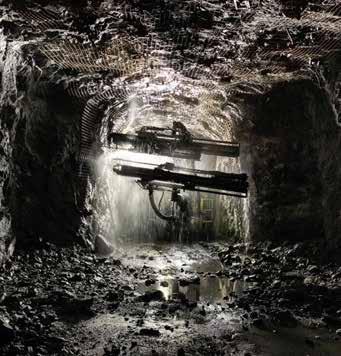
7 minute read
AM Hub case study: Gazmick
from AMT JUN/JUL 2021
by AMTIL
Mining solutions firm Gazmick worked with the Additive Manufacturing Hub in the development of an innovative new concept for rock bolts used to provide mining ground support.
Gazmick is a small, privately owned business dedicated to improving ground support in the mining industry. Gazmick has enjoyed great success in patenting novel ground support solutions, such as rock bolts. Up to now its most successful bolt is the Stiff Split Set, a modified friction bolt. Via a licensing agreement, Gazmick has sold in excess of 4 million units throughout Australia and Asia. Gazmick looks to solve other rock bolt problems to enhance the safety and efficiency of mining and tunnelling operations. The challenge
One common type of rock bolt is the resin bolt. In this embodiment a steel bar is locked into the rock using a two-part resin pack. Currently the resin is contained in a two-part “sausage” and placed into the hole in the strata. To avoid danger, this is done remotely, with the operator working approximately five metres away behind a protective steel canopy. This resin installation process has remained unchanged for the last 10 years and contributes significantly to the entire bolting cycle time. The process is: 1. Drill the hole. 2. Insert multiple sausages. 3. Insert the steel bar, rotating it, and thereby mixing the resin at the same time. A method of more easily placing resin and rock bolts in holes has been sought for a considerable period of time with little success. Gazmick developed a patented solution whereby a canister full of resin, similar to a hypodermic syringe, is placed onto the rock bolt. The resin and hardener are separated in the canister. The nozzle of the canister is placed into a hole and the combination of the two products are injected into the hole by applying force to the rock bolt. Once the material is fully injected into the hole, further force is placed onto the steel bar. This punctures the top of the canister and allows the rock bolt to enter the hole through the nozzle of the canister. The bolt spins, thereby mixing the product, and a plate attached to the rock bolt crushes the canister between the strata and the plate. Using this method, the old three-step process is reduced to two. It offers mine operators greater safety, improved quality of installation, and invaluable time-savings. The speed of the process is worth millions of dollars to mining companies worldwide. The difficulty Gazmick faced was in determining and proving the mechanical properties of the canister. The tolerances are relatively small, and the need for accurate implementation activation was critical. Moreover, if the crown of the “piston” inside the canister was too strong the bolt could not pierce it and enter the hole. If it was too weak, the bolt would break through prematurely and the resin would not be injected into the hole. Getting the balance of all the components was critical in determining the practicalities of the concept. Injection moulding of protypes would be far too expensive so a fasttracked, cheap prototype construction method was required so that destructive testing could be undertaken. An additive manufacturing program using 3D printing techniques was identified as the fastest and most cost-effective way to construct the protypes, at which point Gazmick sought assistance from the Additive Manufacturing Hub (AM Hub). The solution
The AM Hub engaged registered service providers GoProto (ANZ) Pty Ltd to assist Gazmick in its project. A finite element analysis (FEA) was undertaken of critical parts of the device. The physical properties of the crown of the piston inside the canister were critical. Prototypes were then 3D printed and tested against breakout strength in a calibrated load device. Once a “preferred protype” was achieved, these were tested at the property of a Gazmick partner, where the use of a rock bolt simulation rig test could be undertaken. After multiple iterations, a successful combination of size and strength was achieved, and near-perfect results of resin mixing and rockbolt installation were observed in test sample cross sections. How the Additive Manufacturing Hub helped
It was predicated that the project would make full use of a $17,940 co-contribution under the AM Hub’s Build It Better (BiB) voucher programme for 3D printing performed by GoProto ANZ. In the end, a total of $3,032.22 in total was spent. The fast-tracking of prototypes exceeded expectations, despite some delays that occurred as a result of fires in southern New South Wales, where the test facility was located, and because of the COVID-19 pandemic, which stopped all testing-related travel. Project outcomes
Gazmick was able to test multiple iterations of its concept, which provided enough confidence to move forward with specialised in-field test prototypes – these are about to be constructed. The demonstration of the concept has also provided the confidence for a multi-national company to sign a heads of agreement with Gazmick, which will allow further testing and an option to manufacture and supply this product for worldwide distribution. There is still work to be done, but Gazmick’s confidence has been greatly enhanced and the team is looking forward to conducting mine site trials in the immediate future.
The AM Hub is an initiative delivered by AMTIL in partnership with the Victorian State Government to promote the adoption of additive manufacturing technology. For more information, please contact John Croft, AM Hub Manager, on 03 9800 3666 or email amhub@amtil.com.au. www.amhub.net.au www.goproto.com.au
Chilean mining giant to build new manufacturing facility in Victoria
A Chilean-based international designer and manufacturer of mining equipment chooses Victoria for its state-of-the-art manufacturing facility and global headquarters, in a move that is expected to create up to 100 new highly skilled jobs.
Conymet Duratray International plans to onshore its overseas manufacturing activities to the new facility in West Cranbourne, southeast Melbourne. The facility will include a new innovation division that will focus on mining data analytics, machine learning and the Internet of Things, as well as advanced composite materials for its product line. The company intends to draw on Victoria’s highly skilled workforce and the state’s innovation and research & development (R&D) capabilities to develop expertise in these areas. It will also benefit from Victoria’s international logistics and distribution network to service its key export markets and the state’s growing mining equipment, technology & services (METS) sector. “We’re excited to embark on this new innovation journey in Victoria,” said Marcelo Medel, Managing Director of Conymet Duratray International. “We’re committed to supporting Victoria to become the mining tech hub of Australia, given its strengths in the METS, advanced manufacturing and technology sectors.” Founded in 1974, Conymet Duratray specialises in the design and manufacturing of mining truck trays, spare parts, steel and rubber components for haulage equipment for the mining industry. The company operates facilities in Australia, Chile, the United States, South Africa and Russia and currently exports to more than 35 countries across five continents. Currently, there are more than 2,000 Duratray mining truck trays operating globally, ranging in size from 36 to 360 tonnes for all major truck manufacturers. Conymet Duratray was the first Chilean company to make a substantial investment in Australia and celebrates 20 years in the country this year. The company has been recognised in the Governor of Victoria Export Awards in 2010 and 2019 and was inducted to the Victorian Manufacturing Hall of Fame in 2015. “The support we’ve had from the State Government on many initiatives over the years has been a key enabler for us to develop, expand and grow our business into Australia and the other 34 countries where we export our technology,” Medel added. Victoria’s Minister for Economic Development Tim Pallas welcomed the decision by Conymet Duratray to grow its current Victorian footprint: “Conymet Duratray is relocating its global HQ to Victoria because of our highly skilled workforce, and our world-renowned capabilities in advanced manufacturing, innovation, and research and developments. Attracting investment from companies such as Conymet Duratray will help us grow high-value jobs and boosts our economy.” www.duratray.com

6KW MITSUBISHI STOCK MACHINE ON THE WAY. GET IT BY EOFY! WE WILL ACCEPT TRADE-INS.
OWN FOR AS LITTLE AS $321 A DAY
Mitsubishi‘s 5 year warranty
Mitsubishi’s own Japanese-made fiber laser source comes backed by a 5 year warranty. AGR-eco
Mitubishi‘s exclusive AGR-eco technology reduces Nitrogen consumption by up to 90%, drastically improving processing speeds.
AI Assist Cutting
Mitsubishi’s AI automatically fine-tunes the cut conditions during processing by reading multiple cutting-head sensors, ensuring peak performance with no additional training or operator involvement.
Mitsubishi Zoom Cutting Head
Mitsubishi‘s Zoom Head adjusts the beams FROM diameter and focal height on the fly, far exceeding the performance of traditional autofocus cutting heads.
By providing optimal spot-size, cut quality and speed are improved dramatically across all thicknesses and materials. This next-generation high-performance controller from Mitsubishi allows one touch operation of advanced functionality.

Mitsubishi Bar Code Scanner
The use of a unique job barcode and scanner allows easy operation, minimising additional costs associated with operator training and machine downtime.
BEFORE YOU BUY: MAKE SURE YOU HAVE THESE FEATURES!
Mitsubishi D-Cubes Controller
CALL US TODAY: (03) 9115 1444 sales@kaizenmachinery.com.au www.kaizenmachinery.com.au