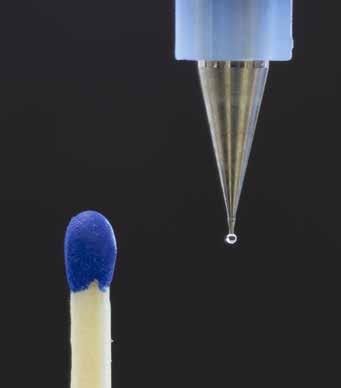
8 minute read
Micro dispensing systems for electronics
from AMT JUN/JUL 2021
by AMTIL
Micro dispensing systems for the electronics industry
Micro dispensing enables state-of-the-art manufacturing processes in the electronics industry and increases the service life of individual components. Adhesives, sealants, potting compounds or heat conductive pastes are processed in various applications.
In consumer electronics in particular, the prerequisites for performance are increasing with ever- smaller components and simultaneously falling manufacturing costs. Fully automatic and process-reliable micro dispensing systems make this possible. For example, in the manufacture of smartphones, components are bonded, potted, and sealed in fully automated micro dispensing systems. A camera in a smartphone has up to 40 different bonding and dispensing applications. Micro dispensing comprises various processes: • In Bonding applications, dispensing systems must be able to provide absolute stable dispensing. On the one hand, the bond must withstand external environmental influences such as high temperature fluctuations, vibrations, or moisture. On the other hand, adhesive residues on the edges or overflowing adhesives between two assembled parts are not acceptable.
It is important not to apply too much or too little adhesive: in most applications, a precisely defined amount of material is required without pulling the thread of the material. Adhesive residues can otherwise cause great damage, for instance, due to contamination during production. Moreover, a quantity too small would impair the adhesive strength. • In Dam & Fill applications, a highly viscous barrier, the socalled “dam” in the form of a closed outer contour, is first applied to the surface to be sealed. The internal area is then filled with a low-viscosity sealing compound. Both materials are then cured together. The area to be protected is thus sealed and optimally shielded against external influences. The primary goal is to protect the highly complex and sensitive assemblies. • Glob Top potting protects sensitive components, usually semiconductor chips, from mechanical stress such as vibrations or temperature fluctuations. And it also protects them from external environmental influences such as moisture or corrosion. Simultaneously to Dam & Fill, a liquid resin matrix usually based on epoxy resin is applied, whereby the dam can be eliminated. • Classic Underfill applications are primarily used to mechanically stabilise various components on printed circuit boards while at the same time compensating for different thermal expansions.
In this way, damage due to stress is avoided. As a rule, the adhesives used in this process display a very high capillary flow behaviour and thus completely fill the gap between the chip and the printed circuit board (PCB), though the adhesive is only dosed along the outer contour of the chip. • Micro dispensing means that the dosing volume is in the range of 0.001ml. Whether bead dosing, sealing, point dosing, potting or two-component applications, precision, repeatability and reliability are essential. ViscoTec dosing systems, for example, process low- to high-viscosity liquids and pastes with a repeat accuracy of higher than 99 %. The repeat accuracy depends both on the dosing process and the material properties. • Encapsulation means that an electronic potting compound is applied to a predetermined surface. It protects the component during transport and against external influences such as vibrations, shocks, moisture, dust, and extreme temperatures. The joint not only protects, but also improves electrical insulation, protection against damage and chemical resistance. • Optical Bonding eliminates the gap between the glass and display of smartphones and tablets, reducing the effect of different refraction and reflection. In addition, the stability and damage resistance of the display is increased. The main goal is to improve readability of the displays outdoors. • Conformal Coating, for example, protects PCBs from moisture, contamination with dust or chemicals or temperature fluctuations. In addition, reliability and electrical properties can also be improved. The automated application of various viscous materials is intended to offer maximum flexibility in the selection of the suitable dosing material on the one hand and to enable uncomplicated processing through maximum reliability on the other. There are several important parameters that determine the dosing process. Short cycle times, cyclical application, or continuous operation, low to highly viscous, structure-sensitive, solids-laden liquids, tribological losses such as friction, leaks, wear, aging, fracture mechanics. The suitable dosing pump takes all variables into account and is adapted to the material. In addition, chemical reactions can occur that lead to wear, such as plastic deformation, abrasion, static friction, and fracture mechanics. For the optimal design of the dosing components for abrasive or chemically aggressive liquids, special know-how is required. In addition, it is often necessary to carry out preliminary or long-term testing. How should the dosing system be designed so that highly viscous, abrasive and shear-sensitive liquids can be reliably processed? And at the same time changes in the flow behaviour of these liquids be tolerated? The progressive cavity pump technology combines both: long maintenance intervals due to optimum pump assembly, and absolute low-shear and viscosity-independent conveying of the material. Metering pumps based on this principle, the so-called endless piston principle, achieve a long service life and very high energy efficiency.
The special rotor-stator geometry of the progressive cavity pump technology, and thus also of the ViscoTec and preeflow dispenser, enables pulsation-free dosing. Dosing quantities ranging from less than 1 μl up to larger quantities can be dosed with the highest precision as dot, bead, or potting applications. Another decisive advantage of the endless piston principle is the automatic or programmable reverse flow. This prevents the material from dripping at the end of a dosing process and ensures clean dosing. With the gentle technology, even very sensitive materials such as UV adhesives or anaerobic adhesives can be dosed. Due to the compact and weight-reduced design of the dispensers, they can be integrated into almost all axis and robot systems. Moreover they can be operated and controlled as complete dosing units in systems. They can also be easily integrated into existing production systems. Progressive cavity pumps belong to the family of positive displacement pumps. The volume flow and the quantities to be dosed are directly proportional to the number of revolutions. The precise co-ordination of rotor and stator makes the dispenser pressure-tight, so that no additional valve is required. In this way, volumetric conveying can be guaranteed at all times. And this in turn makes the very gentle dosing of even the smallest quantities possible. A separate control unit allows the operator to program the speed. If the properties of an adhesive are known, user-specific quantities can be programmed via the controller - independent of viscosity and temperature. The micro dispensers from ViscoTec and preeflow allow dosing with a volume flow of 0.1ml to 60ml/ min. Typically, the one- and two-component dispensers are used in fully automated processes. However, they can also be used as hand-held devices. The perfect combination: Know-how and technology
Progressive cavity pumps are ideally suited for pressure-sensitive liquids containing hollow polymer spheres, for example, but also for viscosity-independent applications with liquids up to several million mPas or thixotropic materials. Two-component applications with mixing ratios of up to 100:1 or even materials with a short pot life can be easily processed and dosed directly as required. The material to be dosed is perfectly prepared for a dosing application with direct, gentle emptying and a constant supply, which can also be achieved with progressive cavity pumps. Liquids requiring pre-treatment can be introduced into a combined extraction or treatment and buffer system for homogenisation and degassing. The portfolio of the Bavarian dosing technology specialist offers all this. The dosing process is optimally planned and adapted to the respective application - from the emptying of the container through the preparation of the material to the actual dosing - for maximum process reliability and cost control. ViscoTec and preeflow dosing systems are suitable for numerous applications: thanks to the endless piston principle, which is built into the entire portfolio, liquids and pastes are dosed purely volumetrically and treated extremely gently. Solid-laden and shearsensitive adhesives can also be transported without any problems - and with a repeat accuracy of 99% - without air inclusions! In addition to UV-curing and various other adhesives, solder pastes, electrically or thermally conductive or abrasive pastes or other liquids with viscosities ranging from aqueous to pasty are also processed. Low maintenance costs, absolute process reliability and high planning reliability are important for system suppliers. The purely volumetric pumps and dispensers combine various advantages: dosing processes run independently of pressure, time, and temperature; and the valve-less tightness technology guarantees very easy handling.
Engineering and consulting
Working with ViscoTec, almost every well-functioning dosing application begins with expert advice and carefully thought-out decisions. The process requirements and the dosing material must be defined. The appropriate dosing components are selected, and the correct application parameters determined. The dosing applications are simulated in laboratory tests and all parameters are checked and optimized again - validation is carried out. The reliable results of such tests can be easily transferred to the application situation to integrate the dosing task into the overall process. A positive co-operation between the customer, the material manufacturer and the dosing technology manufacturer enables the qualification of suitable solutions from material selection to implementation in the dosing process. The comprehensive consultation leads to the consistent development of a highly reproducible dosing application, to an increase in production rates and process reliability. And all this with full cost control. Customers receive fast support and service from specialized partners worldwide. Spare parts and accessories are always in stock and available at short notice - worldwide.
www.viscotec-asia.com
The Toughest just got TOUGHER
The new SLAGHOG™ Version 3 has 50% more torque making slat cleaning even faster and easier! Built tough in the USA the SlagHog laser slat cleaner is the most powerful and fastest slat cleaner in the world. Increased ROI through fast and efficient cleaning of steel or copper slats on CO2 or Fiber laser cutting machine.
Watch your productivity SOAR
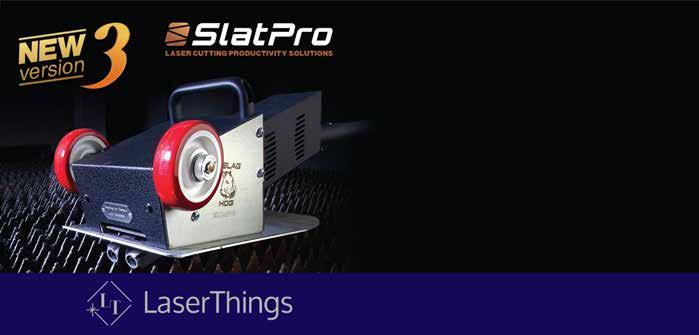