
6 minute read
HMS Group – Driven by safety and efficiency
from AMT JUN/JUL 2021
by AMTIL
Headquartered in Thornton, NSW, HMS Group has developed a thriving line of business in the manufacture of autonomous safety equipment for the mining industry.
The first thing you notice when meeting Jamie Howard, Group Managing Director of HMS Group, is his unwavering commitment to Australian manufacturing and his belief in huge opportunities for local industry. With a trade and engineering background and a passion for safety, innovation and training, it quickly becomes apparent how Howard’s philosophy has made HMS Group a success. He describes HMS Group as a proudly Australian company operating in a zero-harm environment, designing and manufacturing safety solutions, while driven by innovative productivity and skills education. “We are about workplace safety,” says Howard. “Manual labour is hard work and it limits the productive life of people. If an autonomous machine like ours can save wear and tear on the human body, that is a great benefit.” The HMS Mini Loader
Howard saw a need for a safe solution to removing coal from under conveyors. Previously, removal of spilled coal was a dangerous operation, involving up to five people to shovel coal from underneath the conveyor belt. While undertaking this dangerous operation, the belt had to be stopped, which was an extremely expensive process. The solution from HMS Group was the design and manufacture of the remote-controlled HMS 200 Mini Loader. With a height of only 600mm, the Mini Loader is able to reach any dangerous or inaccessible area where material needs to be removed with safety. “Our remote-control technology was developed and is manufactured by our company Hetronic Australasia,” says Howard. “We have a large customer base in Australia, including one of the major electricity utilities. Hetronic supplies mining companies, construction cranes, agricultural machinery, concrete pumps and other equipment that benefits from the safety provided by remotecontrol technology. “Within our electronic group we have thousands of remote-control units in the market, many being used by major global equipment brands. We currently export our remote-control Mini Loaders and equipment to China, Brazil, South Africa, just to name a few.” The company’s technology has won New South Wales mining awards, the Hunter region manufacturing awards, and export awards. In 2019 HMS Group received the Endeavour Award for the Australian safety solution of the year. Evidence of HMS Group’s dedication to Australian manufacturing can be clearly seen in the country’s factory in Thornton, the walls of which are adorned by Australian flags. “Every product we make is proudly badged as Australian made,” says Howard. “For any manufacturer to be competitive in today’s global market, it is essential that you invest in the latest machinery and technology. It is this approach that has been the cornerstone of our success and we are always on the lookout for ways to make our manufacturing processes safer and more efficient.” Blending tradition and innovation
The company recognises the importance of embracing the latest technology, but it also places a great emphasis on the need to blend the knowledge and practical experience of the past while transitioning to new methods. “We have invested heavily in making our manufacturing more efficient and finding new technologies to make jobs all easier,” says Howard. “We are producing an innovative product but need to find smarter ways to reduce costs as well as speeding up our operations. “We need machinery that enables us to make immediate changes. It is important to be self-reliant and not have to wait on suppliers, whether it is one week or month. Our new machinery enables us to perform design changes for manufacture immediately and this is a huge benefit to the way we operate.” One of HMS Group’s most recent acquisitions is a Baykal APHS31160 hydraulic CNC press brake, with a Delem DA69T touch screen control. The machine has programmable X, Y1, Y2, V, Z1, Z2 and R-Axis, CNC table crowning, and a laser guarding system.
Jamie Howard, Group Managing Director of HMS Group, with the company’s Baykal APHS-31160 hydraulic CNC press brake.
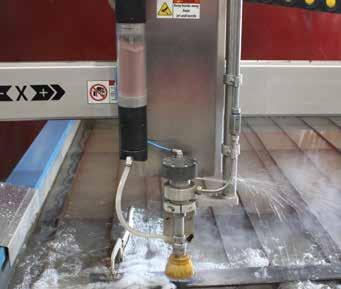
Cutting steel with HMS Group’s Jekran X-MW waterjet.
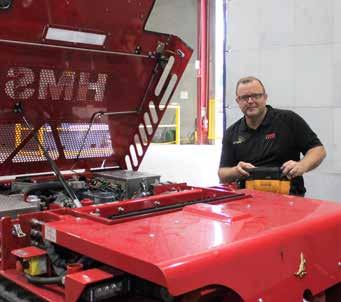
Jamie Howard with an HMS-200 Mini Loader.
“The touch screen control enables us to program the whole process without actually putting the metal into the machine,” explains Howard. “It also enables us to make changes on the screen and shows you each stage exactly as it occurs and there is no wastage. Another recent addition to the HMS Group workshop has been a Jekran X-MW series waterjet cutter. “That delivers our need for thick metal cutting of 25 to 50mm thickness,” Howard adds. “The accuracy of the waterjet machine is absolutely amazing in terms of accuracy and versatility. The Jekran can cut up to 100mm-thick steel, plastics, glass, stone, wood or virtually any material with great accuracy.” Training the next generation
“We need to bring back manufacturing know-how and technology that has been lost in the past,” says Howard. “I come from a trade background; I worked in company where every year there were 15 apprentice fitters,15 boilermaker apprentices, five electricians and four engineering professionals. “There is a need to return to the days when apprentices and people learning on the job were mentored by experienced people who could pass on a huge amount of knowledge that contributes to manufacturing efficiency,” Howard concludes.
www.machineryhouse.com.au www.hms-group.com.au
For progressive engineers, fabricators and metal workers to manage your core business, your labour
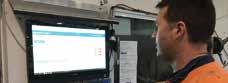
Touch Screens on the Workshop Floor – Tracking: Jobs, Tasks and Workshop Staff in Real Time
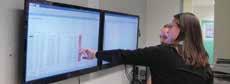
50 inch TV Monitors on Office Walls and Workshop Floor Walls – Report: Jobs, Tasks, Staff, Times, Job Status, ... in Real Time
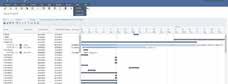
Scheduling is Updated Automatically in Real Time at Job Change
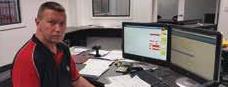
Essential Tool for Production Management to Drive Weekly Production •Software App developed for engineers producing custom one off products or projects, 6 to 200+ workshop staff •Empower Software is simply an App. Cloud & Web based •Empower can interface to any accounting or ERP software •Pricing Low Cost Subscription eg 10 workshop staff is $108 per week •If you use manual time sheets, to record workshop staff times on their jobs 10 workshop staff for example will cost you $775 per week = $37,975 per year, in lost chargeable staff time to fill in daily and admin cost daily to rekey to produce. If you replace your manual time sheet system with Empower then you will save $667 per week saving you $32,683 per year. •Supplying Australian engineers for 13 years •Available to you on request: info pack and free trial software •Engineering Client Short Videos on youtube.com. In Youtube search: Empower MARs Transport, Empower Peppertree ... •90% of engineers using tablets on the workshop floor and the
Empower Software App achieve a 20% to 40%+ reduction in time on jobs – therefore a 20% to 40%+ reduction in labour cost on jobs. •An Engineer with 10 workshop staff is projected to increase production by 80 hours per week, therefore increase revenue by $6,000 per week and (80 hours by $75 per hour overhead cost), therefore increase revenue by $294,000 per year. This $294,000 per year is largely additional profit because overhead costs have been incured in existing production. Your 10 year investment $2.94m additional revenue, largely additional profit.
Sean O’Sullivan B Com (Hons) Otago University
Founding Director, Empower Software
sean@manufacturingandengineering.co.nz +64 27 2284211