
7 minute read
Overcoming process uncertainty to reduce scrap/rework
from AMT DEC/JAN 2021
by AMTIL
Overcoming process uncertainty to reduce scrap and rework Product quality is a key performance indicator for manufacturing businesses. Many workshops believe that achieving quality-standard certifications such as ISO, NADCAP and API affirms the quality of their work. In reality, the standards do not fully focus on how to make acceptable finished workpieces, but rather concentrate on establishing procedures for rejecting bad parts. By Patrick de Vos, Corporate Technical Education Manager, Seco Tools.
A true picture of a manufacturer’s product quality comes from a look into the shop’s quality control area, especially where there are parts with stickers or tags calling for “re-inspection.” The tags indicate that for some reason the workpieces were rejected or must be returned to production for rework. Scrap and rework result when manufacturing processes do not meet expectations. Some processes, especially machining, are based on the interaction of many variables and thereby are subject to uncertainty and some degree of unreliability. It is essential that manufacturers recognise the sources of uncertainty, understand how they arise, and find ways to resolve them. In many cases, however, the sources of process uncertainty are not recognised or are ignored and accepted as standard practice. In the end, overcoming uncertainty and limiting scrap and rework comes down to the awareness, knowledge and motivation of those on the shop floor. Sources of uncertainty Competitive pressures prompt manufacturers to perform costreduction analyses. The analyses include examination of spending for materials, tooling and machining time. Seeking out and eliminating the many instances of lost time offers significant opportunities for controlling costs. Methods used in cost analyses include overall equipment effectiveness (OEE) and Lean programs. Such analyses, however, often are based on a view of the manufacturing process as a kind of self-contained, simple box. A shop puts raw material or a semi-finished product into the box, machining processes occur, then a certain number of workpieces exit the box, either as finished products or as semi-finished workpieces destined for another box. What is often missing in the analyses is recognition that in the real world, it is not totally certain that every product that leaves the box will be acceptable. Unacceptable products must be reworked or scrapped. The number of unacceptable workpieces produced depends on how closely the variables in the manufacturing process are controlled. Processes such as forging, for example, are not extremely complex and do not require an extreme level of precision. These processes therefore are relatively controllable, reliable and capable of consistently delivering the expected number of acceptable workpieces. In contrast, other manufacturing processes involve multiple variables that can reduce the predictability of the outcome. The number of acceptable workpieces coming out of the box is not reliably predictable. It is an exaggeration to call all machining processes unreliable, but describing them as not entirely predictable is quite accurate. Machining involves many variables. It subjects cutting tools and workpiece materials to strong cutting forces and high temperatures. The combination of forces and temperatures creates a complex and fluid situation. The hardness of a tool determines its ability to cut effectively, and hardness will vary between room temperature and the 800˚C temperatures generated in machining. Heat also affects the machining characteristics of the workpiece material. The effects of the variables are unpredictable. Even if machining parameters are specified for a certain application, the exact values that exist during operation will be unknown. Varying results in surface finish or dimensions can make a part a candidate for rework or the scrap bin. When parts are unacceptable, two areas need to be examined. One area is technological: a manufacturer needs to know what is actually happening, recognise which variables caused the unexpected result, and decide how to resolve the problem. The other area for examination involves determining the financial effects of producing
unacceptable parts. That includes calculating the unexpected cost of rejection or rework and deciding how the company will account for it. Mass production scenarios generally compare the number of unacceptable parts statistically with the hundreds or thousands of parts produced overall. Over long production runs, the shop can analyze the operation, note the factors that resulted in the unacceptable parts, and update machining parameters to minimise uncertainty and maximise reliability. In high-mix, low-volume manufacturing scenarios, however, there is minimal time to examine unacceptable parts and change machining processes to eliminate them. The challenge is greater if a production run consists of only a single item. The issue is multiplied further when the shop is not familiar with the workpiece material and the end customer requires the finished part immediately. An unacceptable result on a job involving a single part demands machining of another part, increasing cost and disappointing the customer. In the case of mass production, eliminating the production of unacceptable parts is relatively simple. Technological staff review and update the process, make trial runs, and arrive at a solution. In true mass production scenarios, the number of unacceptable workpieces is relatively very small compared to the total production output, and the costs are negligible. But in the case of high-mix, low-volume or even single-part production, the cost of unacceptable parts can severely depress profit margins or even result in an operating loss. The manufacturer has just one opportunity to make an acceptable part in an extremely limited amount of time. Hidden or ignored costs Some costs that should be included in the total cost of manufacturing may be hidden or ignored. An example is the cost of deburring. A workpiece is considered complete when its machined surface finishes match specifications and its edges and geometries match blueprint requirements. A part with a burr is not complete. Although a burr represents a lapse in machining quality, burrs often are accepted as a normal consequence of the process. In any case, burrs must be removed and the cost of accomplishing that can be significant. In a real-world example, a highly-automated shop with five-axis milling machines produced a family of parts that required manual deburring. Ultimately, the time and labour involved in deburring represented 20% of the cost of a finished workpiece. In some cases, the cost and price calculations for a part are based on machining processes without considering the cost of deburring or other secondary operations. Such costs may not be negligible. To gain an accurate picture of total manufacturing cost, hidden costs must be recognised and mitigated. Tool selection Use of appropriate production equipment and tooling will minimise variability in machining operations. Large, rigid machine tools can resist the forces of heavy machining that cause inconsistent workpiece dimensions. Machine tool features such as glass scales, linear guides and thermal management systems maximise accuracy. Cutting tool selection plays a major role in limiting variability. Over the last two or three decades, the approach to tool selection has evolved. Previously, tool choice was basically divided between highperformance tools that offered the greatest possible output rates and economical tools that provided the lowest possible cost per part. In some cases, however, the highest-performing tools were relatively fragile. When they worked well, they worked brilliantly, but careful application was paramount. The lower-priced tools did not match the speed and output capability of the high-performance tools, but the price advantage came at the expense of lower output. When choosing tools today, a key consideration before choosing geometries, speeds and feeds is what a user requires in terms of tool performance. For mass production operations, there remains a need for tools that maximise metal removal rates and tools that offer maximum tool life. Extremely high-precision applications require tools whose manufactured dimensions, wear characteristics, and application parameters have been developed with extreme accuracy in mind, albeit at a premium tool cost. In the present era of frequent high-mix, low-volume production scenarios, it is extremely important that the quality of the finished workpiece meets expectations the first time the part is machined. The focus is on tools that work in a wide variety of situations with minimal process development time. When put to use by production engineers and operators who know the tools’ capabilities and limitations, tooling engineered to be reliable and versatile is the answer for many applications. Working with a limited number of versatile tools enables an operator to learn and understand tool performance over time while adapting to machining of variety of different workpieces. Knowledgeable application of versatile tooling can minimise production of rejected workpieces, and increased process reliability can help management gain an accurate picture of costs and profit margins. www.secotools.com
Built tough in the USA, the SLAGHOG™ removes slag buildup from your laser cutter support surface with much less effort. This patented motorized tool works on both copper and steel support slats and is easily cleaned in minutes by a single operator. Watch your productivity SOAR
Save time and money with Slat Shield Plus.
Slat Shield Plus is a slag/dross preventative that reduces spatter on backside of cut parts and makes cleaning slats faster and easier.
Slat Shield Plus now available from as low as $80. Visit LaserThings.com.au for 10% off Use promo code: AMT Offer expires 1/02/21
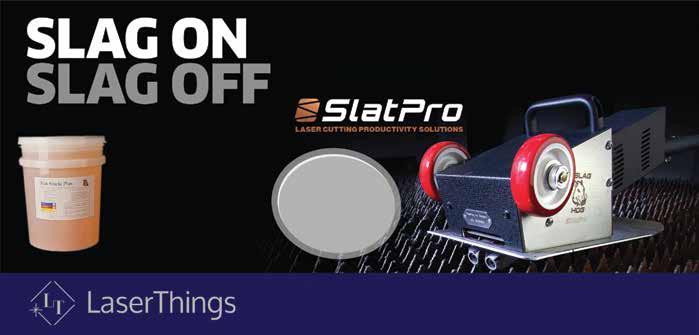