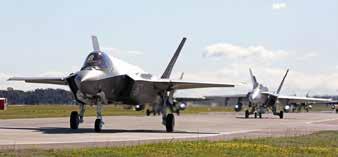
5 minute read
Laser AM tech for military aircraft repair
from AMT JUN/JUL 2021
by AMTIL
Using laser additive technologies in the repair of military aircraft
The increased precision of next-generation military requires new and innovative repair and sustainment solutions, as traditional repairs become more difficult or even impossible. Recently a collaboration between a group of Australian organisations has resulted in the development of laser additive repair, which is now being employed by RUAG Australia.
Military aircraft represent some of the most advanced engineering on the planet, with minimal weight design, precise machining and highly specialised materials all contributing to the high cost of new platforms and spare parts. The incredible price tag associated with maintaining such platforms is a major issue for Australia, where harsh sunlight and coastal corrosion accelerate the need for part replacements in addition to the rigors of service. Australia’s current reliance on legacy systems and overseas suppliers can also lead to aircraft being grounded until suitable replacements are found, presenting major costs in aircraft readiness and reliability. To address this critical problem, a collaborative project led by RUAG Australia and involving Swinburne University, DMTC, the Department of Defence (Defence Science and Technology Group) and the RMIT Centre for Additive Manufacturing is targeting new and innovative technologies for sovereign industrial repair of military aircraft. A key research area at RMIT is laser additive repair of aerospacegrade steels, in which a scanned laser beam is combined with metal powder delivery to successively build up multiple layers and replace damaged material. This is advantageous compared with traditional grind-out and weld repair methods, as not only is the original component geometry maintained, but thermal damage to surrounding areas is also limited due to the rapid heating/cooling of laser processing. While the concept of laser additive repair is simple, its successful implementation is very challenging, particularly for aircraft steels where the process must be optimised both to avoid defects such as porosity, and to control the thermal history during deposition. This temperature control is necessary to optimise the properties of the deposited steel by providing an in-situ heat treatment, since conventional bulk heat treatments risk relaxing service stresses in used parts, causing them to become warped and unusable. Further difficulty is presented by the different requirements of different steels, with changing melting temperatures, tempering ranges, and risks of embrittlement all needing to be considered for desirable performance. A wide number of aerospace steels have been investigated through this project, including AISI 4340, AISI 420SS, 15-5PH, Aermet 100, and 300M, which can reach incredible strengths up to 2,000 megapascals (MPa). Such strength is vital
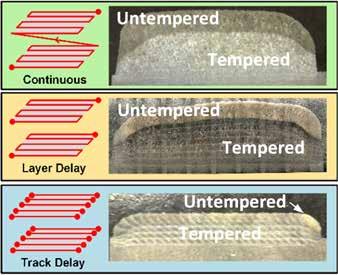
Image courtesy of CPL Brett Sherriff. © Commonwealth of Australia 2020.
Different deposition strategies alter the pattern of in-situ tempering (left), with sacrificial deposition layers used to remove brittle untempered regions in simulated repair specimens (right).
to landing gear components as they must withstand the shock of impact while also being subject to intense fatigue loading during take-off and landing as they carry the aircraft’s weight. The bulk of the deposition has been carried out on an industrialscale 3kW TRUMPF TruLaser Cell at the RMIT Centre for Additive Manufacturing, which makes use of a large working volume (1,500mm by 1,800mm by 750mm) and motorised focus optics for the rapid assessment of various processing parameters, material behaviour, and deposition strategies. Supported by Swinburne University, and the RMIT Microscopy and Microanalysis Facility (RMMF), the critical analysis of both microstructure and mechanical performance of simulated repairs has led to more than 25 publications since 2015 and over 500 citations. Most recently, a detailed examination of the repair of 300M has shown laser additive repair to provide significant improvement in tensile properties compared to traditional methods, with the fatigue performance of deep 40% repairs showing similar fatigue performance to light 10% grind-out repairs used for legacy aircraft. As such, laser additive repair is capable of restoring structural capacity and is not limited to cosmetic surface repair of worn geometries, with the final properties converging to that of the deposit as the repair depth is increased. This is limited by the capacity for in-situ tempering capacity of the steel grade, which for 300M is achieved by replicating the typical quench and temper cycles through additional cooling times between tracks and layers. While the peak temperature during deposition may lead to a slight softening of the deposit, the overall strength remains sufficient to reclaim a wide range of components previously believed unsalvageable.
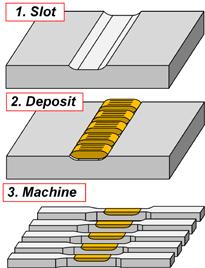

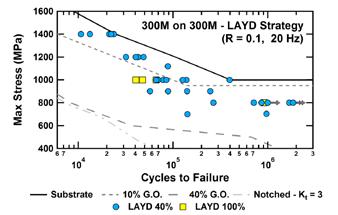
Test results showing significant improvement in tensile (top) and fatigue performance (bottom) for laser additive repair compared with the traditional grind-out method, using track delay (TRAD) and layer delay (LAYD) strategies for different proportions of the cross-section. The ability to restore large cross sections with similar performance to shallow grind-outs means a greater variety of components can be reclaimed.
Based on the above research, RUAG Australia has continued to develop its state-of-the-art laser additive repair facility with the support of RMIT and Swinburne, which has already been used for the repair of in-service components for the Royal Australian Air Force (RAAF). This not only includes the geometric restoration of a worn parts deemed beyond safe limits, but also the refurbishment of internal cylinder threads using specialised deposition nozzles. These repairs are currently with the airworthiness authority for acceptance and incorporation approval. This new sovereign capability to restore worn surfaces and carry out structural repairs in this country is a significant gain for Australia, as parts can be restored at a fraction of the cost of replacement while reducing Australia’s reliance on overseas suppliers. Continued laser repair research at RMIT and Swinburne into modern stainless steels looks to further expand the repair capacity at RUAG, safeguarding the longevity of next-generation platforms where traditional repairs are not possible or very difficult.