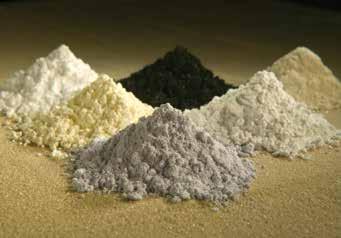
7 minute read
Rare earths becoming less “rare” in Australia
from AMT JUN/JUL 2021
by AMTIL
Rare earths – Becoming less ‘rare’ for Australia
Around the world, Australian rare earth miners are striking major business deals: in the US, Lynas Corporation has won funding to build a processing plant in Texas; Hastings Technology Metals has reached an agreement with German conglomerate Thyssenkrupp for the supply of high-grade rare earths; and Australian Strategic Materials (ASM) has successfully tested its rare earth powders for KIRAM in South Korea; to name but a few. So what, asks Gabriele Richter, is going on?
Rare earth elements are a collection of 17 soft heavy metals that are indispensable to a growing array of advanced technologies ranging from smartphones to electric vehicles (EVs) to military weapon systems. Despite their name, rare earths are relatively widespread in the Earth’s crust. Their “rarity” is due to their low concentrations, which makes them difficult to extract. China contains approximately 35% of the rare earth deposits in the world, but over 95% of the world’s production. In 1992, China’s then-leader Deng Xiaoping remarked: “The Middle East has oil, China has rare earth” Because China prioritises not just extraction, but separating and processing into usable elements, its monopoly is forecast to last for a few more years. Exercising this much control puts it in powerful position. The Chinese monopoly is why manufacturers globally are actively seeking non-Chinese supply. As noted by Ursula von der Leyen, EU President of the European Commission: “Green and digital technologies currently depend on a number of scarce raw materials. We import lithium for electric cars, platinum to produce clean hydrogen, silicon metal for solar panels. 98% of the rare earth elements we need come from a single supplier – China – and this is not sustainable.” Building a single F-35A fighter jet, for example, requires at least 420 kg of rare earths, which come primarily from China (indeed, there are reports that China is considering using rare earth export restrictions to undermine the US defence industry). China’s Northern Rare Earths, the world’s leading supplier, is expected to double production within three years as smaller Chinese producers also accelerate. China took over the title of largest producer from the US in the 1990s. It was noted by MetalMiner’s Stuart Burns that: “The US sends its ores to China for refining. That’s not because it doesn’t have the technical know-how; the US simply lacks the facilities.” Rare earths, tungsten and lithium were among 35 minerals deemed “essential” to US economic and national security by the Trump administration, and the new Biden presidency has continued this focus on removing China from the country’s manufacturing supply chains – signing agreements with Australia and Canada in 2018 and 2020 respectively to secure the supply of rare earths. Additionally the US recently provided $US60m in funding for Australian rare earths miner Lynas to build a plant in Texas. Lynas has positioned itself to become the Western world’s largest supplier of rare earths to the US military. The US funding is a sign of how anxious the US and other Western nations are to break China’s dominance. Lynas is the only rare earth producer outside China, and it has overcome significant challenges to establish itself in this way. It sends rare earth concentrates from its mine site in Western Australia to Malaysia for processing into saleable rare earth oxide products. But this has not been without disruption, amid the Malaysian government’s concerns about the low-level radioactive waste generated. Meanwhile, Germany’s Thyssenkrupp Materials Trading has signed a binding off-take agreement with WA-based Hastings Technology Metals for the supply of high-grade mixed rare earth carbonate, in a big boost to Hastings’ hopes of starting its proposed $449m Yangibana Rare Earths Project in WA. The timing coincides with a strong increase in demand for rare earths driven by the EV revolution.
Grasping the opportunity for Australia
Merely possessing deposits of rare earths is no guarantee of being able to exploit them. The mining and extraction processes are capital-intensive, consume large amounts of energy, and release toxic by-products. Large amounts of capital will be needed to set up facilities to compete with, and supply to, the world. It is for this reason that Prime Minister Scott Morrison mentioned critical minerals during his address to the National Press Club on 1 February, as part of $1.5bn in new funding for the Federal Government’s Modern Manufacturing Strategy. In March, the Resources Technology and Critical Minerals Processing National Manufacturing Priority road map was made available to create more processing capacity. This roadmap aims to strengthen Australia in becoming a global centre for commercialising and manufacturing resources technologies and establishing a critical minerals processing industry. The moves are part of a broader push to make Australia one of the developed world’s vital suppliers of rare earths. This is a growth opportunity for Australia, with its abundant untapped domestic deposits, existing infrastructure, stable regulatory framework, and globally recognised expertise in developing and operating complex mines. To state some examples: WA’s Iluka Resources is negotiating with overseas governments seeking non-Chinese supply as it plans to become the only fully integrated supplier in Australia. And Australian producer ASM – building its first processing plant – recently strengthened its supply chain by closing a deal with two regional governments in South Korea , in what was considered a snub to China. Australian companies such as Lynas and Iluka are already shipping many resources offshore – including to the US, which is rapidly developing its own capacity with Australian support. But the Federal Government is now eager to drive what many in the industry have been demanding for decades: to add more value to the materials mined in Australia. The next wave towards high-tech manufacturing increasingly involves rare earths. Australia is positioning itself not to miss the opportunity.
www.lynasrareearths.com www.hastingstechmetals.com www.asm-au.com
ANSTO – New tech to cut environmental impact of mining
The Australian Nuclear Science & Technology Organisation (ANSTO) has developed a new, cutting edge technology that may minimise the effects of mining by making it more efficient.
Using ‘Dingo’, one of the highest-intensity neutron imaging machines in the world, ANSTO scientists have figured out how to greatly reduce the time needed to measure the exact mineral content of core samples. Senior Instrument Scientist at ANSTO’s Australian Centre for Neutron Scattering Dr Joseph Bevitt developed the technology, which has the potential to significantly change the way minerals are explored around the world. “At the moment, many drill core samples are X-rayed for surface mineral content, which is essentially a guesstimate,” says Bevitt. “While some drill cores are fully 3D-imaged with X-rays, many cannot be studied in this way because X-rays do not have sufficient penetrating power. Our neutron-imaging technology creates a full 3D map of the core, delivering the total mineral content for metalrich and dense ores.” The procedure is non-destructive and as quick as traditional X-rays, meaning the search for valuable minerals and their processing can be carried out in a more targeted manner, resulting in reduced environmental impacts of mining. “If you take gold for example, current X-ray technology is limited as to what it can reveal, especially when more abundant heavy metals such as lead are present in the ore as these prevent 3D X-ray imaging,” Bevitt explains. “Our 3D neutron tomography measures the exact gold content of a mining core, with neutrons able to image through lead, iron and other abundant metals, allowing parties to know the exact size of the lode underground through core samples without breaking earth.” An upcoming upgrade to ANSTO’s 3D neutron imaging facility will also ensure simultaneous 3D neutron and X-ray imaging is achievable, enabling even more accurate mineral identification and quantification. “This technology is revolutionary and a first for Australia,” says Bevitt. 3D neutron tomography also has enormous benefits across numerous academic fields including environmental science, palaeontology, engineering, and cultural heritage. Speeding the method up opens the possibility for more, and deeper, research opportunities. “By examining fossils, for example, we can learn how animals and plants evolved to thrive through changing environmental conditions,” says Bevitt. “This research is essential as we seek solutions to the problems caused by climate change. The device also can look for material imperfections down to a tenth of a human hair without damaging a sample. This is an integral part of ensuring the safety of materials being used for space and ocean exploration.”
www.ansto.gov.au
WHAT’S IMPORTANT TO YOU
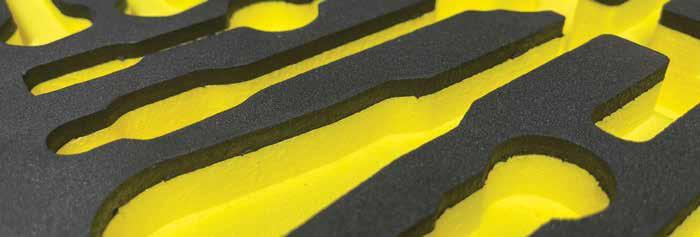
DESERVES A CUSTOM-MADE FOAM SOLUTION
Protect your valuable products from damage in transit with our range of foam packaging solutions. From anti-static carton foamcasing to case inserts protecting cameras, medical equipment, musical instruments or your tools, we cater to many diff erent needs. Call us today to discuss your options; (02) 974 269 00
ADFOAM INDUSTRIES PTY LTD 9 Ford Street, Greenacre, NSW 2190 Phone: (02) 974 269 00 Email: sales@adfoam.com.au ADFOAM.COM.AU
• anti-static foam packaging • case inserts • die-cut foam solutions • promotional signs and shapes