
8 minute read
One size does not fit all
from AMT OCT/NOV 2020
by AMTIL
One size does not fit all: Environmental and ergonomic considerations in choosing the right robot When making a robot selection, criteria such as payload, dimensions, weight or force are often given priority, but environmental and ergonomic considerations are equally as important.
The modern industrial robot has come a long way since 1961 when Unimate #001, the first industrial robot arm, appeared on the General Motors assembly line in Trenton, New Jersey. When entreprenuer Joseph Engelberger, the father of modern robotics, appeared on the Tonight Show with Johnny Carson in 1966 to demonstrate the Unimate, many began to envision a future where it might be possible for artificial intelligence to completely take over industrial production processes. Six decades later, we have not seen the Hollywood narrative of the 1956 sci-fi movie Forbidden Planet play out, where robots perform every task requested of them by their masters. And we are still some time away from full automation with a science fiction icon like ‘Robby the Robot’ taking control of manufacturing systems. We have, however, seen industrial robotics improve rapidly and adapt into its most commonly recognisable form: the SCARA (Selective Compliance Assembly Robot Arm, or Selective Compliance Articulated Robot Arm) format. For business owners and engineers, selecting the right SCARA robot for the task is critical for maximising return on investment. There are a myriad different robot manufactures globally, with an exhaustive number of robot models to choose from. But what makes a robot the best fit for your business? Most engineers would primarily be concerned with objective and quantitative criteria (payload, dimensions, weight, force) when making a robot selection, however the environmental and ergonomic considerations are equally as important when choosing the right robot for the application. One of the most obvious environmental consideration factors in the ability to isolate human-robot interactions safely, with advances in collaborative robot development in response to a growing requirement for flexible alternatives to completely caging a robot. Robot manufacturers have long identified the need for robots to endure harsh operational environments, freeing up workers from potentially hazardous conditions. Painting robots are a good example of this, exemplifying just one sector of a very wide area of specialist robot designs based on environmental requirements. Just as paint series robots are able to operate in the hazardous environment of a spray booth due to their specific design, there are other specially designed robots for working in the fabrication, food and semiconductor industries and other harsh environments. Robots designed for industrial food applications must be able to withstand regular cleaning with sanitising chemicals, and robot construction materials must conform to regulatory standards to avoid the introduction of toxins into the food processing stream. This is a good example of how the environment dictates the robot permissible for selection. Ergonomic design features would include the elimination of deep crevasses in the robot body to ensure effective cleaning and the removal of sharp edges to prevent snagging fibres during the cleaning process. Another example where environmental and ergonomic considerations have driven the design of a robot is modern MIG or GMAW (Gas Metal Arc Welding) robots. These are is the result of many years of research & development in the laboratories of robot manufacturers together with operating feedback from real life scenarios.
Whilst essentially identical up to the Axis Joint #3, there are some significant differences between a MIG welding robot and a standard manual handling robot (apart from the obvious end-of-arm tooling). Consider the M20iA and the M120iA FANUC robots: this comparison highlights how two similar robots built on the platform can be customised based on their end use. Effectively what we see between these two robots is an ergonomic variation in the wrist assembly configuration (Axes #4, #5 and #6) to allow a rear entry to the end of arm tooling, specifically for the MIG torch. Both robots offer the same payload capacity and degrees of accuracy; however the MIG customisation for the Arc Mate M120iA model includes specific internal cabling for the wire feeder and welder power systems. Additionally the Arc Mate M120iA is fitted standard with severe dust and liquid protection cabling for its operational environment, whereas for the M20iA these are optional additions if the manual handling application is required to operate in an environment that requires such protection. Remember, taking a one-size-fits-all approach generally ends up costing more in the long run. Beware of buying more robot than you need or buying into a lack of reliability. It is important to formulate a checklist when selecting a robot that includes not just the payload, reach and size requirements, but the environmental conditions and ergonomic criteria to select the robot for the best fit for your application. Intelligent design variations allow for robot selection to be specifically tailored to your individual needs, providing a degree of certainty about selecting the right robot for your business.
www.automatedsolutions.com.au
Agile Robotic Systems – Flexible, affordable productivity
Having supplied Australian manufacturers with innovative advanced manufacturing technologies since 1946, John Hart’s depth of experience and technical knowledge has formed the foundation for the development of its Agile Robotic Systems range of robotic machine tending solutions.
Joining a small group of Australian companies that build and export manufacturing technology, John Hart designs and manufactures the systems in its Melbourne facility for local and international markets. With a facility in Cincinnati, Ohio, Agile Robotic Systems offers on-site demonstrations, technical support and sales for the entire North American region. Three levels of machine tending products provide the basis of this innovative success story. The Agile Flex range is an out-of-thebox machine tending solution that is solid in construction, rapid to deploy, easy to use and very affordable. The Agile Modular range offers a flexible machine tending solution created by bringing together pre-engineered modular system components to meet project requirements. Finally the Agile Engineered range offers a fully bespoke solution designed specifically to meet the unique requirements of each project. Known for their advanced design, simplicity of use, build quality and reliability, Agile Robotic Systems come in a range of sizes and configurations to meet the individual needs of manufacturers. Unique to Agile Robotic Systems is the Agile Flex Cell Controller software. Developed in-house to offer unparalleled ease of use, this revolutionary control system allows users to efficiently change to new parts in a matter of minutes. At the heart of this system is a revolutionary wizard-based process, which prompts users in a question and answer format to input simple process information for the next part. Ideally suited to small and large batch sizes alike, Agile Robotic Systems allow customers with no robotic knowledge to be fully self-sufficient in setting up any number of new parts over a normal week. System flexibility together with simple and fast part changeovers helps customers to remain flexible, productive, and profitable in a tough global market. Having successfully installed many systems into a large variety of industries locally and in the USA, John Hart is a local success story highlighting what can be achieved through the hard work and ingenuity of the very capable people in Australia’s manufacturing industry. Agile Robotic Systems set a new benchmark in rapidly deployable, compact, and affordable machine tending systems.
www.johnhart.com.au www.agilerobotics.com
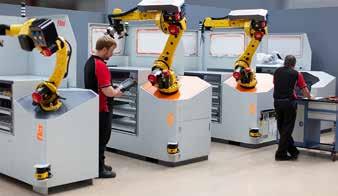
For progressive engineers, fabricators and metal workers to manage your core business, your labour
Touch Screens on the Workshop Floor – Tracking: Jobs, Tasks and Workshop Staff in Real Time
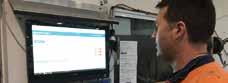
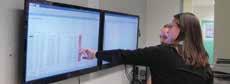
50 inch TV Monitors on Office Walls and Workshop Floor Walls – Report: Jobs, Tasks, Staff, Times, Job Status, ... in Real Time

Scheduling is Updated Automatically in Real Time at Job Change
Essential Tool for Production Management to Drive Weekly Production • Software App developed for engineers producing custom one off products or projects, 6 to 150+ workshop staff • Empower Software is simply an App. Cloud & Web based • Empower can interface to any accounting or ERP software • Pricing Low Cost Subscription eg 10 workshop staff is $108 per week • If you use manual time sheets, to record workshop staff times on their jobs 10 workshop staff for example will cost you $775 per week, in lost chargeable staff time to fill in daily and admin cost daily to rekey to produce. If you replace your manual time sheet system with Empower then you will save $667 per week saving you $32,683 per year. • Supplying Australian engineers for 13 years • Available to you on request: info pack and free trial software • Engineering Client Short Videos on youtube.com. In Youtube search: Empower MARs Transport, Empower Peppertree ... • 90% of engineers using tablets on the workshop floor and the
Empower Software App achieve a 20% to 40%+ reduction in time on jobs – therefore a 20% to 40%+ reduction in labour cost on jobs. • An Engineer with 10 workshop staff is projected to increase production by 80 hours per week, therefore increase revenue by $6,000 per week and (80 hours by $75 per hour overhead cost), therefore increase revenue by $312,000 per year. This $312,000 per year is largely additional profit because overhead costs have been incured in existing production. Your 10 year investment $3.12m additional revenue, largely additional profit.

Sean O’Sullivan B Com (Hons) Otago University
Founding Director, Empower Software
sean@manufacturingandengineering.co.nz +64 27 2284211