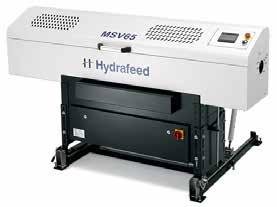
18 minute read
PRODUCT NEWS
from AMT OCT/NOV 2020
by AMTIL
Hydrafeed and Dimac – A winning combination
In recent years it has become common knowledge that a barfeeder significantly increases any CNC turning centre’s productivity. But like any piece of equipment, not all barfeeders are created equal.
The Hydrafeed barfeeder offers a number of unique features. One of those is that it is a full servo-driven barfeed eliminating the need for compressed air. It can also accommodate different bar diameters and lengths including random bar lengths, and is suitable for both bar or shaft feed. One of the most important time-saving features of the Hydrafeed is that once you’ve set a bar size and saved the set-up, you never have to open the cover again. Simply call up the program from the touch screen and the Hydrafeed will set itself on the centreline automatically thanks to the servo drive bar lifter mechanism. “This feature alone puts the Hyrdafeed Barfeeder on a different level and really does take barfeeder productivity to a new level,” said Paul Fowler, Managing Director of Dimac Tooling, suppliers of the Hydrafeed barfeeder. “It’s also quick and easy to set up which helps businesses to remain flexible as they can run small batch jobs without excessive set-up times.” Other standard features include complete servo control on all axes plus a fully automated set-up through a user-friendly HMI screen. The product is CE-certified and comes with a comprehensive 12-month warranty. The quality and features of the Hydrafeed is what has attracted numerous customers to the brand. Greg Humphries from Tasmanianbased Maltec Engineering chose the Hydrafeed as it offered a number of features over and above their existing barfeeders. “The ability to quickly set up the servo-driven backstop when processing multiples of non-barfed material is a real time saver compared to having to manually set-up and fit one,” said Humphries. “Having the barfeeder mounted on linier rails allows us to move it out of the way and accurately return it to its previous position when machining longer parts or servicing the machine.” guiding stage for the machining of steel.
When undertaking the fine machining of steel, long chips can prove detrimental to machining performance and surface finishes, especially when machining with tools that incorporate guide pads. To prevent long chips from wrapping around the tool and creating a negative impact on surface quality, dimensional accuracy and automated process flow,
Mapal has introduced the new line of inserts with chip guides.
The new chip guiding stage combats these very problems; a credit to the new geometry design. With a special geometry that has been designed and optimised with extensive finite element method (FEM) analysis and practical testing, Mapal now
It is not just the quality of the Hydrafeed that has seen many customers choose the brand – it is the quality of Dimac’s service and support that has been a key reason for purchase. “After the Hyrdafeed was installed we received a follow-up to ensure that the machine was functioning correctly and met our expectations,” Humphries added. “We have always received terrific service from the team at Dimac – reliable and timely service is very important to us,” he went on to say. It was the same experience for Jorge Campagno of Campagno Engineering in Melbourne. “Price of course was important in our purchase decision, but it’s the support and service from the supplier which I believe is crucial, as wasted time becomes very expensive,” said Campagno. “I’ve been dealing with Dimac for 30 years and it’s their knowledge, quality products and after-sales support that was another key reason for opting for the Hydrafeed.” To further enhance productivity, Dimac offers the Royal Rota-Rack; a patented, cost-effective device that safely collects finished parts as they come off of a CNC lathe, providing a competitive advantage to manufacturers by enabling their machine tools to run unattended for extended periods of time. “We can now offer CNC owners a unique retrofit automation solution to improve both productivity and efficiency whilst protecting the finished product,” said Fowler. “By using a Hydrafeed Barfeeder and a Royal Rota-Rack working in conjunction, you can add a massive dose of productivity, keep your machines running long after your last employee has left for the night or weekend and improve your competitiveness in the market. They can be retrofitted to any entry level CNC machine as well as multi-tasking turning centres. It’s really
Mapal: Getting chips under control
To ensure reliable chip breaking and the optimal machining performance, Mapal has now developed a new chip
the ultimate in ‘lights-out’ production.” www.dimac.com.au
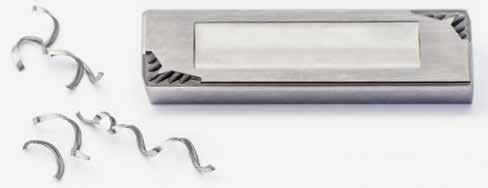
ensures that chips are broken reliably. This prevents automated workflows and production environments from being disrupted. The chip guiding stage is compatible with all indexable inserts with AS leads. Furthermore, the new chip-guiding inserts are available with a wide variety of coatings to support the machining of a vast selection of material types. That means the new chip guiding inserts can be integrated with the relevant inserts irrespective of the application in question.
www.mapal.com
Bridgman brings in cost-effective laser cutting with Bystronic
When Queensland manufacturer Bridgeman Stainless Solutions decided to invest in a laser cutter, it found the solution it needed with Bystronic Australia.
Based in Brendale, north of Brisbane, Bridgeman has been in operation for over 20 years. During this time the company has evolved into a specialist in stainless steel fabrication, with the ability to undertake fully customised designs, engineering and installation. Bridgeman’s work can be found in restaurants, shopping centres, domestic and commercial kitchens, and bespoke bars , as well as for leading food manufacturers in Queensland and across Australia. A key to Bridgeman’s success has been its ability to work within tight deadlines while producing complex solutions. To enhance this capability, the company recently moved into brand new purposebuilt facilities with greater floor space. The nature of Bridgeman’s activities necessitated working around the clock and on weekends to meet tight deadlines. Third-party supply for profile parts also created delays. This prompted Bridgeman to investigate the purchase of a laser cutter for internal use. When Bridgeman began narrowing down the list of potential suppliers, Bystronic was identified as a leading manufacturer. To support the case for investment, several companies were asked to provide time and cost studies. The Bystronic BySmart Fibre 4kW laser provided ample evidence to Bridgeman that this was the way forward. Purchase price and operational efficiencies were important to Bridgeman. A chance meeting with one of Bystronic’s service technicians during an equipment demonstration at a reference customer offered real insight into the support that Bystronic offered. That meeting also provided the reassurance that Bystronic had technicians based in Brisbane, rather than flying in. The operational efficiencies have been greater than anticipated. The speed and efficiency of the laser, coupled with the accuracy and repeatability that can now be achieved, have further enhanced Bridgeman’s profitability. The company has found that it is turning jobs around in days that would have taken weeks, and there has been a substantial reduction in the amount of scrap metal due to reworks. Paul Walmsley, Finance Manager at Bridgman, notes that cutting operations are particularly simple due to the ease of use of the Byvision software installed with the machine. The original plan had been to have dedicated operators at the laser, but the intuitive interface has allowed for a number of confident people to be trained quickly in the machine’s use. In dealing with Bystronic, the team at Bridgeman has been reassured by the strong support it received during the sales and installation phase, and its ongoing access to Bystronic’s dedicated hotline. With further investment in equipment planned in the future, Bridgeman expects to look to Bystronic again.
www.bridgeman.com.au www.bystronic.com
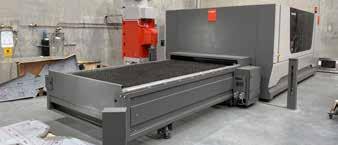
Konecranes – New C-Series lasts more than a million lifting cycles
Konecranes is introducing to Asia-Pacific its toughest and most reliable electric chain hoist for lifts up to five tonnes, with extended service life for more than one million lifting cycles.
The new Konecranes C-Series – now launched in Australia, Singapore, China, and Malaysia, with the rest of the APAC region to be included progressively in the months ahead – is designed to be the most durable electric chain hoist available, to provide a hard-working industrial hoist for industries such as manufacturing, materials handling, infrastructure, power generation, steel, automotive and waste-to-energy. “The new Konecranes C-Series is designed for operators seeking minimal downtime and long hoist service life,” says James Dowe, Managing Director, Konecranes Australia & New Zealand. “It has an entirely new workhorse motor, improved chain sprockets, proven braking technology, enhanced operator comfort and simple serviceability.” The Konecranes C-Series features a new motor engineered for optimum efficiency with enhanced built-in cooling to reduce heat build-up and extend power to the hoist. The enhanced cooling, coupled with its extended cycle duty factor, allows for longer continuous operation up to 60% ED compared with the standard 40%. (“% ED” refers to Intermittent Duty Rating, which shows how much time a motor can be operating within a given period of time – maximum 10 minutes.) “Rigorous in-house testing has resulted in Konecranes’s most reliable and long-lasting motor to-date,” adds Dowe. “The longevity of the motor also reduces the need to service the hoist as often, further reducing downtime.” To keep busy operations moving, Konecranes has designed improvements into the core components of the new hoists to boost their service life, enhance safety and improve performance. New features include: • Purpose-built long-lasting gearbox. The new lifetimelubricated gearbox is capable of greater speeds, low noise levels, and enhanced performance and safety – with a new safety clutch design. • Redesigned sprocket. The new sprocket fits seamlessly with the hoist chain drive. The pairing decreases hoist downtime and provides smooth, consistent performance.
The new laser enables more advanced welding capabilities for high thermal conductivity metals, and aligns to welding requirements for e-mobility, energy storage, and general electrical interconnects consisting of dissimilar materials, such as copper and aluminium, and foil stacks that require precise control. The new technology represents a significant improvement in simplicity, and overcomes the limitations of other joining technologies. The latter include unstable welds due to welding head wear and the large heat-affected zone caused by ultrasonic or standard fibre laser welding. The ability to move beyond the limitations of traditional fibre laser for welding thin conductive materials is possible because of a unique dual beam output (the centre beam surrounded by a ring beam). The centre beam has extremely high brightness (the nominal beam parameter product (BPP) is 0.6) allowing a smaller spot size compared with its multi-mode
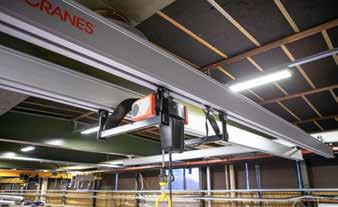
• Proven braking technology. Konecranes’ brakes are designed to last more than one million operations, and the
Konecranes C-Series includes improved self-adjusting brakes with a longer coil life. Safety is enhanced with a brake that always engages, even in cases of power loss. The new Konecranes C-Series has been designed for efficient use of available working space. A new top bracket design allows easy installation, positioning the hoist in an optimal position to have less wear between chain and chain guide. “In addition to user comfort features, the hoists are fast to install and simple to maintain, to maximise uptime,” says Dowe. “There is easy access to all wearing components, so the hoist can be up and running in minutes.” The new Konecranes C-Series hoists, along with the complementary Konecranes S-Series hoists, have been recognised by Design Forum Finland, winning the 2020 Fennia IPR Excellence prize for the protection of intellectual property rights and with the S-series earning honourable mention for the top design award. The Fennia Prize competition awards companies and organisations that use design strategically in their business operations.
Coherent – Major leap in fibre laser welding technology
The new Coherent HighLight FL4000CSM-ARM fibre laser builds on the success of Coherent HighLight ARM fibre laser series that is already qualified for automotive applications.
www.konecranes.com
counterpart. The small spot size results in very high laser intensity that minimises heating of the material, and, together with the preheating effect achieved by the ring beam, significantly improves stability of the melt pool and therefore weld consistency – a challenge when welding thin conductive materials. The Coherent HighLight FL4000CSM-ARM is available with an output power of 4kW (a 1.5kW centre beam and a 2.5kW ring beam). As with other Coherent Adjustable Ring Mode lasers, power in the centre and ring beams can be independently varied and modulated. The CSM-ARM is supplied with a 15m length process fibre, making it easy to integrate in virtually any production environment, and is compatible with the standard process heads from Coherent and other manufacturers.
www.coherent.com

Kennametal introduces KCS10B for Superalloy Applications Kennametal has introduced KCS10B, its newest and most advanced turning grade for nickel, cobalt and iron-based superalloys used in aerospace and other high-temperature applications.
KCS10B, which features a revolutionary coating applied to an ultra-fine grain carbide substrate for superior layer adhesion, delivers up to 50% greater tool life, more predictable processes, and improved productivity when working with difficult-to-machine superalloys. KCS10B overcomes the most common challenges encountered in turning superalloys – cratering and depth-of-cut notching – two wear modes that often lead to unexpected and even catastrophic tool failure. Robert Keilmann, Senior Global Product Manager – Turning at Kennametal, explains that the secret behind the success of KCS10B is the company’s proprietary High-Power Impulse Magnetron Sputtering (High-PIMS) technology. Rather than the light rain of droplets that fall on cutting tools during traditional physical vapour deposition (PVD) coating processes, High-PIMS generates a fine mist of AlTiN, building a series of “extremely thin, smooth, and wear-resistant layers”. Metals such as Inconel 718 and Stellite 31 are notorious for causing rapid wear and unpredictable tool life. KCS10B is proven to reduce The electric Soft Gripper is food-grade certified (complies with FDA 21 CFR for non-fatty items and EC 1935/2004) and unlike traditional vacuum grippers, it requires no external air supply, so it can reduce both cost and complexity. “Our new Soft Gripper is challenging existing solutions for picking hard-to-grasp, delicate and odd-sized items,” says Enrico Krog Iversen, CEO of OnRobot. “Unlike proprietary solutions, the Soft Gripper offers seamless integration with most collaborative robots and light industrial robots through our One System Solution.” OnRobot’s award-winning One System Solution is a platform that provides a unified mechanical and electrical interface between leading robot arms and any OnRobot end-of-arm tooling (EoAT). The One System Solution has been newly expanded to include integration with robots from ABB Robotics and Hanwha Precision Machinery. Now, users of those robots can take advantage of the unified mechanical and electrical interface of any OnRobot product, for easier integration and faster return on investment (RoI). While the Soft Gripper is ideal for food & beverage applications, it also provides flexible, delicate gripping for manufacturing and packaging. Features include: • Payloads up to 2.2kg based on shape, softness and friction of items to be handled. • Grip dimensions ranging from 10mm-118mm depending on cup used. • FDA certification. • Flexible, interchangeable silicon cups. depth-of-cut (DOC) notching and extend tool life from three minutes to upwards of five minutes in roughing operations. Tool life in finishing operations fares even better, with visible cratering and subsequent tool failure often delayed by a factor of two or three compared to competitive brands. Positive and negative rake inserts are available, as well as various chip formers, edge preparations, and geometries, making KCS10B the ideal solution when turning iron-based (S1), cobalt-based (S2), or nickel-based (S3) alloys. “Aside from a smoother surface, the new coating process also allows us to create a much sharper edge,” Keilmann adds. “Our advanced honing and edge-preparation process reduces the friction that leads to heat, which further improves tool life. It also means less built-up edge, another common failure mode in super alloy materials. “When coupled with the excellent dimensional accuracy that Kennametal turning inserts are known for, shops can now expect the increased performance, stability, and predictability needed to be
OnRobot – Soft gripper for challenging pick-and-place applications
The flexible OnRobot Soft Gripper uses three interchangeable silicon-molded cups in star and four-finger configurations to pick up almost any small object under 2.2kg with a delicate, precise touch.
successful with these challenging alloys.” www.kennametal.com

• Ideal handling for delicate objects and irregular shapes. • No need for supplied air. • Fast, flexible deployment with seamless integration on all major robot brands. IDC has forecast that global spending on robotics systems and drones will reach $128.7bn for 2020, with spending expected to reach $241.4bn by 2023. AlphaBeta estimates that automation can boost Australia’s productivity and national income by $2.2 trillion by 2030, while leading to the development of new products, services and business models. www.onrobot.com
McIntosh Farm Machinery selects SYSPRO
McIntosh Farm Machinery has selected enterprise resource planning (ERP) specialist SYSPRO to help the company expand its highly customisable range of agricultural machines that it supplies in New Zealand and Australia.
McIntosh specialises in supplying quality forage and feed-out wagons, tip trailers, manure spreaders and bale feeders to farms and vineyards and wanted to replace its existing ERP system to significantly improve its production and scheduling capabilities. The company has been designing and manufacturing reliable farm and agricultural machinery for more than 60 years from its Palmerston North production facility on New Zealand's North Island, after being established by the McIntosh brothers as a farm equipment maintenance business. The company provides its farming equipment through over 200 trusted dealers across New Zealand, Australia and Chile. The firm had concerns over its ability to plan for future customer orders, ensuring it had the right stock on hand to meet production needs. The management team also felt that as a family-run business with a loyal longstanding workforce, much of the knowledge and expertise is in people’s heads. Many processes are paper-based, and the company has over 6,000 production drawings featuring around 20,000 parts. “We found our former system to be incredibly inflexible and the technology was too complex for our current workforce to grasp,” said Managing Director Brett McIntosh. “What we really needed was a more flexible ERP system that was built around simplifying the manufacturing process and would improve our ability to plan ahead. We selected SYSPRO ERP for its ease of use and strong scheduling and planning capabilities.” McIntosh has fully embraced automation at its high-tech manufacturing plant, with a Yaskawa robot welder and Hypotherm plasma cutter being some of its smart factory investments to date. The next part of the company’s Industry 4.0 strategy was to replace its existing ERP system. Implementing SYSPRO will enable the equipment manufacturer to manage its endto-end supply chain, from inventory management, production and bill of materials (BOM), part traceability, quality control and financials, which is being implemented first and will go live in November. Additionally, the company requires the new ERP system to integrate with CADTalk and other software such as payroll.
ABB is providing integrated safety functionality for its all-compatible variable speed drives (VSDs) to simplify the engineering design process in machine manufacturing and automation. The new plugin PROFIsafe module (FSPS-21) removes the need for external safety components and reduces the need for configuration.
Machine builders must ensure applications can be controlled safely and stopped quickly if anything goes wrong. To meet demanding safety requirements, engineers have traditionally designed and installed safety functions using external (hardwired) devices. This usually requires additional installation space as well as being costly and time-consuming. These challenges can now be overcome by using drivebased safety solutions.

“We are excited to be working with SYSPRO and its channel partner, MNM Business Solutions, to implement our new ERP system,” Brett McIntosh continued. “The SYSPRO platform will help us to continue developing innovative new products and will enable us to maintain our reputation as a quality provider of robust farm machinery that is delivered on schedule.” The rolling implementation will be completed during 2021 and its workforce will receive practical training as each major phase goes live. “Implementing SYSPRO will enable McIntosh Farm Machinery to improve its production scheduling, streamline and simplify its manufacturing operations and automate its new equipment design processes, whilst providing end to end supply chain management and part traceability,” said Rob Stummer, CEO at SYSPRO Asia Pacific. “Together with our partner MNM Business Solutions, we are excited to be working with this highly innovative and trusted farm equipment developer that is positively impacting the production of food and wine across New Zealand and Australia to ensure it remains competitive in the future.”
ABB integrates drive safety functionality to simplify machine automation ABB’s PROFIsafe plug-in module with integrated safety functions for variable speed drives provides cost-effective safety functionality to simplify installation and commissioning.
www.mcintoshfarmmachinery.co.nz www.syspro.com
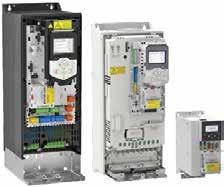
The new functionality enables safe machine control and seamless safety communications between the drive and the programmable logic controller (PLC) in a wide range of machines from conveyors to grinders. This is enabled through the PROFIsafe over the PROFINET IO communication protocol. The FSPS-21 module is TÜV Nord-certified and is compatible with ABB ACS380 machinery drives, ACS580 general purpose drives and ACS880 industrial drives. The module offers Safe Torque Off (STO) and Safe Stop 1-time controlled (SS1-t) safety functions. It achieves the highest safety levels in machinery safety: SIL 3 / PL e and is, therefore, suitable for even the most demanding applications and simplifies the design and verification of the safety solution. www.abb.com/au