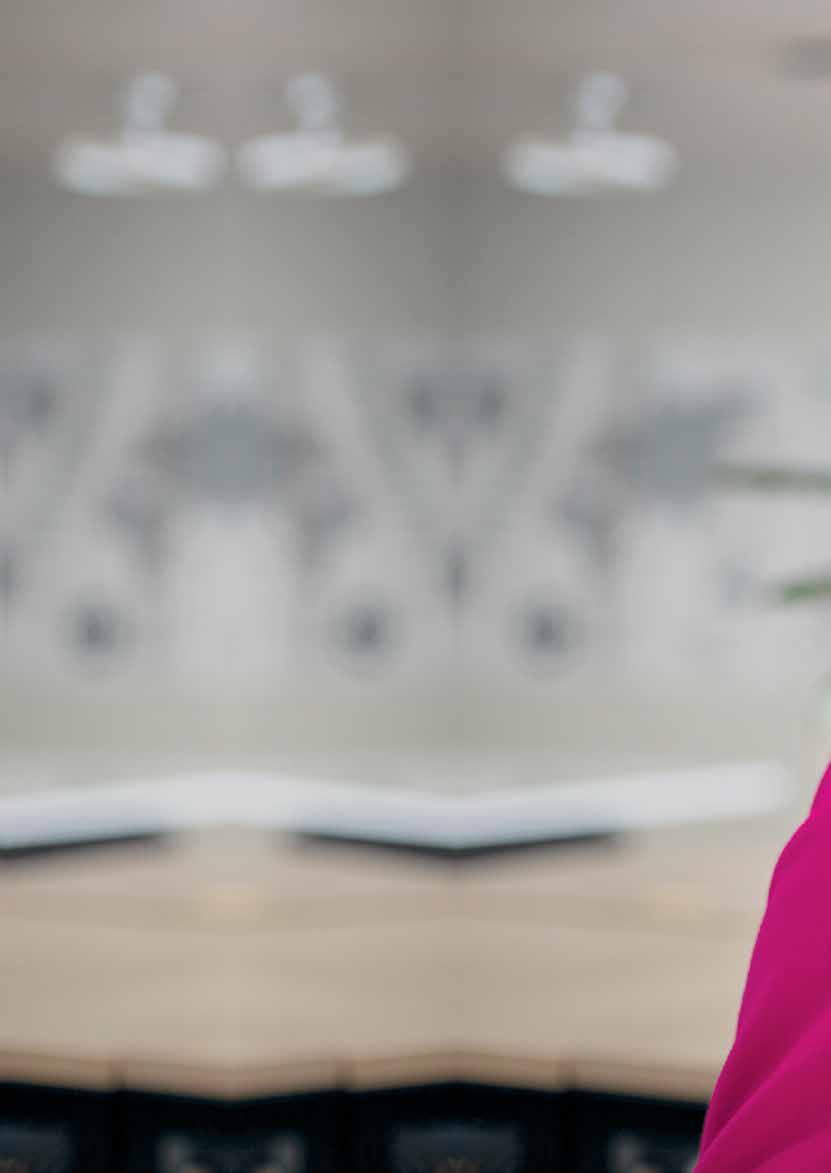
14 minute read
ONE ON ONE Professor Bronwyn Fox
from AMT OCT/NOV 2020
by AMTIL
Professor Bronwyn Fox is the Deputy Vice-Chancellor (Research and Enterprise) at Swinburne University of Technology. She spoke to William Poole.
AMT: Swinburne has always been very active in the manufacturing space. What can you tell us about any projects and initiatives you’ve got on at the moment in that area? Bronwyn Fox: Well, Swinburne has a really deep history in manufacturing, and that comes from our founder, George Swinburne himself. He did a world tour in about 1897, where he travelled the world, looking at energy technologies. He went to the UK and the US and looked at gas and electricity, which were emerging as competitive technologies, and he realised that actually the solution would be to integrate the two systems. I think that that holistic approach of George Swinburne, to integrate different, seemingly competitive systems together to create a better outcome, is a part of our history and part of our DNA at Swinburne. So it’s really exciting to be here, it’s a very creative environment. Most recently, we’ve been really focused on our Industry 4.0 strategy. My former role was heading up Swinburne’s Manufacturing Futures Research Institute, and when we launched that in 2016, it was the first institute in Australia to focus on Industry 4.0. It raised a few eyebrows at the time – some people thought ‘Oh you know, this will never catch on’ – but it has turned out to be really ahead of its time. We could see what was happening in Europe. We could see this emerging trend of the digitisation of manufacturing and thought that it was such an opportunity for Australia and other developed economies. It brings us back into competition because it’s independent of labour costs, and yet it enables you to scale, which also creates more jobs at the same time. So a great opportunity for Australia. And since then we’ve worked with industry extensively: everything from the automotive sector to the aerospace sector, to the food and beverage industries. We’ve worked on new materials and photovoltaics, and looked at how digitalisation can transform these industries. It’s been a really fun and exciting adventure, and we’ve got a great team of researchers who are really industry-engaged and down to earth, and able to talk with industry and listen to them, hear their challenges and help solve problems for them. There’s also some really inspiring work being done around sustainability and the circular economy. One of our staff members, Dr Stacy Konash, works in our Factory of the Future facility, and she has actually been awarded a Fulbright fellowship to look at the circular economy in particular. I’ve been working with her on a project with a company called Mallinda in the US, who have an incredible technology for completely recycling carbon fibre composites. They have a resin system that can be completely recovered, as well as the fibre, which can be recovered in strips and continuous fibres, rather than having to be chopped up, where you lose the properties. To actually recover the fibre and the matrix is really hard, and that’s what this start-up Mallinda is able to do. AMT: Obviously the COVID-19 pandemic has been a challenging time. How has it affected Swinburne? BF: Every university is experiencing challenges, particularly with respect to our budgets, which have all dropped due to our inability to enrol international students, who have really brought so much to the diversity of our community and are such an important part of the
fabric of our university and the way that we do research. So that’s been particularly challenging. What’s really inspired me is the resilience of our researchers and where they’ve been able to look at finding creative solutions. We’ve had researchers working on everything from developing a carbon fibre stretcher for carrying patients, to 3D printing copper door plates, because copper has been shown to be more resistant to viruses than other materials. One of my favourite projects involved an epidemiologist who got together with an astrophysicist at a coffee machine. Our leading epidemiologist Richard Osborne had come up with a very well thought-through questionnaire for tracing the transmission of influenza. He’d had that translated into more than 50 languages. And he bumped into Matthew Bailes, who being an astrophysicist is naturally au fait with data analytics and data visualisation, and he said: “Why don’t you create an app out of it?” Within 40 days they had held a hackathon and had a workable version of that. And I think it really will come into its own as we start to open up society more. It’s a symptom tracker where rather than just tracking the contacts of someone who’s been tested positive, you’re actually looking at the symptoms that are leading to that positive test. It’s a canary in the coalmine for COVID19 effectively. During the pandemic I’ve been hearing it from the manufacturing sector as well: so many different manufacturing companies who wouldn’t ordinarily work together getting together to find solutions and develop new technologies. And that’s really inspiring. I think the reason that it happens is it gives us a sense of agency, that there’s something that we can do to help rather than just sitting back passively. AMT: What are some of the most exciting developments that you’re currently seeing emerging in advanced manufacturing? BF: There’s some really incredible things. The first thing I need to talk about is the National Industry 4.0 Testlab in Composite Additive Manufacturing, our new joint facility with CSIRO. That will be on CSIRO’s Clayton campus, and the building is now almost completed. It will house a world-first process for additive manufacturing with carbon fibre composites. To me, that’s really super-exciting, and it’s at industrial scale. We can make parts that are 1.6 x 1.6m. To do that in partnership with the national science agency in Australia is so important. It gives us access to their depth and their national reach. The facility will not just allow us to rapidly prototype new materials, it will also allow us to push the boundaries of virtual commissioning, of the digitalisation of manufacturing, and of remote access to the facility. We’ll have CSIRO’s Data 61 team to look at the data analytics, the production data. How do we turn that into information? How do we create self-correcting processes? And how can we demonstrate the benefits of digitalisation to the broader manufacturing sector in Australia? One of the centrepieces is a process developed by a company called Fill, which is based in Gurten in Austria. It’s really beautiful: ‘The Sound of Music’ country, and you turn a corner and there’s an enormous factory that employs 700 people. Fill is the world leader in digitalisation: the company started from a family business that made
skis, then they realised a ski was a composite, and then they were the major supplier for the BMW i3 factory in Leipzig, in Germany. Their new technology, which is a world-first multilayer process, enables you to put fibre down really quickly and minimise waste. It reduces the waste from 60% to about 10%. You create a near net shape pre-form. I was in Austria late last year, where one of our Swinburne students had designed a car bonnet; he’d optimised it for pedestrian impact and reinforced areas of it with additional carbon fibre. He sent the code to Austria, and it was printed out while I was there, which was incredible. There’s a lot of other exciting trends. One of them is the monetisation of manufacturing production data. This is an emerging trend in Europe, which uses integrated ledger to securely transfer data between companies. So for example, I might be making a gin. I’ve got a process for making a gin, I have botanicals that I use, I have temperatures that I can control. And you might see in a window shop that I have data for gin manufacturing. So you can make me an offer to share that data in a secure way. And that way I’m not only making money from making gin, I’m making money from sharing my data on making gin. You might be in another location around the world, but we can still securely share that data. That’s a trend that’s coming through Europe. Another trend that I’m seeing is around secure cloud platforms. There’s a program in Europe called GAIA-X, which is really interesting, which is looking at a secure cloud platform for Europeans who do

not necessarily want to be locked in to having all of their historical data accessed. It’s really to avoid the locking effects of some of the major cloud providers who, once your data is with them, they own it for eternity. So there’s gonna be a lot of changes in the way that we transact data. And then enormous changes to the internet of things (IoT). The time is right to really re-explore IoT. It feels like we’re already familiar with it, it feels like we already know it. We’ve all got lightbulbs and heaters that are IOT-connected, but there’s so much more that’s possible. As sensors are becoming cheaper and smaller, there’s so much more we can do with IoT in manufacturing, and we’re really just at the beginning of what we do with that, how we integrate those sensors, what we do with that information. And I think that’s going to be really important for the Australian economy in the future, that we look at that as a platform and invest and utilise it in manufacturing - and learn from the mining sector and what they’ve done in particular. AMT: What can Australian manufacturers do to capitalise on these developments? BF: Well, I think that there’s an enormous appetite to do that right now. We are suddenly really valuing our own manufacturing sector for the first time in a long time. And that’s a wonderful change, that we really value our own ability to make things. It’s an incredibly important cultural shift. Continued next page
And with that will be enabled the development of new products, new processes, new technologies that are still globally connected, we’re still exporting them, but it’s using advanced manufacturing to connect into those global value chains with something that’s really unique. I see a lot more collaboration than has ever happened before, and I see a lot more cross-sectoral learning than we’ve previously seen. All of those things will set us up for success if we stay focused, if we remain focused on developing and commercialising new technology, and if we can continue to build public private partnerships. My first job was at CSIRO; I’ve collaborated with them for my whole life, since I was probably 22. They were a core partner in building the Carbon Nexus hub that became a key part of my former role at Deakin. I really saw there the advantage of having a publicprivate partnership with government-supported research between a university and the national science agency and industry. If we can continue to look at that as a model and work together, we will continue to develop new technologies. That’s what I’m really excited about with what we’re doing with Swinburne at Clayton. You create an innovation ecosystem, with industry, university, you get that talent through those graduates who have unencumbered thinking and you can do really incredible things. The establishment of Carbon Nexus supported the creation of a whole precinct, a whole ecosystem. (Australian manufacturer) Quickstep made the decision to set up their presence there on Deakin’s Geelong campus, the day that Carbon Nexus opened in 2014. And then my former PhD students founded Carbon Revolution, which was supported by the growth of the whole area, and they’ve just employed 570 people. And that’s been so important to the economy of the Geelong region, because that all happened right at the time of the global financial crisis. That’s when we got the funding for Carbon Nexus and right at the time were Ford was shutting down and Alcoa was shutting down. AMT: We often hear about the importance of collaboration between industry and universities or research bodies. What’s your advice to manufacturers about engaging with an organisation like Swinburne? BF: It’s really about building trust, and having constant conversations. Picking up the phone: “What do you think about this? I’ve heard this is happening.” You know, constantly having those mechanisms for knowledge transfer, which create trust networks. I think that’s most important side of it. And it’s based around individuals; you need to have the right people involved. AMT: What do you think are the biggest challenges and opportunities right now for manufacturing in Australia? BF: The challenge is re-establishing supply chains. We have relied on bringing in a lot of materials from overseas. If we’re cut off again, we may not be able to do that. So how do we develop robust supply chains? I thank that’s going to be a big question for the future. The opportunity is to still think globally when we can’t travel. A lot of countries will become inwardly focused and insular. We need to shore up our own capabilities, but at the same time think globally and think where we can export, and to continue to have those conversations digitally where we can’t meet physically. There are a lot of opportunities. We had a fantastic visit from the head of materials and manufacturing at Mercedes at the beginning of this year. They are focused on sustainability; sustainable luxury is their new focus. They’re making leather out of apple skins. They’re doing incredible work around recycled plastics. And there’s an opportunity for Australian technology to be integrated into their supply chains because we’re really creative, we’re focused on sustainability, and we can develop some of the technology they’re really looking for. One more challenge: companies like Mercedes are now not only making their business decisions based on cost. Now they are basing the business decisions on your CO 2 footprint, and they have tools to evaluate what the CO 2 footprint is of your manufacturing process

and your product. That will determine whether you’re integrated into their supply chain. That’s a challenge for the future for Australia: to be aware of that and to be able to demonstrate compliance. AMT: Tell us about your professional background up to your current role. BF: It’s kind of embarrassing. Both of my parents were scientists, so I tried not to be a scientist; I tried very hard, but I think it was in my genes. I guess I grew up in a family where we were building papier-mâché volcanoes and exploding things in the backyard. We were always just making things and testing them and blowing things up. I did a chemistry degree because I didn’t quite get into optometry, which was my first choice, and I’m so glad I didn’t. I got into chemistry and then realised that what I was really interested in was engineering. I don’t think we articulate what engineering is very well. It’s really about working in teams and solving big problems and making a difference to society. I think that would really help us engage with more STEM students, if we were able to articulate some of the really exciting career paths you can have in engineering. I finished my PhD and I was offered a job at Deakin by Peter Hodgson, who had come from industry, from BHP. And he was really inspiring in setting up Deakin to do something different other than the big universities. He was really supportive of new ideas and gave you the space to try things and fail. So I was lucky to be in that really great environment. We grew from a one-man band into a team of 30 people and part of a hundred-million dollar precinct around Carbon Nexus. And then I moved to Swinburne having been at Deakin for 15 years. I just needed something new to do, and I’ve loved the move. Swinburne has that same really open creative environment where if you come up with a new idea, it’s “Let’s explore that and test it”, rather than “Oh, that’s never gonna work. We tried that in 1984 and this happened.” It’s a really wonderful environment and a lot of fun to be part of. AMT: And you’ve been Deputy Vice Chancellor (Research and Enterprise) since April. What does the role entail? BF: The role really entails supporting our research community, understanding where the strategic opportunities are, and leading the research at the university through what is a very challenging time. I’m very fortunate to be working with not only some very clever, innovative academics, but very nice human beings as well. I’m incredibly grateful for that; they’re strategic and smart and they’re fun to work with. Through everything that’s happened, that’s really kept me inspired every day. If I can meet with a researcher or a research team every day, it just puts a spring in my step to hear about the incredible things they’re working on – everything from health technologies, to social innovation, to smart cities. It’s a really interesting role to think about research much more broadly than my own discipline. AMT: What’s the most satisfying part of the job? BF: Absolutely the people. The incredible leadership, but also the emerging talent, and looking at how you can nurture that and help it grow. www.swinburne.edu.au