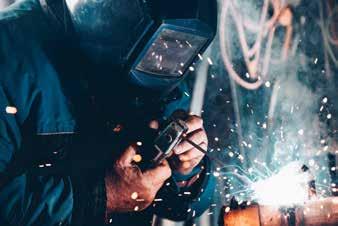
8 minute read
Government urged to modernise outdated welder training
from AMT OCT/NOV 2020
by AMTIL
Weld Australia is calling on the Federal Government to undertake an in-depth review of the TAFE welding curriculum, describing the latest Manufacturing and Engineering (MEM 2.0) training package as inadequate for the needs of industry while imposing significant burdens on apprentices, employers and TAFEs. Weld Australia’s Chief Executive Officer Geoff Crittenden explains.
Welder training in Australia is outdated. The TAFE curriculum has remained relatively unchanged since 1998. TAFE has been required to teach courses such as fabrication, in which the welding modules are of varying degrees of complexity and are usually optional. This has not produced welders that are skilled or qualified to the levels needed by industry, especially within the defence sector. Young welding apprentices enter the workforce without the requisite skills or knowledge. Generally speaking, TAFE graduates cannot read a welding procedure, set up a welding machine, or weld according to Australian standards. Released in June 2019, the latest version of the Manufacturing and Engineering training package (MEM 2.0) differs very little from the previous versions (released in 1998 and 2005). In fact, many of the units and much of the content remains identical to the 1998 version. Not surprisingly then, MEM 2.0 bears no relation to what is actually required by industry. It ignores the huge technological advancements and changes that will continue to occur in Australia’s engineering and manufacturing industries. The course still devotes time and energy to oxy-acetylene welding, which industry has not used for about 20 years. The future of Australian industry in a post-COVID-19 world cannot rely on regurgitating a curriculum that is 20 years old. The MEM 2.0 training package The only real differences in the MEM 2.0 training package are a significant increase in prerequisites, and the addition of more than 2,000 hours of mandated workplace practice. Both of these will impose significant restrictions and burdens on students, industry and TAFE. • Significant increase in prerequisites – The significant increase in prerequisites in MEM 2.0 will eradicate any modicum of flexibility for students, industry and TAFE. Course duration will be extended, increasing both the delivery costs for TAFE and the course costs for students. With extended courses, completion rates are likely to drop, with students expected to complete a greater number of theory-based, non-practical units before having the opportunity to learn the hands-on practical skills in which they are most interested. For TAFEs, delivering courses in a meaningful way will be hampered by the additional prerequisites, and there will be little opportunity to deliver short, sharp micro-credentials. • Prescribed workplace practice – MEM 2.0 mandates a workplace practice component of more than 2,000 hours.
This will place considerable burden on employers who have to ensure that students are able to meet this requirement.
Over 90% of manufacturing firms in Australia are classified as
Small to Medium Enterprises (SMEs), which are comprised of fewer than 19 employees. These businesses are unlikely to have the capacity to sufficiently monitor the workplace practice requirements and may deter businesses from employing apprentices. This situation will be difficult enough for apprentices but is likely to be even more challenging for transitional workers hoping to train up and enter manufacturing and engineering. In essence, welders will be required to be employed in industry before they can successfully gain their formal qualifications.
The skills of the future The implementation of MEM 2.0 by Australian TAFEs is due for completion by the end of 2020. Before this happens, industry must voice its concerns. The welding curriculum must concentrate on the skills that will be essential to the future of industry. These skills must be focused on advancements such as automation, robotics, artificial intelligence, big data, and advanced manufacturing processes. It is these skills that will see Australian industry continue its push into high-quality, complex, small-batch manufacturing. The Federal Government must revise MEM so that the curriculum teaches skills such as programming, operating and maintaining robots, co-bots and welding machines integrated with artificial intelligence. It must include units that teach students how to analyse and leverage big data. It must delve into concepts such as Industry 4.0 and additive manufacturing. The TAFE welding curriculum must be revised so that it meets industry demand both now and into the future. It cannot be bogged down by excessive prerequisites, mandated workplace practice that employers simply can’t deliver, and training in skills that just aren’t relevant to industry anymore. While many of the state governments have backed this vision and invested in Advanced Welder Training Centres around the country, TAFEs still need real support from the Federal Government. TAFEs do not need more free apprenticeship programs. They need funding from the Federal Government so that they can invest in the necessary cutting-edge technology and equipment required to teach a forward-looking curriculum focused on the skills of the future. Our young people need to acquire complex, high-order technical knowledge and skills. They need robust, deep and transferrable qualifications that provide a strong base for life-long learning and skill development. They need a TAFE system that is properly funded with curricula focused on the future.
If you support Weld Australia’s position that MEM 2.0 training package is inadequate for the needs of industry, apprentices and TAFEs, Weld Australia encourages you to write to the Hon Steve Irons MP, Assistant Minister for Vocational Education, Training & Apprenticeships, via am.irons@employment.gov.au or PO Box 1060, East Victoria Park, Western Australia, 6981. www.weldaustralia.com.au
TruFlow bolsters capability with Deratech press brake
TruFlow Spray Booths Australia designs and manufactures industrial and commercial spray booth products. TruFlow’s Director Anton Pirie discussed their recent purchase of a Deratech press brake from CMTS Sheetmetal Machines.
From humble beginnings with only two staff members almost 20 years ago, TruFlow Spray Booths Australia has grown to an Australia-wide operation employing 40-plus workers. The company manufactures unique custom-made spray booths that have been installed in a variety of industries including aviation, automotive repair, commercial trucking, industrial painting and cabinet making. AMT: Why did you need the new machine? Anton Pirie: We had an old second-hand 3.2m press brake that we had purchased through CMTS about 10 years ago, and although it was still running well, it wasn’t keeping up with our production. Neither was the additional 5m press brake machine, which is about 40 years old now, so we understood that we needed to update our press brake technology. AMT: How important are the press brakes to your business? AP: Very important! The press brake machines are a major piece of our production; they run all day every day. They are a major part of the manufacture of the roof and wall packs for our spray booths and burner boxes. Both machines are 95% of our business. This is why it is so important to get the right machine from the right company. If something goes wrong, it will have a drastic effect on our production. AMT: How is the Deratech press brake machine? AP: It’s brilliant; it’s so simple to work with. We purchased a Deratech Technica 250-ton, 6,100mm machine, with two CNC front sheet supports. We had just put on a new operator, and it normally takes a while for a new operator to get up to speed. The Deratech press brake machine is so easy to use it is like the operator has been doing it for years. The software is so simple that if you can draw the folds with your finger and insert the sizes required, then you are good to go. It’s just that easy to deal with. This is so important to us because the new operator is now running the machine like a pro and that helps production levels. AMT: Why did you choose CMTS? AP: We had about six different companies who gave us quotes. When Michael [Schneider, Director of Sales & Service at CMTS] came in, there was a difference about him. He was honest and to the point, he told me exactly how it is – that enabled me to trust him. He even talked about competitor products in high regard, and I liked that. I liked the way he approached things. He didn’t talk down his competitors, and just told me the facts about the Deratech machine and everything I needed to know. AMT: How was your experience with CMTS? AP: It was great. Michael kept us updated all the way through the process. When the machine was installed, they were fantastic - so helpful. He came in and gave my team all the training we needed. He even came back to deliver extra training when we asked. He knew that this installation was important to us and treated it with the respect it needed. I’ve had machines installed before and sometimes it can take months to get it operational, but with CMTS it only took a short time and we were up and running. They are such good people to deal with – if more people were like them the world would be a better place.
www.truflowspraybooths.com.au www.cmts.net.au
MTI PE200 SWING DOORS The most robust solution for food industry, retail and logistics
The new PE200 HDPE double acting impact traffic door, exclusively available from MTI See-Thru, offers the perfect solution for insulation, functionality and durability.
Benefits of the MTI PE200 Swing Door; • Made of solid polyethylene – non breakable • Hygienic (EU/FDA approved) • Maintenance-free • Made to measure • Short production time • Easy installation • Long service life • PVC finger protection • 10 year guarantee on door leaves • Stainless steel hinges
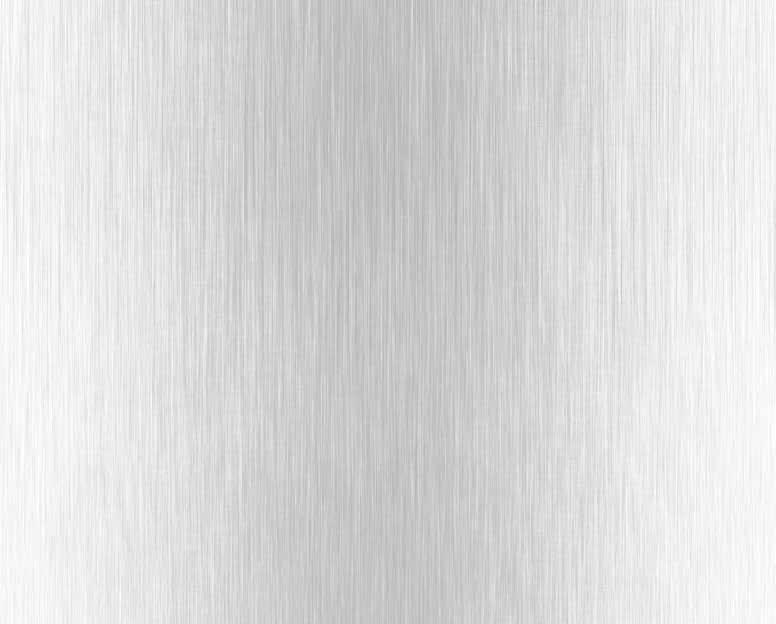
Trusted by food and retail companies worldwide; • Kraft Foods, Bahrain • Nestlé, Germany • Aldi, Ireland • Lidl , Germany, England • Edeka, Germany • Kaufland, Germany • IKEA, Turkey Contact M.T.I. Qualos today to discuss your industrial door needs.