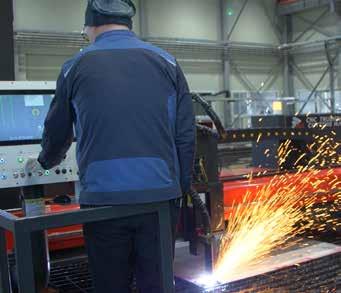
6 minute read
Hypertherm’s XPR300 - Raising productivity, quality
from AMT DEC/JAN 2021
by AMTIL
Raising productivity, product quality with Hypertherm’s XPR300
Today’s manufacturing landscape is changing rapidly with the onset of technological advancements, leaving businesses to grapple with a variety of associated challenges. One such challenge is maintaining an edge over business rivals, requiring manufacturers to pay close attention to the way they maximise productivity while ensuring product quality is not compromised.
For South Korean metal fabricator Daeyoung Sus Tech, in seeking to thrive in this competitive business environment, it was paramount to find a solution that will enable it to retain its competitive edge and improve production capabilities for the long term. Since beginning its operations in 2001, Daeyoung Sus Tech (formerly known as Cheolwon Stainless) has been focused on producing stainless steel parts and bars for semiconductor manufacturers and construction companies. A solution to meet future needs In 2018, in a bid to consolidate its capabilities and expand operations, Daeyoung Sus Tech began the process of setting up a new factory building — one that was almost four times larger than its former plant. The management team wanted not only to update the company’s equipment, but also to find a solution to enhance its production capabilities. Previously, the company had deployed a local plasma system for its cutting needs. However, this system — which took over 12 hours to fulfil an order — was proving to be inefficient. The Daeyoung Sus Tech team embarked on a hunt for a cutting system that would reduce cutting times and equip the company to meet future production needs. After an extensive search, the team found that the Hypertherm’s XPR300 plasma cutting system met all their rigorous requirements. “We were focused on searching for a solution that would help us improve on work speed and cut quality,” says Cho Woo Je, General Manager at Daeyoung Sus Tech. “After meeting with the Hypertherm customer service team we were very impressed by both the X-Definition technology, and their service. So we made the XPR300 our top choice.” Reaping the benefits of the XPR300 Hypertherm’s X-Definition technology offers improved cut quality on mild steel, stainless steel, and aluminium. Through features such as HyFlow vortex or vented nozzle technology, Vented Water Injection (VWI), and vent-to-shield technology, X-Definition plasma cutting systems bring about cleaner, sharper, more consistent edge quality and colour. With this latest technology, Hypertherm’s XPR300 cutting system allows users to enjoy increased cut speed, significant improvements in productivity, and reduced operating costs. For Daeyoung Sus Tech, which works with stainless steel materials that range from 6mm to 100mm in thickness, finding a solution that could address its varied cutting needs while enjoying excellent cut quality was a dream fulfilled. New features on the XPR300 system also made things easier for operators, while ensuring optimal performance and unmatched reliability. Users possess full control of functions and settings via the CNC, which is intuitive to operate and provides automatic monitoring. All these features made it easy for the team at Daeyoung Sus Tech to get accustomed to the XPR300 system quickly and to commence their production processes. “After an initial set-up, it was very convenient for our workers to commence the cutting process automatically by simply pressing the start button,” says Shin Hui Seong, Senior Manager for Operations.
Above: The XPR300 offers users full control of all functions and settings via the CNC, allowing efficient work processes on the production floor.
Left: Hypertherm’s XPR300 plasma cutting system.

Speaking about how the XPR300 has improved his team’s capabilities, Shin adds: “The old system used to take almost 12 hours to fulfil an order. With the new XPR300, we can now complete the same order within just 7-8 hours. Our production time has been reduced by more than 30% and we have expanded our production capacity for more orders.” A partnership set to last After just two months, Daeyoung Sus Tech noticed the obvious benefits of the new addition to its production floor, especially the multiple improvements that the XPR300 had made over its previous system. “Our efficiency and product quality have improved significantly,” comments Cho. “I am satisfied that we’ve not had any problems since using the XPR300, which I’d highly recommend. We’re also looking at additional purchases in the future so as to move forward with our expansion plans.”
www.hypertherm.com
transfluid – K series targets reliability, durability
Following a recent review of its portfolio of machines to bend and process tubes, transfluid has revealed a number of changes to its K series of machines.
All the machines in this series can now be controlled with a touch panel, opening up new possibilities such as displaying the comparison of target and actual values for all axes. Control of the tolerance of length and rotation reduces the need for operator involvement during tube manufacturing. The options have also been improved by the ability to load bending data for individual products from a PC via a USB port. The machines are robust and easy to operate. A selection of setups is available to process tubes of different lengths, from 1,500mm up to 6,000mm. The machines feature a range of special equipment options such as an integrated saw, a burring device, a tool for cutting ring pre-assembly, or one for flaring. The machines cover all standard diameters from 6mm to 42mm in hydraulics, and can process tubes with thin and thick walls. The DB 2076K model is capable of processing tubes with diameters of 6-76mm and all the standard wall thicknesses and materials. To obtain radii of 1.5 x D (tube diameter) of ideal quality with a bending procedure, this machine has a follower pressure die. It is operated hydraulically and supports the tubes during the bending process. This makes many applications possible, including construction of railings, tubing for installations, and the production of systems for exhaust gasses. transfluid’s K series is completed by the DB20101 machine with mandrel. Particularly suitable for the constructions of pipelines, the machine covers almost the whole range of tubes for installations. The different types of equipment available are the same as those for other types of machines. All materials can be processed, and small radii can be manufactured without any problems.
All of transfluid’s K series machines are now equipped with touch panel controls that are easy to use and compatible with several different interfaces. © transfluid
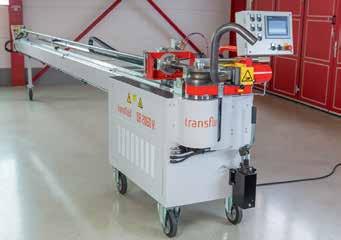
In addition to this, all machines can be equipped with a programmable controlled mandrel withdrawal, mandrel lubrication device and wiper dies. These machines are extremely reliable for tube processing, thanks to their stable construction. For this reason and because of the many options, the transfluid K series offers solutions to different sectors with the most diverse applications. This optimisation helps a lot with the reliability and the durability of the machines. www.transfluid.de
SMALL THINGS CAN MAKE A BIG DIFFERENCE.
EXAPRESS PBH 110/3100 - Delem 58T Graphical Controller - 5 Axis as Standard - Japanese Style vertical loading Quick Clamps - DSP Laser Guarding System from $74,500 EX-STOCK
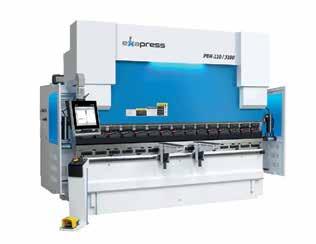
from $88,000
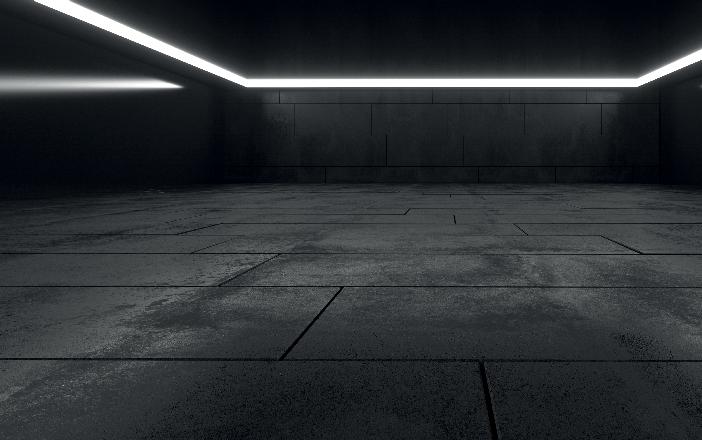
LASTECH RAPTOR - SMALL FOOTPRINT FIBER LASER
- Cut up to 20mm Mild Steel - IPG Laser Source - Swiss designed Raytools cutting head - Simple Operation via Cypcut
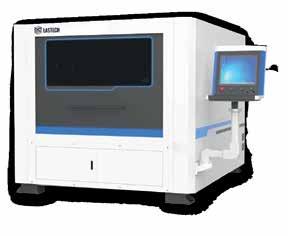
sales@capitallaser.com.au CALL US TODAY: 1300 596 381 www.capitallaser.com.au
