
26 minute read
INDUSTRY NEWS Current news from the Industry
from AMT JUN/JUL 2021
by AMTIL
New research shows surge in support for Australian-made
New consumer research from Roy Morgan shows the preference for Australian-made goods continued to increase in 2020, with the huge majority of 93% of Australians stating they are more likely to buy products made in Australia – up from 87% a year earlier.
Michele Levine, Chief Executive Officer of Roy Morgan, said Australian-made goods enjoyed an outpouring of support in 2020 as international travel was restricted. “Australian-made products have experienced a surge in support during 2020 with a large majority of 93% of Australians more likely to buy a product that is ‘made in Australia’, up 6% points from 2019,” said Levine. “Less than 1% of Australians say they are less likely to buy a product that is ‘made in Australia’ unchanged on a year ago. “The closure of international borders and restrictions on travel around the world appears to have helped increase support for Australian-made goods. Although the preference for Australianmade goods is very high across all age groups, it is Baby Boomers (96%) and Generation X (94%) who are even more likely to prefer Australian-made products than other generations.” Australian Made Chief Executive Ben Lazzaro said Roy Morgan’s latest research comes as no surprise, as more and more Australians are looking to the green and gold Australian Made logo to find authentic Australian-made goods. “Australia’s over-reliance on imported products has been highlighted during the COVID-19 pandemic,” said Lazzaro. “This research shows Australians are placing priority on manufacturing self-sufficiency and job creation along with a renewed appetite to address the imbalance between locally made and imported products to ensure Australia’s long-term prosperity. “When you buy Australia Made, Australian Grown products, you know what you are getting - products made to the highest of manufacturing standards and grown in our clean, green environment. At the same time, you are helping to support our manufacturing industry, create Aussie jobs and give back to local communities.” Almost all Australians (99%) are aware of the Australian Made logo, with the vast majority (92%) confident products displaying the logo are made in Australia. 97% of Australians also associate the iconic kangaroo logo with the support of local jobs and employment opportunities, 95% with safe and high-quality products, 89% with the use of ethical labour and 78% with sustainability. www.australianmade.com.au
Medical treatments to be fast-tracked with launch of Australian-first facility
The launch of Australia’s first medical device development and manufacturing facility in Melbourne is set to fast-track new treatments for people with diseases such as epilepsy, Parkinson’s disease, hearing loss, stroke and diabetes.
The new facility called Neo-Bionica, a joint venture between the Bionics Institute and the University of Melbourne, is a highly specialised laboratory, purpose-built with the latest cleanroom technology, cutting edge robotic equipment, enhanced 3D printing and precision engineering tools needed to develop prototypes and manufacture medical devices for clinical trials. Bionics Institute CEO Robert Klupacs said that providing researchers and engineers with the capability to build clinical trial grade medical devices in Australia will increase the speed from initial concept to clinical application. “Our Institute is renowned worldwide for developing life changing medical devices such as the cochlear implant, Minder epileptic seizure monitoring device and a unique nerve stimulation technique for the treatment of ulcerative colitis,” Klupacs said. “And yet, we currently depend on companies overseas to build prototypes of the latest medical devices for use in clinical trials. “The opening of Neo-Bionica in July will completely change how we translate Australian innovation, enabling home grown inventions to be manufactured rapidly in Australia for the benefit of patients throughout the world. We estimate that Neo-Bionica will enable the translation from research to clinic of at least 20-30 new medical devices over the next 10 years.” Ken Jefferd, Executive Director of Research, Innovation and Commercialisation at University of Melbourne, said Neo-Bionica will grow Melbourne’s reputation as a global biomedical powerhouse and boost the Australian economy. “Not only will patients reap the benefits of groundbreaking medical devices more quickly, Neo-Bionica will attract international collaborators, generate employment, strengthen Australia’s export capability and boost the economy,” Jefferd said. “Research impact through collaboration is a critical priority for the University and Neo-Bionica is a stellar example of our vision turning into reality.” University of Melbourne Professor Mark Cook, Chair of Medicine and Director of Neurology at St Vincent’s Hospital where Neo-Bionica is located, said the launch of the new facility will enable clinicians, scientists, engineers and industry partners to collaborate closely in the quest to find solutions for people with hard-to-treat diseases, like epilepsy. “The ability to walk from my consulting rooms to the Neo-Bionica facility and talk to the engineers developing prototypes for my patients to test will have a huge impact on the speed of developing new treatments, and the future of medicine in Australia,” Professor Cook said.
The Bionics Institute and the University of Melbourne are seeking $25m in philanthropic, investment and government funding for employment, manufacturing capacity and equipment at Neo-Bionica. For more information, go to: www.neo-bionica.com
Australian-made inspection machines to support US COVID-19 vaccine injector manufacturing
Australian automation system builder Andrew Donald Design Engineering (ADDE) has shipped the second of three specialist machines to prefilled injector manufacturer ApiJect Systems Corp in the USA.
Under Operation Warp Speed, the US Government’s initiative to accelerate delivery of COVID-19 vaccines, ApiJect has assembled three high-speed lines to enable the complete fill and finish of up to 1.5 million injectors per day. The ApiJect injector system is based on Blow-Fill-Seal (BFS) technology, for which ADDE has over 20 years’ experience building custom manufacturing and packing equipment, including for AstraZeneca in Sydney, which operates the largest BFS facility in Australia. When ApiJect required a system to perform 100% inspection of each injector it, contracted ADDE to build the highly specialised machinery. As expected for a COVID-19 vaccine and a program named Operation Warp Speed, time was of the essence, and ApiJect needed the shortest possible lead time. “Our first proposal was for a six-month program to completely design, build and commission three machines, and we thought that was pretty aggressive,” said Barry Hendy, Managing Director of ADDE. “But ApiJect then asked us if we could do it in three months!” Thanks to the strong support from ADDE’s key suppliers, the first machine is now installed and has completed testing in the client’s site in the USA. The second machine has been shipped while the third machine is in Melbourne for now to allow parallel product testing if needed. The ApiJect prefilled injectors are produced in a card of five doses with each card needing to be inspected for general profile, liquid fill, particles, and geometry. ADDE had built similar systems for another BFS operator in Australia so was able to leverage key elements of that design to achieve the fast timeline required. The ApiJect product, however, also required significant innovation in the handling, lighting, and inspection processes to perform the unique inspections required. “The ADDE team has done an amazing job to deliver this equipment in record time,” said Philip Leslie, ApiJect’s Acting Head of Manufacturing. “We have worked closely with them to produce a great system with the mechanical design and detailed inspection processes to enable us to achieve our unique inspection requirements.” While there is plenty of discussion about the challenges of developing a COVID-19 vaccine, there are also significant constraints in the supply and filling of vials and syringes to distribute the vaccine. The ApiJect technology provides a low-cost, high-speed, and sterile system to deliver safe, single-dose pre-filled injector. Each ADDE inspection machine supports the production of close to 500 injectors per minute, with 100% inspection of the critical parameters of the cards.
Swinburne, Sutton Tools to launch Smart Manufacturing Centre
Swinburne University of Technology and Sutton Tools have signed an agreement to establish a joint Smart Manufacturing Centre to work on projects in advanced manufacturing over the next five years.
A research agreement was signed by Swinburne’s Deputy ViceChancellor (Research and Enterprise) Professor Bronwyn Fox and Peter Sutton, Managing Director of Sutton Tools, on 26 April. The new centre will play a key role in training students, staff and industry end users and will pursue joint R&D activities through different funding bodies. The centre will also play a role in the Australian Government’s Modern Manufacturing Strategy through developing a digital and sustainable local supply chain with Sutton Tools. Features of the collaboration will include: • The loan of equipment from Swinburne to Sutton Tools. • The joint funding of three PhD scholarships as part of our industry and impact PhD program. • The placement of undergraduate/postgrad students with Sutton Tools via Swinburne’s Work Integrated
Learning program. Professor Fox commented “This partnership builds on a longstanding relationship between Swinburne and Sutton Tools that dates back to the early 1990s and underscores Swinburne’s research strengths in the manufacturing sector. In recent times this relationship has been advanced significantly by Professor Suresh Palanisamy.”
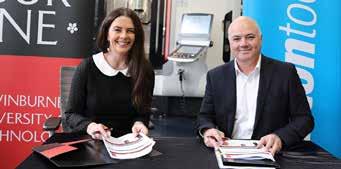
The agreement was signed by Swinburne’s Deputy Vice-Chancellor (Research and Enterprise) Professor Bronwyn Fox and Peter Sutton, Managing Director of Sutton Tools, on 26 April. Peter Sutton added: “Sutton Tools and Swinburne’s strengthening collaboration will be instrumental in the continued local development and manufacture of advanced engineering cutting tools. We see the Smart Manufacturing Centre as not only crucial in supporting R&D, but as importantly, providing the infrastructure to train both current and future engineers in systems and techniques required by increasingly demanding machining applications.” The new centre will be based at Sutton Tools’ plant in Thomastown.
AMTIL announces AMW speaker program themes
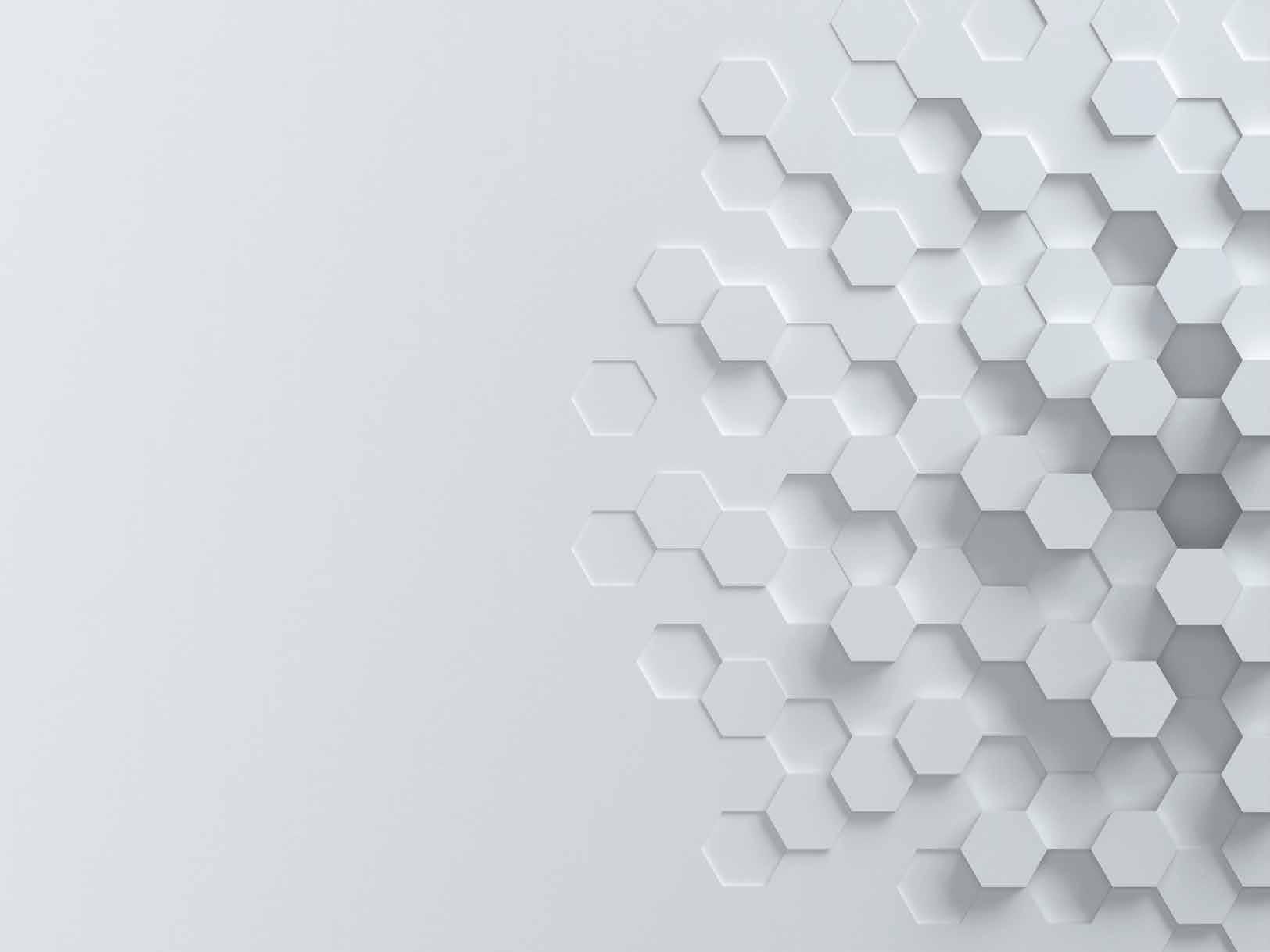
AMTIL has unveiled details of the themes that will be explored in the Future Solutions Stage speaker program during the Australian Manufacturing Week (AMW) exhibition in Melbourne next March.
In addition to the country’s biggest manufacturing industry expo, AMW 2022 will feature several complementary parallel events. Situated in the middle of the AMW exhibition, the Future Solutions Stage will feature a series of speakers sharing knowledge, expertise and insights, exploring a specific theme for each of the four days of AMW. They are: • Tuesday 8 March: Women in Manufacturing • Wednesday 9 March: Unlimit3D – Unlocking Additive
Technology Opportunities • Thursday 10 March: Research & Innovation • Friday 11 March: A Celebration of Australian
Manufacturing The first day of AMW will coincide with International Women’s Day, so the show will begin with a day-long celebration of the contribution made by women to Australian manufacturing, with the Future Solutions Stage featuring an all-female line-up of speakers. The opening of AMW will also be preceded by a special Women in Manufacturing networking breakfast. “It’s a happy coincidence that next year’s show is opening on International Women’s Day, so the first day of the speaker program will reflect that,” says Kim Banks, AMW Exhibition Manager and Head of Events at AMTIL. “We’re working on a great program aimed at celebrating the achievements of women in this industry, and perhaps inspiring a next generation of younger women to consider manufacturing as a career.” For the second day, the Future Solutions Stage will be devoted to additive manufacturing, with Unlimit3D returning after its launch at AMTIL’s Austech exhibition in 2019. With generous support from the event’s major sponsor Amiga Engineering, Unlimit3D will next year take place right at the heart of the AMW exhition, open to all. “The first Unlimit3D was a big success two years ago, but as the event was separate the Austech exhibition, it felt kind of removed from the main event,” explains Banks. “For AMW 2022, we’ve decided to stage it at the Future Solutions Stage, so anyone visiting AMW can come along and learn about this technology. We think it’ll be a big hit.” Day three will look at Research & Innovation, with speakers from across industry, government and academia discussing ways manufacturers and researchers can collaborate more effectively to develop and commercialise Australian innovations. Finally, the last day will celebrate some of the great success stories coming out of Australian manufacturing today – with a focus on how the use of new technology is driving the industry forward. AMTIL is currently hard at work curating an exciting, inspiring program, and is inviting industry to contribute their ideas for speakers or subjects to cover. Suggestions should be sent to: events@amtil.com.au. “AMTIL’s motto is ‘Connect. Inform. Grow’, and having a compelling speaker program at events like these is a big part of that,” said Banks. “Keep an eye on the AMW website and our social media channels – there will be plenty of further announcements between now and March.”
www.australianmanufacturingweek.com.au
Survey finds Australian manufacturers gearing up for reshoring
One in two manufacturers to bring operations back to Australia within the next three years, according to a new survey.
The survey, released by PROS, found that 55% of Australian manufacturers intend to reshore their operations to Australia by 2023 following market volatility caused by the COVID-19 pandemic and international relations with neighbouring countries. The Australian Manufacturing Outlook survey revealed confidence in that the Australian economy is growing, with more companies signalling they intend to bring manufacturing operations back to Australia. Nearly one quarter (22%) of respondents have already reshored their operations, with nearly half of companies’ overall manufacturing capacity (48%) targeted to return to Australia by 2023. Western Australia, Northern Territory and South Australia are poised to lead the nation’s charge on reshoring over the next three years according to respondents, with a focus on creating local jobs and growing priority sectors such as lithium batteries, defence and space, and capitalising on their respective geographic advantages. The drive to reshore has been prompted by the need to future-proof critical supply chains in the face of market change and disruption, to minimise risk and protect jobs in key industries, coupled with Federal Government support through its Modern Manufacturing Strategy and strong consumer preference towards Australia producing more products. Three-quarters of those surveyed (78%) believe Australia possesses the technology, people and economic strength to support the creation of an agile manufacturing base, which would better protect and reinstate the local production of goods. However, Australian manufacturers are underprepared to compete in a digital economy, with 82% of survey respondents still in the planning process or yet to implement e-commerce channels to sell to domestic or international buyers. Only 9% also have market-aware, dynamic pricing strategies. “The economic recovery is well underway, but Australian manufacturers must equip themselves with e-commerce and dynamic pricing capabilities,” said Haley Glasgow, APAC Head of Strategic Consulting and Alliances at PROS. “Australia is incredibly well-placed to leverage smart technologies like artificial intelligence and digital selling channels to overcome the competition challenges from imports and online sources. But to reinvent themselves, investment must be made by the government, industry and companies themselves. “Accelerating the sales process with AI-powered insights can also deliver prescriptive guidance on product recommendations, identify cross-sell and up-sell opportunities and proactively mitigate churn risk. This investment can improve the buying experience, order accuracy and accelerate business growth as the economy recovers.” In support of strengthening self-reliance, nine in ten (90%) Australian manufacturer who responded to the survey were confident their company has access to a skilled Australian workforce capable of producing, marketing and selling its products through traditional and digital channels. The Australian Manufacturing Outlook survey was conducted by independent market research firm OnePoll in December 2020. The research sample consisted of 500 senior employees in the manufacturing sector across Australia.

Sentient Bionics bids to save one million lives with oxygen machine in a briefcase
Since March 2020, Melbourne-based company Sentient Bionics has been working on a philanthropic project to develop a portable oxygen machine, with the aim of saving one million lives.
When COVID-19 overwhelmed hospitals around the world, Sentient’s team of engineers, supervised and funded internally by CEO Dr Paul Boxer, realised that low and middle-income countries (LMICs), unlike developed countries, don’t have access to sufficient effective oxygen resources. Because of the COVID-19 crisis, the World Health Organization (WHO) estimates that 32 million people will require oxygen therapy. Sentient is a registered charity whose vision is to create a device with social benefit, with a passionate team of engineers behind it. Aaron Duivenvoorden, lead engineer of the project, explains: “We are a small team providing a necessity that will make a big difference and have a lasting impact in the world and people’s lives!” Sentient’s project has resulted in Sentox, a low-cost oxygen machine compact enough to fit inside a briefcase. SentOx is rugged, hand-portable and designed to WHO specs, which makes it ideal for countries which have scarce medical equipment. Since the beginning, Sentient’s project has evolved a lot: the design has been validated and local production has started. Units have been sent to South Africa and Indonesia, where potential manufacturering partners are examining the device. Last month, the team applied for a Modern Manufacturing Initiative (MMI) grant, which would allow them to scale up massively and make a difference rapidly. In addition to local production, Sentient’s team hopes to be able to develop SentOx directly in the countries who need them most (Indonesia, South Africa, Ethiopia and Papua New Guinea amongst others) to create a distribution network. Sentient is calling for potential partners offering manufacturing services which have ISO 13485 certification as well as medical device experience. The company is also looking for people experienced with PCB assembly, extruded aluminium, medical products and gas separation. www.sentientoxygen.net
SA manufacturing given boost with opening of Auto Innovation Centre
The Australian Automotive Aftermarket Association (AAAA) has announced the official opening of its new Auto Innovation Centre (AIC) in Adelaide. The cutting-edge facility offers new technology and services to fast-track product development for the South Australian manufacturing industry.
Held on 29 April in Edinburgh, the AIC opening Director Luke Truskinger, and the AIC team saw nearly 100 industry representatives, have worked wonders to activate these sponsors, dignitaries, and media come services in the market.” together to join this historic industry moment For Truskinger, opening the South Australian in a new ‘Centre of Excellence’. Underscoring facility is another exciting opportunity to the significance of the event for South further serve the aftermarket. “We can’t Australia and Australian manufacturing, wait to start utilising our unique technology, Senator Rex Patrick was the guest of honour, equipment and know-how to improve who symbolically cut the ribbon to declare development capabilities of our diverse and the industry leading facility open for business. exciting automotive aftermarket businesses Patrick was joined by Jon Gee MP, State Member for Taylor; AIC Managing Director Luke Truskinger, and Stuart Charity, CEO of Senator Rex Patrick cut the ribbon to declare the Auto Innovation Centre (AIC) open, with Stuart Charity, CEO of the AAAA (left), and AIC Managing Director Luke Truskinger. here in S.A, nationally and beyond. Our core purpose is business support, so we welcome enquiries on how the centre can directly assist the AAAA. with any bespoke business requirements.” “We are proud to launch this facility in Adelaide, a location that The AIC offers state-of-the-art robotic equipment to deliver boasts a great number of innovative aftermarket companies,” said premium vehicle testing services, including Sine-with-Dwell testing Charity. “This facility, in addition to the Melbourne AIC centre, is the (ADR88/89) to validate ESC performance, and brake performance culmination of eight years of passion and hard work, and opens testing (ADR31/35). Product level testing includes vibration testing, up new product development opportunities for businesses, while hydraulic durability, tensile testing and a shock dyno, while additive playing a role in supporting the health of this great industry. manufacturing capability offers further product development “Bringing these centres to life has been an incredible effort. I opportunities. The AIC offers a database of premium-quality vehicle would like to thank the Federal Government’s commitment to scan data, thanks to high-tech scanning and processing equipment. manufacturing, and investment in these incredible facilities, as The cutting-edge workshop is available for hire for company use, well as Senator Rex Patrick’s unwavering support. The vision of ADAS calibration, as well as for automotive training and education the AAAA and AIC Boards, and our hugely supportive Champion activities. www.autoic.com.au companies was crucial. Finally, our passionate AIC Managing

Headland Machinery achieves ISO accreditations
Headland Machinery has announced that it has recently received ISO certification in three key areas.
The accreditation were in the following categories: • ISO 9001-2015 Quality Management (QMS) • ISO 14001-2015 Environmental Management • ISO 45001-2018 Occupational Health & Safety
Management The project to secure the certifications was led by Headland Project Manager Karthik Anantha and Managing Director Richard Kloe, with Financial Controller Nick Bedson acting as project sponsor. Anantha explained that upon receiving the news, he was very pleased to obtain accreditation quickly, but not surprised. “I’m very happy that Headland has achieved ISO accreditation so quickly,” he explained. “From a quality perspective Headland had always followed best practices. During the audit stages, the auditor mentioned a few times that Headland’s quality was already at an ISO standard by looking at past records. Since the majority of our process and procedures are in accordance with ISO, we achieved ISO in a short amount of time.” The accreditations mean clients can be assured Headland is following international best practice in delivering quality products and services. Accreditation guarantees a commitment to continual improvement and positive client experiences. Under ISO 9001 (Quality), Headland has achieved international recognition of its quality management systems and processes. It attests that Headland responds to clients’ needs quickly, identifying problems and providing solutions faster. The ISO 14001 (Environmental) certification demonstrates that Headland is committed to continually improving its environmental standards, following compliance guidelines and how it operates. Headland is committed to minimising its impact on the environment, and is conscious of how its actions impact the environment. Finally, ISO 45001 (OH&S) certifies that the safety of staff, clients and suppliers is paramount in what Headland does. International audit of its practices and processes provides best practice guidelines to ensure it minimises workplace injury and illness, that its safety systems are efficient, and that it maintains the highest standards possible. George Yammouni, CEO of Headland, said: “We are committed to continual improvement, and achieving ISO accreditation ensures we benchmark ourselves against best practice. Not once, but regularly and continuously. We are dedicated to striving for positive client experiences whilst always being focused on quality, the environment and occupational health & safety”.
Victoria unveils plans for Fishermans Bend innovation precinct
The Victorian State Government has announced measures to place the state at the forefront of global innovation in advanced manufacturing, engineering and design, with the announcement of investment in a major new innovation precinct close to Melbourne CBD.
Premier Daniel Andrews’ Government will invest $179.4m to support stage one of the Fishermans Bend Innovation Precinct development at the former General Motors Holden factory, just 4km from Melbourne city centre. The precinct will encourage collaboration between industry and academia, with the University of Melbourne leading the way. Fishermans Bend will house the University of Melbourne’s School of Engineering from 2024 and the innovation precinct is forecast to be capable of supporting up to 30,000 STEM jobs by 2051. The precinct is intended to cement Victoria’s status as a major centre for advanced manufacturing and support high-paid innovation jobs in defence, aerospace, clean energy and transport. It will also strengthen the state’s capacity to commercialise new ideas and foster new business ventures. GM Holden established its Fishermans Bend operations in the 1930s, first to assemble imported engines and locally produced car bodies. In the late 1940s, the site delivered Australia’s first massproduced vehicle – the FX Holden – and GM Holden’s operations expanded, while fellow carmakers also set up factories in the area. Development Victoria bought the former GM Holden site in 2017 and is leading the project to remake the historic precinct. “The old Holden factory is part of Victoria’s manufacturing history,” said Martin Pakula, Victorian State Minister for Business Precincts. “This important first step will help transform it into Victoria’s manufacturing future. We’re creating the foundations for a worldleading hub for ideas, innovation and 21st century industry – it’s an investment in jobs and the people of Victoria.” This first step will involve remediation of the 32-hectare GM Holden site – an area equal to 15 Melbourne Cricket Grounds – and the installation of crucial infrastructure and services to make an investment-ready precinct. As many as 300 people will work on the innovation precinct project at any one time, with close to 700 indirect jobs also supported. Stage one is expected to unlock developable land capable of supporting 2,000 jobs by 2024. The innovation precinct is at the heart of the 230-hectare Fishermans Bend Employment Precinct, recognised as a strategically important employment and innovation cluster, which is already home to worldrenowned firms including Boeing and Siemens. Fishermans Bend is Australia’s largest urban renewal project, covering around 480 hectares that will be home to around 80,000 people and 80,000 jobs by 2050.
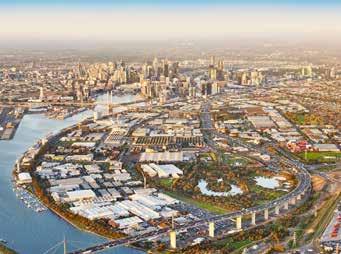
Grants for Victorian manufacturers to support competitiveness, jobs
Victorian manufacturers can now apply for grants of up to $500,000 to support and expand their operations, under a $20m drive by the State Government to boost competitiveness and drive new jobs.
The Business Competitiveness Program is a key plank of Premier Daniel Andrews’ Government’s $60m Manufacturing and Industry Development Fund, launched on 27 April by the State Minister for Industry Support and Recovery, Martin Pakula, who urged businesses that are eligible to apply. “Victoria is the manufacturing state. At the core of our strength are businesses that continually innovate and lead the way in their industries,” said Pakula. “We’re backing businesses to keep ahead of the pack because we know that it means more jobs for Victorians and an even stronger future for the sector.” The Business Competitiveness Program will help eligible Victorian manufacturers implement new manufacturing technologies and processes. Grants will cover up to one-third of eligible project costs. The program will help to secure Victoria’s sovereign manufacturing capability by improving productivity, creating sustainable local jobs, increasing industry competitiveness and strengthening local supply chains in key sectors including medtech and food manufacturing. Grants can go towards the purchase and commissioning of capital equipment, manufacturing product and process improvements and supply chain capability development. Another initiative under the Manufacturing and Industry Development Fund will open in coming months, providing grant support to growing businesses for projects that help them capitalise on new opportunities. The Fund is expected to create hundreds of new jobs, with funding spread over three years to boost the capabilities of Victorian businesses so they can expand and generate ongoing job growth.
For more information about the Business Competitiveness Program and to apply for a grant, go to: www.business.vic.gov.au/midf
Renewed support for Australian automotive R&D
The Federal Government has extended the automotive research & development tariff concession until 2025, keeping high-end research activities in Australia and supporting high-wage jobs.
Minister for Industry, Science and Technology, Christian Porter, said vehicle research & development is vital to the nation’s prosperity with Australia being a significant competitor on the global stage. “By extending the automotive research and development tariff concession, the Morrison Government is supporting the ongoing design and development of cars here at home, and providing ongoing job opportunities for our highly-skilled workforce,” Minister Porter said. “We’re supporting highly-skilled Australians such as engineers, designers, technical, automotive and other specialists to remain in these important jobs. It’s also evidence that while automotive manufacturing in Australia has changed over the past 10-15 years, we still have a healthy sector with well-paid jobs right along the value chain.”
Ford Australia, which employs more than 2,500 staff, is a key beneficiary of the tariff concession, along with Toyota Motor Corporation Australia and Robert Bosch Australia. The tariff concession is demand-driven and was worth more than $4m on goods imported from 35 countries in 2018 and 2019. This extension capitalises on the Government’s investment in the automotive sector with programs such as the Automotive Transformation Scheme. “Extending the tariff concessions will also strengthen Australia’s engineering and design capability, which will have flow-on benefits to many other parts of the economy, including manufacturing,” Minister Porter said. “By retaining the tariff concession we’re also cutting red tape and reducing the administrative burden for businesses, making it easier for them to remain competitive and contribute to Australia’s economic recovery.” NT Government announces partnership with AMGC to promote advanced manufacturing
The Northern Territory (NT) Government has announced a new partnership aimed at accelerating innovation opportunities for manufacturers.
The Territory Government will invest $8.75m over five years with the Federal Government’s Advanced Manufacturing Growth Centre (AMGC) that will fast-track innovation projects and generate millions of dollars in co-investment. AMGC has connections with manufacturers, universities, research institutions and export hubs around the country, and co-funds industry projects to lead to commercialisation, with a goal of driving innovation, productivity and competitiveness across Australia’s manufacturing industry. Announcing the new partnership, NT Chief Minister Michael Gunner said: “We are backing innovation and local business, because we know how exciting this space is for the Territory and for our economic comeback. We want to make things in the Territory, lock in more local projects and get them off the ground. “This will lead to more jobs for Territorians, and higher paying ones at that. This announcement is Kickstarter on steroids – and it will turn Territorians’ ideas into reality.” The new partnership will fast-track research, pilot projects and commercialisation of advanced manufacturing opportunities in minerals processing, agribusiness and carbon across the Territory. Successful applicants through the partnership will be required to match funding dollar-for-dollar. This partnership will see: • A permanent AMGC Territory Director appointed to build connections between local manufacturers and interstate research institutions and accelerate new opportunities. • AMGC establish an office in Darwin, which will house the dedicated Territory-based Director who will be supported by
AMGC’s existing national team. • A competitive co-funded grant program for industry stakeholders which will be managed by AMGC. “The Northern Territory sits at the intersection of innovation and opportunity,” said Dr Jens Goennemann, Managing Director of AMGC. “AMGC believes that by leveraging the Territory’s rich natural resources and convenient access to international markets, the Top End has the opportunity to create smart jobs for Territorians and spur a new era of innovation and prosperity
for the region. “AMGC in partnership with the Gunner Government is committed to helping transform the Territory’s economy from being a lucky economy to a smart one, underpinned by smart companies manufacturing smart products and services with global relevance.” Over the past three years, AMGC has facilitated more than 340 national collaborations and co-funded over 80 industry projects, while creating more than 2,300 jobs across the country. It has invested over $66.8m of combined industry and Government funds into manufacturing projects, resulting in an estimated $1.2bn in additional national revenue. The latest announcement delivers on the recommendations of the Territory Economic Reconstruction’s final report. It will accelerate the creation of advanced manufacturing businesses, which will create more jobs for Territorians and bolster the local economy with new investment opportunities. Goennemann added: “Through encouraging collaboration, greater engagement with research institutions, and focusing on being better, not cheaper, Northern Territory-based manufacturers have a significant opportunity ahead of them and AMGC is here to drive that change.”