
10 minute read
Evolve Group: The value of Oz design/manufacturing
from AMT OCT/NOV 2020
by AMTIL
Evolve Group – Proving the value of Australian design and manufacturing Queensland-based Evolve Group is proving the extraordinary value to the Australian economy of innovative advanced design and local manufacturing, with exports from this multiple-award winning company destined for more than 130 countries.
Founded in 1978, Evolve Group’s status as a company at the very forefront of competitive Australian manufacturing has never been more apparent than in its response to the ongoing COVID-19 crisis. In a vivid demonstration of the benefits of manufacturing in Australia, Evolve Group was able to provide an advanced design and a commitment to manufacture 100,000 P2/N95 respirators and medical face masks per day, with the construction of a clean room and production commencing within just two weeks. Working closely with local Queensland hospital surgical teams, Evolve Group’s design of a new face shield is now being heralded as the most comfortable face shield in the healthcare industry. Studying how a face shield is used by medical professionals has delivered the outcome of a shield featuring a comfortable gel pad relieving pressure on the forehead of the wearer, a removable vent cap for ventilation, an easily replaced shield with anti-fog and scratch properties, and an ergonomic design for all-day comfort. With the further benefit of one size fitting all, this advanced design medical face shield is already attracting interest from the USA, South Africa and Europe. “So many companies source product from overseas in the belief that it is cheaper,” says Mayer Jung, Evolve Group’s Design & Development Manager. “Yet as a company, we have been successfully reshoring manufacturing to Australia and expanding our exports with a competitive advantage and shorter lead times for our clients.”
Evolve Group recently acquired an Okuma MB56VA S15 CNC vertical machining centre.
To meet the critical time frame and the precision tooling required, Evolve Group invested in the latest Okuma MB-56VA S15 CNC vertical machining centre, with an OSP-P300MA control. Featuring an extremely rigid double-column structure and a large bed size incorporating a highspeed 32 position automatic tool changer, the machining centre is providing greatly enhanced additional capacity, consistent precision output that does not require finishing, plus the ability for long multiple unaided production runs. With the COVID-19 lockdown in place, the installation and commissioning were successfully and seamlessly completed remotely, with all training undertaken by Okuma’s National Technology Manager Karl Cory, via online meetings applications such as Zoom and TeamViewer. Further training will be undertaken by Okuma as required by Evolve Group engineers once the current pandemic restrictions are eased. “In looking at CNC machining centres, Okuma was our first choice based on our experience,” explains Jung. “It is considered to be top of the range and the machine we needed was immediately available. “For the operators of the Okuma machining centre there is the ability to produce more tooling in-house. The operating system is good to work with, there is a dramatic increase in utilisation of the machine and the quality of the finished product is exceptional.” “Our company has had a long-term relationship with Okuma and still operates a 20-plus year machine that has served the company well. And back-up service and technical advice from Okuma Australia is amazingly supportive.” Wide-ranging capabilities Headquartered in Crestmead, in Brisbane’s southern suburbs, Evolve Group has been innovating and expanding its wide-ranging capabilities for many years. Today the company employs a highly skilled team of more than 100 staff, and services a diverse range of markets including medical; automotive; electrical; heating, ventilation, air conditioning and refrigeration; building and DIY; plumbing and gas fitting; pool and spa; fishing; industrial; and general engineering.
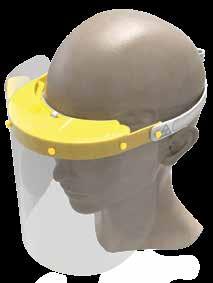
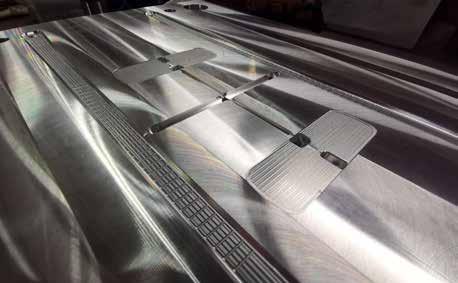
Evolve Group’s extend design and manufacturing capabilities encompass injection moulding, over-moulding, material sourcing, tooling and fabrication, robotics and automation, supply chain and distribution. The company utilises the latest rapid tool and conformal tool verification technology, and every injection moulding machine on the floor is equipped with a servo-driven robot with a custom-made end of arm to retrieve specific parts in the most efficient way. Design, development and sustainable marketing is at the heart of this innovative ISO 9001 accredited company, winning it awards such as the coveted 2016 Good Design Award of the Year, and also the prestigious Best Product Innovation Award for the design, manufacture and optimisation of the Flow Hive, an inventive beehive system. The company has been named in the top 50 most innovative companies in the Australian Financial Review Awards, plus multiple Australian Good Design Awards. “Our team not only designs new products but works closely with customers to refine and/or improve a design to maximise efficiency, reduce the cost of production

and improve return on investment for your clients,” says Jung. “Our ability is getting it right the first time, at the lowest possible cost, in the shortest time-frame with minimal risk, but we also look and advise customers on the marketing aspects for long-term sustainability of a product.” A recent demonstration of the advantages of reshoring manufacturing production back into Australia has been Evolve Group’s involvement in the innovative Seabin Project. Created by two Sunshine Coast residents and a Byron Bay local, the Seabin collects tens of thousands of discarded plastic bags, disposable
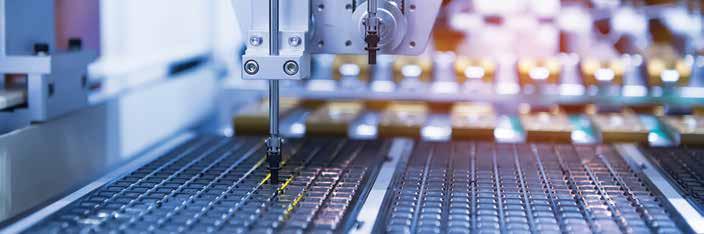
cups and plastic bottles from waterways, currently operating across 52 countries. Seabin production has recently been relocated from France to Evolve Group’s facility in Crestmead – a decision taken both on a sound economic basis as well as the advantage of supporting local jobs. The company is already looking at acquiring additional sites to provide for further expansion of its design, manufacturing and logistics facilities. “At Okuma we understand the importance of competitive manufacturing to Australia and the need to adapt service levels to meet customers’ essential service requirements in the current climate,” said Dean McCarroll, Managing Director for Okuma Australia. “It is a pleasure to work with such an innovative company as the Evolve Group in commissioning latest Okuma CNC machining technology, and an example of what can be achieved to ensure Australian manufacturers remain highly competitive in the international market.”
www.okumaaustralia.com.au www.evolvegrp.com
QSP Engineering gears up for the future With a vision for future demand, QSP Engineering recently moved premises from Loganholme to Bethania in the outer suburbs of Brisbane, and introduced new technology into its metal spraying business.
With the aim of retaining QSP’s position as a key provider of metal spraying repairs for worn parts, Managing Director Neville Brokenshire looked to install the latest innovations in metal spraying technology, to ensure high-quality output and a more efficient, cost-effective process to integrate into its workshop services. Already utilising a fibre-coupled high-power diode laser by Laserline supplied by Raymax Applications for laser cladding with metal powder, Brokenshire sought advice from Dr Cédric Chaminade from Raymax in regard to improving output. A new coaxial nozzle was deemed the solution. High processing speeds with specifically designed coaxial nozzles used with Laserline fibre-coupled diode lasers provide distinct advantages, including low exposure time, strong metallurgical bonds between the cladding layers and substrate, low warpage, and short, highly energy-efficient cladding times. By introducing a new laser cladding nozzle, QSP has effectively extended the current available advantages to its customer base. A coaxial nozzle combines inert gas flows and metal powder with exceptional throughput capability. Additionally, protection glass monitoring extends the lifetime of consumables, while at the same time ensuring a reliable process. The new Coax11, developed by the Fraunhofer Institute for Material and Beam Technology, represents a flexible processing tool for cladding applications and guarantees CNC machines to its already-impressive machine shop. Established in 1982, GMG is a metal manufacturing and engineering company offering customers exceptional quality and service utilising the latest advances in technology. Located in Maryborough with a second facility in Gladstone, GMG employs 60 highly skilled staff servicing industries including mining, defence, construction, transport, rail, medical, marine/shipping, and oil & gas. GMG offers a complete turnkey solution using world-class equipment and Lean manufacturing principles. The new Mazak machines are a VTC-530/20 vertical travelling column machining centre, a VCN 530C vertical machining centre, and a HCN-5000 twin-pallet horizontal machining centre. GMG Managing Director Richard Aylward cites increasing client demand as the driver for the investments, together with productivity increases brought by newer technology. “The latest Mazatrol Smooth conversational controllers have delivered a significant reduction in programming and set up time for us,” he explains. “And together with the latest technology Mazak offers in their machines, this has given us significantly reduced in-process times.” The Mazak VTC-530/20 vertical machining centre features a fixed 2,300mm x 530mm table design and travelling column, providing exceptional versatility for mounting long workpieces as well as multiple parts along the table length. The VCN-530C vertical machining centre has a 1,300mm x 550mm table and performs heavy-duty machining of steel and high-speed machining of aluminium. The HCN-5000 horizontal machining centre, with 500mm x 500mm pallets and a BT50 spindle, is capable of heavy machining and highspeed operation. “We know Mazak machines very well so we didn’t need to look any further than John Hart for advice in the purchasing a stable and controllable process as well as the highest precision in material deposition. Highpower diode lasers from Laserline in Germany can provide cladding solutions with up to 20kW of laser power, and use wide track processing optics providing the highest powder deposition rates available. Industries where components are constantly exposed to high stress become fatigued and worn, requiring replacement or repair. Today, highthroughput laser cladding, or metal deposition, is demonstrating not just the effectiveness of repair but the metallurgical connection between the additional layer and the basis material can actually extend the life of the original part. Repairs to large-sized drilling tools used in oil extraction, boring or mining, marine engine parts, or earthmoving equipment can all be effectively repaired using laser cladding. In Australia, there is a growing market for laser coating of hydraulic cylinders from technical mining facilities such as coal extraction. Its new laser cladding equipment is a timely acquisition for QSP, as the economic downturn and limitations imposed on importing new component parts are changing industry behaviour and fuelling demand for local repairs. With trained and experienced staff and over 25 years in the industry, QSP stands to gain an edge over its competitors, geared up and ready to meet this increased local
Global Manufacturing Group continues to invest in Mazak.
Global Manufacturing Group (GMG) has recently made significant investments in productivity, adding three new Mazak
demand. www.qspengineering.com.au www.raymax.com.au process,” Aylward adds. “Just a good deal and short lead time was what we needed, and John Hart delivered on all fronts. The training with each new purchase was a big benefit. Most of our operators are already well across Mazatrol, so our young apprentices were able to get some really high-level one-on-one training, which advanced them significantly.” The Mazak machines continue to perform under high workloads, so GMG benefits from John Hart’s service and support. “The fact John Hart is committed to providing support for our much older Mazak machines means we would be reluctant to look elsewhere,” says Aylward. “I think the back-up service is 80% of your decision. John Hart responds very rapidly to our needs, and this reliability is a big part of why we like to continue with Mazak machines.” www.johnhart.com.au www.gmqld.com.au
AMTIL is an organisation that is ‘For the Manufacturer’ and that is why Hardman Bros. is a member. Manufacturing in Australia is facing some challenges and having AMTIL as our voice I believe is invaluable. The organisation of the Austech exhibition coupled with the Manufacturers Pavilion is a brilliant showcase and a great opportunity to meet with peers from the industry. AMTIL’s association with large suppliers has brought discounts to my company that pay for our membership tenfold each year, savings we need to stay competitive.
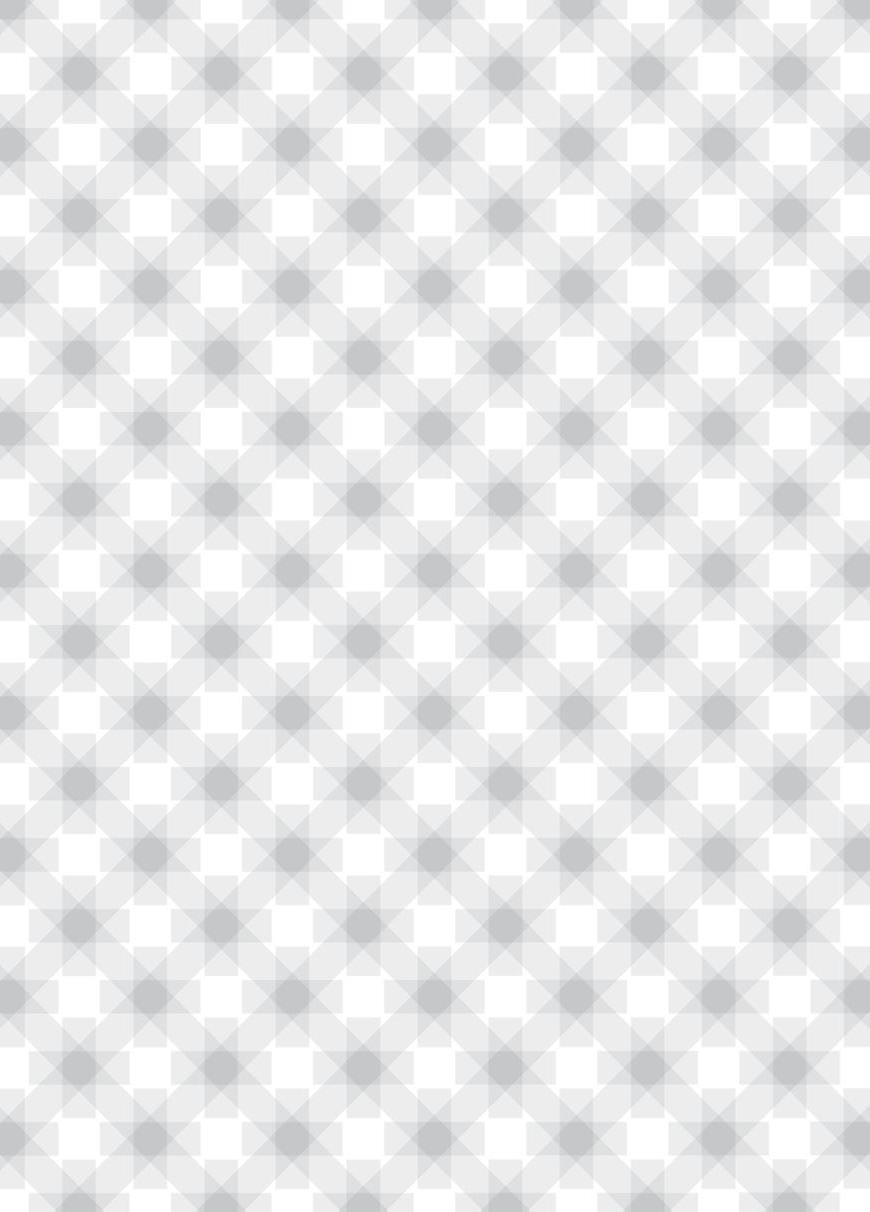
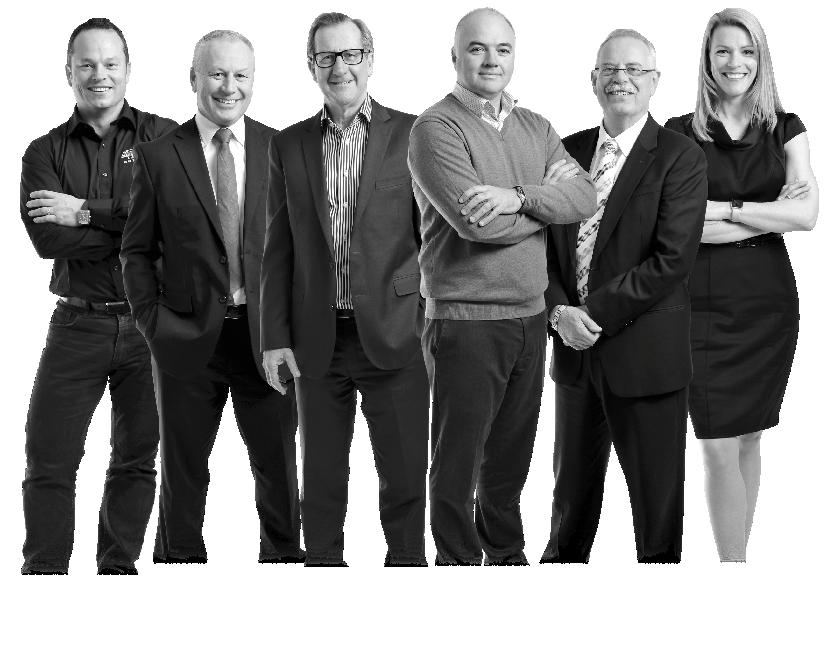
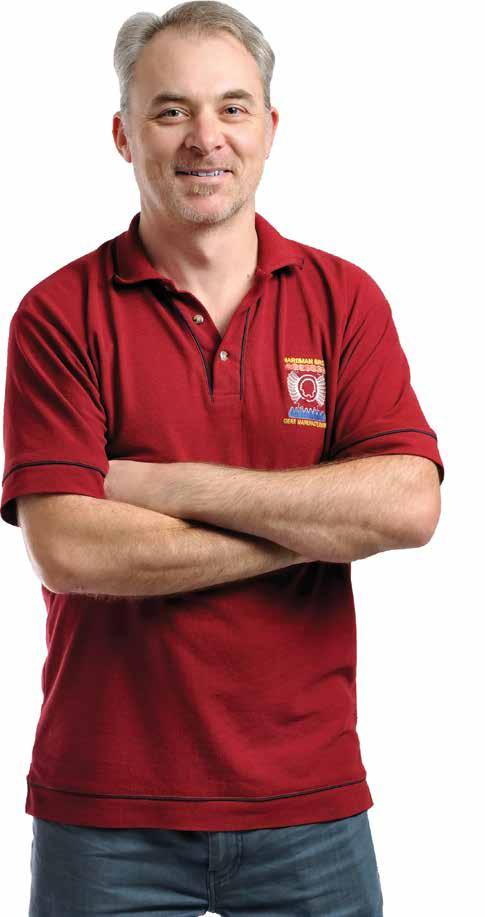
Mark Hardman, Hardman Brothers
Real Business Real People Real Members
Since 1999, AMTIL has been connecting business, informing of opportunities and growing the manufacturing community.