advance whether it will impact your arrangements further downstream. If your suppliers are unable to rely on force majeure, it is more likely that they will be liable to compensate you for any delay or failure to perform the supply. If you are able to rely on force majeure, it is more likely that you will be able to claim relief from your delay or failure to perform. Given the potentially significant impact on your legal rights and obligations, you should be looking into this issue now, so that you can navigate a course through this outbreak.
Nathan Cecil is a Partner in the national Transport, Shipping & Logistics group at Holding Redlich; a large national independent Australian law firm with offices along the East coast. Holding Redlich partners with many Australian manufacturers, importers and distributors in relation to their Australian and international operations, assisting them with their commercial issues, regulatory compliance and resolving disputes. Nathan.cecil@holdingredlich.com Ph: 02 8083 0429 www.holdingredlich.com
There are multiple opportunities to address lead exposure risks within the advanced manufacturing sector, as explained by Phoebe Gane.
Lead is an abundant heavy metal with diverse industry applications due to its low melting point, electrical conductivity, high density, malleability, and chemical stability. There are, however, numerous associated adverse health effects of exposure including impacts to the nervous, cardiovascular, skeletal, immune, gastrointestinal, reproductive, and urinary systems. Inorganic lead and organic lead compounds are also classified as a Group 2A - Probable Carcinogen to humans by the International Agency for Research on Cancer (IARC). The use of lead has consequently been phased out of many of its former applications such as in fuels and paints. However, lead and lead alloys continue to be utilised in the production of leadacid batteries, alloys for solder and ammunition, some plastics, protective coatings and ceramics, and therefore remains a hazardous chemical of concern for industry. Legislative duties Australian Model Workplace Health and Safety (WHS) legislation states Persons Conducting a Business or Undertaking (PCBUs) must ensure that workers are not exposed to hazardous chemicals, including lead, at concentrations higher than the relevant exposure standard. Model WHS Regulations also include specific additional requirements for work activities with potential for significant lead exposure - referred to as lead processes. Where lead processes are undertaken, PCBUs must identify whether ‘lead risk work’ is carried out in their workplace and, as part of wider risk controls, implement routine health surveillance to ensure the level of lead in workers’ blood does not exceed acceptable ‘blood lead levels’. Lead processes in the manufacturing industry include production/ recycling of lead-acid batteries; melting or casting lead or alloys; handling lead compounds such as lead UV stabilisers and dry lead pigments; machining or foundry processes involving lead or lead alloys; and welding, cutting or cleaning leaded, or lead-paint coated steel. Routes of exposure Lead is not readily absorbed through the skin and most human exposure occurs rather via inhalation of dusts and fumes contaminated with lead, or by ingesting lead-contaminated particles. Additional exposure routes also include dermal absorption; absorption from retained or embedded leaded foreign bodies; or even trans-placental (endogenous) routes. IARC research (completed 2006) identified workers with the greatest potential exposure risk in the manufacturing industry to be those directly employed in production undertaking tasks such as machining, welding, and soldering. The production and recycling of lead-acid batteries also presents a high exposure risk, albeit to a relatively small group of workers within Australia. Controlling exposure There are multiple opportunities to address lead exposure risks within the advanced manufacturing sector. Industry trends and technological innovations can, in the longer term, reduce the potential for workplace lead exposure, for example by elimination through replacement of lead-acid batteries with lithium-ion batteries, or via transitioning away from lead-tin solder. The establishment of the Advanced Robotics for Manufacturing (ARM) Hub in Queensland supports accelerated industry uptake of process automation for activities such as welding and metalwork through the use of innovative technologies such as collaborative robots, augmented and virtual reality and robotic vision. Advances in offline robot programming, and its interaction with 3D modelling software, allows greater flexibility in the use of plasma cutting cells, welding cells and other automated processes, giving greater flexibility and opportunities for substitution of traditionally manual production processes. Whilst these advancements will certainly play a role reducing exposure, there are also readily accessible control mechanisms immediately available to individual PCBUs including: • Engineering Controls including ventilation systems to control welding fumes; and dust suppression, extraction and filtration technologies to minimise lead inhalation risks. • Administrative Controls including amended shift patterns and task rotation to reduce the exposure duration for individual workers. • Use of PPE - the training, use and maintenance of appropriate PPE and Respiratory Protective Equipment (RPE) can provide an additional layer of protection to workers. Ensuring effective risk control and compliance with legislative duties The development of an Occupational Health and Hygiene RiskBased Management Plan (OHHMP), followed by implementation of exposure monitoring and assessment programs, provides PCBUs with robust tools for WHS compliance. OHHMPs and associated monitoring help to identify potential occupational exposure risks for workers; document processes to manage these risks; define the controls; and monitor the process by which efficacy of these controls is confirmed. When combined with operational and appropriately designed engineering and administrative control systems, the ongoing and future technological advances and innovations in production, assembly and manufacturing processes have the potential to transform the risk profile of lead exposure within the Australian manufacturing industry. Notwithstanding this, continued application of robust processes to identify, assess and mitigate lead risks are critical to ensure a safe and healthy work environment for workers, and drive best practice in accordance with WHS legislation.