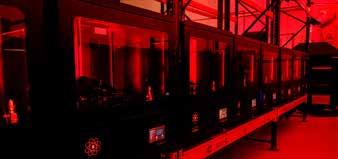
14 minute read
PRODUCT NEWS Selection of new and interesting products
from AMT JUN/JUL 2021
by AMTIL
Photocentric reimagines manufacturing with LC Magna
The LC Magna 3D printer from Photocentric delivers an impressive combination of large build volume and accurate printing, making it a powerful tool for custom mass manufacture.
The build volume of the LC Magna is 510mm by 280mm by 350mm, making it the largest build volume LCD screen-based 3D printer currently available. LC Magna has a 60cm 4K Ultra HD screen, offering unbeatable precision and detail when creating high-resolution, mass-manufactured parts. The screen has been matched with a custom-built backlight. These two elements work together to ensure extremely high print accuracy, delivering amazing detail. Product designers, engineers and manufacturers alike can now benefit from LC Magna’s large build volume capabilities and maximise build plate capacity to increase throughput, speed up assembly production and reduce lead times. “LCD screen-based 3D printers have been the fastest growing area in 3D resin printing,” says Sally Tipping, Sales Director at Photocentric. “This machine sets new standards, making it best in class in almost every respect – it really is a disruptive industrychanging machine.” The hardware and electronics of LC Magna have been designed by Photocentric with high-precision reliability in mind to ensure consistent robust performance. The patented peel release mechanism ensures low force, which creates reliable prints, small support tips and very fast printing. LC Magna also comes with a large 18cm interactive graphical user interface (GUI) to aid user control, which also facilitates the printer hardware to be used to its full potential. Delivering consistent accuracy across a massive build plate with 100% of models’ tolerance at less than 100μm and an average accuracy of within 50μm, LC Magna can be used for batch producing small parts such as 3D printer components, orthodontic aligners, detailed game figurines, or for scaling up to large prototype parts such as automotive suspensions or bike stands. The advanced technology of LC Magna accommodates the evolving need of 3D printing in businesses looking to turn their digital images into physical parts more and more rapidly. Building on the company’s core expertise in the innovation of photopolymer manufacture, Photocentric’s in-house team of chemists have formulated a range of high-performance Daylight photopolymer resins covering all essential applications. Photocentric enjoys a partnership with BASF 3D Printing Solutions, which focuses on establishing and expanding the 3D printing business with materials, system solutions, components, and services. The two companies are working together to provide solutions for specific applications to enable custom mass manufacture of functional parts in scale and at cost-effective prices. This co-operation offers solutions to industries that enable processes to be made using additive manufacturing to replace traditional tooling methods and creating flexibility of geometry, absence of tooling costs and custom design.
Bilby 3D recently became the Australian distributor for Photocentric. www.bilby3d.com.au
John Hart – One-stop shop for OnRobot EoAT range
John Hart has entered into a distribution agreement for the OnRobot product range, featuring a wide assortment of end-of-arm tooling (EoAT) and end effectors for collaborative robot applications.
The OnRobot range of robotic arm grippers, sensors and tool changers makes it faster and simpler to automate tasks such as packaging, materials handling, machine tending, assembly, and surface finishing. With its new partnership with OnRobot, John Hart aims to provide effective solutions to help small and mid-sized manufacturers optimise their processes and grow their businesses, with greater flexibility, higher output and improved quality. According to John Hart, collaborative automation has levelled the playing field for small and mid-sized manufacturers, and as robots become easier to buy and implement, the tooling has become the vital element in adapting for a wide range of applications. OnRobot’s product range features a wide assortment of tools for collaborative applications, including: electric, vacuum and magnetic grippers, the award-winning Gecko gripping technology, force/torque sensors, a 2.5D vision system, screwdriver, sander kits and tool changers. Headquartered in Odense in Denmark, OnRobot also has offices in Los Angeles and Dallas in the US, Soest (Germany), Barcelona (Spain), Warsaw (Poland), Budapest (Hungary), Shanghai (China), Tokyo (Japan), Seoul (South Korea) and Singapore. In a statement, John Hart said: “OnRobot provides compatibility and versatility beyond compare. It’s everything manufacturers need from one supplier, providing even more value from an automation investment.” www.johnhart.com.au
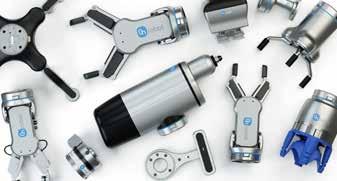
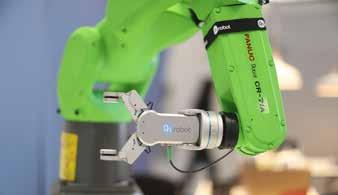
Kaeser Aircenter: Efficient and future-proof
The latest generation of the compact and dependable Aircenter all-in-one compressed air systems from Kaeser are not only more efficient than ever before, but also now include a future-proof compressed air refrigerant dryer.
The user-friendly Aircenter is a complete turnkey system which incorporates a Kaeser rotary screw compressor, an energy efficient refrigeration dryer and an air receiver – all in one space-saving compact package. The space-saving design has long since made the Aircenter the ideal solution where space is at a premium, such as in auto body garages and workshops. For 5.5kW to 9kW requirements, the Aircenter incorporates the Kaeser SM series rotary screw compressor. For maximum efficiency, the SM 10 and SM 16 compressor models both have premium efficiency IE3 motors, and the SM 13 compressor model is now equipped as standard with a super-premium efficiency IE4 motor. These motors comply with and exceed prevailing Australian GEMS regulations for three-phase electric motors. IE4 motors are the technology of tomorrow, with current regulation introduced in January 2015 only requiring the use of IE3 Class motors. For the end user this translates into the best possible compressor performance, reduced energy costs and significantly enhanced compressed air production efficiency, all available today. For even greater intake volume and efficiency, the latest generation of SM series rotary screw compressors are also equipped with the SIGMA 06 screw compressor block, featuring even further refined Sigma Profile rotors. Together with the IE4 motor for example, Kaeser has been able to reduce the energy requirement of these compressors by up to 13%. From the end of 2019, all refrigerant dryers from Kaeser Compressors have been using the new R-513A refrigerant. This includes the refrigeration dryers that can be found in the Aircenter models. R-513A refrigerant offers the most future-proof operating solution for refrigeration dryers. Utilising this climate-friendly refrigerant will assist compressed air users in future-proofing their system as Australia transitions to low-GWP (global warming potential) refrigerants as part of the Australian hydrofluorocarbon (HFC) phase-down. All Kaeser refrigeration dryers are designed to provide maximum efficiency and energy cost savings. Thanks to the new refrigerant, they are also future-proof for their entire service life when it comes to applicable refrigerant legislation. With sound levels as low as 62 dB(A) the Aircenter is also suitable at point of use. The SM series Aircenter compressed air systems are available with drive powers of 5.5mkW to 9 kW, and produce flow rates from 0.59 to 1.62 cubic metres per minute, designed for pressures up to 15 bar.
www.kaeser.com.au
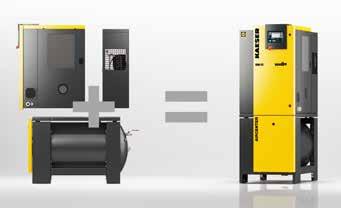
ECI Manufacturing 2021 Webinar Series
Throughout 2021, we’ll be hosting a series of exclusive webinars demonstrating how ECI’s unique manufacturing solutions can support your entire business - helping you reduce costs, improve productivity and increase profitability.
We’ll be covering industry relative topics including:
Diversifying your supply chain
Untangling your scheduling spaghetti
Power Innovation with visible data
and more...
Dont miss out. Register today to reserve your place. info.ecisolutions.com/webr
AUS: 1300 130 241 | NZ: 0800 441 186
www.ecisolutions.com/au | How business gets done.
FARO RevEng Software 2021: New auto-surfacing capabilities for fast, high-quality CAD surfaces
FARO has announced the release of FARO RevEng Software 2021, the latest update to its RevEng software platform, featuring automatic surfacing capabilities, creating surfaces quickly directly from scanned point clouds and meshes.
As one of the most affordable, fastest reverse engineering Scanto-CAD software solutions available, RevEng 2021 helps users get work done faster by reducing data capture time and eliminating overlapping data points. It is ideal for aftermarket design, creation of replacement parts, new design iterations or additive manufacturing. The Automatic NURBS (Non-Uniform Rational B-Spline) Surfaces Creation Tool allows for the creation of a full network of curves and surface patches with the click of a button, ready for immediate export into a CAD file. Full control is also possible by customising the surface patches in the sketch mode with its flexible control point placement, while curves are colour-coded to quickly verify surface continuity. The 3D point cloud capture enables users to create models up to 1.75X lighter with a grid management feature to obtain clean, light, and consistent point cloud data. “Reverse engineering with RevEng is easier and faster than ever,” said John Chan, FARO Software Product Marketing Manager. “Users can scan with a FARO ScanArm – paired with the optional eightaxis rotating platform to increase acquisition speed – to generate a mesh of the highest quality and quickly produce exportable CAD surfaces for machining, finite element analysis simulations or 3D modeling.” Users can also import point cloud or mesh files from any source and repair the mesh with RevEng state-of-the-art optimisation tools, automatically repairing meshes up to 20 times faster than current leading tools and improving smoothing effectiveness up to 1.5 times faster. This makes RevEng software agnostic and can be paired with any inspection program – even for customers working with other software products. Additional RevEng 2021 upgrades include: • Deviation colour range – When reviewing deviations, users can adjust the range of colours, facilitating the validation and review of critical areas. • Info Panel – Additional data, including the number of holes as well as watertight mesh confirmation have been added, readily exportable for downstream applications. • Feature-reserving remeshing – Makes it possible to preserve sharp features, allowing changes to mesh density while preserving the design intent in corners and edges, improving compatibility with downstream workflow and applications. The RevEng intuitive user interface is another advantage that distinguishes this powerful software suite. The set-up, which displays all tools in a single location, facilitates the easy manipulation and customisation of a 3D object and enables the fastest cloud-toCAD conversion in the industry, significantly enhancing workflow productivity. www.faro.com
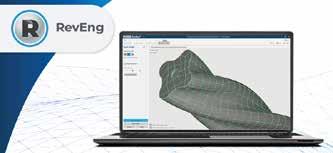
Dormer Pramet – Grooving growth continues
Dormer Pramet has expanded its GL assortment for parting-off and deep grooving applications with a new range of tools, double-edged inserts and geometries.
The additions provide new tooling options for small part machining and grooving with a shorter overhang. These support copy profiling and longitudinal turning in a variety of materials. It follows the company’s development of its parting-off and grooving range in November 2019, when the global manufacturer introduced the 25mm GL insert and the G8330 PVD grade to provide a versatile and stable option when machining steel, stainless steel and cast iron. These latest tools include new 12x12 holders to support additional radial operations, accommodating various insert widths and depth of cut capabilities. A reinforced brace design provides high rigidity and vibration resistance for good quality surface finish. Users can also benefit from set-up time savings due to an easily accessible clamping screw [30° angled] and a one-hand insert replacement feature. The new Pramet tool holders include the universal GLSF (RL) EXT for an overhang of 24-32mm and the GLSF (RL) EXT-G for grooving operations with a 10-12mm overhang. The GLSF (RL) EXT-S is the shank tool option and suitable for small parts machining and Swiss lathes. The long GL insert, which achieves 60% deeper capacity, over the previous LCMF16 insert, is also now available in two new geometries, GM and MM. Both feature a positive T-land for prolonged tool life due to low cutting forces and reduced risk of built-up edge. With a round cutting edge, the MM geometry is suitable for turning and copy profiling operations, while the GM geometry is designed for grooving and longitudinal turning. In addition, a range of wider inserts are available (up to 6mm) for small part machining. The design of the 5mm and 6mm wide MM inserts, for example, requires no tool modification for deeper cuts. All the inserts are available in both CVD T7325 and PVD G8330 to cover a wide range of materials. www.dormerpramet.com
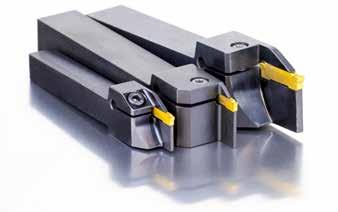
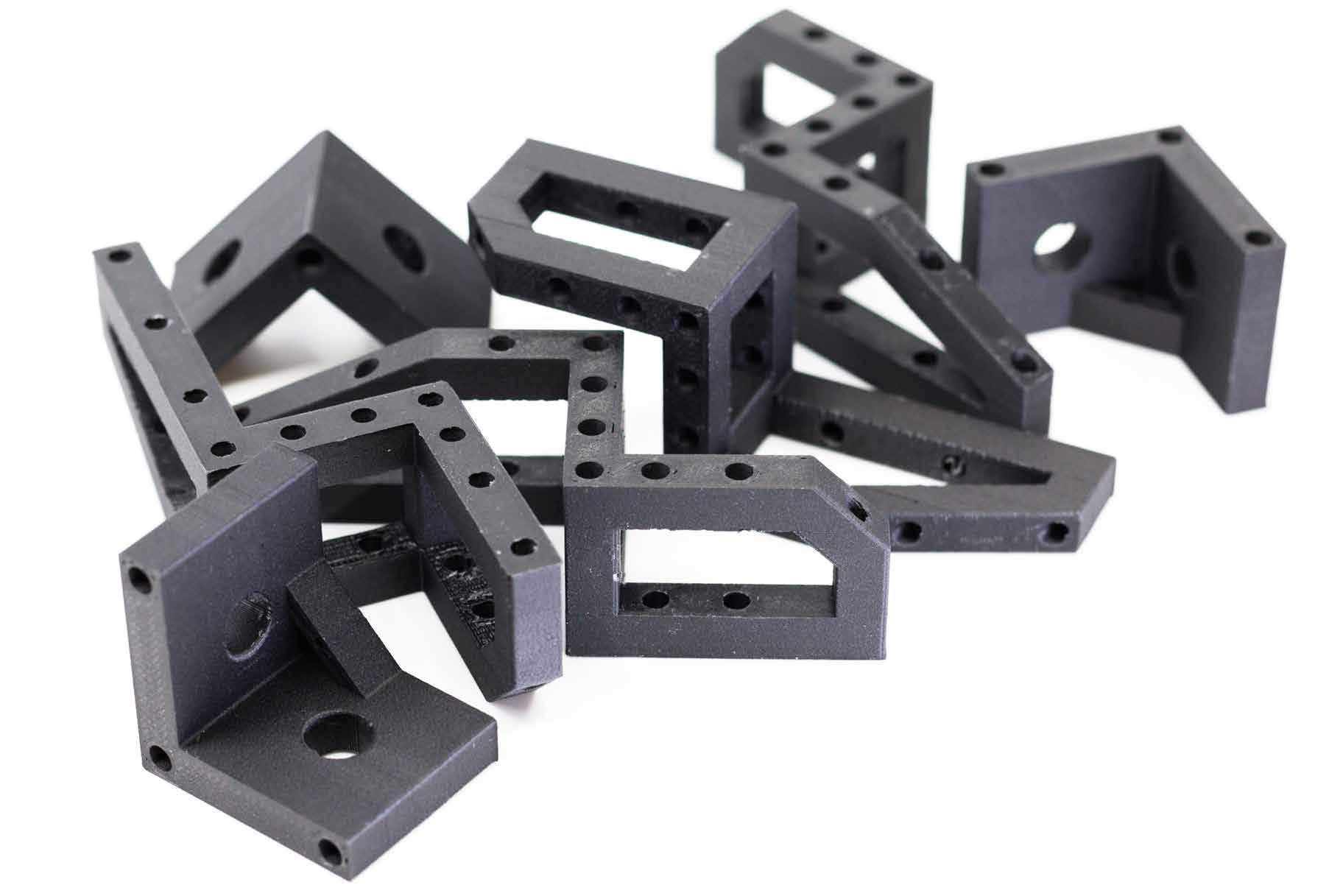
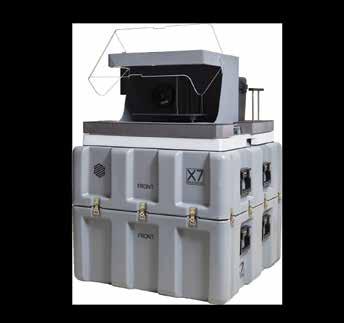
Mitee-Bite Heavy-Duty VersaGrip accomodates all workpiece shapes
US manufacturer Mitee-Bite is the innovator of compact, low-profile edge clamps geared towards improving productivity and providing solutions for difficult workholding applications. Its revolutionary Pitbull clamp remains the lowest-profile, highest-holding-force clamp in the industry today.
The company is now launching a new product to add to its extensive portfolio of clamps. The Heavy-Duty VersaGrip gripper is designed for those aggressive operations on harder materials while providing the versatility to hold just about any workpiece shape that can be imagined. The rotatable, flat, serrated top face allows for additional holding force in horizontal pockets in jaws or hard stops. Standard gripping height is 5mm; if a higher height is required, the workpiece can be elevated by resting part of it on the Original VersaGrip gripper, allowing for cutter clearance around jaws. The standard VersaGrip, as the name implies, provides versatility for clamping standard vise work as well as providing a solution for difficult applications that would normally require fixturing or machining soft-jaws. The VersaGrip is just one of a number of new products that the company has recently introduced, one of which is the new Heavy Duty T-Slot clamp. Designed to be used in the T-slots of machine tables, the versatile heavy-duty model is capable of generating an impressive 88kN of down force. This is coupled with a very low gripping profile, which reduces material cost and the number of machining operations required. The ‘HD’ clamp bolts straight down onto the machine table eliminating the need for a separate fixture. Set up time is accordingly reduced, making the machining operation quicker and more efficient. The hardened steel clamping element has both a smooth surface for machined workpieces and a serrated clamping surface for rougher work. The ‘HD’ clamp is designed specifically for use with Pitbull and OK-Vise clamps, which can be used on the same base in a variety of configurations, ensuring plenty of holding force. Another recently introduced product is TalonGrip; a simple bolton system that allows operators to perform aggressive machining operations while clamping on as little as 1.5mm. It is ideal for small lot sizes, difficult applications or proto-type work when building a fixture would not be beneficial. The new TalonGrip LL (long length) serrated grips are designed for applications where specific grip location is not necessary or higher and full length penetration is required. These new grips are designed as a “drop fit” into the original TalonGrip jaw sets or for use on a fixture, with a gripping height range of 1.27mm to 4.06mm. The grips are made from S7 steel, heat-treated and finished with a black oxide coating. The grips are laser engraved with a useful 10mm scale for reference on repeatable part placement. Mitee-Bite Products LLC began in 1986 with the original Mitee-Bite hex clamp created to save time on a re-occurring production job. The company has since grown to become the innovator of compact, low-profile edge clamps for CNC machining. Fast forward more than 30 years and Mitee-Bite continues to develop new products that provide customers with a wide assortment of high-density low profile clamping solutions.
www.dimac.com.au
ECI launches JobBOSS2 cloud-native ERP for manufacturing SMEs
ECI Software Solutions, a leader in cloud-based business management solutions, has announced its newest product: JobBOSS2 .
JobBOSS2 will be ECI’s go-forward cloud-based enterprise resource planning (ERP) software for the job shop and maketo-order segment of the manufacturing market, combining the strengths of existing ERP products, JobBOSS and E2 SHOP, the latter of which was acquired during ECI’s acquisition of Shoptech in Q4 2020. JobBOSS2 combines E2 SHOP’s cloud-native, user-friendly platform with JobBOSS’ depth of functionality and flexibility into one ERP platform designed to give shop owners more control over how they scale their businesses, grow revenue and maximise profitability. JobBOSS2 includes: • Customisable features and workflows so that users can make their software work for their business, rather than the other way around. • Robust reporting to fuel decisions based on data and current business and market conditions, rather than estimates. • A streamlined user experience to make it easier for manufacturers to maximise their operational efficiency and act more quickly. Best-of-breed advanced modules that complement JobBOSS2’s core capabilities, giving manufacturers one interface that meets all of their needs. JobBOSS2 will also integrate with Alora, a machine intelligence platform by Data Inventions. This integration will connect JobBOSS2 with real-time machine performance to give operators and managers the visibility they need to run business operations more efficiently, improving overall equipment effectiveness and decreasing downtime. “ECI’s first core value is ‘Crave Greatness’ – which means that we are dedicated to delivering innovative solutions for our customers, setting high goals for ourselves and creating a future where customers have exactly what they need to build and grow their businesses,” said Matt Heerey, President of ECI’s Manufacturing Division. “We have a unique opportunity to take the best of E2 SHOP and JobBOSS to create the most innovative and userfriendly product on the market.”