
10 minute read
Sentient Bionics gets a helping hand from the AM Hub
from AMT OCT/NOV 2020
by AMTIL
When Sentient Bionics required rapid production of prototype parts for its new robotic hand project, it turned to AMTIL’s Additive Manufacturing Hub (AM Hub) for assistance.
Based in Port Melbourne, Sentient Bionics has been developing anthropomorphic robotic grippers for more than half a decade. During that time the company has worked with prosthetic users, hospitals and industry partners to develop a range of grippers suitable to satisfy everyday human and robotic needs. Familiarity, versatility and affordability are at the core of Sentient Bionics’s ethos, and it has developed hands that allow people and robots to interact in a natural and effective way. Additive manufacturing has already been a large part of Sentient’s business, giving it the ability to quickly prototype both adult and child-sized prosthetic mechanical hands. Additive manufacturing’s fast development time has allowed Sentient Bionics to start clinical trials and quickly respond to feedback gained through them with helpful and progressive design changes. While Sentient Bionics specialises in the design and assembly of technology and devices, it has outsourced the manufacturing of components. Although it has some basic desktop fused deposition modelling (FDM) printers in-house, which it uses for rapid prototyping operations, the company gets all the parts that it uses for testing and consumer-level products made professionally by additive manufacturing (AM) service providers. The challenge Sentient Bionics accessed the Build It Better (BiB) voucher programme via the Additive Manufacturing Hub (AM Hub) to assist it in initiating a new robotic hand project, as well enhancing the continuation of its prosthetic hand product line. Sentient Bionic’s dynamic design process required
several prototype parts to be manufactured quickly so they could be tested and altered according to results, and additive manufacturing was chosen as the primary method of manufacture. The solution Sentient Bionics received manufacturing services from two Victorian companies – GoProto (ANZ) Pty Ltd and Objective 3D Pty Ltd – within the scope of its BiB voucher, which covered 50% of the service costs. AM Hub member GoProto was engaged for a range of additive manufacturing services including: • Manufacturing structural and functional parts designed by Sentient Bionics for the robotic and prosthetic hands, including the palm (front and back), internal mechanism and phalanges, using GoProto’s HP Multi-jet Fusion
Printing capabilities. • Manufacturing various other parts designed by Sentient Bionics required for internally used tools and rigs, as well as parts for several smaller side projects of Sentient Bionics as part of their professional design contract work. The services received from GoProto reflected Sentient Bionics’s sustainable mindset, through the use of HP MJF PA11 and PA12. Both PA11 and PA12 are highreusability materials that minimise waste, and PA11 is a renewable raw material produced from vegetable castor oil, resulting in a reduced environmental impact. Objective 3D, also an AM Hub member, was engaged for services including the manufacture of structural and functional parts of the prosthetic and robotic hands, which require alternative manufacturing methods not supplied by GoProto such as metal 3D printing and Polyjet 3D printing.
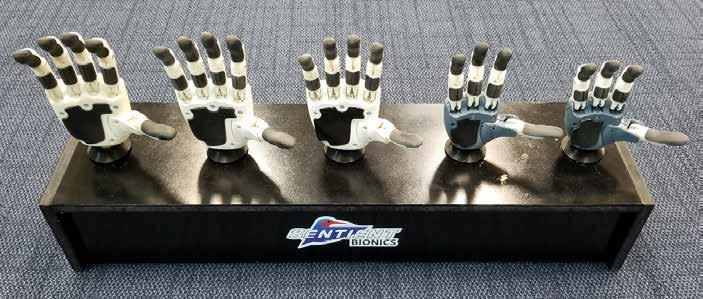
Sentient Bionics’s prosthetic hand product line
With the help of the AM Hub, Sentient Bionics went from a simple, harness-powered prosthetic product with no motor actuation (left), to a versatile robot gripper capable of integration with existing robotic systems (right).
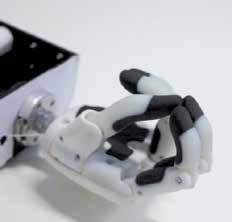
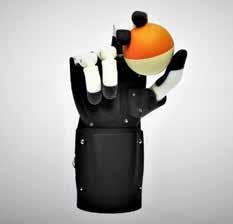
The BiB voucher programme would be crucial in allowing Sentient Bionics the capacity to expand its product range, grow its intellectual property (IP), and delve into new industries. The outcome With the help of the BiB voucher programme, Sentient Bionics went from a simple, harness-powered prosthetic product with no motor actuation, to a versatile robot gripper capable of integration with existing robotic systems. Thanks to the financial assistance of the BiB voucher programme and the guidance and expertise of the AM Hub, Sentient Bionics’s research project was able to cut down manufacturing costs significantly. It made it feasible to undertake more development work across one year than Sentient Bionics had previously achieved ever since forming as a company. More engineers were hired, and the company relaunched its website with new content and new products. In addition the team attended more conferences, broke into new industries, and developed promising leads for future collaboration and sales pipelines as a result of networking within the AM Hub community. Sentient Bionics now sees additive manufacturing playing a crucial role in its future – as its development continues (as it will for a number of years), so do its requirements for a manufacturing method that allows for iterative design changes and high-quality parts. The current designs for its new robotic product rely primarily on additive manufacturing, and the team at Sentient Bionics do not expect that to change anytime soon. With the help of the AM Hub, Sentient Bionics was able to expand into new industries and markets, and within these new markets demonstrate the benefits of additive manufacturing.
The AM Hub is an initiative delivered by AMTIL in partnership with the Victorian State Government to provide an industry-driven collaborative network of technology users, suppliers and supporters that will promote the adoption of additive manfacturing technology. For more information, please contact John Croft, AM Hub Manager, on 03 9800 3666 or email amhub@amtil.com.au. www.amhub.net.au www.goproto.com.au www.objective3d.com.au www.sentientbionics.com
Is your business ready for the future of manufacturing?

More than 40 years of cutting edge technology in sheet metal machinery along with the laser and electronics industries has led Prima Industrie to Prima Additive - A division which is dedicated to metal additive manufacturing systems that guarantee a close partnership with customers, competitiveness, and efficiency.
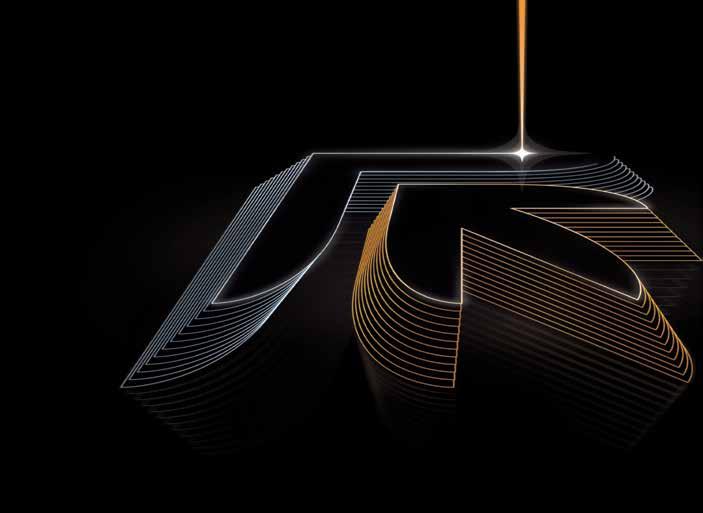
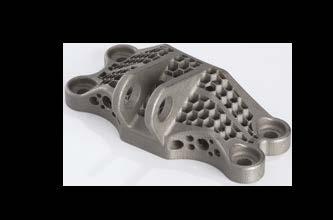
Thanks to our Powder Bed Fusion and Laser Metal Deposition systems, now you can build, repair and prototype - adding value and shaping the new vision of your business.
So, add something new and choose Prima Additive from IMTS Machinery.
IMTS Machinery E | sales@imts.com.au W | imts.com.au P | +61 3 9314 9888
3D printing during COVID-19 – A blueprint for future manufacturing While the COVID-19 pandemic has disrupted many industries and their supply chains, it has been incredible to see how the healthcare sector has responded – helped in many ways by the clever use of 3D printing. By Michael Boyle, Managing Director, HP Australia & New Zealand.
The sudden shortage of essential medical equipment brought on by the pandemic, including respiratory support and personal protective equipment (PPE), has offered a glimpse at how supply chain disruptions can be mitigated with 3D printing, as well as new business opportunities 3D printing can provide when adopted at a large scale. One advantage of 3D printing is extreme flexibility and the ability to rapidly redeploy equipment from one task to another – in other words, to retool. Using a 3D printer, you can be creating building materials one moment and medical prosthetics the next by loading a digital design of the new part into the printer. This agility makes 3D printing useful for prototyping and for making lowrun parts that can be used to repair outdated equipment or create custom products to solve unique challenges. Flexibility has allowed industries to repurpose their production and R&D capabilities towards manufacturing mass quantities of hand sanitizer, producing tens of thousands of masks and gowns, and retooling factories to assemble face shields. In New Zealand, notfor-profit group ShieldsUp has worked with HP New Zealand, Emirates Team New Zealand and Rodin Cars New Zealand, along with hundreds of 3D printing enthusiasts and volunteers across the country, to design and deliver almost 18,000 face shields in under two months. Triple Eight Race Engineering managed to successfully transfer its 3D printing capabilities from the racetrack to the ICU ward. When approached by the Queensland State Government, the team redirected their HP 3D printers that were typically reserved for producing car parts, towards designing and manufacturing critical ventilator components. At HP, we have been mobilising our 3D Printing team and global Digital Manufacturing Partner Network to design, validate and produce essential parts for medical responders and hospitals. More The new machines build on Amaero’s existing product line-up, including the SP500 and SP100 metal 3D printers, and decanter, conveyor, autosieve and depowdering modules. Their launch means Amaero will have one of the safest, most cost/capital-efficient and diverse ranges of metal 3D printers on the market. The new SP260 machine has a build chamber volume of 250mm x 250mm x 400mm. Rapid changeover capability makes it ideal for producing components for the aviation, defence and biomedical industries. The SP260 is simple to use, easy to maintain, ideal for research and small scale manufacturing, and with the safe powder handling ancillary equipment is one of the safest on the market. Similarly suited to manufacturing for the aviation, defence and tooling industries, the SP400 machine has a larger build volume of 400mm x 400mm x 400mm, and with its advanced technology, is safer and more productive than alternative machines of a similar size. Both machines feature a tethered build chamber for rapid job changeover and a bi-directional re-coater for faster production than 158,000 3D-printed parts have been delivered to frontline workers in Asia Pacific, with over 2.3 million parts printed globally. Beyond boosting the supply of PPE for healthcare workers during COVID-19, 3D printing is allowing companies to transform their supply chain strategies and introduce on-demand manufacturing for the long term. The real-time nature of 3D printing not only helps businesses retool to solve immediate supply shortages, it simplifies and shortens supply chains by allowing components to be produced closer to home and nearer to the customer. By extension, the headaches that often come with navigating international transportation, tariffs, and exposure to geopolitics, are reduced. Moreover, cost-effective trial and error can encourage rapid prototyping that fosters greater innovation, personalisation of products, and improved time-to-market. The ability to print a customer’s order as required also has the potential to save businesses from holding large inventories of product and reduce costs associated with holding warehouse space. The current crisis has reminded us how interconnected our supply chains are, with conduct in one country having a ripple effect across the globe. Yet thanks to 3D printing, the pandemic has also reminded us of the value of local manufacturing and the need to promote capability-based alliances across industries. Replicating experiences seen in the healthcare sector, the benefits of on-demand printing to shortened supply chains and improved timeto-market apply to all industries and businesses. As businesses begin assessing their strategic priorities and changes to manage the impact of COVID-19 on operations, we should learn from past experiences and embrace cutting-edge technology, like 3D printing, to streamline operations and reduce exposure to global fluctuations.
Amaero launches two new machines
Amaero has expanded its machine offering with the launch of two additional metal 3D printers – the SP260 and the SP400 – as well as new powder-handling ancillary equipment.
www8.hp.com
cycles, and also provide optimised powder usage with variable build areas, further improving efficiency and cost-effectiveness. Amaero CEO Barrie Finnin commented: “Amaero welcomes the new SP260 and SP400 to its line-up, giving our customers access to a broader range of machine sizes to meet their needs. Previously, Amaero had commissioned the SP500 and SP100 machines, providing customers with access to products at both the larger and smaller end of the scale. After the addition of the new machines to the lineup, Amaero’s product list meets the market’s requirements for small to mid-sized machines, addressing a larger segment of the market.” Amaero also plans to further expand its line-up with the launch of the SP800 (currently under development), which is anticipated for release in 2021. The SP800 will address the large build volume capacity segment of the market with a build chamber size larger than 800mm x 400mm x 500mm (which is currently the largest laser powderbed fusion build volume available).
www.amaero.com.au
Explore your unlimited possibilities additively
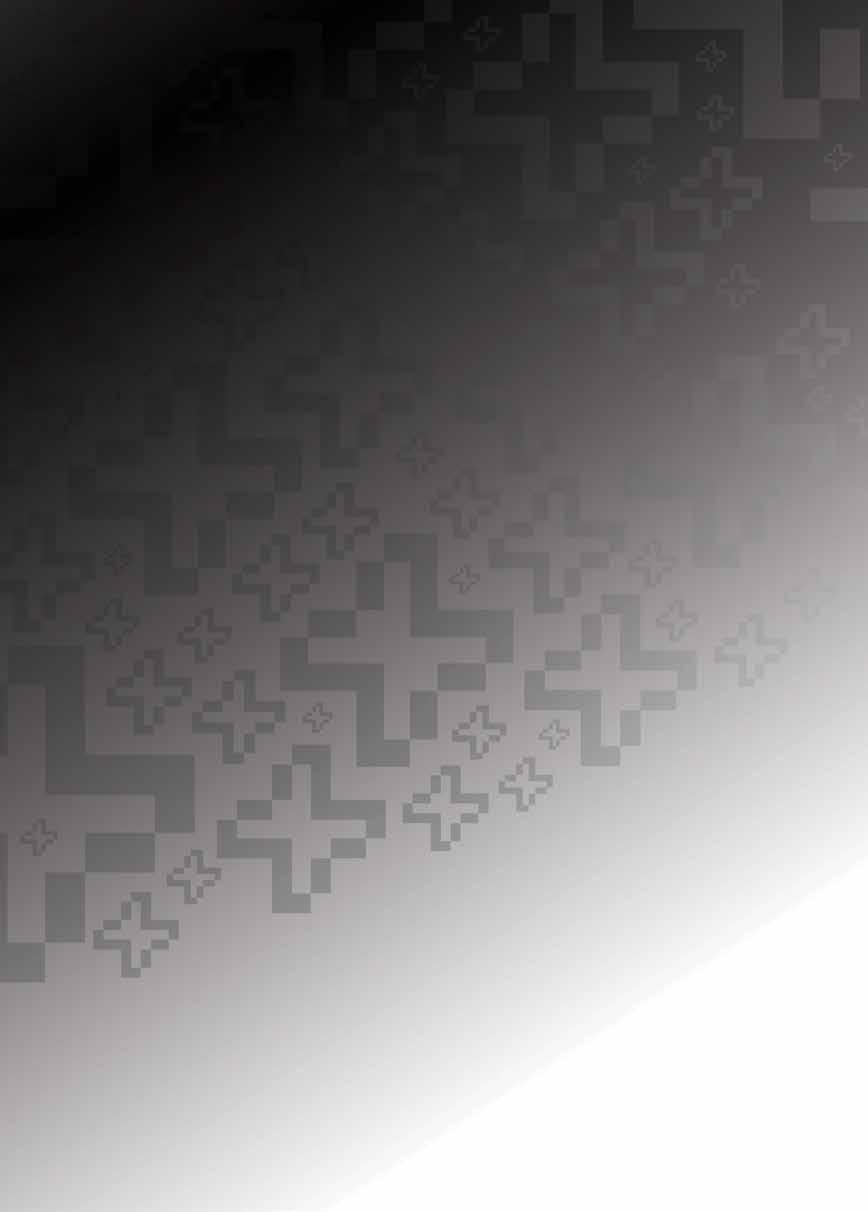
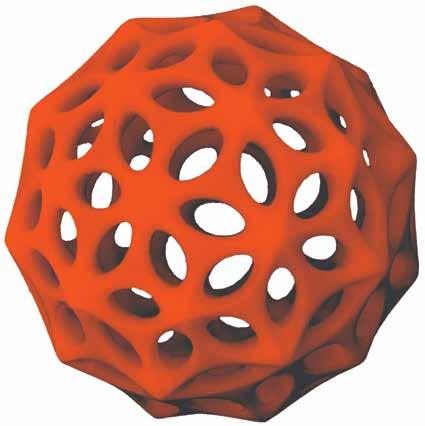
The Additive Manufacturing Hub is a $1.85m programme that will grow and develop additive manufacturing capability and investment in Victoria. The vision of the AM Hub is to provide an industry-driven network of users, suppliers and supporters that will foster and grow the use of Additive Manufacturing technology in Australia. + Promote and market additive manufacturing sector capabilities. + Expand the knowledge base of additive manufacturing technologies. + A grant programme for Victorian businesses to encourage adoption of additive manufacturing technologies. + Support the creation of high quality additive manufacturing jobs. + Be a voice to Government on additive manufacturing sector development.