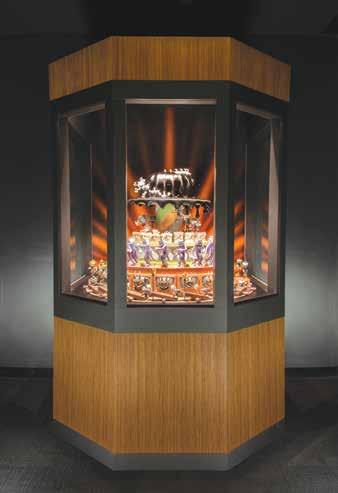
7 minute read
ADDITIVE MANUFACTURING
from AMT JUN/JUL 2021
by AMTIL
Additive Manufacturing Hub case study: Megafun
Commisioned to created an innovative animated zoetrope exhibit for the Australian Centre for the Moving Image in Melbourne, Megafun made use of 3D printing to overcome the challenges the project presented, working with GoProto via the Additive Manufacturing Hub (AM Hub) at AMTIL.
Based in Melbourne, Megafun is a designer and project manager of exhibitions and theatre works with more than 23 years of experience in providing creative and technical services to companies, artists and exhibitions around the world. The company specialises in delivering quality theatre and events and creating intriguing and engaging interactive experiences. Megafun was engaged to develop, construct and install a new 3D animated zoetrope in ACMI’s permanent exhibition space. For this new zoetrope, Canadian video game company Studio MDHR was approached to provide the characters and storyline from its Cuphead series of games. While the historical zoetrope concept was a slitted drum, this new variation is a 3D animation. A disc spinning at a set speed is illuminated with flashing strobe lighting. Each flash illuminates a slightly new position of the disc as it turns. By aligning objects and characters at just the right spacing with slight adjustments of position, these elements will appear to move – exactly like filmed animation, only in three dimensions. Design
The Cuphead range of characters from Studio MDHR existed only in a two-dimensional form, and it required a skilled 3D artist to develop three-dimensional versions of these characters that could exist in a dimensional world. This work was undertaken by video games artist John Aitchison, who laboriously recreated every nuance of each character. This wasn’t easy, as some of the characters defied physics in their 2D form, so they had to be adapted and adjusted in order to make the transition. The Cuphead characters were created in a 1940s/50s drawing style and incorporate “stretch and squash” characteristics; they also feature elements that are quite fine. These features made the 3D modelling process more complex, and certain features needed to be adjusted to allow for the limitations of the printing process. For example, very fine limbs with large hands can be particularly difficult in the world of 3D models, especially when spinning at 60rpm. Studio MDHR developed the animation storyboard and created a series of images of both the individual characters as well as an overview of the collective characters in the animation, which were passed to John, the 3D artist. He then worked closely with the creators over a period of months to turn the characters into models based on the material provided, the limitations of the modelling/3D process, and in response to feedback from Studio MDHR. Once the individual characters were approved, he laid them out according to the storyboard, taking support structures into account for when the digital version would become physical. Posts of stainless steel 4mm in diameter were used to support the characters, so they had to be designed and modelled to allow for this, with suitable holes into which the post could fit. Once complete, a digital 3D animation of the final zoetrope was created for review and adjustment prior to rendering each character as an individual file. The disc that supports the zoetrope animation was constructed of a high quality aluminium plate. This plate is pressed and then ground perfectly flat to avoid any noticeable movement, then mounted on a quality bearing, and spun with a motor capable of precise speeds and fine control. The plate included a series of pre-drilled holes designed to take the posts that supported the characters. These holes needed to be extremely accurate and could not be placed until the digital animation was complete and signed off.
Megafun developed a 3D animated zoetrope at the Australian Centre for the Moving Image in Melbourne, based on the Cuphead video game series.
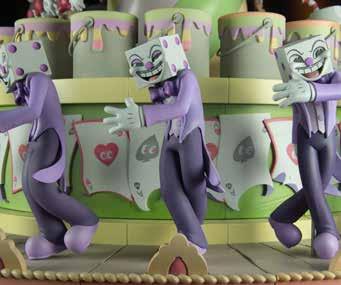
“Initially it was intended to 3D print the supporting understructure; however this proved to be far too costly,” explains Keith Tucker, Director of Megafun. “We did however need it to be highly accurate. The result was to create it with a CNC router using high-density fibreboard in numerous layers. We needed to cut away the interiors to keep the weight down, but it proved to be over 800% cheaper than the 3D option.”
The models that would feature in the zoetrope were produced using a full colour 3D printing technique. Keith Tucker, Director of Megafun.
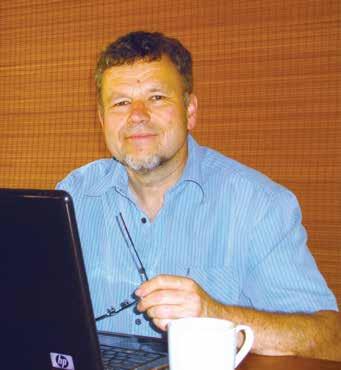
Printing 3D models
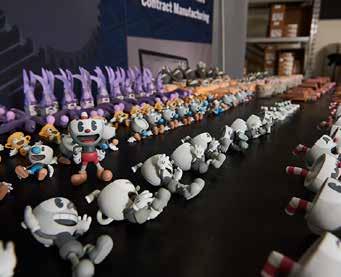
Of course, the digital models needed to be turned into physical models, which was undertaken using a full colour 3D printing technique. In taking this approach, Megafun sought support from AMTIL’s AM Hub through its Build It Better (BIB) voucher programme. “One of the reasons these types of zoetropes are now achievable is 3D printing,” Tucker explains. “Before this technology it would have been very difficult to create characters with the highly accurate small movements of limbs and facial expressions that 3D printing allows. “Printing techniques have developed considerably over time, and we elected to use a full colour nylon print that resulted in robust and lightweight characters. This process has the advantage of being much more robust, lighter and able to support much finer features.” Megafun used GoProto as the print house, which received the models from the artist and reviewed them for efficacy and structure. Various adjustments were made during this process to address some vertex errors and internal structures. “We faced a number of significant budget pressures due to the size and shape of the models being difficult to fit into the print bin in large numbers,” says Tucker. “We were able to address some of the cost issues by printing some characters in parts – legs, arms and torsos – allowing a tighter fit in the print bin. However we were hampered by the colour rendering restraints where models had to sit in the same orientation in order to ensure an accurate colour match.” Colour ended up being another significant issue, as the printed colours were often considerably different to the digital colours. Megafun had to make many adjustments and undertake numerous test prints before the rendering was suitable. Black proved particularly difficult as the darkest black would always only print in grey, meaning some compromises in the final rendering were unavoidable. Once printed, the models needed to be prepared by cleaning, sandblasting and sealing with clear lacquer. This was timeconsuming work as it is done by hand. The overall print process proved to take a considerable time, further exacerbated by limitations stemming from the COVID-19 crisis. “We ended up being in the print phase for over six months, which was very challenging” recalls Tucker. “Were we to undertake this again we would need to have a process that could minimise this timescale.” Once printing was complete, the models were fitted to their support posts and mounted into the pre-drilled holes in the disc surface, ensuring correct orientation and character order. Finally, a drop of adhesive was used to ensure the models didn’t move when the disc is spinning.
Result
After extraordinary levels of detail and fine tuning, Megafun finally had the opportunity to fire up the finished piece – a moment that Tucker describes as “magical”. Characters that had previously been static now came to life. Locked into their respective frames they created a seamless fully dimensional animation. The exhibit was transported into ACMI where it was fitted into its joinery housing and accompanied by a composed soundtrack. “The reaction from staff and guests has been universally positive,” says Tucker. “The experience of seeing static models come to life is so unusual people are genuinely amazed. It is a truly powerful animation technique.” Megafun has a well established reputation for delivering highly technical interactive exhibits for major institutions, and this project has further enhanced its standing – a hugely positive outcome for the business. While there is not a lack of interest in the possibility of delivering similar projects to other organisations, the very high costs involved represent an ongoing obstacle. “If we were able to create this type of dimensional animation at a lower cost, I am confident we would be able to place work of this kind in numerous locations, where the content could effectively support the nature of the site,” says Tucker. “The current delivered price of around $200,000, however, makes it very difficult to compete with the more ubiquitous but considerably cheaper computer or videobased displays.” Megafun’s aim is to continue to pursue opportunities in this field and will investigate the options for reducing costs. In the 3D printing area in particular, the company intends to try to bring the delivered price down to a level where it starts to become competitive. “We take this opportunity to thank AMTIL and the AM Hub for their support and for the inclusion in the BIB voucher programme,” says Tucker. “Without this, we may not have successfully been able to deliver this project.” The AM Hub is an initiative delivered by AMTIL in partnership with the Victorian State Government to promote the adoption of additive manufacturing technology. For more information, please contact John Croft, AM Hub Manager, on 03 9800 3666 or email amhub@ amtil.com.au